Файл: Курсовой проект по дисциплине Производство и ремонт подвижного состава на тему Технологический процесс деповского ремонта универсальной платформы.docx
ВУЗ: Не указан
Категория: Не указан
Дисциплина: Не указана
Добавлен: 26.04.2024
Просмотров: 7
Скачиваний: 0
ВНИМАНИЕ! Если данный файл нарушает Ваши авторские права, то обязательно сообщите нам.
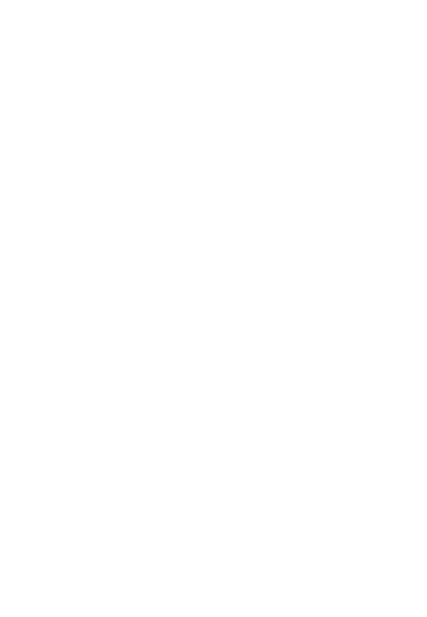
| | ||
Подп. и дата | | ||
Инв. № дубл. | | ||
Взам. инв. № | | ||
Подп. и дата | | ||
Инв. № подл. | |
Федеральное государственное бюджетное образовательное учреждение высшего образования
«ПЕТЕРБУРГСКИЙ ГОСУДАРСТВЕННЫЙ УНИВЕРСИТЕТ ПУТЕЙ СООБЩЕНИЯ ИМПЕРАТОРА АЛЕКСАНДРА I»
(ФГБОУ ВО ПГУПС)

