Файл: Учебное пособие Пермь, 2011 удк 621. 791 Рецензенты др техн наук, проф. Ю. Д. Щицын.doc
ВУЗ: Не указан
Категория: Не указан
Дисциплина: Не указана
Добавлен: 05.05.2024
Просмотров: 105
Скачиваний: 0
ВНИМАНИЕ! Если данный файл нарушает Ваши авторские права, то обязательно сообщите нам.
ажнейшей характеристикой упругой прочности является предел упругости. Теоретический предел упругости максимальное напряжение, до которого образец получает только упругую деформацию, т.е.
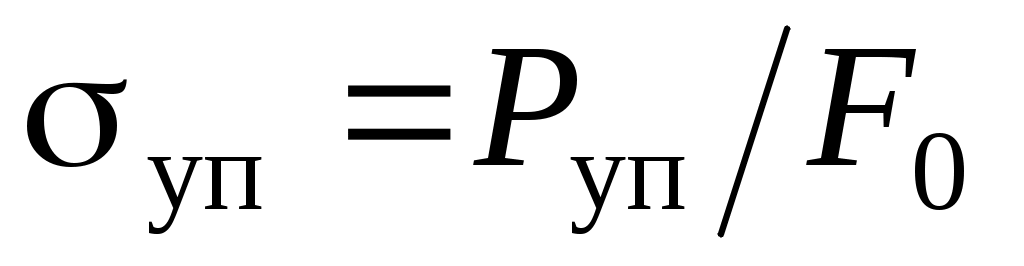
Ввиду трудности определения уп практически пользуются условным пределом упругости, под которым понимают напряжение, вызывающее остаточную деформацию 0,005…0,05 % от начальной длины образца.
Нагрузке в точке а, определяющей конец прямолинейного участка диаграммы растяжения, соответствует предел пропорциональности.
Теоретический предел пропорциональности максимальное напряжение, до которого сохраняется линейная зависимость между напряжением (нагрузкой) и деформацией (см. рис. 9, а)
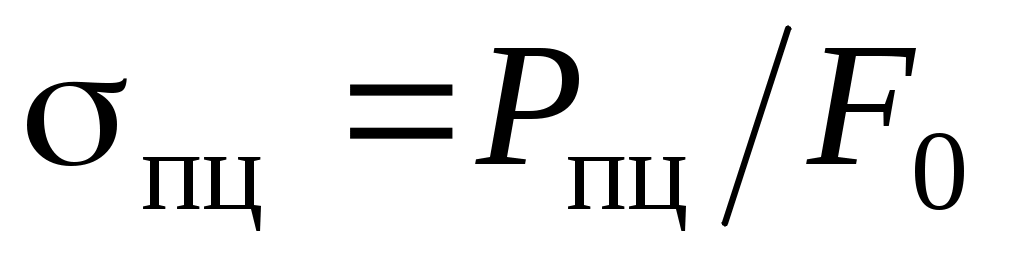
Для большинства материалов теоретические пределы упругости и пропорциональности близки по величине.
Физический предел текучести напряжение, при котором происходит увеличение деформации при постоянной нагрузке
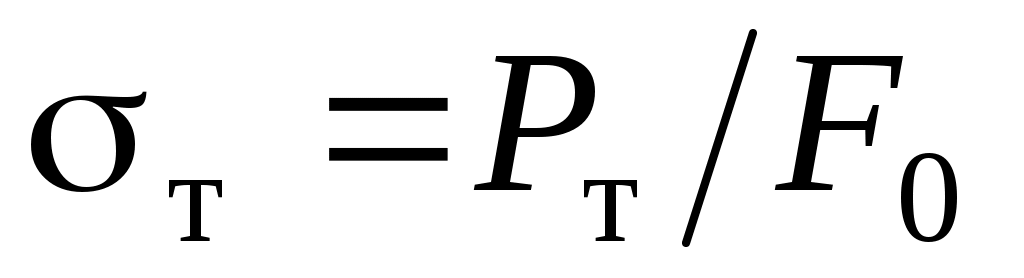
На диаграмме растяжения пределу текучести соответствует горизонтальный участок с d: пластическая деформация (удлинение) «течение» металла при постоянной нагрузке.
