ВУЗ: Не указан
Категория: Не указан
Дисциплина: Не указана
Добавлен: 16.03.2024
Просмотров: 50
Скачиваний: 0
ВНИМАНИЕ! Если данный файл нарушает Ваши авторские права, то обязательно сообщите нам.
Скважинное или глубинное дозирование – способ подачи химреагента непосредственно на прием насоса, для этой цели используют несколько конструкций скважинных дозаторов.
В настоящее время применяют дозированные установки УДЭ представленный на (рисунке 1) монтируемый в закрытом блоке и устанавливаемый на устье скважины.
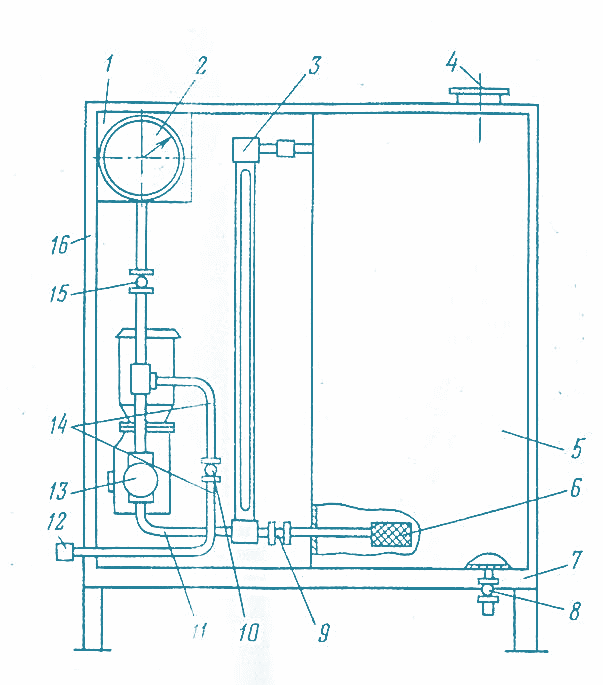
1 - дозировочный блок, 2 – электроконтактный манометр, 3- указатель уровня, 4- заливная горловина, 5 – бак, 6 – фильтр, 7 – рама, 8 – сливной вентиль, 9, 10, 15 – вентили, 11 - всасывающий трубопровод, 12 – обратный клапан, 13 – электронасосный агрегат, 14 – нагнетательный трубопровод, 16 – кожух
Рисунок 1 – Дозировочная электронасосная установка УДЭ
Блок включает в себя емкость с реагентом, из которой дозировочным электронасосом, реагент подается в нагнетательный трубопровод, а затем в затрубное пространство в скважины. Блок быстро монтируется, однако, для его установки требуется свободная площадка на устье, прокладка трубопроводов. При ремонтных работах на устье скважины требуется перенос блока и коммуникаций, что удлиняет время ремонта и увеличивает его стоимость.
Установка дозировочная, входящая в состав УДЭ, состоит из технологического отсека и технологической емкости, примыкающих друг к другу и размещенных на общем основании (раме).
В технологическом отсеке в зависимости от варианта исполнения УДЭ могут быть смонтированы:
- дозировочный электронасосный агрегат (насос-дозатор), осуществляющий непрерывное объемное дозирование реагента;
- трубопроводная технологическая обвязка (с арматурой) насоса-дозатора и технологической емкости;
- взрывозащищенный электромагнитный пускатель;
- электроконтактный манометр;
- выключатель ВПВ.
Таблица 4 – Технологическая характеристика УДЭ
Параметры | Исполнение | |||
100/2,5 | 25/4,0 | 10/10 | 2,5/10 | |
1 | 2 | 3 | 4 | 5 |
Подача насоса, л/ч | 100 | 25 | 10 | 2,5 |
Максимальное давление, МПа | 2,5 | 4 | 10 | 10 |
Объем бака, м3 | 0,45 | 0,45 | 0,45 | 0,45 |
Срок службы, лет | 10 | 10 | 10 | 10 |
Масса, кг | 220 | 200 | 200 | 200 |
Глубинные скважинные дозаторы имеет ряд преимуществ перед наземными:
а) они подают химреагент непосредственно в область приема при высокой температуре, что усиливает их активность;
б) они нормально работают в любое время года, так как вязкость химреагента постоянна;
в) они не загромождают устьевую площадку и не требуют сложных монтажно-демонтажных работ.
