Файл: Производство губчатого железа по дисциплине Металлургия черных металлов.doc
Добавлен: 28.04.2024
Просмотров: 37
Скачиваний: 2
ВНИМАНИЕ! Если данный файл нарушает Ваши авторские права, то обязательно сообщите нам.
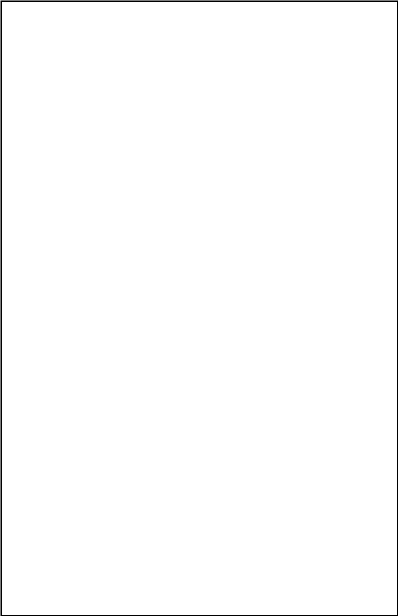
Министерство науки и высшего образования Российской Федерации
ФГАОУ ВО «ЮУрГУ» (НИУ)
Филиал в г. Златоусте
Факультет «Техники и технологии»
Кафедра «Техника и технологии производства материалов»
Семестровая работа
по теме: «Производство губчатого железа»
по дисциплине «Металлургия черных металлов»
ЮУрГУ – 22.03.02.2022.395.00.00
Руководитель
_________________Пятыгин Д.А.
_________________2022г.
Автор работы
студент группы ФТТ-334
__________________Попова Е.С.
_________________2022г.
Работа защищена с оценкой
___________________2022 г.
Аннотация
Цель семестровой работы – изучить методы производства губчатого железа .
В настоящее время значительно изменились требования к качеству металла. Различные технологии металлургии железа обеспечивают получение черных металлов различного качества. Промышленный опыт убедительно показал, что сталь, полученная в электропечах из губчатого железа, обладает лучшими свойствами (прочность, пластичность и др.). Исчерпывающих объяснений этому феномену до сих пор нет. Чаще всего основную причину видят в том, что металлизованные материалы, в отличие от металлического лома, практически не содержат нежелательных примесей, особенно примесей цветных металлов. В этом смысле говорят о "первородных свойствах" металлизованных материалов или "первородной шихте", подчеркивая, что губчатое железо не прошло ранее стадию металлургического переплава. Добавим, что металлизованные материалы практически не содержат также растворенных в металле газов и неметаллических включений.
Содержание
ВВЕДЕНИЕ 3
Устройство для вдувания порошкообразных материалов в жидкий металлСоветский патент 1982 года по МПК C21C7/00 B22D1/00 23
Описание патента на изобретениеSU971890A1 23
ВВЕДЕНИЕ
Прямое получение железа непосредственно из руд, существовавшее задолго до появления доменных печей и возникновения двух стадийной технологической схемы производства железа и стали, в последнее время вновь, но уже на современной основе, развивается во все увеличивающихся масштабах.
Особенно большое значение этому способу придается в странах с ограниченными ресурсами высококачественного металлургического сырья и топлива. Производство железа методом прямого восстановления в основном сосредоточено в Швеции (в 1956 г. было произведено 122 тыс. г). Имеются также промышленные установки в Китае, Японии, Чехословакии, Канаде, США, ФРГ и России.
Существующие способы прямого получения железа из руд в зависимости от физического состояния получаемого продукта и температуры процесса можно разделить на три группы.
1. Способы получения губчатого железа, осуществляемые при сравнительно низких температурах, при которых происходит только восстановление окислов железа без плавления пустой породы. Продукт восстановления получается в твердом виде.
2. Способы получения крицы. Температурные условия процесса значительно выше, при этом происходит расплавление пустой породы с образованием шлака, а частицы восстановленного металла свариваются между собой, образуя тестообразную крицу.
3. Способ прямого получения жидкой стали, осуществляемый при температурах выше точки плавления железа. Конечные продукты процесса — жидкий металл и шлак.
При производстве губчатого железа обычно используются богатые, чистые от вредных примесей руды или концентраты и малосернистые восстановители, так как пустая порода процесса восстановления не претерпевает никаких изменений и остается в губчатом железе, а сера восстановителя может перейти в железо.
При производстве крицы в связи с переходом пустой породы в шлак, который затем отделяется от металла, можно использовать бедные руды и низкосортное топливо. В качестве восстановителя применяют окись углерода, водород или смеси газов, а также кокс и различные виды твердого низкосортного топлива.