Факультет «Транспортные и энергетические системы»
Кафедра «Вагоны и вагонное хозяйство»
Специальность 23.05.03 «Подвижной состав железных дорог»
Специализация «Вагоны и вагонное хозяйство»
Курсовой проект
по дисциплине: «Производство и ремонт подвижного состава»
на тему: «Технологический процесс деповского ремонта универсальной платформы»
Выполнил:
Принял:
Доцент
Санкт-Петербург
2021
Содержание
Введение 3
1 Назначение платформы и его роль в обеспечении безопасности движения поездов 5
2 Описание основных дефектов и неисправностей платформ, анализ причин их появления. Технологический процесс ремонта. 8
3 Технологический процесс ремонта платформы 9
4 Технологическое оборудование для осуществления деповского ремонта 16
5 Расчет технико-экономической эффективности от внедрения ремонта 18
6 Мероприятия по повышению надежности и увеличению срока платформы 20
Библиографический список 22
Введение
Одной из главных стратегических задач, стоящих перед вагонным хозяйством, является поддержание работоспособности парка грузовых вагонов за счет повышения качества их ремонта.
Большое внимание уделяется развитию технической базы для текущего ремонта вагонов. Необходимо создание крупных механизированных пунктов подготовки вагонов к перевозкам. Совершенствуется работа пунктов технического обслуживания, расположенных на сортировочных и участковых станциях. Широко внедряются средства механизации трудоемких процессов. Таким образом, вагонное хозяйство железных дорог, развивая современную техническую базу для обслуживания и ремонта вагонов, приобретает прочную индустриальную основу для обеспечения высокого уровня работоспособности вагонного парка в современных и перспективных условиях его эксплуатации.
Для восстановления работоспособности вагонов, обеспечения их безаварийной работы и качественных перевозок грузов и пассажиров производится техническое обслуживание и ремонт вагонов.
Под системой технического обслуживания и ремонта вагонов понимают проводимые с определенной периодичностью виды работ по поддержанию и восстановлению работоспособности оборудования.
Деповской ремонт вагона - ремонт, выполняемый для восстановления исправности и частичного восстановления ресурса вагона с заменой или восстановлением составных частей ограниченной номенклатуры и контролем технического состояния составных частей. Деповской ремонт грузовых вагонов производится по истечении межремонтных нормативов (календарного срока в месяцах или пробега в километрах), и в соответствии с требованиями настоящего Руководства, при наличии уведомления формы ВУ-23М. Допускается досрочная постановка грузовых вагонов в деповской ремонт по инициативе собственника вагонов.
Ремонт вагонов производится согласно требованиям «Грузовые вагоны железных дорог колеи 1 520 мм. Руководство по деповскому ремонту» по истечении межремонтных нормативов (календарного срока в месяцах или пробега в километрах).
Перед постановкой на ремонт вагоны должны быть очищены от остатков перевозимых грузов. До постановки в ремонт каждый вагон осматривается мастером совместно с приемщиком. Объем работ отражается в дефектной ведомости ремонтных работ формы ВУ-22.
Ремонт вагонов производится по способу непосредственного ремонта деталей и узлов на вагоне или замены неисправных узлов и деталей отремонтированными или новыми соответствующего типа, отвечающими техническим требованиям и характеристикам данной модели вагона.
Ремонт узлов и деталей сваркой производится в соответствии с «Инструкцией по сварке и наплавке при ремонте грузовых вагонов». [5]
1 Назначение платформы и его роль в обеспечении безопасности движения поездов
Железнодорожная платформа является грузовым вагоном открытого типа, предназначенным для перевозки штучных грузов, контейнеров и оборудования, не требующих защиты от атмосферных осадков.
Железнодорожные платформы подразделяются на два вида: универсальные и специализированные. Универсальные ж/д платформы предназначены для перевозки различных грузов, не требующих специальных крепежных деталей. Они используются для перевозки широкой номенклатуры грузов. Специализированные ж/д платформы предназначены для перевозки какого-то одного вида грузов и имеют специальные приспособления для удобного крепления данного вида грузов и облегчения погрузочно-разгрузочных работ. Наиболее широко распространены специализированные вагоны для перевозки автомобилей, контейнеров, лесоматериалов.
Кузов универсальной четырехосной ж/д платформы состоит из рамы с восемью продольными и двумя торцевыми бортами. Торцевые борта имеют меньшую высоту, чем продольные. Рама сварная. Пол платформы металлический в средней части и деревянный по бокам. Борта фиксируются в вертикальном положении при помощи клиновидных запоров. В откинутом положении боковые борта служат для погрузки колесной техники самоходом.[6]
Дополнительно различаются следующие виды железнодорожных платформ:
по конструкции:
-
бортовые; -
безбортовые; -
тормозная; -
нетормозная.
по грузоподъемности:
-
13-тонная; -
23-тонная; -
38-тонная.
Для курсового проекта был выбран 4-осная платформа, модель 13-4012, который показан на рисунках 1.1 и 1.2.

