Файл: Содержание анализ и систематизация поставленной задачи.docx
ВУЗ: Не указан
Категория: Не указан
Дисциплина: Не указана
Добавлен: 08.02.2024
Просмотров: 25
Скачиваний: 0
ВНИМАНИЕ! Если данный файл нарушает Ваши авторские права, то обязательно сообщите нам.
СОДЕРЖАНИЕ
1.1. АНАЛИЗ И СИСТЕМАТИЗАЦИЯ ПОСТАВЛЕННОЙ ЗАДАЧИ
1.1.1.1 Существующие типы лазеров для резки металлов
Волоконные технологические лазеры
1.1.1.2 Технологическое сравнение плазменной и лазерной резки
1.1.2 Систематизация теоретической информации по лазерным технологиям
1.1.2.1 Экономическое сравнение лазерной и плазменной резки
Шапарев А.В. - Обзор лазерной резки металлов
СОДЕРЖАНИЕ
1.1. АНАЛИЗ И СИСТЕМАТИЗАЦИЯ ПОСТАВЛЕННОЙ ЗАДАЧИ
1.1.1 Анализ научно-технической литературы, нормативно-технической документации и других материалов по теме проекта
1.1.1.1 Существующие типы лазеров для резки металлов
СО2-лазеры
В CO2-лазере лазерное излучение испускается молекулами CO2. Молекула CO2 состоит из одного атома углерода и двух атомов кислорода. Они образуют цепочку, в которой атом углерода располагается между атомами кислорода. Когда молекула возбуждается, она начинает совершать колебания. Различные формы колебаний соответствуют различным по величине энергетическим уровням. Процесс формирования излучения в CO2-лазере происходит с использованием 4-х энергетических уровней. Уровень накачки и верхний лазерный уровень находятся очень близко друг другу.
Однако активная среда лазера состоит не только из CO2. Она представляет собой смесь гелия (He), азота (N2) и углекислого газа (CO2). Гелий и азот выполняют роль вспомогательных газов. Они лишь поддерживают процесс непосредственного формирования лазерного излучения в молекулах CO2.
За счет разряда электротока высокого постоянного или высокочастотного переменного напряжения в газовой смеси образуются свободные электроны, которые, соударяясь с молекулами азота, возбуждают их. Молекулы азота начинают совершать колебания. Соударяясь, они передают свою энергию молекулам CO2 и переводят их из основного состояния на верхний лазерный уровень, - в колебательное состояние, при котором все три атома молекулы находятся в движении. При переходе на нижний лазерный уровень молекулы CO2 испускают лазерное излучение с длиной волны 10,6 микрометра.
С него, выделяя тепло, они снова возвращаются в основное состояние. Теперь вступают в действие атомы инертного газа гелия: соударяясь с молекулами CO2, они ускоряют расселение ниңнего лазерного уровня, поглощают и отводят тепло.
Лазер состоит из следующих узлов:
-
генератор излучения; -
распределительный шкаф; -
холодильный агрегат.
В генераторе излучения смесь лазерного газа, проходящая через резонатор, под воздействием высокочастотного разряда приводится в состояние испускания лазерного излучения.
Состав лазера представлен ниже на рис.1.