Но они обладают и серьезным недостатком: дозирование реагента сложно организовать в скважине. Именно на это и направлены в последние годы усилия многих разработчиков. Приведем описание некоторых конструкций, получивших применение на промыслах.
Дозатор химреагентов невставного ШГН включает в себя плунжер пару – цилиндр и плунжер, а также клапанную систему. Особенностью конструкции является шток всасывающего клапана штангового насоса, перемещающийся при получении импульса «всасывание-нагнетание» за счет движения плунжера насоса. При этом штатный всасывающий клапан трубного насоса заменяется на тарельчатый через переводник к корпусу присоединяется контейнер. Последний собирается из НКТ, количество которых определяется временем дозирования химреагента.
При всасывании жидкости штанговым насосом происходит подъем тарели и связанного с ней штока. В накопительной камере создается разряжение, и химреагент из контейнера поступает в камеру. При ходе плунжера насоса тарель движется вниз, и шток вытесняет реагент через нагнетательный клапан в область приема насоса.
Техническая характеристика дозатора: производительность – 30 – 150 г/м3; объем контейнера – до 400 л; диаметр – до 60 мм; длина – до 1000 мм; масса – до 20 кг.
В настоящее время отечественной промышленностью изготовляются блоки и установки дозирования химических реагентов (деэмульгаторов, ингибиторов коррозии, солеотложения и т.п.) БР-2.5; БР-10; БР-25. Предназначены для приготовления и дозированного ввода жидких деэмульгаторов и ингибиторов коррозии в любой точке трубопровода промысловой системы транспорта и подготовки нефти на участке скважины до установки комплексной подготовки нефти.