Продукты восстановления в зависимости от степени чистоты используются для различных целей. Губчатое железо используется для производства железного порошка и как заменитель железного лома при выплавке высококачественной стали в кислых мартеновских и электрических печах.
Крица, обычно более загрязненная примесями, применяется в доменных печах или в качестве заменителя лома в мартеновских и электродуговых печах.
Основной недостаток всех известных способов прямого получения железа из руд — сравнительно небольшая производительность установок, что и ограничивает их распространение.
В настоящее время во многих странах, в том числе и в России, совершенствуют существующие и ищут новые, более производительные и перспективные методы получения губчатого железа или непосредственно жидкой стали из руд, минуя доменный процесс.
-
Производство губчатого железа
ГУБЧАТОЕ ЖЕЛЕЗО, продукт, получаемый путем восстановления железной руды при температуре ниже температуры плавления металла. Такое железо было первоначальным продуктом железоделательного производства до введения в практику металлургии доменной плавки. В последние десятилетия в некоторых странах ряд научных учреждений, а также отдельных специалистов, занимались разработкой методов получения губчатого железа при использовании низкосортных руды и топлива; было заявлено несколько десятков патентов на способы выработки губчатого железа и дальнейшей переработки его в торговые сорта и полуфабрикаты. Сам процесс восстановления окислов железа, содержащихся в руде, производится твердым углеродом (непосредственное восстановление) или окисью углерода (т. н. косвенное восстановление). В первом случае восстановление руды происходит при температуре от 700° и до температуры спекания данной руды; во втором случае - от 800—850° и до температуры спекания руды. Как тот, так и другой метод работы, в зависимости от качеств руды, имеет свои преимущества и свои недостатки.
-
Производство железа в шахтных печах и ретортах
В шахтных печах и ретортах получают губчатое железо газообразными восстановителями в толстом слое железосодержащих окатышей. В качестве восстановителей применяют конвертированный природный газ, состоящий в основном из водорода (H2) и оксида углерода (CO).
Процесс производства железа осуществляют в противотоке железорудных материалов, загружаемых в агрегат сверху, и нагретых восстановительных газов, подаваемых снизу. Работа агрегата в противотоке дает возможность достигать высокой производительности при хорошем использовании газа.
Восстановительный газ получают в кислородном реакторе, путем неполного сжигания природного газа в кислороде по реакции:
2CH4+ O2=2CO+4H2
Полученный газ, содержащий 29% CO, 55% H2 и 13% окислителей (H2O и CO2) освобождают частично от окислителей, нагревают, до температуры 1100 –1150 °С и через фурмы подают в печь. Горячий газ, поднимаясь навстречу опускающимся окатышам, нагревает и восстанавливает их. Процесс восстановления проходит при температуре 850 – 1050 °С в зоне нагрева и восстановления, расположенной над фурмами печи. Ниже фурм расположена зона охлаждения, в которой окатыши охлаждаются оборотными газами, предварительно подвергнутые очистке. К оборотным газам для охлаждения добавляют небольшое количество природного газа, обеспечивающее частичное науглероживание окатышей (около 1%), что целесообразно для сталеплавильного производства.
Охлажденные металлизированные окатыши выгружаются из печи непрерывно и поступают в электропечи для выплавки стали.
Существует несколько разновидностей этого процесса. Главным отличием их от описанного выше является способ конверсии природного газа. В одном случае она осуществляется двуокисью углерода по реакции:
CH4+CO2=2CO+2H2
Конвертированный газ содержит в этом случае около 35% CO и 60% H. В другом случае конверсию природного газа проводят водяным паром по реакции:
CH4+H2O=CO+3H2
Получаемый конвертированный газ содержит около 14% CO, 58% H2, 21% H2O и 4 – 5%CO2. Перед использованием он подвергается осушке и содержит 16% CO, 73% H2 и 6 – 7% CO2.
Разновидностью способа является процесс в периодически действующих ретортах, используемых в качестве агрегатов восстановления. На установке таких реторт четыре. Емкость каждой реторты 100 – 150 т. Реторты переставляются с одной позиции на другую, что обуславливает циклический характер процесса, состоящего из последовательных операций загрузки, нагрева и восстановления шихты, охлаждения и выгрузки губчатого железа. Реторты загружают и подают газ сверху.
Выгрузку губчатого железа производят снизу с помощью специальных скребков. Губчатое железо поступает на конвейер транспортирующий губку в сталеплавильное отделение.
На установке участвуют четыре реторты, в каждой из которых протекают различные процессы. В одной реторте происходит предварительный нагрев и восстановление шихты газом, выходящим из других реторт. В двух ретортах происходит довосстановление железа подогретым газом получаемым в кон-версионной установке. В четвертой происходит науглероживание губчатого железа. Готовое железо поступает на конвейер, а в освобожденную реторту загружают исходную шихту.