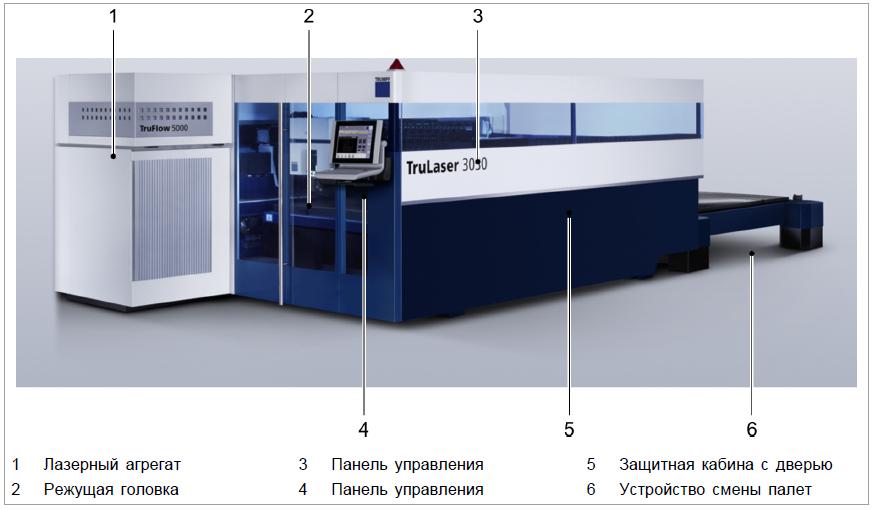
Рис.1. Лазерный станок TruLaser 3030
Достоинства CO2-лазера TruFlow (рисунок 1):
-
высокая мощность лазера и ее стабильность; -
высокий КПД; -
оптимальное распределение интенсивности по сечению луча; -
оптимизированный режим ожидания во время проведения наладки и во время ожидания; -
отсутствие износа и необходимости техобслуживания: вал центробежного турбокомпрессора выполнен магнитным, поэтому имеет бесконтактные опоры, не требующие никакой смазки; -
возбуждение активной среды лазеров TruFlow происходит за счет подачи высокочастотного переменного напряжения; -
возбуждение высокой частотой приводит к гомогенизации газового разряда и достижению очень высокого качества излучения; -
для возбуждения лазерного газа требуется меньшее напряжение, чем при подаче энергии от источника постоянного тока. Как следствие: снижение интенсивности разложения CO2 и уменьшение расхода газа; -
так как электроды не имеют непосредственного контакта с активной средой лазера и, следовательно, не подвержены воздействию газового разряда, отпадает проблема их износа. Кроме того, материал электродов не загрязняет резонатор и зеркала. При этом сокращаются затраты на техобслуживание (т.е. простои станка) и расход газа; -
мощность лазера остается на постоянном уровне в течение многих лет, что значительно повышает надежность планирования и калькуляций для пользователя; -
значительно сниженное потребление мощности благодаря оптимированному режиму ожидания;