Рисунок 1.1 – Платформа модель 13-4012
Технические характеристики платформы модели 13-4012 представлены в таблице 1.1
Таблица 1.1 – Технические характеристики
Грузоподъемность, т | 71,9 |
Масса тары вагона, т | 21,7 |
Габарит | 0-ВМ (01-Т) |
База вагона, мм | 9720 |
Длина, мм: - по осям сцепления автосцепок - по концевым балкам (длина рамы) | 14620 13400 |
Ширина максимальная, мм | 3150 |
Высота от УГР, мм | 1820 |
Количество осей, шт. | 4 |
Высота продольных бортов, мм | 740 |
Высота торцевых бортов, мм | 640 |
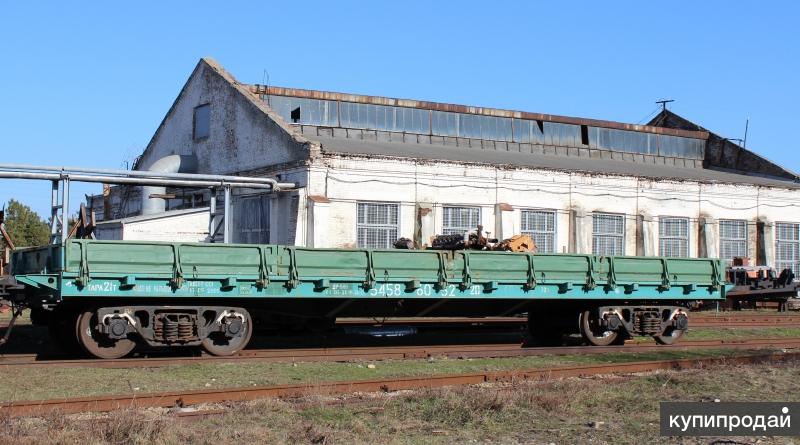
Рисунок 1.2 – Платформа 13-4012
2 Описание основных дефектов и неисправностей платформ, анализ причин их появления. Технологический процесс ремонта.
В процессе эксплуатации платформы появляются различные неисправности, которые приходится устранять при техническом обслуживании или ремонте. Неисправности платформы изображены на рисунке 2.1. Причинами этих неисправностей могут быть процессы естественного происхождения, ошибки при выборе конструкторских или технологических решений, нарушения правил технической эксплуатации вагона.
Неисправности, обусловленные процессами естественного происхождения, проявляются чаще всего в виде значительного изнашивания деталей и сборочных единиц, накапливающегося в результате длительной эксплуатации вагона (постепенный отказ) или в форме внезапных отказов, вызванных исчерпанием конструкционным материалом своего ресурса (старение и явление усталости материала). [6]
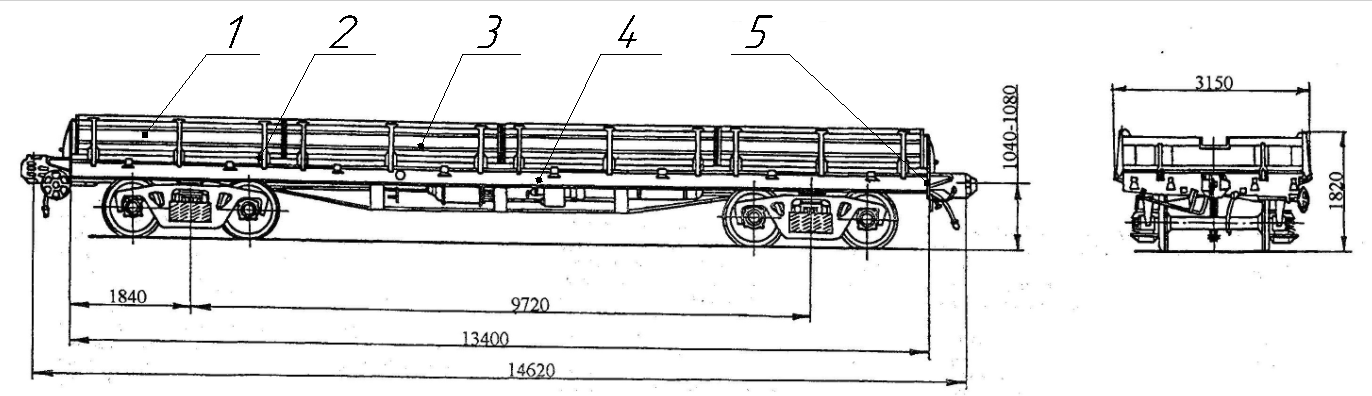
Рисунок 2.1 - Неисправности платформы
Неисправности платформы:
-
Повреждение, излом, пробоина борта; -
Повреждение петель и запоров бортов; -
Обрыв борта -
Излом или трещины в раме -
Обрыв сварных швов
3 Технологический процесс ремонта платформы
При ремонте вагона рекомендуется применять сварочные материалы, основываясь на следующих нормативных документах: «Инструкция по сварке и наплавке при ремонте грузовых вагонов» и «Грузовые вагоны железных дорог колеи 1520 мм». [1], [2]
3.1 Универсальные платформы
-
Искривление продольного металлического борта в вертикальной и горизонтальной плоскостях не должно превышать 25 мм. Разрешается деформированные борта править без демонтажа с платформы. -
После ремонта зазор между бортами и армировочными угольниками при закрытых бортах допускается не более 5 мм, при этом местные зазоры не должны превышать 5 мм на длине не более 500 мм. Местные зазоры до 10 мм разрешается устранять путем приварки планок с внутренней стороны кромки борта толщиной 4 мм на длине не более 300 мм. Зазоры свыше 10 мм устраняют правкой нижних кромок борта. -
Зазоры между торцами продольных бортов в закрытом состоянии допускаются не более 6 мм. -