К недостаткам метода относят:
-
периодичность процесса; -
неравномерность металлизации по высоте; -
низкая степень металлизации в сравнении с процессами осуществляемыми в шахтных печах.
-
Метод Виберга
В шахтных печах (метод Виберга) в качестве восстановителя используют газовую фазу из CO и H2, которая циркулирует по замкнутой системе, включающей электрогазогенератор, фильтр и собственно шахтную печь (рис. 18).
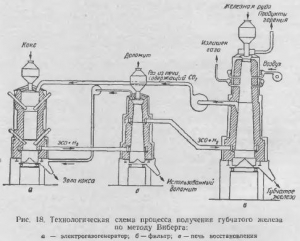
Газовая смесь при 950° вводится в нижнюю часть печи и при движении вверх навстречу опускающейся шихте восстанавливает окислы железа до металлического железа. Большая часть газа при 800° отводится из печи и подается в электрогазогенератор, представляющий собой довольно узкую и высокую шахту, заполненную древесным углем или коксом. В верхней и нижней части шахты расположено четыре пары электродов, служащих для нагрева столба топлива до 1100—1150.
В электрогазогенераторе газ, который содержит примерно 25% CO2, проходя сверху вниз и омывая раскаленные куски кокса, подвергается регенерации по реакциям
CO2 + С = 2СО;
H2O + С = H2 + CO.
На выходе газ состоит в основном из окиси углерода, 20—30% H2 и 3—5% CO2.
Для обогащения газа водородом в электрогазогенератор подается водяной пар или природный газ Природный газ, реагируя с поступающим газом по реакции
CH4 + CO2 = 2СО + 2Н2,
улучшает его состав.
По пути к шахтной печи газ проходит через фильтр с доломитом, где поглощается содержащаяся в нем сера. Циркуляция газа через систему осуществляется вентилятором.
В качестве сырья используются обогащенные окатыши, окомкованные железорудные концентраты с содержанием 64—67% Fe.
Губчатое железо обычно содержит не менее 90% Fe, 0,005% S, 0,005% P и используется для производства высококачественных сталей.
-
Метод Хагенес
Способ получения губчатого железа в тиглях (метод Хагенес) предусматривает использование твердого восстановителя.
В огнеупорные тигли чередующимися слоями загружают тонкоизмельченный богатый железом концентрат или окалину и смесь коксика с известняком. Коксовую мелочь дают в избытке, чтобы предотвратить окисление железа при охлаждении. Известняк необходим для поглощения серы коксика.
Тигли помещает в печь периодического действия, кольцевую или туннельную, где нагревают до 1100—1200° и выдерживают 50—60 час. Весь процесс, включая нагрев и охлаждение в печи объемом 3000 м3, вмещающей 35 000 тиглей, длится 180 час.
При применении очень чистой руды или концентратов получается высокого качества губчатое железо, в котором содержание пустой породы не превышает 0,5%, 0,1% С и менее 0,02% S.
Губчатое железо используют для получения железного порошка и производства высококачественных сталей. Установки этого типа имеют производительность 15—30 тыс. т в год. Таким способом получают железо в Швеции, Канаде, США и других странах, в том числе в России.
При производстве губчатого железа во вращающихся печах в трубчатую наклонную печь загружают смесь руды (концентрата или агломерата) с коксовой мелочью (или другим низкосортным углем). В печи поддерживается температура не выше 1000—1100° во избежание образования настылей на футеровке печи и сваривания частиц восстановленного железа. При вращении печи шихта непрерывно перемешивается и передвигается к разгрузочному концу.
Избыток углерода в шихте создает восстановительные условия и обеспечивает примерно 90% восстановления окислов железа. Конечный продукт охлаждают и при необходимости дробят. Железо отделяют от остатка восстановителя магнитной сепарацией.
Этот способ не нашел широкого распространения: имеются только полупромышленные установки в Швеции, США и Японии.
1.2 Получение губчатого железа во вращающихся печах, на конвейерных машинах
Применение вращающихся печей позволило перерабатывать различные руды по химическому и фракционному составу, а в качестве топлива применять коксовую мелочь и уголь всех марок, вплоть до лигнита.
Вместе с железорудным сырьем в печь загружают уголь в качестве восстановителя, известняк или доломит в качестве десульфуратора. Восстановитель загружают в печь в количестве, превышающее теоретически необходимое для удаления кислорода руды (часть избыточного восстановителя используется как топливо и для защиты металлического железа от вторичного окисления.)