Файл: Контрольная работа по дисциплине Технология и организация производства продукции и услуг.docx
ВУЗ: Не указан
Категория: Не указан
Дисциплина: Не указана
Добавлен: 28.04.2024
Просмотров: 13
Скачиваний: 0
ВНИМАНИЕ! Если данный файл нарушает Ваши авторские права, то обязательно сообщите нам.
МИНИСТЕРСТВО НАУКИ И ВЫСШЕГО ОБРАЗОВАНИЯ РОССИЙСКОЙ ФЕДЕРАЦИИ
Федеральное государственное бюджетное образовательное учреждение
высшего образования
«Уральский государственный экономический университет»
(УрГЭУ)
КОНТРОЛЬНАЯ РАБОТА
по дисциплине «Технология и организация производства продукции и услуг»
Институт непрерывного Студент
дистанционного образования Гришин Л.К.
Направление подготовки Группа: ИДО ЗБ УГ-22 КЧ
Управление качеством Преподаватель: Мирошникова Е.Г.
Направленность (профиль)
Управление качеством в производственно-
технологических системах и сфере услуг
Оценка: ________________
Екатеринбург
2022 г.
Содержание
-
Особенности организации поточного метода производства …….. 3 -
Задачи службы технического обслуживания и ремонта оборудования ……………………………………………………………………... 6
Список использованных источников…………………………………..…. 14
1. Особенности организации поточного метода производства
Производственный процесс – это сложное технологическое действие, которое может быть организовано разными способами и средствами. Работа предприятия в условиях поточного выпуска продукции сегодня считается наиболее эффективной, но в то же время и требовательной с точки зрения трудовых, организационных и материальных затрат. В общем смысле поточное производство – это формат производственной деятельности, в котором на первый план выходят принципы ритмичности и повторяемости технологических согласованных операций. Далее будет подробнее рассмотрена сущность этого процесса, его особенности, методы организации и т.д.
В основе любого производства лежит модель организации основных, обслуживающих и вспомогательных процессов, благодаря которым осуществляется рабочая деятельность предприятия, направленная на создание тех или иных продуктов. Относительно организационной модели используемые орудия труда (станки, конвейеры, инструменты) можно рассматривать в качестве объектов организации, находящихся в прямой связи с предметами производства, то есть выпускаемой продукцией.
В значительной степени функции связки между разными элементами производства внутри организационной модели по-прежнему выполняет человек. Как максимум, он непосредственно участвует в процессах изготовления, как минимум – управляет оборудованием, реализующим технологические операции.
В числе особенностей поточного способа производства выделяется упор на автоматизацию рабочих мероприятий с минимальным участием человека. Возможности организации бесперебойного автоматизированного производства могут реализовываться по большей части в основных технологических процессах, касающихся материального превращения условной заготовки в предмет товарных отношений. Например, изготовление мебели на этапах обработки пиломатериала – это основной рабочий процесс мебельной фабрики, который на крупных предприятиях сегодня выполняется на станках под числовым программным управлением. И напротив, обслуживающие и вспомогательные процессы производственной деятельности выполняются в основном рабочим персоналом непосредственно, так как большинство подобных действий требует принятия сложных нестандартных решений.
Модель производственной деятельности в поточной форме основывается на ритмичной повторяемости определенного набора технологических операций, которые выполняются в соответствующих цехах на рабочих местах. Согласование между отдельными операциями может происходить на разных технических и организационных уровнях с разделением во времени и в пространстве. Иными словами, поточное производство – это заранее продуманный алгоритм действий, направленных на изготовление целевой продукции предприятия.
Для более четкого понимания рассматриваемой формы производства можно привести в пример принцип непоточной модели. В данном случае может применяться организация производства как в единичном, так и в серийном формате изготовления продукции. Разница же заключается в том, что поточная технология производства строится на взаимосвязи нескольких групп рабочих операций. В модели непоточного производства цеховые участки организуются по принципу выполнения однотипных и ритмичных, но не согласованных процессов. Изготовление происходит с перерывами между операциями, а обработанные предметы и заготовки отправляются по сложным маршрутам на следующие уровни производства без сопряжения.
Среди отличительных черт технологической организации поточного изготовления продукции можно выделить следующие:
-
Рабочие места обслуживают операции, выполняемые по отношению к одинаковым предметам, обладающим схожими технико-конструкционными характеристиками. В более сложных моделях работа поточного производства допускает изменение формата обработки в определенном диапазоне режимов. То есть конвейерная линия в рамках даже одного технологического процесса может переориентироваться на разные группы обрабатываемых предметов. -
Конфигурация расположения рабочих мест подбирается в зависимости от производственной логистики. Соблюдается четкая иерархия последовательностей при выполнении технологических операций. -
Переход предмета от одного рабочего узла к другому может осуществляться как в поштучном формате, так и партийно, но в любом случае по возможности должен выдерживаться общий ритм производства. -
Основные и часть вспомогательных операций выполняются в механизированном или автоматизированном режиме поточного производства. Это позволяет выдерживать высокий темп исполняемых процессов, но не исключает возможности технологического перерыва, допустимые параметры которого заранее просчитываются в алгоритме действующей модели.