Детали металлических бортов, требующие ремонта, демонтируют (срезают), изогнутые выправляют. Суммарный износ поверхностей клина бортового запора допускается не более 8 мм. Петли, детали запоров бортов с трещинами или изломами ремонтируют сваркой с постановкой накладки или заменяют новыми.
3.3 Вагонная рама и ее детали
3.3.1 Балка хребтовая
Материал - сталь 09Г2, 09пд, 09пс, 1ОГ2Б по ГОСТ 19281 ПГ2ФД по
ТУ 14-1-5391-99.
При плановых видах ремонта разрешается:
а) по всей длине хребтовой балки, изображенной на рисунке 3.1:
-
заварка изломов, трещин, деф. 2, двутавра (тавра) с последующей постановкой усиливающих односторонних накладок (толщина накладок должна отвечать требованиям, при условии, что трещина со стенки не распространяется на нижнюю полку двутавра; -
частичная замена двутавра (тавра) вставками длиной не менее
1000 мм;
3) заварка трещины горизонтальной полки, деф. З, с последующей приваркой угловой накладки.
б) в средней части балки между пятниковыми опорами:
-
заварка не более двух трещин, деф. 1, длиной менее 2/3 сечения основных горячекатаных элементов хребтовых балок с усилением накладками. Для постановки горизонтальной накладки в двутавре (тавре) должен быть сделан вырез с последующей обваркой;
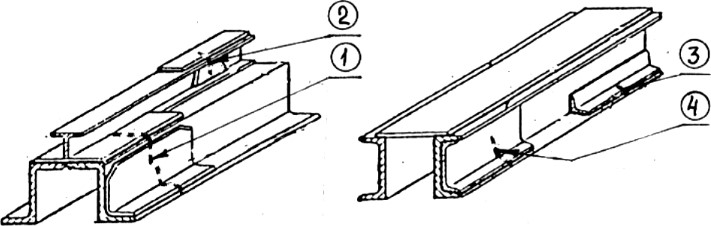
-
не более двух трещин длиной менее 2/3 сечения основных горячекатаных элементов хребтовых балок; 2- изломы и трещины двутавра; 3- трещина горизонтальной полки; 4- не более двух трещин, переходящих на вертикальную стенку не более чем на 10 0 0 высоты хребтовой балки.
Рисунок 3.1 - Балки хребтовые с трещинами и изломами, отремонтированные накладками
-
заварка не более двух трещин, деф. 4, переходящих на вертикальную стенку не более чем на 10 0 0 высоты хребтовой балки с постановкой угловой накладки;
З) заварка не более двух трещин, деф. З, на одной горизонтальной полке, не переходящих на вертикальную стенку, с постановкой угловой накладки;
4) наплавка пораженных коррозией мест глубиной до 6 мм при деповском ремонте и техническом обслуживании с отцеплением (текущем ремонте), или усилении их накладками толщиной от 8 мм до 10 мм;
в) в консольной части хребтовой балки на рисунке 3.2:
-
заварка трещин горизонтальной полки, переходящих на вертикальную стенку хребтовой балки, но не более чем на 50 0 о высоты хребтовой балки и не ближе 200 мм от шкворневой балки, с последующим усилением накладками. Накладка устанавливается под заклепки упорных угольников и приваривается по двум сторонам параллельно продольной оси хребтовой балки• -
планки в местах постановки поглощающего аппарата, имеющие трещины и износ глубиной более 8 мм, сваркой не ремонтируются и заменяются на новые;[1]