Все оборудование установок БР-2.5 и БР-10 (рисунок 2) размещено в теплоизолированной будке 1, смонтированной на сварной раме-санях 2. Будка разделена герметичной перегородкой 4 на два отсека (технологический и приборный).
В технологическом отсеке размещены технологическая емкость 8, трубчатый электронагреватель 5, шестеренный 7 и дозировочный 6 насосы, а также средства контроля и управления 3.
Таблица 5 –Технологические характеристики блока реагентов типа БР
Показатели | Исполнение | ||
БР-2,5 | БР-10 | БР-25 | |
1 | 2 | 3 | 4 |
Размер дозы, г/т | 10 | 10 | 10 |
Вязкость дозируемой среды, МПа×с. | 50 | 50 | 50 |
Подача дозировочного насоса, л/ч. | до 1000 | до 850 | до 850 |
Рекомендуемое давление нагнетания, МПа. | 2,5 | 2,5 | 2,5 |
Температура дозируемого реагента, °С | 50¸60 | 20¸60 | 20¸60 |
Температура окружающей среды, °С. | -40¸+50 | -40¸+50 | -40¸+50 |
Масса, кг | 300 | 300 | 300 |
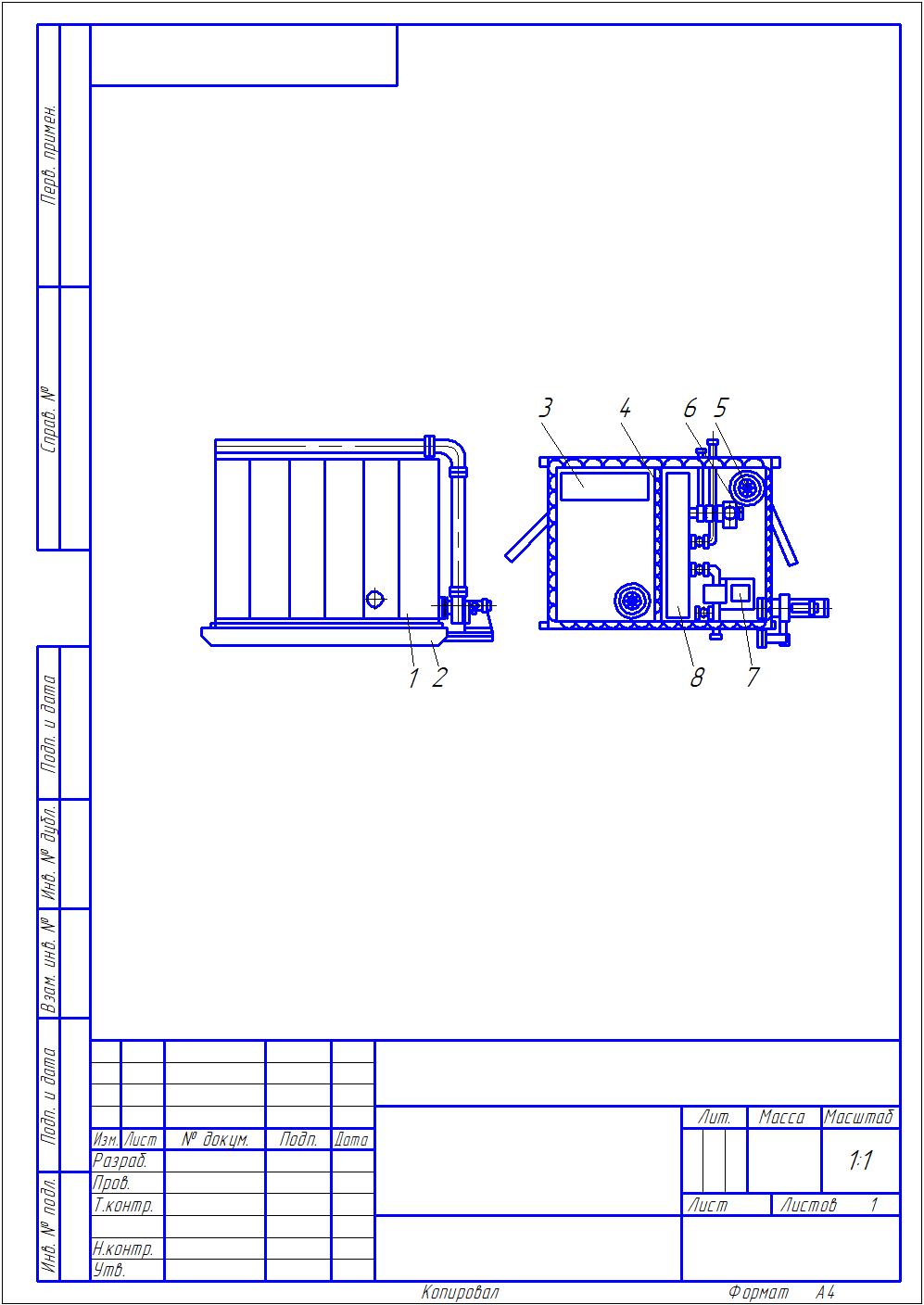
Рисунок 2 - Блоки дозирования химреагентов БР-2.5 и БР-10
На (рисунке 3) представлены элементы электрического кабеля УЭЦН с капиллярной трубкой. Капиллярная трубка изготавливается из того же полипропилена, что и двухслойная изоляция трех жил кабеля питания УЭЦН.

Рисунок 3 - Конструкция специального погружного кабельного устройства (СПКУ)
Полипропилен отличает высокая химическая стойкость к действию самых различных реагентов: кислот, щелочей, солей, органических растворителей, нефтепродуктов. Он обладает требуемой инертностью к применяемым в нефтедобыче реагентам.
При всех способах эксплуатации скважин подъем жидкости и газа на поверхность происходит по насосно-компрессорным трубам. Достаточно широко на нефтяных промыслах применяются НКТ, внутренняя поверхность которых покрыта стеклом, эпоксидными смолами. Менее распространенные эмалированные трубы.
