ВУЗ: Не указан
Категория: Не указан
Дисциплина: Не указана
Добавлен: 04.02.2024
Просмотров: 17
Скачиваний: 0
ВНИМАНИЕ! Если данный файл нарушает Ваши авторские права, то обязательно сообщите нам.
Всего на данный момент известно 3 электрохимических метода обработки металлов: анодный, катодный и смешанный.
Травление - удаление какой-либо части поверхностного слоя заготовки. Чаще всего применяется перед покраской или сборкой. Используется и в качестве подготовки к сварке под давлением.
Полирование - травление шероховатостей болванки вплоть до зеркального состояния, а также дезактивация радиоактивного заражения изделий. Отдельного упоминания заслуживает возможность снятия слоя до ста микрон.
Размерная обработка – окисление верхних слоев изделия с дальнейшим удалением оксидов недостаточной плотности.
Катодная обработка, или же гальванотехника, состоит в нанесении металлического покрытия на заготовку. Применяется заметно реже анодирования, но тоже имеет несколько видов:
Гальваностегия - нанесение на внешний слой заготовки тонких металлических покрытий толщиной до нескольких десятков микрометров.
Гальванопластика – основное отличие от гальваностегии в том, что толщина покрытия достигает нескольких миллиметров и отличается составом от материала болванки.
Смешанная обработка - состоит в попеременном использовании двух перечисленных выше методов, что позволяет пользоваться преимуществами обоих из них.
Однако, несмотря на кажущуюся трудность подобных работ, сложные изделия получить описанными выше методами довольно проблематично. Для того, чтобы наладить массовый выпуск изделий, применяются всевозможные станки с электрохимическими методами обработки металлов. С их помощью можно уплотнить поверхность или же труднодоступные участки, шлифовать и резать изделия… Список их возможностей можно продолжать практически до бесконечности.
Однако, как это всегда бывает, не обошлось и без отрицательных моментов. В данном случае он присутствует в единственном, зато очень заметном аспекте – узко направленность производства. По сути, под каждый тип детали требуется отдельный станок.
Не утрачивают популярности и копирно-прошивочные станки, за счет которых производятся режущие инструменты, пуансоны, матрицы и многое другое, что сильно помогает в любой рабочей специальности.
Подводя итог всему написанному выше, хочется отметить тот факт, что, несмотря на затянувшийся кризис, работа с металлическими изделиями переживает настоящий бум.
Остается лишь надеяться, что подобная тенденция будет сохраняться еще не одно десятилетие, так как в отрасли трудится огромное количество человек.
С другой стороны, настоящий профессионал своего дела найдет работу в любых условиях. На нашей выставке вы сможете увидеть новые разработки в этой области.
Современные электрохимические методы обработки металлов демонстрируются на ежегодной выставке «Металлообработка».
40. Назначение и устройство реверсивных механизмов
Реверсивный механизм изменяет направление вращения барабанов грузовой и стреловой лебедок и поворотной части крана. Распределительный механизм распределяет крутящий момент между грузовой и стреловой лебедками и механизмом поворота, обеспечивая независимый раздельный привод всех механизмов или некоторых из них. Реверсивные и распределительные механизмы применяют только на кранах с механическим приводом; на электрических и гидравлических кранах их функции выполняют электро - и гидродвигатели. Реверсивные механизмы как самостоятельные сборочные единицы трансмиссии используют только на кранах серии МКА для реверса грузовой лебедки и механизма поворота. На остальных кранах с механическим приводом реверсивный и распределительный механизм объединены в один корпус, составляя реверсивно-распределительный механизм. Реверсивно-распределительный механизм крана КС-2561К-1, установленный в центре поворотной рамы между грузовой лебедкой и механизмом поворота, состоит из реверсивного механизма I (рис.37), изменяющего направление вращения барабанов лебедок и поворотной части, и распределительного механизма II, передающего движение грузовой лебедке и механизму поворота или стреловой лебедке. Вал 13 реверса, установленный на двух шарикоподшипниках в корпусе 26, ведущий. На нем на подшипниках посажены две конические шестерни 20 и 25, находящиеся в постоянном зацеплении с валом-шестерней 17. На торцах ступиц шестерен 20 и 25 имеются кулачки. Между этими шестернями на шлицах установлена кулачковая муфта 23, которая может занимать три положения: нейтральное, крайнее верхнее и нижнее. В нейтральном положении муфта не входит в зацепление с шестернями 20 и 25 и все механизмы поворотной части крана отключены.
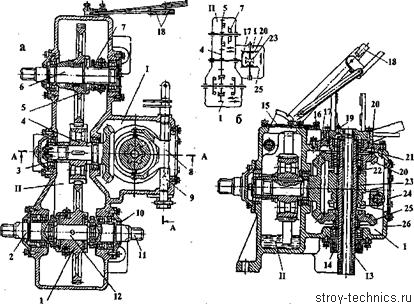
Рисунок 1. Реверсивно-распределительный механизм крана КС-2561К-1 (а) и его кинематическая схема (б):
1, 4, 5, 20, 25 - шестерни; 2, 6, 9, 11-13 - валы; 3, .21, 22 - регулировочные прокладки; 7, 23 - муфты; 8 - вилка; 10, 14 - уплотнения; 15, 24 - крышки; 16 - болт; 17 - вал-шестерня; 18 - рычаг; 19 - масленка; 26 - корпус.