Рисунок 3.2 - Балка из Z-образного профиля, усиленная накладками в месте расположения упорных угольников
3.3.2 Балка концевая грузового вагона
Материал - сталь 09Г2, 09пд, Опс по ГОСТ 19281.
При всех видах ремонта разрешается:
а) наплавка пораженных коррозией мест при условии, что толщина стенки до наплавки не менее 0,5 номинального размера. Допускается вместо наплавки приварка накладок толщиной не менее 4 мм и площадью не более
б) частичная замена (не более половины длины) вертикального листа балки сварной конструкции с усилением накладками при условии, что верхний и нижний листы не имеют повреждений изображена на рисунке 3.3;
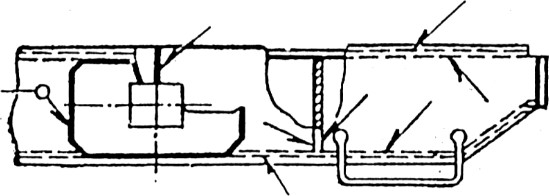
Рисунок 3.3- Вертикальный лист балки сварной конструкции, отремонтированный путем замены половины листа и усиленный накладкой
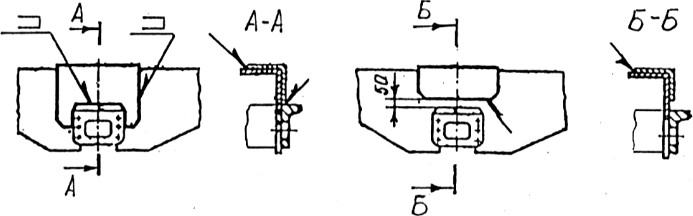
Рисунок 3.4 - Постановка накладки на балке над ударной розеткой
д) заварка не более двух трещин и одного излома в любом месте концевой балки с усилением накладками;
е) полная или частичная замена верхнего или нижнего листа с последующим усилением накладкой при условии, что стыки верхнего и вертикального листов не должны совпадать;
ж) частичная замена (не более половины длины) штампованной балки с последующим усилением накладкой;
и) полная или частичная замена порога или заварка на нем не более трех трещин с усилением накладками;
м) штампованные балки, имеющие повреждения в местах постановки кронштейна и державки расцепного рычага, ремонтируют сваркой с постановкой усиливающих планок шириной не менее 150 мм и толщиной 8мм, на всю высоту вертикальной части балки;
н) в штампованной балке, имеющей коррозионное повреждение более 30% поперечного сечения, поврежденную часть заменяю вставкой с усилением места стыка накладками;
При деповском ремонте и техническом обслуживании с отцеплением вагонов (текущем ремонте) разрешается:
а) заварка не более трех трещин и одного излома в любом месте балки;
б) заварка не более четырех трещин дверного порога с усилением их накладками.
3. 3. 3 Балка шкворневая и промежуточная грузового вагона
Материал –сталь09Г2, 09Г2Д,09Г2С, 10Г2БпоГОСТ 19281.
При плановых видах ремонта разрешается:
а) заварка трещин длиной до 30 мм без постановки усиливающих накладок;
б) заварка трещин или изломов верхнего листа шкворневой и промежуточных балок с усилением накладками при условии, что на листе, при деповском ремонте и техническом обслуживании с отцеплением -не более трех, показано на рисунке 3.6.