Большая часть технических металлов и сплавов не имеет площадки текучести. Для них наиболее часто определяется условный предел текучести, под которым понимают напряжение, вызывающее остаточную деформацию
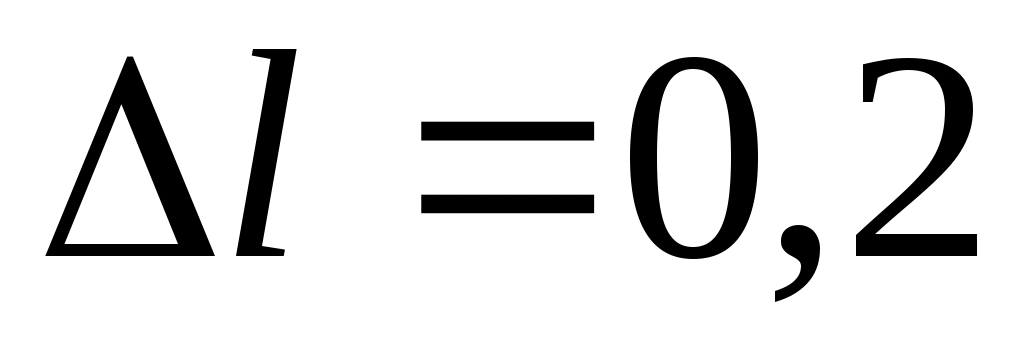
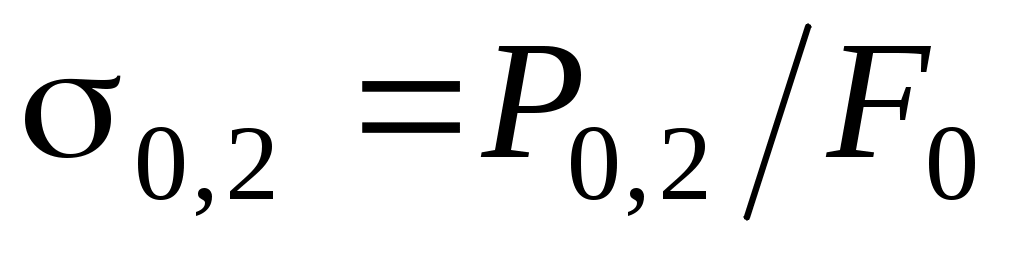
В точке В, в наиболее слабом месте образца начинается образование «шейки» сужения поперечного сечения, деформация из равномерной переходит в местную. Напряжение в материале в этот момент испытания называют пределом прочности.
Предел прочности в напряжение, соответствующее максимальной нагрузке, которую выдерживает образец до разрушения:

Пластичность способность тела (металла) получать остаточное изменение формы и размеров без нарушения сплошности. Пластичность характеризуется
относительным удлинением и относительным сужением, определяемыми при испытаниях на растяжение.
Относительное удлинение
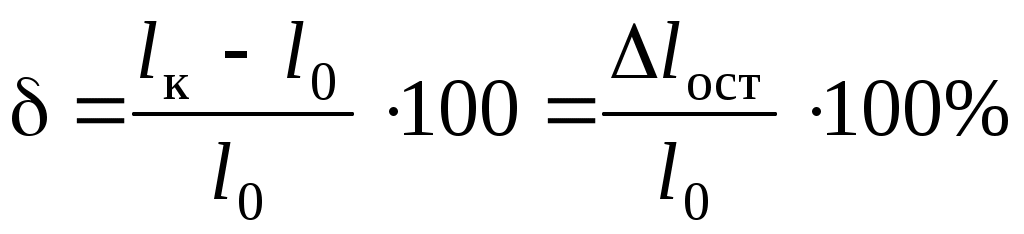
где l0 и lк начальная и конечная длина образца;
lост абсолютное удлинение образца, определяемое измерением
образца после разрыва или по диаграмме растяжения (см. рис. 9).
Относительное сужение
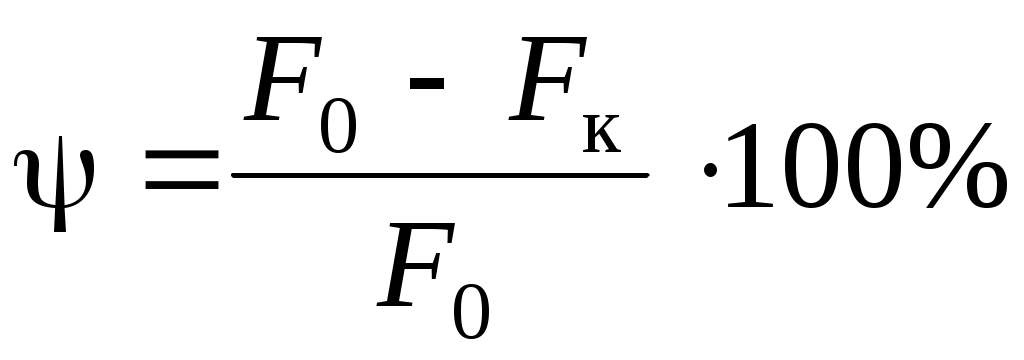
где F0 начальная площадь поперечного сечения образца;
Fк конечная площадь поперечного сужения образца в шейке после
разрыва.
