ВУЗ: Не указан
Категория: Не указан
Дисциплина: Не указана
Добавлен: 17.10.2024
Просмотров: 4
Скачиваний: 0
ВНИМАНИЕ! Если данный файл нарушает Ваши авторские права, то обязательно сообщите нам.
Министерство образования и науки РФ
Федеральное государственное образовательное учреждение
Высшего профессионального образования
Волгоградский Государственный Технический Университет (ВолгГТУ)
Факультет «Технологии конструкционных материалов»
Кафедра «Технология материалов»
Контрольная работа
по дисциплине «Основа общей металлургии»
на тему: «Кислород в стали и способы раскисления металла»
Выполнил: студент
Группы М-233
Белоусов М.А.
Проверил:
доцент Руцкий Д.В.
Волгоград 2022
Содержание:
Содержание…………………………………………………………………………2
Раскисление стали………………………………………………………………….3
Способы раскисления стали……………………………………………………….7
Диффузионное раскисление под белым шлаком…………………………………8
Диффузионное раскисление под карбидным шлаком…………………………..10
Раскисление под известково-глиноземистым шлаком………………………….11
Глубинное и диффузионное раскисления металлов…………………………….11
Раскисление алюминием………………………………………………………….11
Раскисление кремнием……………………………………………………………12
Раскисление стали в кислой электропечи………………………………………..12
Раскисление углеродистой стали…………………………………………………13
Раскисление легированной стали…………………………………………………13
Раскисление металла обработкой в вакууме……………………………………..14
Раскисление стали
Высокая концентрация кислорода, растворенного в стали (повышенная активность кислорода), полученная после окончания окислительных процессов, не дает возможности получить качественный слиток, так как понижение температуры металла в процессе кристаллизации приводит к возобновлению реакции окисления углерода [С] + [О] → СОгаз и образованию газовых пузырей, как правило, остающихся в слитке и не всегда заваривающихся при обработке давлением. Неиспользованный при протекании этой реакции кислород выделяется из металлического расплава в конце кристаллизации в виде пленок оксида железа FеО по границам зерен и резко ухудшает механические свойства стали. Это вызывает необходимость проведения раскисления металла. Раскислением называют технологическую операцию, приводящую к снижению концентрации растворенного кислорода (или активности кислорода) в стали до пределов, обеспечивающих требуемое качество готового металла. Содержание растворенного в металле кислорода можно уменьшить или за счет снижения общего содержания кислорода, или путем связывания растворенного кислорода в прочные соединения, не растворяющиеся в стали. Известны следующие способы раскисления стали: осаждающее (ранее не совсем точно называвшееся глубинным) раскисление; экстракционное, или диффузионное, раскисление (раскисление шлаком); раскисление обработкой вакуумом и электрохимическое раскисление. В практике сталеплавильного производства применяют первые два способа, в последнее время все чаще используется и раскисление обработкой вакуумом.
При осаждающем раскислении в металлический расплав вводят элементы-раскислители, обладающие большим химическим сродством к кислороду, чем железо. В результате протекания реакции между растворенным кислородом и раскислителем образуется практически не растворимый в железе оксид, плотность которого меньше плотности жидкой стали, т. е. растворенный кислород переводится в нерастворимый оксид и в расплаве образуется своеобразный «осадок» из нерастворимых оксидов. Полученный «осадок» всплывает или каким-либо другим способом удаляется в шлак. Отсюда и название способа – осаждающее раскисление. Так как раскислители обычно вводят (или пытаются вводить) в глубину металлического расплава, то данный способ раскисления иногда называют глубинным раскислением. В общем виде осаждающее раскисление можно изобразить следующей схемой:
m[R] + n[O] = (RmOn),
где R – элемент-раскиcлитель.
В металлургической практике для осаждающего раскисления стали чаще всего используют (как наиболее дешевые и доступные) марганец в виде ферромарганца, кремний в виде ферросилиция, алюминий, углерод в различном виде. Иногда для раскисления стали используют более дорогие сплавы щелочно-земельных металлов (чаще кальция) и редкоземельных металлов (с преобладанием церия). Все реакции раскисления такими раскислителями идут с выделением тепла, поэтому глубина протекания реакции раскисления увеличивается при понижении температуры (равновесие реакции раскисления сдвигается вправо, в сторону образования дополнительного количества оксида раскислителя). Оксиды элементов-раскислителей, образующиеся в процессе раскисления, в отечественной специальной литературе принято называть продуктами раскисления. Продукты раскисления, образующиеся в жидком металле в процессе технологической операции раскисления, принято называть первичными продуктами раскисления. В течение всего времени существования научно обоснованных технологий сталеплавильного производства специалисты стремились проводить осаждающее раскисление так, чтобы первичные продукты раскисления возможно более полно и возможно быстрее удалялись из металла. Этой проблеме были посвящены многие исследования, результаты которых позволили металлургам быстро и почти полностью удалять из металла первичные продукты раскисления. Но в процессе кристаллизации стали при понижении температуры реакции осаждающего раскисления продолжают идти, при этом образуются «новые» (вторичные) продукты раскисления, которые уже практически не могут удалиться из кристаллизирующего очень вязкого металла и остаются в стали. Поэтому после осаждающего раскисления готовая сталь всегда содержит некоторое количество неметаллических включений – продуктов раскисления, что и является главным недостатком данного способа раскисления. Но благодаря простоте осуществления операции и большой скорости удаления растворенного кислорода из металла осаждающее раскисление остается основным способом раскисления стали.
Для уменьшения количества и размеров вторичных (кристаллизационных) продуктов раскисления очень важно понизить концентрацию растворенного кислорода при раскислении жидкого металла до возможно более низких значений. Остаточная концентрация растворенного кислорода в металле зависит от температуры, концентрации элемента раскислителя и раскислительной способности элемента- раскислителя. Раскислительной способностью элемента-раскислителя принято называть концентрацию растворенного кислорода [O]р (или активность кислорода a[O]), соответствующую конкретной концентрации элемента-раскислителя, при которой он находится в равновесии с кислородом при данной температуре. Данные о раскислительной способности различных раскислителей получают в лабораторных исследованиях, так как в производственных условиях достичь равновесия реакций раскисления не удается. Обычно сравнение раскислительной способности раскислителей проводят при температуре 1600 °С. Для практических нужд удобнее всего использовать данные о раскислительной способности, представленные графически в координатах [O]р – [R] или a[O] – [R], lga[O] и т.д. Следует отметить, что данные о раскислительной способности тех или иных раскислителей, полученные разными исследованиями, часто сильно различаются. Это объясняется тем, что применяется различное оборудование, различные методики исследования; а также различной исходной концентрацией растворенного кислорода и различным составом продуктов раскисления.
Кислород — постоянный спутник железа и стали. Максимальная растворимость кислорода в жидкой стали при температуре ее плавления не превышает 0,22%. С повышением температуры растворимость кислорода в жидкой стали увеличивается. Кислород в стали частично находится в виде раствора, входя, главным образом, в состав неметаллических включений: оксидов — FeO, MnO, SiO2, Al2O3, CaO и ряда их соединений между собой и серой (так называемые силикаты, алюминаты, шпинели, оксисульфиды и пр.).
Кислород ухудшает механические свойства стали, снижает ее ударную вязкость при низких температурах, уменьшает временное сопротивление (прочность на разрыв), повышает неоднородность металла. Комбинированные кислородные и сернистые соединения образуют легкоплавкие неметаллические включения, располагающиеся по границам зерен. В процессе обработки давлением (прокатка или ковка) в таком металле при высоких температурах возможно образование трещин и рванин (явление красноломкости).
Форма, количество и состав кислородных включений в готовой стали зависят от способов раскисления металла, внепечной обработки, разливки и условий затвердевания расплава, а также от характера процессов выплавки стали (основной или кислой). Раскисление стали проводят таким образом, чтобы уменьшить в ней содержание кислорода и неметаллических включений и понизить их вредное влияние на качество металла. Для этого применяют следующие методы раскисления стали: диффузионное — воздействие на металл шлаком с низким содержанием оксидов железа; осадочное — воздействие на металл непосредственно элементами-раскислителями; комбинированное — одновременное воздействие на металл шлаком и элементами- раскислителями.