Режущая лазерная головка (рис.3) является основным конструктивным элементом установки. Линза (ZnSe) преломляет параллельные лазерные лучи и собирает их в фокус, в котором излучение достигает максимальной плотности своей энергии. В зависимости от используемого типа линзы фокусное расстояние составляет 130 мм или 250 мм.
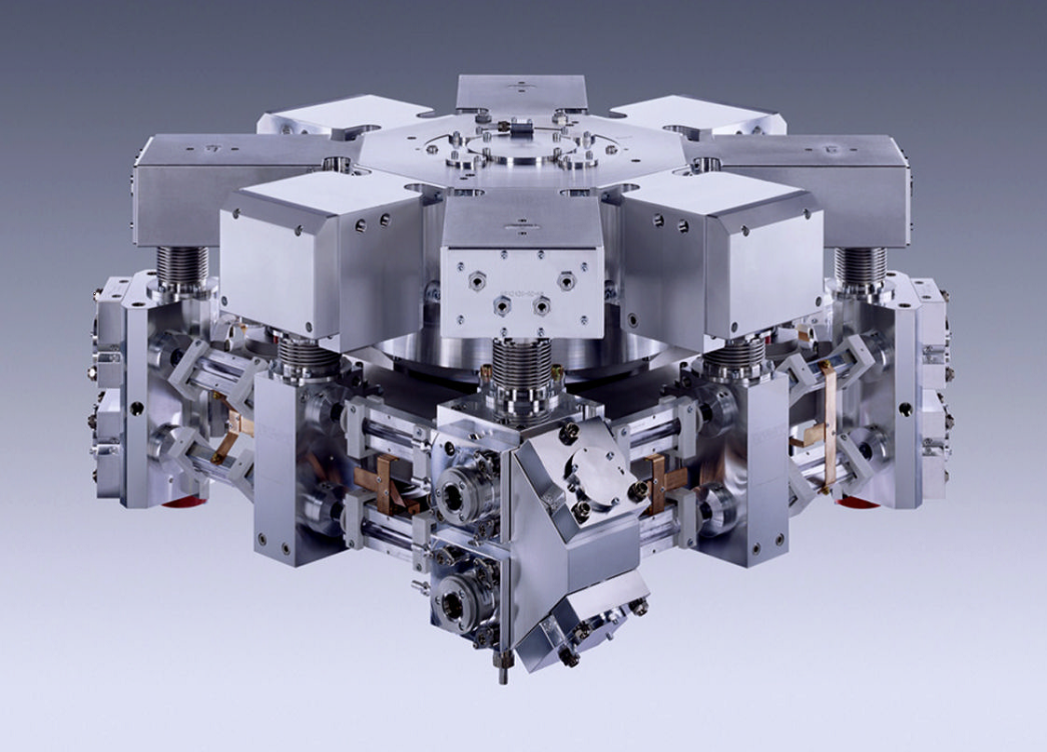
Рис.2. Внутренняя головка лазера TruFlow
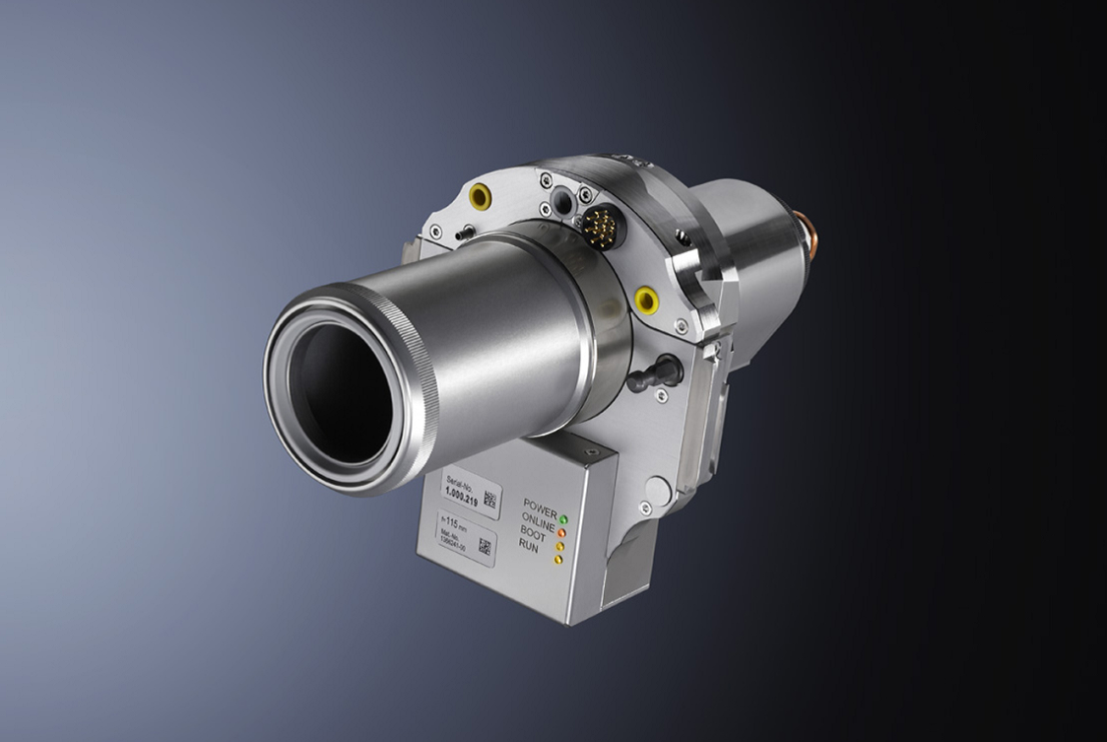
Рис.3. Режущая головка CO2-лазера TruFlow
Для оптимального результата работы фокус должен быть настроен в определенной точке на поверхности заготовки. Все соединения для питающих шлангов и кабелей были интегрированы в интерфейс.
Таким образом, для автоматического создания всех соединений достаточно установить режущую головку в крепление.
Механизм отклонения посредством системы считывания данных режущей головки, контролируемой датчиками, немедленно останавливает движение в случае столкновения и предотвращает повреждение подключения режущей головки. Режущая головка отклоняется; затем ее снова можно установить в исходное положение вручную. При небольшом столкновении режущая головка автоматически переходит в нужное положение. Затем без необходимости проведения других наладочных работ можно продолжать обработку. Через режущее сопло, которое дополнительно охлаждается очищенным сжатым воздухом, излучение и режущий газ подводятся на заготовку для ее обработки.
Плазменная резка
Под плазмой понимают высокотемпературный ионизированный газ, который может проводить электроток [1]. А плазменная дуга формируется в агрегате под названием плазмотрон из обычной электрической. Плазменную дугу сжимают, а затем привносят в нее газ, обладающий возможностью образования плазмы.