Твердость материала сопротивление проникновению в его поверхность стандартного тела наконечника (индентора), например шарика, конуса и т.п., недеформирующегося при вдавливании.
Твердость измеряют методами Бринеля, Роквелла, Виккерса и др.
Твердость по Бринелю определяют статическим вдавливанием в испытуемую поверхность под нагрузкой Р стального закаленного шарика диаметром D (рис. 10, а). Число твердости НВ определяют отношением нагрузки Р к сферической поверхности отпечатка лунки (шарового сегмента) F диаметром d т.е.
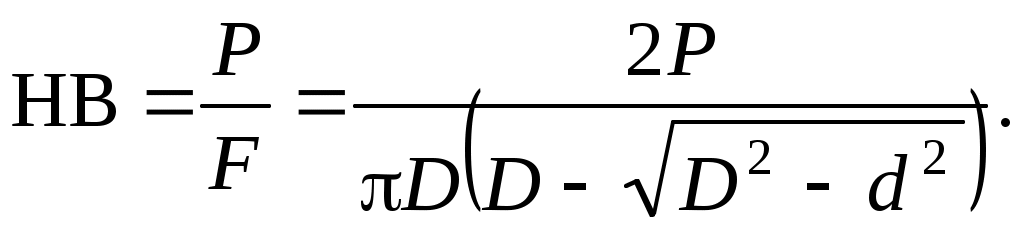
По методу Роквелла (рис. 10, б) в испытуемую поверхность вдавливают индентор алмазный конус с углом при вершине 120 или стальной шарик малого диаметра. Число твердости HR обратно пропорционально глубине внедрения индентора.
В
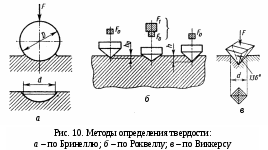
зависимости от шкалы прибора введены следующие обозначения чисел твердости: HRA, HRB и HRC. Шкалы С и А используют при измерении твердых, очень твердых (твердость > 450 НВ) и тонких материалов. Шкала В предназначена для испытания мягких материалов.
Метод Виккерса (рис. 10, в) позволяет измерять твердость как мягких, так и очень твердых материалов. Этим методом можно измерять твердость очень тонких изделий, а также твердость поверхностных слоев, например, при обезуглероживании, поверхностном наклепе, цементации и т.д.
Твердость по Виккерсу определяют путем статического вдавливания в испытуемую поверхность алмазной четырехгранной пирамиды с углом = 136 между противоположными гранями (рис. 10, в). Число твердости
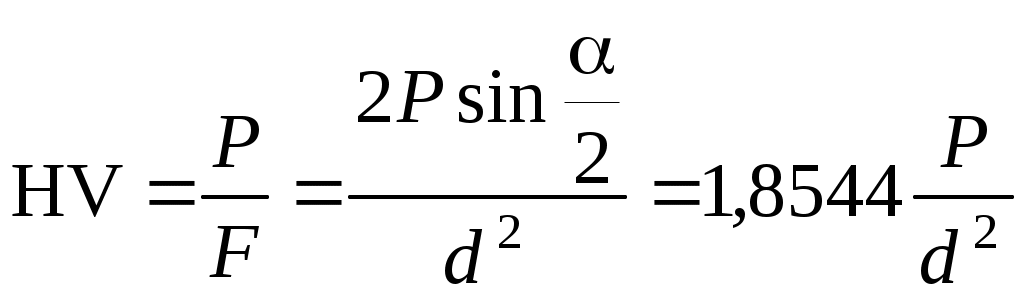
,
где d величина диагонали отпечатка;
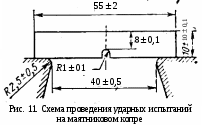
Р = 50…1000 Н (5…100 кгс).
Вязкость является одним из основных механических свойств. Она выражает способность материала поглощать работу внешних сил за счет пластической деформации. Для оценки вязкости материалов и установления их склонности к переходу из вязкого в хрупкое состояние наиболее часто проводят ударные испытания на маятниковом копре надрезанных образцов по схеме (рис. 11). Характеристикой вязкости является ударная вязкость.