При равновесии отношение содержания кислорода в железе [О] к содержанию монооксида железа в шлаке (FeO) является постоянной величиной и зависит от основности шлака и температуры. При основности шлака, равной 2, и температуре 1600 °С данное отношение составляет величину 0,005. Если содержание (FeO) в шлаке ниже равновесного, то обеспечивается переход кислорода в виде FeO из металла в шлак. Другими словами, обработкой ванны безжелезистым шлаком можно добиться снижения содержания кислорода в металле.
Присадка в печь порошкообразных материалов — кокса, ферросилиция, алюминия — обеспечивает взаимодействие элементов-рас- кислителей с (FeO) шлака и снижение его концентрации ниже 0,5%. Если конечное содержание (FeO) в шлаке 0,5%, то конечное содержание кислорода в металле в условиях равновесия, определяемое из соотношения [О]кон/0,5 = 0,005, составит: [0]кон = 0,0025%.
Практически равновесие между шлаком и металлом в восстановительный период плавки (доводки) не достигается и содержание кислорода в металле перед выпуском из электропечи колеблется в пределах 0,003—0,012%. При этом уменьшение содержания кислорода в металле происходит, в основном, за счет диффузии кислорода из металла в шлак, поэтому такой способ раскисления называют диффузионным. Диффузионное раскисление ванны металла имеет место при выплавке стали в дуговых печах емкостью до 25 т. Процесс осуществляют под «белым» *(серым) или карбидным шлаком. Белый шлак получают раскислением основного шлака коксом, а затем порошками ферросилиция и алюминия. Карбидный — в результате интенсивного раскисления известкового шлака порошком кокса.
Современные большегрузные дуговые печи оборудуют высокопроизводительными установками для отсоса и очистки отходящих газов, которые при работе создают интенсивный газообмен в рабочем пространстве.
С учетом этого восстановительный шлак требуемых состава, консистенции и раскисленности наводят на жидкой ванне в печи за 15-20 мин до выпуска плавки в ковш путем интенсивной присадки порошков кокса, ферросилиция и алюминия. Период доводки металла (корректировка химического состава стали, нагрев металла и др.) проводят в течение минимального времени под известковым шлаком с основностью 3—4.
Диффузионный способ рафинирования металла позволяет существенно снизить загрязненность стали продуктами раскисления — неметаллическими включениями, так как взаимодействие происходит в шлаке и на поверхности раздела металл-шлак. Однако процесс малопроизводителен. Формирование восстановительного основного шлака к моменту выпуска плавки из большегрузной печи позволяет существенно повысить эффективность взаимодействия фаз в момент слива шлака и металла и тем самым обеспечить высокую степень рафинирования стали от кислорода и серы.
Раскисление стали путем непосредственного ввода в жидкий металл раскислителей в виде кусков или порошка называют глубинным или осадочным. Оно имеет место в металле на разной глубине в зависимости от удельного веса материала-раскислителя, размеров его кусков и способа ввода в металл. Эффект осадочного раскисления металла возрастает с уменьшением температуры плавления веществ- раскислителей и с повышением их растворимости в железе. Сочетание процессов осадочного раскисления металла с диффузионным взаимодействием элементов-раскислителей с кислородом относят к комбинированным методам.
Способы раскисления металла
В восстановительный период электроплавки раскисление металла осуществляют диффузионным способом, при котором реакция раскисления, т. е. связывание кислорода в прочные оксиды, протекает не в металле, а в шлаке, и металл, следовательно, не загрязняется продуктами раскисления. Это основное преимущество диффузионного раскисления перед глубинным. Другим преимуществом диффузионного раскисления является более слабое развитие реакции окисления металла шлаком во время и после выпуска металла из печи. Этим, в частности, объясняется незначительный угар легирующих элементов и раскислителей в электропечах,
К недостаткам диффузионного раскисления относятся:
-
уменьшение производительности печи;
-
снижение стойкости откосов и подины, особенно при раскислении шлака кремнием, так как образующийся кремнезем взаимодействует с основной футеровкой;
-
восстановление фосфора из шлака в металл, что вызывает необходимость тщательного удаления окислительного шлака;
-
повышенный расход раскислителей и необходимость их измельчения;
-
сложность осуществления герметизации печей (особенно большой емкости) для исключения подсоса воздуха.
Несмотря на отмеченные недостатки дуффузионного раскисления, его преимущества, связанные с возможностью получать хорошо раскисленный металл с низким содержание серы и неметаллических включений столь очевидны при производстве качественной и высококачественной стали, что этот способ находит широкое распространение при выплавке стали в электропечах.
Однако для уменьшения отрицательного влияния диффузионного раскисления металла в последнее время получила распространение технология, сочетающая преимущества диффузионного и глубинного раскисления. В этом случае перед началом диффузионного раскисления в металл присаживают кусковые раскислители: ферромарганец, ферросилиций, алюминий и т.д.
Иногда глубинное раскисление применяют и для окончательного раскисления металла.
Для диффузионного раскисления металла широко используют углерод, который дают на шлак чаще всего в виде коксика или электродного боя. При достаточно большом расходе коксика или электродного боя и высоком содержании CaO в шлаке в зоне дуг под электродами образуется карбид кальция по реакции
(CaO) + 3CТ = (CaC2) + {CO}.
Карбид кальция, обладая большим сродством к кислороду, взаимодействует с оксидами железа шлака:
(CaC2) + 3(FeO) = 3[Fe] + 2{СО} + (CaO).
Под карбидным шлаком (>2% CaCr) содержание FeO в шлаке может быть снижено до 0,5%, чему соответствует равновесное содержание кислорода в металле 0,0012% в металле при 1600° С. Подобное содержание кислорода в металле не может быть достигнуто даже при 0,3% Ti. Особенностью углерода как раскислителя является малое влияние температуры на его сродство к кислороду. Относительная дешевизна коксика и электродного боя и хороший эффект раскисления ими объясняет широкое применение их для диффузионного раскисления шлака.
В зависимости от содержания карбида кальция и шлаке, а следовательно, и степени его раскисления шлак восстановительного периода разделяют на белый (до 2% CaC2) и карбидный (>2% CaC2). Под белым шлаком выплавляют конструкционные стали с содержанием углерода ниже 0,35%, под карбидным шлаком — средне- и высокоуглеродистые стали.
Иногда рафинирование металла в окислительный период проводят под известково-глиноземистым, известково-шамотным или магнезиально-глиноземистым шлаками.
Диффузионное раскисление под белым шлаком
После скачивания окислительного шлака в ванне наводят шлак из извести и плавикового шпата в соотношении 3:2 и в количестве 2—4% от массы металла. Жидко-подвижный шлак образуется через 10—15 мин и на него задают восстановительную смесь из извести, плавикового шпата и молотого просеянного кокса или древесного угля с размером частиц не более 0,5—1,0 мм в соотношении 8:2: 1.
В результате раскисления шлака углеродом кокса содержание FeO в нем примерно через 40 мин снижается до 1,5%, и проба шлака после остывания принимает серый цист вместо черного в начале восстановительного периода, когда в шлаке содержится относительно много оксидов железа.
Вследствие возможности науглероживания металла дальнейшее его раскисление проводят кремнием. В шлаковую смесь вводят мелкоизмельченный ферросилиций марок ФС45 и ФС75. Состав шлаковой смеси следующий: четыре части извести, одна часть плавикового шпата, одна часть кокса и одна часть ферросилиция. Раскисление шлака кремнием длится
20 мин. Около 50% Si, вводимого из шлака ферросилицием, усваивается металлом.
Раскисление шлака кремнием иногда производят с начала восстаковительного периода, что устраняет науглероживание металла. Однако содержание кремния в металле возрастает, он реагирует с растворенным в металле кислородом и образующиеся продукты раскисления частично остаются в металле. Поэтому загрязненность металла неметаллическими включениями при такой технологии может возрасти.
Белый шлак имеет обычно следующий состав 55— 65% CaO, 10—20% SiO2, до 1% FeO, 0,4% MnО, 12— 16% MgO, 2-3% Al2O3, 5-10% CaF2, 1% CaS, до 2% CaC2. Проба белого шлака при остывании рассыпается, что связано с присутствием в нем силиката кальция 2 CaO • SiO2, который при 675° С меняет свою модификацию, увеличиваясь при этом в объеме.