Добиться достаточной эффективности производства «на потоке» можно только при соблюдении ряда принципов технологической организации рабочего процесса, среди которых:
-
Принцип непрерывности. Минимизируется зависимость между отдельными линиями производства по временному признаку. Например, темп работы одного рабочего места в данном случае не может становиться причиной циклических задержек других участков производства. -
Принцип параллельности. Готовые изделия и заготовки при поточном методе производства движутся по технологическим маршрутам параллельно, что также способствует выполнению принципа непрерывности без задержек. -
Принцип прямоточности. И рабочие места, и оборудование размещаются в четком порядке, соответствующем технологическому процессу изготовления продукции. -
Принцип специализации. Обеспечивается разделение производственных функций между отдельными группами поточных линий. То есть исключается универсальность рабочих мест с точки зрения возможностей выполнения разных операций. -
Принцип ритмичности. В рамках функционирования одного рабочего места обеспечивается цикличность операций не только при выпуске одного изделия, но и в режиме изготовления партий продукции. Благодаря этому принципу организуется серийное поточное производство с плановым подходом к массовому выпуску целевого товара.
Серийное производство как таковое является экономически оправданной формой работы большинства крупных промышленных предприятий. Но вместе с этим предполагаются высокие финансовые и материально-технические затраты, без оптимизации которых производственная деятельность будет неэффективной. В этом отношении поточное производство – это оптимальный формат серийного изготовления сложной продукции, требующего применения множества технологических операций. Другое дело, что для организации таких производственных линий должны изначально выполняться особые условия. В их числе можно отметить широкие возможности для углубления специализации отдельных рабочих мест в рамках предприятия и высокую степень унификации технико-конструкционных параметров выпускаемых изделий.
2. Задачи службы технического обслуживания и ремонта оборудования
В процессе эксплуатации технологическое оборудование подвергается физическому и моральному износу и требует постоянного технического обслуживания. Работоспособность оборудования восстанавливается путем его ремонта. Причем в результате ремонта должно не только восстанавливаться первоначальное состояние оборудования, но и значительно улучшаться его основные технические характеристики за счет модернизации. Таким образом, сущность ремонта заключается в сохранении и качественном восстановлении изношенных деталей и регулировки механизмов и другого технологического оборудования.
В машиностроении затраты на ремонт оборудования ежегодно достигают 17-26% его первоначальной стоимости, что соответствует 5-8% себестоимости продукции завода. Практика показывает, что затраты на ремонт и техническое обслуживание оборудования постоянно увеличиваются, растут мощности ремонтных служб и численность ремонтных рабочих (15%). В то же время организационный уровень и качество ремонтных работ в целом далеко не всегда удовлетворительны. Децентрализация ремонта приводит к параллельности однородных работ и низкому техническому уровню их исполнения, затраты на капитальный ремонт станка иногда превышают стоимость нового, простои станков в ремонте, как правило, превышают плановые. Отсюда вытекает важное направление деятельности предприятия ‑ постоянное совершенствование организации ремонтного хозяйства.
Задача ремонтной службы предприятия ─ обеспечение постоянной работоспособности оборудования и его модернизация, изготовление запасных частей, необходимых для ремонта, повышение культуры эксплуатации действующего оборудования, повышение качества ремонта и снижение затрат на его выполнение.
Ремонтную службу предприятия возглавляет отдел главного механика предприятия (ОГМ). Структура ремонтной службы представлена на рис. 3.22
Функции ремонтной службы предприятия:
· разработка нормативов по уходу, надзору, обслуживанию и ремонту оборудования;
· планирование планово-предупредительных ремонтов (ППР);
· планирование потребности в запасных частях;
· организация ППР и ППО планово-предупредительного обслуживания (ППО);
· организация изготовления, закупки и хранения запчастей;
· оперативное планирование и диспетчирование сложных ремонтных работ;
· организация работ по монтажу, демонтажу и утилизации оборудования;
· организация работ по приготовлению и утилизации смазочно-охлаждающих жидкостей (СОЖ);
· разработка проектно-технологической документации на проведение ремонтных работ и модернизации оборудования;
· контроль качества ремонтов;
· надзор за правилами эксплуатации оборудования и грузоподъемных механизмов.
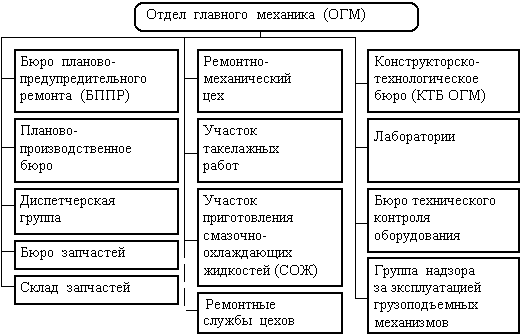
Рис. 3.22. Состав служб ремонтной службы предприятия
Обслуживание и эксплуатация оборудования на предприятиях производятся по единой системе планово-предупредительных ремонтов (ППР).
Система ППР ─ это комплекс планируемых организационно-технических мероприятий по уходу, надзору, обслуживанию и ремонту оборудования. Мероприятия носят предупредительный характер, то есть после отработки каждой единицей оборудования определенного количества времени производятся его профилактические осмотры и плановые ремонты: малые, средние, капитальные.
Чередование и периодичность ремонтов определяется назначением оборудования, его конструктивными и ремонтными особенностями, а также условиями эксплуатации. ППР оборудования предусматривает выполнение следующих работ:
· межремонтное обслуживание;
· периодические осмотры;
· периодические плановые ремонты: малые, средние, капитальные.
Межремонтное обслуживание ─ это повседневный уход и надзор за оборудованием, проведение регулировок и ремонтных работ в период его эксплуатации без нарушения процесса производства. Оно выполняется во время перерывов в работе оборудования (в нерабочие смены, на стыке смен и т.д.) дежурным персоналом ремонтной службы цеха.