Рисунок 3.6– верхние листы промежуточной и шкворневой балок, отремонтированные сваркой
в) заварка трещин, деф.1, изломов, и коррозионных повреждений вертикальных листов шкворневой и промежуточной балок с постановкой усиливающих накладок показано на рисунке 3.7.
г) заварка трещин или излома нижнего листа шкворневой балки с постановкой усиливающей накладки изображено на рисунке 3.12. Допускаемое расстояние от начала трещины или излома до границы крайнего элемента хребтовой балки не менее100 мм.
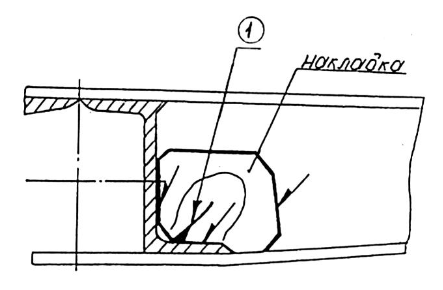
-
трещина
Рисунок 3.7- Отремонтированный вертикальный лист шкворневой балки в месте соединения с хребтовой балкой

Рисунок 3.8 - Нижний лист шкворневой балки, отремонтированный сваркой
д) усиление накладкой нижнего листа шкворневой балки в месте постановки пятника, при наличии трещины на расстоянии менее 100 мм от хребтовой балки или замене половины листа, показанного на рисунке 3.9, с постановкой уравнительных накладок на скользуны. Толщина уравнительных накладок должна соответствовать толщине усиливающей накладки;

Рисунок 3.9 - Усиление накладкой нижнего листа шкворневой балки
е) частичная (не более половины длины) или полная замена нижнего листа шкворневой балки. При частичной замене стык усиливают накладкой. При деповском ремонте и техническом обслуживании с отцеплением - не более четырех усилений;
ж) частичная или полная замена распорок концевой балки изотермического вагона при наличии в них трещин или изломов, расположенных на расстоянии не ближе 400 мм от концевой балки. При капитальном ремонте допускается не более двух, а при деповском ремонте и техническом обслуживании с отцеплением - не более трех заваренных мест, усиленных односторонними накладками;
Косынки, ребра жесткости, упоры крышки люка и другие детали балок, имеющие трещины, ремонту сваркой не подлежат и должны заменяться на новые.

Рисунок 3.10 - Вертикальный лист промежуточной балки, отремонтированный в месте размещения упора люка
3.3.4 Скользуны рамы вагона
Материал - сталь СтЗ по ГОСТ 380.
При всех видах ремонта разрешается наплавка изношенной рабочей поверхности при ее износе не более 200 0 номинальной толщины, а также приварка планок соответствующей толщины с предварительной механической обработкой для устранения неравномерного износа. [2]
4 Технологическое оборудование для осуществления деповского ремонта
Вагоны при эксплуатации изнашиваются, и они периодически подвергаются различным видам ремонта, которые проводятся в депо. Ремонт узлов вагонов сопровождается их разборкой. Так при ремонте вагона, нужно отсоединить тележку (является опорой кузова) от вагона, выкатить, а вагон установить на временные стационарные или переносные опоры.
Машина вагоноремонтная ВРМ «Сибиряк» предназначена для заводского, деповского, а также текущего отцепляемого ремонта товарных вагонов и полувагонов.
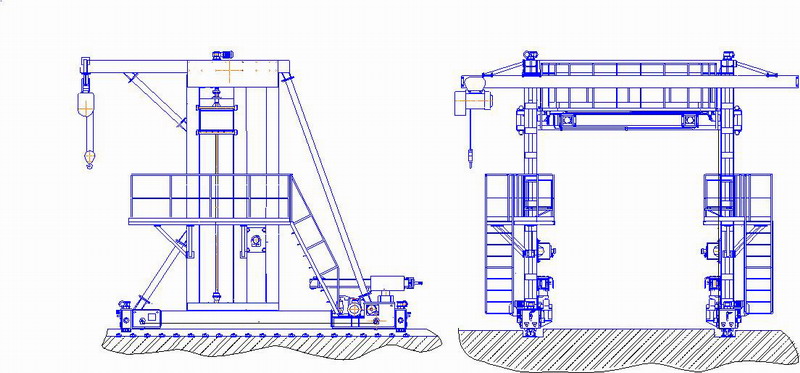
Рисунок 4.1 – Вагоноремонтная машина
Выполняемые работы:
-
поджим крышек люков полувагонов; -
правка снаружи боковых стен вагонов, стоек, раскосов и верхних, нижних рамочных балок; -
правка снаружи торцевых стен вагонов на опускающей торцевой площадке; -
замена дверей крытого вагона и полувагона; -
поджатие отдельных элементов при сварочных работах; -
смена створок дверей; -
производство электросварочных работ; -
смена головки автосцепки; -
транспортировка инструментов, приспособлений и запасных частей; -
обеспечение гидроинструмента гидравлическим давлением; -
производство погрузочно-разгрузочных работ.
Таблица 4.1 – Технические параметры
Наименование параметра | Значение |
Давление гидравлической станции, мне менее МПа | 16 |
Сила штока переносного домкрата, не менее кгс | 20000 |
Сила штока механизма выравнивания боковых и задних стен, не менее кгс | 25000 |
Расстояние между осями рельс машины, не более мм | 4785 |
Габаритные размеры, (длина x ширина x высота), мм | 8450х8350х6850 |
Масса комплекса, не более, кг | 20000 |
5 Расчет технико-экономической эффективности от внедрения ремонта
В качестве примера рассмотрим расчет экономического эффекта от внедрения вагоноремонтной машины.
Фонд оплаты труда при ремонте платформы определяется по формуле 5.1:

где ЧТС – ч.т.с. слесарь по ремонту, составляет 95 руб.,






Начисления на ФОТ составляют 26,7% и равны соответственно 334,8 руб.
Себестоимость ремонта вагона определяется по формуле 5.2:

где Н – начисления на ФОТ.

Фонд оплаты труда при внедрении машины определяется по формуле 5.1 и составляет:

где ЧТС – ч.т.с. слесаря, составляет 95 руб.,





Начисления на ФОТ составляют 26,7% и равны соответственно 41,9 руб.
Себестоимость работ при внедрении машины определяется в соответствии с формулой 5.2 составляет:

Расчет годового экономического эффекта от внедрения производится по формуле 5.3:

где





Срок окупаемости капитальных вложений рассчитывается по формуле 5.4 [3]:

где



6 Мероприятия по повышению надежности и увеличению срока платформы
Стратегией развития железнодорожного транспорта в РФ до 2030 г. определены перспективные направления развития железных дорог. Одно из направлений — повышение грузооборота за счет увеличения провозной способности линий, что достигается наращиванием массы поезда. Возможны два решения этой задачи: повышение грузоподъемности вагонов и, следовательно, осевой и погонной нагрузки, либо увеличение количества вагонов в составе поезда, а значит, и его длины.
В качестве одного из стратегических направлений научнотехнического развития на сети РЖД было заявлено создание принципиально новых вагонов с повышенной осевой нагрузкой 25–30 тс без увеличения воздействия на путь. Главный вопрос, который предстояло решить, касался проектирования новой тележки, позволяющей увеличить грузоподъемность вагонов.[4]
Первый рубеж — 25 тс
В течение прошедшего десятилетия этот рубеж успешно преодолели АО «Уралвагонзавод» (тележка модели 18–194–1) и АО «Тихвинский вагоностроительный завод» (тележка модели 18–9855). Сейчас вагоны с осевой нагрузкой 25 тс пользуются устойчивым спросом у операторов вследствие повышенной грузоподъемности и вместимости, а также увеличенных гарантийных плеч и межремонтных сроков. В начале 2018 г. количество таких вагонов в эксплуатации перешагнуло порог 100 тыс. ед., что составляет почти 10 % от общероссийского парка грузовых вагонов.
Новая цель — 27 тс
Повышение осевой нагрузки — закономерное развитие отрасли и ключевой тренд сегодняшнего дня. Мировой опыт свидетельствует, что недавно освоенный в России стандарт тележек 25 т на ось — только начало пути и возможностей отечественного рынка. Отметим, что тяжеловесное движение получило широкое развитие на всех континентах. В Австралии — странепионере тяжеловесного движения, осевая нагрузка грузового вагона доходит до 37,5 тс, а масса поезда превышает 48 тыс. т. Североамериканские железные дороги переняли австралийский опыт в конце 90х годов, и сегодня осевая нагрузка в США составляет 32,5 тс, на некоторых участках 36 тс, а масса поезда превосходит 20 тыс. т.