Для получения относительно раскисленного металла необходимо выдерживать металл под белым шлаком
1 ч, периодически присаживая некоторое количество раскислительной смеси с коксом или ферросилицием. Хороший белый шлак пенится в печи, густой шлак затрудняет нагрев металла и протекание диффузионных процессов. Поэтому необходимо непрерывно поддерживать нормальную консистенцию шлака, своевременно увеличивая в смеси количество плавикового шпата.
Иногда увеличение вязкости шлака вызывается повышением содержания MgO в шлаке в результате разрушения откосов и подины. В этом случае шлак необходимо скачать и навести новый. Жидкий шлак исправляют присадкой извести.
Диффузионное раскисление под карбидным шлаком
При проведении восстановительного периода под карбидным шлаком металл вначале покрывают шлаковой смесью того же состава, что и при раскислении под белым шлаком. После образования равномерного слоя жидкоподвижного шлака в печь дают смесь из извести, плавикового шпата и молотого кокса в соотношении 3:1:1. Общее количество шлака в восстановительный период составляет 4% в электропечах большой емкости и 7—8% в печах малой емкости (от массы металла).
Карбид кальция образуется в зоне дуг с большим поглощением тепла, поэтому печь хорошо уплотняют и к ней подводят повышенную мощность. Печь не открывают в течение 20—30 мин. Внешним признаком образования карбидного шлака является выбивание из-под заслонок черного дыма.
Карбид кальция из зоны дуг разносится по всему объему шлака. Он является сильным раскислителем, взаимодействуя с FeO по реакции (CaC2) + 3(FeO) = 3[Fe] + 2{СО} + (CaO). Карбид кальция частично восстанавливает кремний из оксида кремния шлака. Поэтому в процессе раскисления металла карбидным шлаком на 0,05—0,1% возрастает содержание кремния в металле. Карбидный шлак плотно прилипает к ложке, а при замачивании ошлакованного инструмента в воде чувствуется специфический запах ацетилена.
Раскисление под карбидным шлаком продолжается не менее 1 ч. Для поддержания в шлаке необходимого содержания карбида кальция в печь периодически задают молотый кокс с известью и плавиковым шпатом, если необходимо уменьшить вязкость шлака.
Существенным недостатком ведения плавки под карбидным шлаком является заметное науглероживание металла в печи и во время выпуска, а также прилипание карбидного шлака к металлу, что приводит иногда к появлению в готовом металле относительно крупных шлаковых включений. Для устранения этого явления карбидный шлак примерно за 30 мин до выпуска переводят в белый. Для этого в печь присаживают известь с плавиковым шпатом, при этом увеличивается общее количество шлака и снижается содержание в нем карбида кальция. Иногда дополнительно открывают рабочее окно, способствуя таким образом, окислению карбида кальция. Если и после этого шлак остается карбидным, то часть шлака (∼1/3) удаляют из печи и забрасывают в печь шлаковую смесь из извести, плавикового шпата и шамотного боя.
Карбидный шлак имеет следующий химический состав: 55-65% CaO, 10-15% SiO2, до 0,5% FeO, до 0,3% MnO, 6—10% MgO, 2-3% Al2O3, 1—2% CaS, 2— 4% CaC2, 8—12% CaF2.
Основное отличие карбидного шлака от белого по составу заключается в несколько более низком в первом шлаке содержании оксидов железа и марганца, а также повышенном содержании карбида кальция.
Раскисление под известково-глиноземистым шлаком
При выплавке нержавеющих и им подобных сталей диффузионное раскисление металла в восстановительный период проводят под известково-глиноземистым или шамотным шлаком. В этом случае устраняется возможность науглероживания металла. Например, на Златоустовском металлургическом заводе после скачивания окислительного шлака наводится новый шлак из извести и отработанного флюса электрошлакового производства (
60% CaF2 и
40% Al2O3) в соотношении 2:1 в количестве
2% от массы металла. Для раскисления известково-глиноземистого шлака применяют порошкообразный ферросилиций, алюминий и силикокальций.
Министерство образования и науки РФ
Федеральное государственное образовательное учреждение
Высшего профессионального образования
Волгоградский Государственный Технический Университет (ВолгГТУ)
Факультет «Технологии конструкционных материалов»
Кафедра «Технология материалов»
Контрольная работа
по дисциплине «Основа общей металлургии»
на тему: «Кислород в стали и способы раскисления металла»
Выполнил: студент
Группы М-233
Белоусов М.А.
Проверил:
доцент Руцкий Д.В.
Волгоград 2022
Содержание:
Содержание…………………………………………………………………………2
Раскисление стали………………………………………………………………….3
Способы раскисления стали……………………………………………………….7
Диффузионное раскисление под белым шлаком…………………………………8
Диффузионное раскисление под карбидным шлаком…………………………..10
Раскисление под известково-глиноземистым шлаком………………………….11
Глубинное и диффузионное раскисления металлов…………………………….11
Раскисление алюминием………………………………………………………….11
Раскисление кремнием……………………………………………………………12
Раскисление стали в кислой электропечи………………………………………..12
Раскисление углеродистой стали…………………………………………………13
Раскисление легированной стали…………………………………………………13
Раскисление металла обработкой в вакууме……………………………………..14
Раскисление стали
Высокая концентрация кислорода, растворенного в стали (повышенная активность кислорода), полученная после окончания окислительных процессов, не дает возможности получить качественный слиток, так как понижение температуры металла в процессе кристаллизации приводит к возобновлению реакции окисления углерода [С] + [О] → СОгаз и образованию газовых пузырей, как правило, остающихся в слитке и не всегда заваривающихся при обработке давлением. Неиспользованный при протекании этой реакции кислород выделяется из металлического расплава в конце кристаллизации в виде пленок оксида железа FеО по границам зерен и резко ухудшает механические свойства стали. Это вызывает необходимость проведения раскисления металла. Раскислением называют технологическую операцию, приводящую к снижению концентрации растворенного кислорода (или активности кислорода) в стали до пределов, обеспечивающих требуемое качество готового металла. Содержание растворенного в металле кислорода можно уменьшить или за счет снижения общего содержания кислорода, или путем связывания растворенного кислорода в прочные соединения, не растворяющиеся в стали. Известны следующие способы раскисления стали: осаждающее (ранее не совсем точно называвшееся глубинным) раскисление; экстракционное, или диффузионное, раскисление (раскисление шлаком); раскисление обработкой вакуумом и электрохимическое раскисление. В практике сталеплавильного производства применяют первые два способа, в последнее время все чаще используется и раскисление обработкой вакуумом.
При осаждающем раскислении в металлический расплав вводят элементы-раскислители, обладающие большим химическим сродством к кислороду, чем железо. В результате протекания реакции между растворенным кислородом и раскислителем образуется практически не растворимый в железе оксид, плотность которого меньше плотности жидкой стали, т. е. растворенный кислород переводится в нерастворимый оксид и в расплаве образуется своеобразный «осадок» из нерастворимых оксидов. Полученный «осадок» всплывает или каким-либо другим способом удаляется в шлак. Отсюда и название способа – осаждающее раскисление. Так как раскислители обычно вводят (или пытаются вводить) в глубину металлического расплава, то данный способ раскисления иногда называют глубинным раскислением. В общем виде осаждающее раскисление можно изобразить следующей схемой:
m[R] + n[O] = (RmOn),
где R – элемент-раскиcлитель.