Покрытие стеклом обладает высокой теплостойкостью и достаточно прочно при небольших деформациях труб. На поверхности стекла не откладывается парафин. Однако покрытие стеклом имеет ряд недостатков. Один из них – образование микротрещин в стекле при покрытии им трубы. В результате образуются очаги коррозии металла и местного отложения парафина у трещин. В настоящее время отрабатывается технология покрытия, уменьшающая трещинообразование. Второй недостаток – разрушение стекла при деформации труб. Это сказывается при больших глубинах подвески труб и их транспортировке, когда трубы не предохранены от изгиба.
Покрытие труб эпоксидными смолами также хорошо защищает их от отложения парафина. Эпоксидные смолы эластичнее стекла, и при деформации труб смола не растрескивается. Но она имеет свои недостатки. Температура, при которой можно применять смолы, обычно невысокая – не более 60-80 0С.
В последние годы расширяется применение эмалированных труб. Они обладают наиболее прочным покрытием (значительно прочнее стекла), высокой температуростойкостью, морозоустойчивостью и гладкой поверхностью, на которой парафин не откладывается. Для защиты НКТ от агрессивных сред трубы покрываются несколькими слоями эмали. Технология нанесения эмали значительно сложнее технологии покрытия стеклом и эпоксидной смолой.
Общий недостаток покрытий в том, что внутренняя поверхность муфтового соединения труб остается незащищенной. В этом месте можно устанавливать эластичные проставки, перекрывающие незащищенное место, или протекторные кольца, потенциал материала которых таков, что кольца корродируют сами, защищая от коррозии близко расположенные участки трубы. Однако применение таких мер создает дополнительные трудности.
Порошковое покрытие, как и другие способы и методы изоляции, имеет большое количество преимуществ и, естественно, некоторые недостатки, к которым в первую очередь стоит отнести невысокую эластичность и повышенное водопоглощение. Хотя основным недостатком, в большей степени ограничивающим области применения, относится все-таки, невысокая ударная прочность данного вида покрытия.
2.1.2 Характеристика оборудования при удалении АСПО
Установка промысловая паровая передвижная предназначена для депарафинизации подземного и наземного оборудования скважин, а также для подогрева трубопроводов и другого нефтепромыслового оборудования.
Оборудование установки, включает котел паровой, цистерну, бак топливный, топливный и водяной насосы, вентилятор, электрооборудование, контрольно-измерительные приборы, обвязочные трубопроводы и силовую передачу, размещено на монтажной раме автомобиля и закрыто металлическим кузовом. Рама и кузов теплоизолированы. Привод оборудования установки осуществляется от тягового двигателя автомобиля через силовую передачу. Паровой котел, вентилятор высокого давления, насосы для подачи питательной воды и топлива в котел расположены в передней части монтажной рамы, а емкость для питательной воды и топлива- в задней части. Котел паровой вертикальный, цилиндрический, прямоточный с нижним расположением горелочного устройства.
Поверхность нагрева выполнена в виде двух цилиндрических змеевиков -наружного и внутреннего. Управление работой установки –дистанционное, из кабины водителя, в который расположены щит приборов, штурвалы регулирующего парового вентиля и вентиля для регулировки количества топлива, подаваемого в топку парового котла, и управление заслонкой вентилятора.