Ударная вязкость КС представляет собой работу (необходимую для разрушения), отнесенную к рабочей площади поперечного сечения образца.
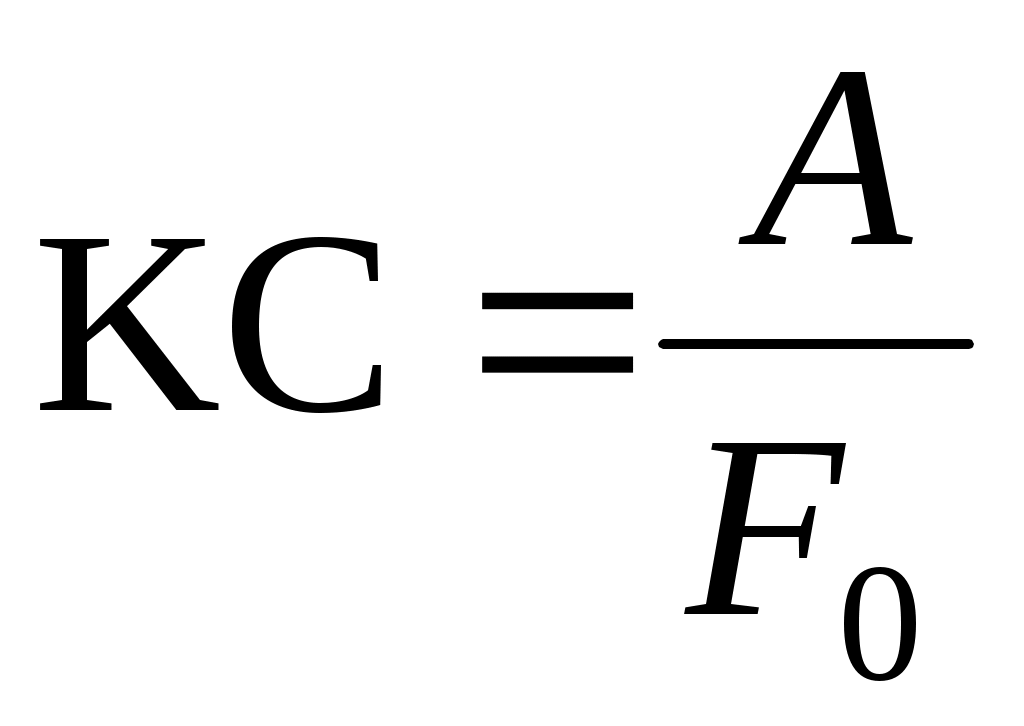
где А работа, затраченная на разрушение образца;
F0 площадь поперечного сечения образца в месте надреза.
В зависимости от формы надреза ударную вязкость обозначают коэффициентом КС с соответствующей последующей буквой (KCV, KCU, KCT).
Усталость. Детали машин могут подвергаться воздействию повторно-переменных (циклических) напряжений. В пределах цикла напряжения могут принимать наибольшее и наименьшее значения. Циклы характеризуются коэффициентом асимметрии
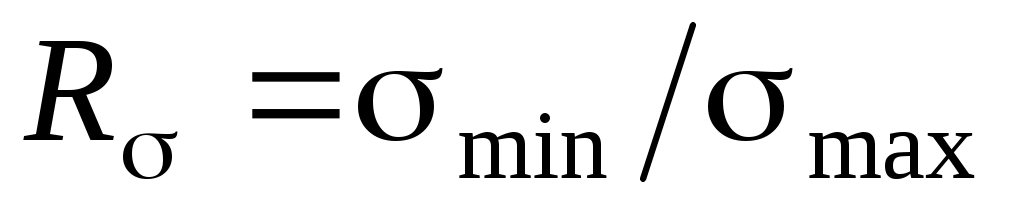
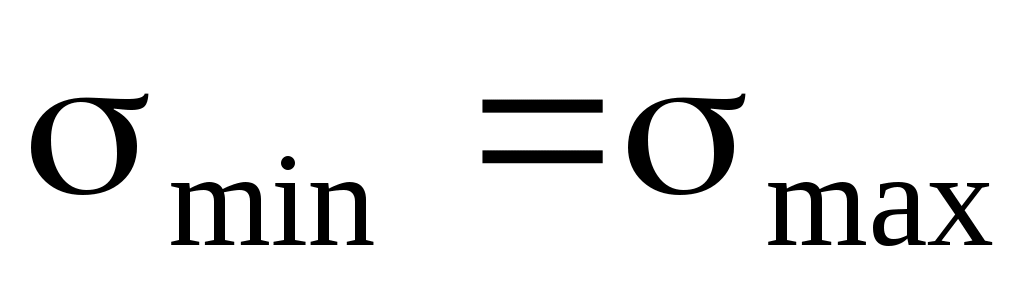
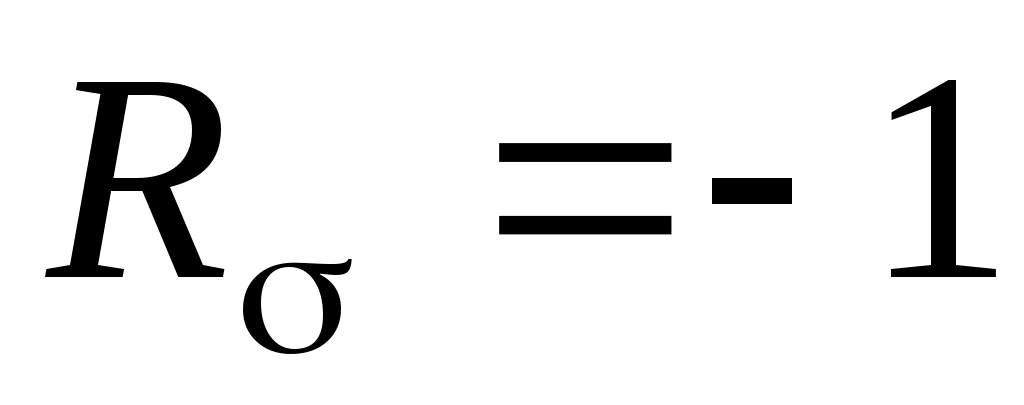
П
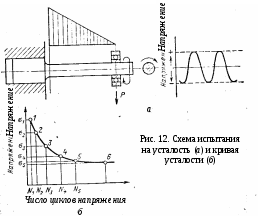
остепенное накопление повреждений в металле, возникающее при действии циклических нагрузок, приводит к образованию трещин и разрушению. Это явление называется усталостью. Свойство же металлов противостоять усталости называется выносливостью.
По результатам специальных испытаний строят кривые усталости (рис. 12, б). Пределу выносливости (1 при симметричном или R несимметричном циклах) соответствует напряжение max, не вызывающее разрушения образцов при бесконечно большом числе циклов нагружений N. Введены базы испытаний: для стали 1 не менее 10106 циклов и цветных сплавов 2 не менее 100106 циклов.
2.2. Физические и химические свойства
Физические свойства характеризуют температуру плавления металлов, их плотность, коэффициент теплового расширения, тепло- и электропроводность, магнитную проницаемость и т.п.
Химические свойства металлов определяются их химической активностью, способностью к химическому взаимодействию с газовыми и жидкими агрессивными средами, расплавленными металлами, коррозионной стойкостью.