В металлургической практике для осаждающего раскисления стали чаще всего используют (как наиболее дешевые и доступные) марганец в виде ферромарганца, кремний в виде ферросилиция, алюминий, углерод в различном виде. Иногда для раскисления стали используют более дорогие сплавы щелочно-земельных металлов (чаще кальция) и редкоземельных металлов (с преобладанием церия). Все реакции раскисления такими раскислителями идут с выделением тепла, поэтому глубина протекания реакции раскисления увеличивается при понижении температуры (равновесие реакции раскисления сдвигается вправо, в сторону образования дополнительного количества оксида раскислителя). Оксиды элементов-раскислителей, образующиеся в процессе раскисления, в отечественной специальной литературе принято называть продуктами раскисления. Продукты раскисления, образующиеся в жидком металле в процессе технологической операции раскисления, принято называть первичными продуктами раскисления. В течение всего времени существования научно обоснованных технологий сталеплавильного производства специалисты стремились проводить осаждающее раскисление так, чтобы первичные продукты раскисления возможно более полно и возможно быстрее удалялись из металла. Этой проблеме были посвящены многие исследования, результаты которых позволили металлургам быстро и почти полностью удалять из металла первичные продукты раскисления. Но в процессе кристаллизации стали при понижении температуры реакции осаждающего раскисления продолжают идти, при этом образуются «новые» (вторичные) продукты раскисления, которые уже практически не могут удалиться из кристаллизирующего очень вязкого металла и остаются в стали. Поэтому после осаждающего раскисления готовая сталь всегда содержит некоторое количество неметаллических включений – продуктов раскисления, что и является главным недостатком данного способа раскисления. Но благодаря простоте осуществления операции и большой скорости удаления растворенного кислорода из металла осаждающее раскисление остается основным способом раскисления стали.
Для уменьшения количества и размеров вторичных (кристаллизационных) продуктов раскисления очень важно понизить концентрацию растворенного кислорода при раскислении жидкого металла до возможно более низких значений. Остаточная концентрация растворенного кислорода в металле зависит от температуры, концентрации элемента раскислителя и раскислительной способности элемента- раскислителя. Раскислительной способностью элемента-раскислителя принято называть концентрацию растворенного кислорода [O]р (или активность кислорода a[O]), соответствующую конкретной концентрации элемента-раскислителя, при которой он находится в равновесии с кислородом при данной температуре. Данные о раскислительной способности различных раскислителей получают в лабораторных исследованиях, так как в производственных условиях достичь равновесия реакций раскисления не удается. Обычно сравнение раскислительной способности раскислителей проводят при температуре 1600 °С. Для практических нужд удобнее всего использовать данные о раскислительной способности, представленные графически в координатах [O]р – [R] или a[O] – [R], lga[O] и т.д. Следует отметить, что данные о раскислительной способности тех или иных раскислителей, полученные разными исследованиями, часто сильно различаются. Это объясняется тем, что применяется различное оборудование, различные методики исследования; а также различной исходной концентрацией растворенного кислорода и различным составом продуктов раскисления.
Кислород — постоянный спутник железа и стали. Максимальная растворимость кислорода в жидкой стали при температуре ее плавления не превышает 0,22%. С повышением температуры растворимость кислорода в жидкой стали увеличивается. Кислород в стали частично находится в виде раствора, входя, главным образом, в состав неметаллических включений: оксидов — FeO, MnO, SiO2, Al2O3, CaO и ряда их соединений между собой и серой (так называемые силикаты, алюминаты, шпинели, оксисульфиды и пр.).
Кислород ухудшает механические свойства стали, снижает ее ударную вязкость при низких температурах, уменьшает временное сопротивление (прочность на разрыв), повышает неоднородность металла. Комбинированные кислородные и сернистые соединения образуют легкоплавкие неметаллические включения, располагающиеся по границам зерен. В процессе обработки давлением (прокатка или ковка) в таком металле при высоких температурах возможно образование трещин и рванин (явление красноломкости).
Форма, количество и состав кислородных включений в готовой стали зависят от способов раскисления металла, внепечной обработки, разливки и условий затвердевания расплава, а также от характера процессов выплавки стали (основной или кислой). Раскисление стали проводят таким образом, чтобы уменьшить в ней содержание кислорода и неметаллических включений и понизить их вредное влияние на качество металла. Для этого применяют следующие методы раскисления стали: диффузионное — воздействие на металл шлаком с низким содержанием оксидов железа; осадочное — воздействие на металл непосредственно элементами-раскислителями; комбинированное — одновременное воздействие на металл шлаком и элементами- раскислителями.
При равновесии отношение содержания кислорода в железе [О] к содержанию монооксида железа в шлаке (FeO) является постоянной величиной и зависит от основности шлака и температуры. При основности шлака, равной 2, и температуре 1600 °С данное отношение составляет величину 0,005. Если содержание (FeO) в шлаке ниже равновесного, то обеспечивается переход кислорода в виде FeO из металла в шлак. Другими словами, обработкой ванны безжелезистым шлаком можно добиться снижения содержания кислорода в металле.
Присадка в печь порошкообразных материалов — кокса, ферросилиция, алюминия — обеспечивает взаимодействие элементов-рас- кислителей с (FeO) шлака и снижение его концентрации ниже 0,5%. Если конечное содержание (FeO) в шлаке 0,5%, то конечное содержание кислорода в металле в условиях равновесия, определяемое из соотношения [О]кон/0,5 = 0,005, составит: [0]кон = 0,0025%.
Практически равновесие между шлаком и металлом в восстановительный период плавки (доводки) не достигается и содержание кислорода в металле перед выпуском из электропечи колеблется в пределах 0,003—0,012%. При этом уменьшение содержания кислорода в металле происходит, в основном, за счет диффузии кислорода из металла в шлак, поэтому такой способ раскисления называют диффузионным. Диффузионное раскисление ванны металла имеет место при выплавке стали в дуговых печах емкостью до 25 т. Процесс осуществляют под «белым» *(серым) или карбидным шлаком. Белый шлак получают раскислением основного шлака коксом, а затем порошками ферросилиция и алюминия. Карбидный — в результате интенсивного раскисления известкового шлака порошком кокса.
Современные большегрузные дуговые печи оборудуют высокопроизводительными установками для отсоса и очистки отходящих газов, которые при работе создают интенсивный газообмен в рабочем пространстве.
С учетом этого восстановительный шлак требуемых состава, консистенции и раскисленности наводят на жидкой ванне в печи за 15-20 мин до выпуска плавки в ковш путем интенсивной присадки порошков кокса, ферросилиция и алюминия. Период доводки металла (корректировка химического состава стали, нагрев металла и др.) проводят в течение минимального времени под известковым шлаком с основностью 3—4.
Диффузионный способ рафинирования металла позволяет существенно снизить загрязненность стали продуктами раскисления — неметаллическими включениями, так как взаимодействие происходит в шлаке и на поверхности раздела металл-шлак. Однако процесс малопроизводителен. Формирование восстановительного основного шлака к моменту выпуска плавки из большегрузной печи позволяет существенно повысить эффективность взаимодействия фаз в момент слива шлака и металла и тем самым обеспечить высокую степень рафинирования стали от кислорода и серы.
Раскисление стали путем непосредственного ввода в жидкий металл раскислителей в виде кусков или порошка называют глубинным или осадочным. Оно имеет место в металле на разной глубине в зависимости от удельного веса материала-раскислителя, размеров его кусков и способа ввода в металл. Эффект осадочного раскисления металла возрастает с уменьшением температуры плавления веществ- раскислителей и с повышением их растворимости в железе. Сочетание процессов осадочного раскисления металла с диффузионным взаимодействием элементов-раскислителей с кислородом относят к комбинированным методам.
Способы раскисления металла
В восстановительный период электроплавки раскисление металла осуществляют диффузионным способом, при котором реакция раскисления, т. е. связывание кислорода в прочные оксиды, протекает не в металле, а в шлаке, и металл, следовательно, не загрязняется продуктами раскисления. Это основное преимущество диффузионного раскисления перед глубинным. Другим преимуществом диффузионного раскисления является более слабое развитие реакции окисления металла шлаком во время и после выпуска металла из печи. Этим, в частности, объясняется незначительный угар легирующих элементов и раскислителей в электропечах,
К недостаткам диффузионного раскисления относятся:
-
уменьшение производительности печи;
-
снижение стойкости откосов и подины, особенно при раскислении шлака кремнием, так как образующийся кремнезем взаимодействует с основной футеровкой;
-
восстановление фосфора из шлака в металл, что вызывает необходимость тщательного удаления окислительного шлака;
-
повышенный расход раскислителей и необходимость их измельчения;
-
сложность осуществления герметизации печей (особенно большой емкости) для исключения подсоса воздуха.