Для резки металлов используется плазменно-дуговая резка. В данном случае дуга горит между материалом, который обрабатывается, и сварочным электродом неплавящегося типа. Плазменная высокоскоростная струя при такой технологии совмещается со столбом плазменной дуги. Сам же процесс резки обеспечивается высокой энергией плазмы столба и факела, исходящего из указанного столба. Данный принцип плазменной резки металла чаще всего используется на современных предприятиях, так как он признается максимально эффективным.
Плазмотрон работает следующим образом. Плазмотрон представляет собой устройство плазменной резки, в корпусе которого размещают небольшую по сечению дуговую камеру цилиндрической формы. На выходе из нее имеется канал, который создает сжатую дугу. С задней стороны такой камеры располагается сварочный стержень.
Между наконечником устройства и электродом зажигают предварительную дугу. Эта стадия необходима, так как возбуждения дуги между разрезаемым материалом и электродом добиться практически невозможно. Указанная предварительная дуга выходит из сопла плазмотрона, соприкасается с факелом, и в этот момент создается уже непосредственно рабочий поток.
После этого формирующий канал полностью заполняется столбом плазменной дуги, газ, образующий плазму, поступает в камеру плазмотрона, где происходит его нагрев, а затем ионизация и увеличение в объеме. Описанная схема обуславливает высокую температуру дуги (до 30 тысяч градусов по Цельсию) и такую же мощную скорость истекания газа из сопла (до 3 километров в секунду).
Плазмообразующая среда является ключевым параметром процесса, который определяет его технологический потенциал. От состава данной среды зависит возможность:
-
настройки показателя теплового потока в зоне обработки металла и плотности тока в нем (за счет изменения отношения сечения сопла к току); -
варьирования объема тепловой энергии в широких пределах; -
регулирования показателя поверхностного напряжения, химсостава и вязкости материала, который подвергается резке; -
контроля глубины насыщенного газом слоя, а также характера химических и физических процессов в зоне обработки; -
защиты от появления подплывов на металлических листах (на их нижних краях); -
формирования оптимальных условий для выноса из полости реза расплавленного металла.
Кроме того, многие технические параметры оборудования, используемого для плазменной резки, также зависят от состава описываемой нами среды, в частности следующие:
-
конструкция охлаждающего механизма для сопел устройства; -
вариант крепления в плазмотроне катода, его материал и уровень интенсивности подачи на него охлаждающей жидкости; -
схема управления агрегатом (его циклограмма определяются именно расходом и составом газа, используемого для формирования плазмы); -
динамические и статические (внешние) характеристики источника питания, а также показатель его мощности.
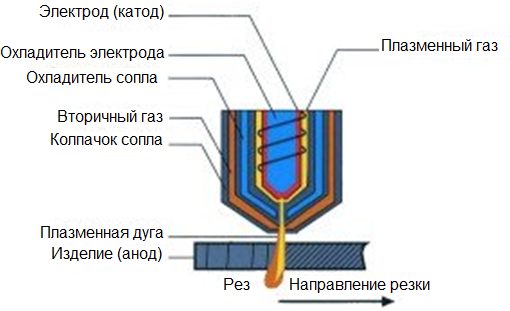
Рис.4. Схема плазменной резки
Большое значение имеет правильно подобранная комбинация газов для создания плазмообразующей среды, принимая во внимание цену применяемых материалов и непосредственно себестоимость операции резки.
Как правило, для полуавтоматической и ручной обработки коррозионностойких сплавов, а также машинной и экономичной ручной обработки меди и алюминия используют среду, образованную азотом. Низколегированная углеродистая сталь лучше режется в кислородной смеси, которую категорически нельзя применять для обработки изделий из алюминия, стойкой против коррозии стали и меди.
К главным достоинствам использования плазменного оборудования можно отнести следующие факты:
-
универсальность технологии: практически все известные материалы можно резать при помощи плазменной дуги, начиная от чугуна и меди и заканчивая алюминиевыми и стальными холоднокатаными листами; -
высокая скорость операции для металлов средней и малой толщины; -
резы получаются по-настоящему качественными и высокоточными, что нередко дает возможность не производить дополнительную механическую обработку изделий; -
минимальное загрязнение воздуха; -
отсутствие необходимости выполнять предварительный прогрев металла для его резки, что позволяет уменьшать (и существенно) время прожига материала; -
высокая безопасность выполнения работ, обусловленная тем, что для резки не нужны баллоны с газом, являющиеся потенциально взрывоопасными.