В крайнем верхнем положении она входит в зацепление с кулачками шестерни 20, от которой движение передается валу-шестерне, а от него через распределительный механизм - лебедкам или механизму поворота. Это положение муфты соответствует подъему груза, стрелы или вращению поворотной части крана влево. В крайнем нижнем положении муфта входит в зацепление с кулачками шестерни 25. При этом меняется направление вращения вала-шестерни и всех последующих механизмов. Нижнее положение соответствует опусканию груза, стрелы и вращению поворотной части крана вправо. Муфта 23 перемещается с помощью, установленной на валу 9 вилки 8, соединенной с рычагом управления реверсом. В рабочем и в нейтральном положении вилка фиксируется шариковым фиксатором. Для осмотра реверсивного механизма в корпусе есть окно, закрытое крышкой 24. К верхнему шарикоподшипнику вала реверса и шарикоподшипникам шестерни 20 смазка поступает из масленки 19. Остальные подшипники и шестерни смазываются маслом, заливаемым в картер корпуса. Правильность зацепления конических шестерен 20 и 25 с валом-шестерней регулируют прокладками 3 и 22. От реверсивного механизма через вал-шестерню движение передается распределительному механизму. На валу-шестерне на шпонке установлена распределительная цилиндрическая шестерня 4, которая находится в постоянном зацеплении с цилиндрическими шестернями 1 и 5. Шестерня 5 свободно вращается на валу 6, передающем движение грузовой лебедке. По шлицам вала 6 перемещается муфта 7, при зацеплении зубьев которой с зубьями ступицы шестерни 5 движение передается валу 6 и от него - грузовой лебедке. Управляют муфтой 7 с помощью рычага из кабины управления. Шестерня 1 свободно посажена на валу 12, установленном в гнездах валов 2 и 11. При перемещении шестерни 1 по валу 12 зубья на ее торцах входят в зацепление с зубчатым венцом вала 2 и 11. При соединении шестерни 1 с зубчатым венцом вала 2 движение передается стреловой лебедке, вала 11 - механизму поворота. Шестерня 1 перемещается с помощью вилки, соединенной с рычагом 18. Осматривают распределительный механизм через люк, закрытый крышкой с прокладкой 15. Смазывается механизм маслом, заливаемым в картер. Картеры реверсивного и распределительного механизмов разделены стенкой, а для определения уровня масла в каждом картере имеется свой масло указатель. Описанный реверсивно-распределительный механизм (рис. 37) обеспечивает независимую работу грузовой лебедки со стреловой лебедкой (шестерня 1 входит в зацепление с зубчатым венцом вала 2) или с механизмом поворота (шестерня 1 входит в зацепление с зубчатым венцом вала 11).
49 Устройство станков
В устройстве металлорежущих станков имеется много общего. Это объясняется самой сущностью процесса резания.
Основу устройства металлорежущих станков составляет совокупность механизмов и других технических устройств, обеспечивающих главным образом два движения - движение резания (резцом, фрезой, сверлом и т. д.) и движение подачи заготовки или режущего инструмента.
Любой металлорежущий станок состоит из привода, передаточного механизма, исполнительного (рабочего) органа и органов управления (это можно проследить на примере уже рассмотренного устройства сверлильного станка).
Привод приводит в действие рабочие органы. Приводы могут быть механическими, Гидравлическими, пневматическими или электрическими.
В современных металлорежущих станках используются преимущественно электроприводы.
Передаточные механизмы передают движение от двигателя к рабочему органу станка и преобразуют это движение.
Исполнительные (рабочие) органы - это устройства, которые непосредственно осуществляют процесс резания металла. На них закреплены режущие инструменты.
Органы управления - устройства, с помощью которых осуществляется пуск и остановка станка, регулируется скорость резания и подачи, т.е. производится управление работой металлорежущего станка.
Многие механизмы, узлы и детали различных металлорежущих станков (например, станины, коробки скоростей, коробки подач), хотя и отличаются конструктивно, но выполняют одинаковые функции.
Станина - чугунное или стальное основание, на котором крепят механизм станка.
Станина обеспечивает точность их взаимного расположения и перемещения.
Коробка скоростей изменяет передаточные отношения между ведущими и ведомыми звеньями (валами), что позволяет регулировать частоту вращения режущего инструмента или заготовки.
Коробка подач изменяет передаточные отношения в цепи подачи, чем регулирует величину подачи режущего инструмента.
Знание функционально общих основных узлов различных типов металлорежущих станков позволяет лучше и быстрее ознакомиться с устройством, управлением и работой любого конкретного станка.