2.3. Технологические свойства
Технологические свойства характеризуют способность металлов образовывать отливки, свариваться, подвергаться обработке давлением, резанием и др.
Литейные свойства металлов определяются жидкотекучестью способностью заполнять литейную форму, усадкой сокращением размеров и объема отливки при затвердевании, склонностью к ликвации неоднородности химического состава по сечению отливки, вызванной условиями затвердевания.
Деформируемость это способность принимать необходимую форму под влиянием внешней нагрузки без разрушения и при наименьшем сопротивлении нагрузке.
Свариваемость это способность металлов и сплавов образовывать неразъемные соединения требуемого качества.
Обрабатываемость резанием способность металлов подвергаться обработке режущими инструментами с целью получения деталей определенной формы, размеров и шероховатости поверхности.
2.4. Эксплуатационные свойства
Эксплуатационные свойства характеризуют способность металла работать в определенных условиях. Сюда относятся:
Коррозионная стойкость сопротивление сплава действию агрессивных кислотных и щелочных сред.
Хладостойкость способность сплава сохранять пластические свойства при температурах ниже 0 С.
Жаропрочность способность сплава сохранять механические свойства при высоких температурах.
Жаростойкость способность сплава сопротивляться окислению в газовой среде при высоких температурах.
Антифрикционность способность сплава прирабатываться к другому сплаву.
Износостойкость способность материала сопротивляться изнашиванию. Чем выше износостойкость, тем дольше режущий инструмент будет сохранять свою остроту и размеры.
Теплостойкость свойство материала сохранять свою твердость и режущие способности при высоких температурах.
3. Строение и свойства сплавов