Таблица 6 – Техническая характеристика ППУ – 1600/100
Показатели | Значения |
Производительность по пару, м/с | 1,6 |
Давление пара, МПа | 10 |
Температура пара, °С | 310 |
Вместимость цистерны для воды, м2 | 5,2 |
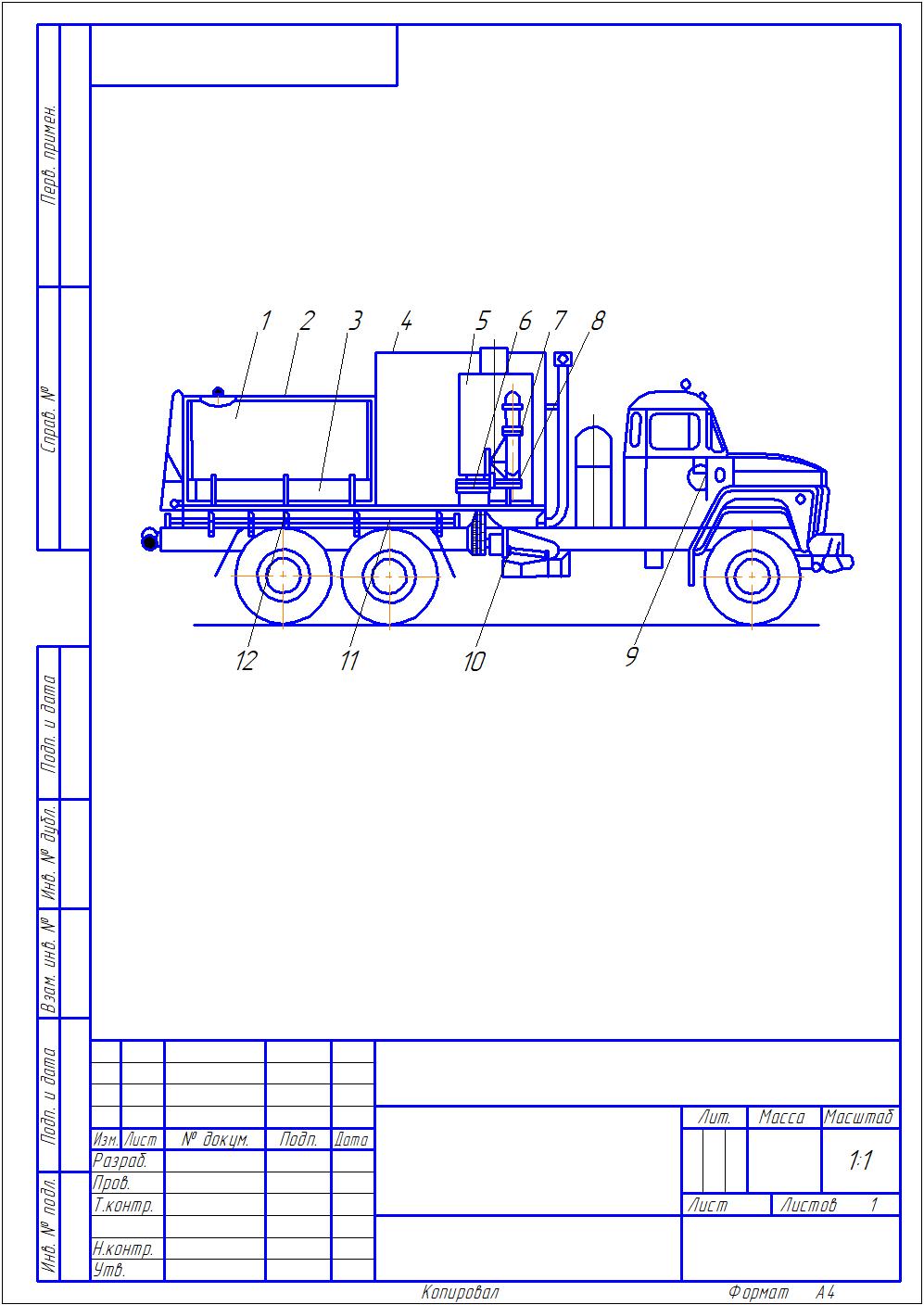
1- цистерна для воды; 2 - укрытие для цистерны; 3 - емкость для топлива, 4 -кузов; 5 - парогенератор; 6 - питательный насос; 7 - вентилятор высокого давления; 8 - топливный насос; 9 - приборы КИП и А; 10 - привод установки; 11 -магистральные трубопроводы: 12 - монтажная рама
Рисунок 4 – Промысловая паровая передвижная установка ППУА-1600/100
Для депарафинизации скважин горячей нефтью предназначен для нагрева и нагнетания нефти в скважину с целью удаления со стенок труб отложений парафина. Агрегат можно использовать также для депарафинизации трапов, мерников, манифольдов и др.
Весь агрегат состоит из нескольких узлов и систем: нагревателя змеевикового типа, нагнетательного насоса, силовой передачи, вспомогательного оборудования, трубопроводов, контрольно-измерительных приборов и системы автоматики.