В плане технологий нашей стране нужно многое наверстывать, и ОАО «РЖД» одной из своих стратегических задач ставит развитие тяжеловесного движения. Вагоны с ходовой частью с осевой нагрузкой 27 тc позволят запустить поезда общей массой более 10 тыс. т, а на некоторых направлениях эта масса превысит 11 тыс. т. При сохранении заданной длины состава 1050 м станет возможным перевезти в таком поезде почти на 20 % грузов больше по сравнению с типовым решением. Соответственно можно увеличить вывоз продукции предприятий на ключевых направлениях сети, не увеличивая парк локомотивов, и при этом сократить рас ходы на тягу.
В России эксплуатация парка сверхтяжёлых инновационных вагонов пока не предусмотрена. У нас придётся ограничиться эксплуатацией вагонов с осевой нагрузкой 27 тс. Для этого существуют весьма веские основания, дающие право настаивать на их массовое использование:
-
существенно увеличивается перевозка грузов данными вагонами на тех направлениях, где пропускная способность подвижного состава ограничена; -
регулярное использование позволит с меньшими затратами перевозить продукцию добывающей отрасли: уголь, руду, щебень и другие подобные грузы; -
позволяет решить проблему перевозки угля, поставляемого на экспорт, объёмы которого всё время увеличиваются; -
перевозка данных составов с успехом может осуществляться имеющимися на балансе РЖД локомотивами, напри мер сдвоенными тепловозами 2ТЭ25А «Витязь»; [4]
Для внедрения 27тонных вагонов не потребуется значительных финансовых вливаний.
Библиографический список
-
Грузовые вагоны железных дорог колеи 1520 мм. Руководство по деповскому ремонту РД 32 ЦВ 1692017, утвержденное Советом по железнодорожному транспорту государствучастников Содружества (протокол от 18 19 мая 2011 г. N 54) 167с. -
Инструкция по сварке и наплавке при ремонте грузовых вагонов. РД ВНИИЖТ059/012019. Утверждена Советом по железнодорожному транспорту государствучастников Содружества, протокол от 45 ноября 2015 г. № 63 (Приложение № 60). Согласована Комиссией вагонного хозяйства, протокол от "0810" сентября 2015 г., № 60 (в ред. 71го заседания Совета по железнодорожному транспорту государств участников Содружества" от 1516.10.2019)122 -
Методические указания к выполнению курсового проекта «Производство и ремонт подвижного состава». Самаркина И.К, Мойкин Д.А – издво ПГУПС 2011г. -
Интернетресурс:
https://www.uniwagon.com/multimedia/media_about_us/effektivnostekspluataciivagonovspovyshennojosevojnagruzkoj/
Объединенная вагонная компания (Эффективность эксплуатации вагонов с повышенной осевой нагрузкой)
-
Интернетресурс: https://vagonmaster.com/services/depovskojremont/
Вагонмастер (Деповской ремонт грузовых вагонов)
-
Интернет ресурс: https://tktranskavkaz.ru/железнодорожныеплатформы/
Железнодорожные платформы
-
Интернет ресурс: http://www.energos.su/production/oborudovaniedlyaremontagruzovyhvagonov/oborudovanievagonosborochnogotseha/dv160#prettyPhoto
Домкрат вагонный Д160.