Несмотря на отмеченные недостатки дуффузионного раскисления, его преимущества, связанные с возможностью получать хорошо раскисленный металл с низким содержание серы и неметаллических включений столь очевидны при производстве качественной и высококачественной стали, что этот способ находит широкое распространение при выплавке стали в электропечах.
Однако для уменьшения отрицательного влияния диффузионного раскисления металла в последнее время получила распространение технология, сочетающая преимущества диффузионного и глубинного раскисления. В этом случае перед началом диффузионного раскисления в металл присаживают кусковые раскислители: ферромарганец, ферросилиций, алюминий и т.д.
Иногда глубинное раскисление применяют и для окончательного раскисления металла.
Для диффузионного раскисления металла широко используют углерод, который дают на шлак чаще всего в виде коксика или электродного боя. При достаточно большом расходе коксика или электродного боя и высоком содержании CaO в шлаке в зоне дуг под электродами образуется карбид кальция по реакции
(CaO) + 3CТ = (CaC2) + {CO}.
Карбид кальция, обладая большим сродством к кислороду, взаимодействует с оксидами железа шлака:
(CaC2) + 3(FeO) = 3[Fe] + 2{СО} + (CaO).
Под карбидным шлаком (>2% CaCr) содержание FeO в шлаке может быть снижено до 0,5%, чему соответствует равновесное содержание кислорода в металле 0,0012% в металле при 1600° С. Подобное содержание кислорода в металле не может быть достигнуто даже при 0,3% Ti. Особенностью углерода как раскислителя является малое влияние температуры на его сродство к кислороду. Относительная дешевизна коксика и электродного боя и хороший эффект раскисления ими объясняет широкое применение их для диффузионного раскисления шлака.
В зависимости от содержания карбида кальция и шлаке, а следовательно, и степени его раскисления шлак восстановительного периода разделяют на белый (до 2% CaC2) и карбидный (>2% CaC2). Под белым шлаком выплавляют конструкционные стали с содержанием углерода ниже 0,35%, под карбидным шлаком — средне- и высокоуглеродистые стали.
Иногда рафинирование металла в окислительный период проводят под известково-глиноземистым, известково-шамотным или магнезиально-глиноземистым шлаками.
Диффузионное раскисление под белым шлаком
После скачивания окислительного шлака в ванне наводят шлак из извести и плавикового шпата в соотношении 3:2 и в количестве 2—4% от массы металла. Жидко-подвижный шлак образуется через 10—15 мин и на него задают восстановительную смесь из извести, плавикового шпата и молотого просеянного кокса или древесного угля с размером частиц не более 0,5—1,0 мм в соотношении 8:2: 1.
В результате раскисления шлака углеродом кокса содержание FeO в нем примерно через 40 мин снижается до 1,5%, и проба шлака после остывания принимает серый цист вместо черного в начале восстановительного периода, когда в шлаке содержится относительно много оксидов железа.
Вследствие возможности науглероживания металла дальнейшее его раскисление проводят кремнием. В шлаковую смесь вводят мелкоизмельченный ферросилиций марок ФС45 и ФС75. Состав шлаковой смеси следующий: четыре части извести, одна часть плавикового шпата, одна часть кокса и одна часть ферросилиция. Раскисление шлака кремнием длится
20 мин. Около 50% Si, вводимого из шлака ферросилицием, усваивается металлом.
Раскисление шлака кремнием иногда производят с начала восстаковительного периода, что устраняет науглероживание металла. Однако содержание кремния в металле возрастает, он реагирует с растворенным в металле кислородом и образующиеся продукты раскисления частично остаются в металле. Поэтому загрязненность металла неметаллическими включениями при такой технологии может возрасти.
Белый шлак имеет обычно следующий состав 55— 65% CaO, 10—20% SiO2, до 1% FeO, 0,4% MnО, 12— 16% MgO, 2-3% Al2O3, 5-10% CaF2, 1% CaS, до 2% CaC2. Проба белого шлака при остывании рассыпается, что связано с присутствием в нем силиката кальция 2 CaO • SiO2, который при 675° С меняет свою модификацию, увеличиваясь при этом в объеме.
Для получения относительно раскисленного металла необходимо выдерживать металл под белым шлаком
1 ч, периодически присаживая некоторое количество раскислительной смеси с коксом или ферросилицием. Хороший белый шлак пенится в печи, густой шлак затрудняет нагрев металла и протекание диффузионных процессов. Поэтому необходимо непрерывно поддерживать нормальную консистенцию шлака, своевременно увеличивая в смеси количество плавикового шпата.
Иногда увеличение вязкости шлака вызывается повышением содержания MgO в шлаке в результате разрушения откосов и подины. В этом случае шлак необходимо скачать и навести новый. Жидкий шлак исправляют присадкой извести.
Диффузионное раскисление под карбидным шлаком
При проведении восстановительного периода под карбидным шлаком металл вначале покрывают шлаковой смесью того же состава, что и при раскислении под белым шлаком. После образования равномерного слоя жидкоподвижного шлака в печь дают смесь из извести, плавикового шпата и молотого кокса в соотношении 3:1:1. Общее количество шлака в восстановительный период составляет 4% в электропечах большой емкости и 7—8% в печах малой емкости (от массы металла).
Карбид кальция образуется в зоне дуг с большим поглощением тепла, поэтому печь хорошо уплотняют и к ней подводят повышенную мощность. Печь не открывают в течение 20—30 мин. Внешним признаком образования карбидного шлака является выбивание из-под заслонок черного дыма.
Карбид кальция из зоны дуг разносится по всему объему шлака. Он является сильным раскислителем, взаимодействуя с FeO по реакции (CaC2) + 3(FeO) = 3[Fe] + 2{СО} + (CaO). Карбид кальция частично восстанавливает кремний из оксида кремния шлака. Поэтому в процессе раскисления металла карбидным шлаком на 0,05—0,1% возрастает содержание кремния в металле. Карбидный шлак плотно прилипает к ложке, а при замачивании ошлакованного инструмента в воде чувствуется специфический запах ацетилена.
Раскисление под карбидным шлаком продолжается не менее 1 ч. Для поддержания в шлаке необходимого содержания карбида кальция в печь периодически задают молотый кокс с известью и плавиковым шпатом, если необходимо уменьшить вязкость шлака.
Существенным недостатком ведения плавки под карбидным шлаком является заметное науглероживание металла в печи и во время выпуска, а также прилипание карбидного шлака к металлу, что приводит иногда к появлению в готовом металле относительно крупных шлаковых включений. Для устранения этого явления карбидный шлак примерно за 30 мин до выпуска переводят в белый. Для этого в печь присаживают известь с плавиковым шпатом, при этом увеличивается общее количество шлака и снижается содержание в нем карбида кальция. Иногда дополнительно открывают рабочее окно, способствуя таким образом, окислению карбида кальция. Если и после этого шлак остается карбидным, то часть шлака (∼1/3) удаляют из печи и забрасывают в печь шлаковую смесь из извести, плавикового шпата и шамотного боя.
Карбидный шлак имеет следующий химический состав: 55-65% CaO, 10-15% SiO2, до 0,5% FeO, до 0,3% MnO, 6—10% MgO, 2-3% Al2O3, 1—2% CaS, 2— 4% CaC2, 8—12% CaF2.
Основное отличие карбидного шлака от белого по составу заключается в несколько более низком в первом шлаке содержании оксидов железа и марганца, а также повышенном содержании карбида кальция.
Раскисление под известково-глиноземистым шлаком
При выплавке нержавеющих и им подобных сталей диффузионное раскисление металла в восстановительный период проводят под известково-глиноземистым или шамотным шлаком. В этом случае устраняется возможность науглероживания металла. Например, на Златоустовском металлургическом заводе после скачивания окислительного шлака наводится новый шлак из извести и отработанного флюса электрошлакового производства (
60% CaF2 и
Министерство образования и науки РФ
Федеральное государственное образовательное учреждение
Высшего профессионального образования
Волгоградский Государственный Технический Университет (ВолгГТУ)
Факультет «Технологии конструкционных материалов»
Кафедра «Технология материалов»
Контрольная работа
по дисциплине «Основа общей металлургии»
на тему: «Кислород в стали и способы раскисления металла»
Выполнил: студент
Группы М-233
Белоусов М.А.
Проверил:
доцент Руцкий Д.В.
Волгоград 2022
Содержание:
Содержание…………………………………………………………………………2
Раскисление стали………………………………………………………………….3
Способы раскисления стали……………………………………………………….7
Диффузионное раскисление под белым шлаком…………………………………8
Диффузионное раскисление под карбидным шлаком…………………………..10
Раскисление под известково-глиноземистым шлаком………………………….11
Глубинное и диффузионное раскисления металлов…………………………….11
Раскисление алюминием………………………………………………………….11
Раскисление кремнием……………………………………………………………12
Раскисление стали в кислой электропечи………………………………………..12
Раскисление углеродистой стали…………………………………………………13
Раскисление легированной стали…………………………………………………13
Раскисление металла обработкой в вакууме……………………………………..14
Раскисление стали
Высокая концентрация кислорода, растворенного в стали (повышенная активность кислорода), полученная после окончания окислительных процессов, не дает возможности получить качественный слиток, так как понижение температуры металла в процессе кристаллизации приводит к возобновлению реакции окисления углерода [С] + [О] → СОгаз и образованию газовых пузырей, как правило, остающихся в слитке и не всегда заваривающихся при обработке давлением. Неиспользованный при протекании этой реакции кислород выделяется из металлического расплава в конце кристаллизации в виде пленок оксида железа FеО по границам зерен и резко ухудшает механические свойства стали. Это вызывает необходимость проведения раскисления металла. Раскислением называют технологическую операцию, приводящую к снижению концентрации растворенного кислорода (или активности кислорода) в стали до пределов, обеспечивающих требуемое качество готового металла. Содержание растворенного в металле кислорода можно уменьшить или за счет снижения общего содержания кислорода, или путем связывания растворенного кислорода в прочные соединения, не растворяющиеся в стали. Известны следующие способы раскисления стали: осаждающее (ранее не совсем точно называвшееся глубинным) раскисление; экстракционное, или диффузионное, раскисление (раскисление шлаком); раскисление обработкой вакуумом и электрохимическое раскисление. В практике сталеплавильного производства применяют первые два способа, в последнее время все чаще используется и раскисление обработкой вакуумом.
При осаждающем раскислении в металлический расплав вводят элементы-раскислители, обладающие большим химическим сродством к кислороду, чем железо. В результате протекания реакции между растворенным кислородом и раскислителем образуется практически не растворимый в железе оксид, плотность которого меньше плотности жидкой стали, т. е. растворенный кислород переводится в нерастворимый оксид и в расплаве образуется своеобразный «осадок» из нерастворимых оксидов. Полученный «осадок» всплывает или каким-либо другим способом удаляется в шлак. Отсюда и название способа – осаждающее раскисление. Так как раскислители обычно вводят (или пытаются вводить) в глубину металлического расплава, то данный способ раскисления иногда называют глубинным раскислением. В общем виде осаждающее раскисление можно изобразить следующей схемой:
m[R] + n[O] = (RmOn),
где R – элемент-раскиcлитель.
В металлургической практике для осаждающего раскисления стали чаще всего используют (как наиболее дешевые и доступные) марганец в виде ферромарганца, кремний в виде ферросилиция, алюминий, углерод в различном виде. Иногда для раскисления стали используют более дорогие сплавы щелочно-земельных металлов (чаще кальция) и редкоземельных металлов (с преобладанием церия). Все реакции раскисления такими раскислителями идут с выделением тепла, поэтому глубина протекания реакции раскисления увеличивается при понижении температуры (равновесие реакции раскисления сдвигается вправо, в сторону образования дополнительного количества оксида раскислителя). Оксиды элементов-раскислителей, образующиеся в процессе раскисления, в отечественной специальной литературе принято называть продуктами раскисления. Продукты раскисления, образующиеся в жидком металле в процессе технологической операции раскисления, принято называть первичными продуктами раскисления. В течение всего времени существования научно обоснованных технологий сталеплавильного производства специалисты стремились проводить осаждающее раскисление так, чтобы первичные продукты раскисления возможно более полно и возможно быстрее удалялись из металла. Этой проблеме были посвящены многие исследования, результаты которых позволили металлургам быстро и почти полностью удалять из металла первичные продукты раскисления. Но в процессе кристаллизации стали при понижении температуры реакции осаждающего раскисления продолжают идти, при этом образуются «новые» (вторичные) продукты раскисления, которые уже практически не могут удалиться из кристаллизирующего очень вязкого металла и остаются в стали. Поэтому после осаждающего раскисления готовая сталь всегда содержит некоторое количество неметаллических включений – продуктов раскисления, что и является главным недостатком данного способа раскисления. Но благодаря простоте осуществления операции и большой скорости удаления растворенного кислорода из металла осаждающее раскисление остается основным способом раскисления стали.
Для уменьшения количества и размеров вторичных (кристаллизационных) продуктов раскисления очень важно понизить концентрацию растворенного кислорода при раскислении жидкого металла до возможно более низких значений. Остаточная концентрация растворенного кислорода в металле зависит от температуры, концентрации элемента раскислителя и раскислительной способности элемента- раскислителя. Раскислительной способностью элемента-раскислителя принято называть концентрацию растворенного кислорода [O]р (или активность кислорода a[O]), соответствующую конкретной концентрации элемента-раскислителя, при которой он находится в равновесии с кислородом при данной температуре. Данные о раскислительной способности различных раскислителей получают в лабораторных исследованиях, так как в производственных условиях достичь равновесия реакций раскисления не удается. Обычно сравнение раскислительной способности раскислителей проводят при температуре 1600 °С. Для практических нужд удобнее всего использовать данные о раскислительной способности, представленные графически в координатах [O]р – [R] или a[O] – [R], lga[O] и т.д. Следует отметить, что данные о раскислительной способности тех или иных раскислителей, полученные разными исследованиями, часто сильно различаются. Это объясняется тем, что применяется различное оборудование, различные методики исследования; а также различной исходной концентрацией растворенного кислорода и различным составом продуктов раскисления.
Кислород — постоянный спутник железа и стали. Максимальная растворимость кислорода в жидкой стали при температуре ее плавления не превышает 0,22%. С повышением температуры растворимость кислорода в жидкой стали увеличивается. Кислород в стали частично находится в виде раствора, входя, главным образом, в состав неметаллических включений: оксидов — FeO, MnO, SiO2, Al2O3, CaO и ряда их соединений между собой и серой (так называемые силикаты, алюминаты, шпинели, оксисульфиды и пр.).
Кислород ухудшает механические свойства стали, снижает ее ударную вязкость при низких температурах, уменьшает временное сопротивление (прочность на разрыв), повышает неоднородность металла. Комбинированные кислородные и сернистые соединения образуют легкоплавкие неметаллические включения, располагающиеся по границам зерен. В процессе обработки давлением (прокатка или ковка) в таком металле при высоких температурах возможно образование трещин и рванин (явление красноломкости).
Форма, количество и состав кислородных включений в готовой стали зависят от способов раскисления металла, внепечной обработки, разливки и условий затвердевания расплава, а также от характера процессов выплавки стали (основной или кислой). Раскисление стали проводят таким образом, чтобы уменьшить в ней содержание кислорода и неметаллических включений и понизить их вредное влияние на качество металла. Для этого применяют следующие методы раскисления стали: диффузионное — воздействие на металл шлаком с низким содержанием оксидов железа; осадочное — воздействие на металл непосредственно элементами-раскислителями; комбинированное — одновременное воздействие на металл шлаком и элементами- раскислителями.
При равновесии отношение содержания кислорода в железе [О] к содержанию монооксида железа в шлаке (FeO) является постоянной величиной и зависит от основности шлака и температуры. При основности шлака, равной 2, и температуре 1600 °С данное отношение составляет величину 0,005. Если содержание (FeO) в шлаке ниже равновесного, то обеспечивается переход кислорода в виде FeO из металла в шлак. Другими словами, обработкой ванны безжелезистым шлаком можно добиться снижения содержания кислорода в металле.
Присадка в печь порошкообразных материалов — кокса, ферросилиция, алюминия — обеспечивает взаимодействие элементов-рас- кислителей с (FeO) шлака и снижение его концентрации ниже 0,5%. Если конечное содержание (FeO) в шлаке 0,5%, то конечное содержание кислорода в металле в условиях равновесия, определяемое из соотношения [О]кон/0,5 = 0,005, составит: [0]кон = 0,0025%.
Практически равновесие между шлаком и металлом в восстановительный период плавки (доводки) не достигается и содержание кислорода в металле перед выпуском из электропечи колеблется в пределах 0,003—0,012%. При этом уменьшение содержания кислорода в металле происходит, в основном, за счет диффузии кислорода из металла в шлак, поэтому такой способ раскисления называют диффузионным. Диффузионное раскисление ванны металла имеет место при выплавке стали в дуговых печах емкостью до 25 т. Процесс осуществляют под «белым» *(серым) или карбидным шлаком. Белый шлак получают раскислением основного шлака коксом, а затем порошками ферросилиция и алюминия. Карбидный — в результате интенсивного раскисления известкового шлака порошком кокса.
Современные большегрузные дуговые печи оборудуют высокопроизводительными установками для отсоса и очистки отходящих газов, которые при работе создают интенсивный газообмен в рабочем пространстве.
С учетом этого восстановительный шлак требуемых состава, консистенции и раскисленности наводят на жидкой ванне в печи за 15-20 мин до выпуска плавки в ковш путем интенсивной присадки порошков кокса, ферросилиция и алюминия. Период доводки металла (корректировка химического состава стали, нагрев металла и др.) проводят в течение минимального времени под известковым шлаком с основностью 3—4.
Диффузионный способ рафинирования металла позволяет существенно снизить загрязненность стали продуктами раскисления — неметаллическими включениями, так как взаимодействие происходит в шлаке и на поверхности раздела металл-шлак. Однако процесс малопроизводителен. Формирование восстановительного основного шлака к моменту выпуска плавки из большегрузной печи позволяет существенно повысить эффективность взаимодействия фаз в момент слива шлака и металла и тем самым обеспечить высокую степень рафинирования стали от кислорода и серы.
Раскисление стали путем непосредственного ввода в жидкий металл раскислителей в виде кусков или порошка называют глубинным или осадочным. Оно имеет место в металле на разной глубине в зависимости от удельного веса материала-раскислителя, размеров его кусков и способа ввода в металл. Эффект осадочного раскисления металла возрастает с уменьшением температуры плавления веществ- раскислителей и с повышением их растворимости в железе. Сочетание процессов осадочного раскисления металла с диффузионным взаимодействием элементов-раскислителей с кислородом относят к комбинированным методам.
Способы раскисления металла
В восстановительный период электроплавки раскисление металла осуществляют диффузионным способом, при котором реакция раскисления, т. е. связывание кислорода в прочные оксиды, протекает не в металле, а в шлаке, и металл, следовательно, не загрязняется продуктами раскисления. Это основное преимущество диффузионного раскисления перед глубинным. Другим преимуществом диффузионного раскисления является более слабое развитие реакции окисления металла шлаком во время и после выпуска металла из печи. Этим, в частности, объясняется незначительный угар легирующих элементов и раскислителей в электропечах,
К недостаткам диффузионного раскисления относятся:
-
уменьшение производительности печи;
-
снижение стойкости откосов и подины, особенно при раскислении шлака кремнием, так как образующийся кремнезем взаимодействует с основной футеровкой;
-
восстановление фосфора из шлака в металл, что вызывает необходимость тщательного удаления окислительного шлака;
-
повышенный расход раскислителей и необходимость их измельчения;
-
сложность осуществления герметизации печей (особенно большой емкости) для исключения подсоса воздуха.
Несмотря на отмеченные недостатки дуффузионного раскисления, его преимущества, связанные с возможностью получать хорошо раскисленный металл с низким содержание серы и неметаллических включений столь очевидны при производстве качественной и высококачественной стали, что этот способ находит широкое распространение при выплавке стали в электропечах.
Однако для уменьшения отрицательного влияния диффузионного раскисления металла в последнее время получила распространение технология, сочетающая преимущества диффузионного и глубинного раскисления. В этом случае перед началом диффузионного раскисления в металл присаживают кусковые раскислители: ферромарганец, ферросилиций, алюминий и т.д.
Иногда глубинное раскисление применяют и для окончательного раскисления металла.
Для диффузионного раскисления металла широко используют углерод, который дают на шлак чаще всего в виде коксика или электродного боя. При достаточно большом расходе коксика или электродного боя и высоком содержании CaO в шлаке в зоне дуг под электродами образуется карбид кальция по реакции
(CaO) + 3CТ = (CaC2) + {CO}.
Карбид кальция, обладая большим сродством к кислороду, взаимодействует с оксидами железа шлака:
(CaC2) + 3(FeO) = 3[Fe] + 2{СО} + (CaO).
Под карбидным шлаком (>2% CaCr) содержание FeO в шлаке может быть снижено до 0,5%, чему соответствует равновесное содержание кислорода в металле 0,0012% в металле при 1600° С. Подобное содержание кислорода в металле не может быть достигнуто даже при 0,3% Ti. Особенностью углерода как раскислителя является малое влияние температуры на его сродство к кислороду. Относительная дешевизна коксика и электродного боя и хороший эффект раскисления ими объясняет широкое применение их для диффузионного раскисления шлака.
В зависимости от содержания карбида кальция и шлаке, а следовательно, и степени его раскисления шлак восстановительного периода разделяют на белый (до 2% CaC2) и карбидный (>2% CaC2). Под белым шлаком выплавляют конструкционные стали с содержанием углерода ниже 0,35%, под карбидным шлаком — средне- и высокоуглеродистые стали.
Иногда рафинирование металла в окислительный период проводят под известково-глиноземистым, известково-шамотным или магнезиально-глиноземистым шлаками.
Диффузионное раскисление под белым шлаком
После скачивания окислительного шлака в ванне наводят шлак из извести и плавикового шпата в соотношении 3:2 и в количестве 2—4% от массы металла. Жидко-подвижный шлак образуется через 10—15 мин и на него задают восстановительную смесь из извести, плавикового шпата и молотого просеянного кокса или древесного угля с размером частиц не более 0,5—1,0 мм в соотношении 8:2: 1.
В результате раскисления шлака углеродом кокса содержание FeO в нем примерно через 40 мин снижается до 1,5%, и проба шлака после остывания принимает серый цист вместо черного в начале восстановительного периода, когда в шлаке содержится относительно много оксидов железа.
Вследствие возможности науглероживания металла дальнейшее его раскисление проводят кремнием. В шлаковую смесь вводят мелкоизмельченный ферросилиций марок ФС45 и ФС75. Состав шлаковой смеси следующий: четыре части извести, одна часть плавикового шпата, одна часть кокса и одна часть ферросилиция. Раскисление шлака кремнием длится
20 мин. Около 50% Si, вводимого из шлака ферросилицием, усваивается металлом.уменьшение производительности печи;
снижение стойкости откосов и подины, особенно при раскислении шлака кремнием, так как образующийся кремнезем взаимодействует с основной футеровкой;
восстановление фосфора из шлака в металл, что вызывает необходимость тщательного удаления окислительного шлака;
повышенный расход раскислителей и необходимость их измельчения;
сложность осуществления герметизации печей (особенно большой емкости) для исключения подсоса воздуха.
Раскисление шлака кремнием иногда производят с начала восстаковительного периода, что устраняет науглероживание металла. Однако содержание кремния в металле возрастает, он реагирует с растворенным в металле кислородом и образующиеся продукты раскисления частично остаются в металле. Поэтому загрязненность металла неметаллическими включениями при такой технологии может возрасти.
Белый шлак имеет обычно следующий состав 55— 65% CaO, 10—20% SiO2, до 1% FeO, 0,4% MnО, 12— 16% MgO, 2-3% Al2O3, 5-10% CaF2, 1% CaS, до 2% CaC2. Проба белого шлака при остывании рассыпается, что связано с присутствием в нем силиката кальция 2 CaO • SiO2, который при 675° С меняет свою модификацию, увеличиваясь при этом в объеме.
Для получения относительно раскисленного металла необходимо выдерживать металл под белым шлаком
Глубинное и диффузионное раскисление металла
После скачивания окислительного шлака на открытое зеркало металла присаживают кусковые раскислители: ферромарганец, ферросилиций, силикомарганец, алюминий и т.д. Расход раскислителей должен обеспечить содержание марганца в металле на нижнем пределе в заданной марке стали, введение 0,15—0,2% кремния и 0,05—0,1% алюминия. Затем загружают шлаковую смесь и после ее расплавления шлак обрабатывают раскислительными смесями с постепенно уменьшающимся количеством порошка кокса. При такой обработке образуется слабокарбидный или белый шлак, содержащий
Раскисление алюминием
Алюминий – очень сильный раскислитель (рис. 3.7). Алюминий, присутствующий в стали в сравнительно небольших количествах (0,02…0,04 %), обеспечивает получение очень низких концентраций растворенного кислорода (менее 0,003 %) в металле. При раскислении алюминием в стали могут образоваться либо мелкие включения чистого глинозема Al2O3 с температурой плавления около 2050 °С, либо легко укрупняющиеся соединения типа nFeO · mAl2O3 , обычно с температурой плавления ниже температуры жидкой стали. Высокие значения σм-вкл на границе жидкий металл-твердое включение глинозема существенно облегчают отделение этих включений от металла и ассимиляцию их шлаком. Кроме того, при введении алюминия в расплав часть алюминия взаимодействует с растворенным азотом, образуя нитриды типа AlN и уменьшая вероятность старения стали. Мелкие твердые включения глинозема и нитридов алюминия в процессе кристаллизации стали регулируют размер зерна (уменьшают его размеры). Поэтому раскисление алюминием очень широко распространено. Применяют либо чистый алюминий (чушки, крупку, порошок, проволоку и т.д.), либо сплавы алюминия.
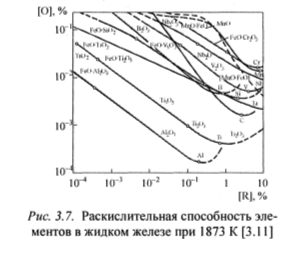
Раскисление кремнием
Кремний – достаточно сильный и сравнительно недорогой раскислитель (рис. 3.7), поэтому он применяется в производстве стали. При раскислении жидкого металла кремнием в зависимости от окисленности металла и концентрации кремния в стали образуются или жидкие силикаты железа (мало [Si] и много [О]), или твердый кремнезем SiO2 (много [Si] и мало [О]). При наличии основного шлака раскислительная способность кремния возрастает. Однако удаление образующихся при раскислении силикатов из металла несколько затруднено, так как они хорошо смачиваются железом. Обычно для раскисления стали кремнием используют ферросилиций и силикомарганец различных марок.

Раскисление стали в кислой электропечи
В кислой электропечи углеродистую сталь обычно выплавляют без диффузионного раскисления в печи. Диффузионное раскисление применяют лишь иногда при выплавке легированной стали.
Раскисление углеродистой стали
В окислительный период металл частично раскисляется восстановившимся кремнием. В конце окислительного периода в ванну присаживают ферромарганец. Повышение содержания марганца в металле способствует восстановлению кремния до 0,2—0,3% по реакции
2 [Mn] + (SiO2) = [Si] + 2 (MnO). (160)
За 7—10 мин до выпуска в ванну присаживают ферросилиций для получения заданного содержания кремния; за 3—5 мин до выпуска вводят ферромарганец для окончательного корректирования содержания марганца в металле.
При расчете необходимого количества ферросилиция необходимо учитывать угар кремния (5—10%) и марганца (15—20%). Иногда ферромарганец при выплавке углеродистой стали присаживают в ковш. Угар марганца в этом случае не превышает 10%. Окончательно металл раскисляют алюминием в количестве 160 —200 г/т при отливке слитков и 1—1,5 кг/т при использовании жидкой стали для фасонного литья. Причем 0,5—0,6 кг/т присаживают во время выпуска, остальное при разливке.
Раскисление легированной стали
При выплавке легированной стали в электропечах содержание серы и фосфора в шихте не должно превышать 0,04%. При выплавке стали, содержащей никель и молибден, в завалку используют содержащие указанные элементы отходы, что уменьшает расход легирующих присадок. Расплавление ведут как при выплавке углеродистой стали. После расплавления отбирают пробу металла на полный химический анализ (С, Cr, Ni, Mo, Cu, S, P) и, если содержание серы и фосфора не превышает заданного, в ванну загружают при необходимости никель и ферровольфрам.
После проведения чистого кипения иногда проводят операцию «перекипа», для чего в ванну присаживают чугун или углеродистый ферромарганец (5—7 кг/т). После этих присадок ванна бурно вскипает, что способствует удалению газов.
Легированную сталь выплавляют иногда с удалением 60—80% окислительного шлака, что уменьшает угар легирующих элементов. Для наведения нового шлака в печь загружают смесь из 1—2% кварцевого песка и 0,5—1 % извести или известняка.
Раскисление легированной стали в кислой электропечи может осуществляться либо диффузионным, либо глубинным методами. Если плавку проводят без диффузионного раскисления металла, то после окончания чистого кипения в ванну присаживают для предварительного раскисления силикомарганед (2—4 кг/т) или ферромарганец и ферросилиций. После тщательного перемешивания ванны присаживают феррохром. Не позже чем за 10 мин до выпуска присаживают ферросилиций для легирования стали. Ферромарганец для легирования присаживают непосредственно перед выпуском. При выпуске из печи металл окончательно раскисляют силикокальцием (1,5—2,5 кг/т), алюминием и ферротитаном.
В случае диффузионного раскисления металла после проведения чистого кипения и «перекипа» на шлак задают коксик в количестве 0,2% от массы металла и иногда молотый ферросилиций. Вязкость шлака регулируют присадками извести или известняка. После присадки кокса ванну выдерживают в течение 5—10 мин. Получив результаты анализа, проводят предварительное раскисление металла силикомарганцем (4 кг/т) или ферросилицием и ферромарганцем. Легирование металла проводят после предварительного раскисления. Ферросилиций присаживают за 10 мин до выпуска, а ферромарганец — непосредственно перед выпуском. Окончательно металл раскисляют при выпуске алюминием (1 кг/т) и силикокальцием (2—3 кг/т).
Ниже приведена длительность плавок различных сталей в кислых электропечах емкостью 7 т по данным одного из уральских машиностроительных заводов.
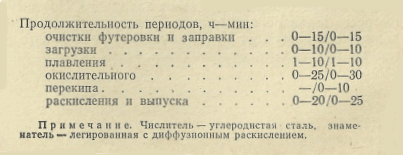
Производительность кислой электропечи на 15—30% выше производительности основной печи.
Раскисление металла обработкой в вакууме
Раскисление металла обработкой вакуумом основано на том, что равновесие реакции
[С] + [О] = СОгаз
в вакууме сдвигается:
К = РСО / а[с]а[о] ,
а[О] = РСО / К • а[С] ,
в сторону образования дополнительных количеств монооксида углерода в результате снижения Рсо, а концентрация растворенного кислорода (активность кислорода) в металле при этом уменьшается. Иногда такой способ называют углеродное раскисление в вакууме, или вакуумно-углеродное раскисление. Раскисление металла углеродом в вакууме эффективно и протекает достаточно быстро лишь при обработке нераскисленного металла, лучше при высоком содержании углерода в стали и при хорошем перемешивании металла. После вакуумноуглеродного раскисления проводят окончательное осаждающее раскисление металла. Внепечное раскисление металла углеродом в вакууме в настоящее время довольно широко применяется в практике сталеплавильного производства, особенно в случае выплавки высококачественных сталей, где необходима низкая степень загрязненности оксидными неметаллическими включениями.
Список литературы:
1) «Раскисление металла в восстановительный период»
https://metallolome.ru/raskislenie-metalla-v-vosstanovitel/
2) «Раскисление стали и неметаллические включения»
https://studfile.net/preview/7051690/page:20/
3) Кнюппель Г.
«Раскисление и вакуумная обработка стали»
4) А.М. Самарин
«Физико-химические основы раскисления стали»