Файл: 1. Металлорежущий станок. Понятие, основные части, классификация по группам и по точности.docx
ВУЗ: Не указан
Категория: Не указан
Дисциплина: Не указана
Добавлен: 18.03.2024
Просмотров: 6
Скачиваний: 0
ВНИМАНИЕ! Если данный файл нарушает Ваши авторские права, то обязательно сообщите нам.
1. Металлорежущий станок. Понятие, основные части, классификация по группам и по точности.
Металлорежущий станок – это оборудование, которое выполняет обработку заготовок на основе процесса резания с помощью режущего инструмента и выполнения требуемых для обработки формообразующих движений. Осн. части: главный привод, приводы подач, несущая система. Группы: 1) токарные и токарно-винторезные; 2) сверлильные и расточные; 3) станки для абразивной обработки; 4) станки для комбинированной обработки; 5) станки для обработки зубчатых колёс; 6) фрезерные; 7) станки для обработки линейчатых поверхностей при возвратно-поступательном движении. По точности: Н – нормальная точность; П – повышенная; В – высокая; А – особо-высокая; С – мастер-станок.
2. Понятие производящих линий, образующая производственные линии. Схема образования поверхности по способу следа.
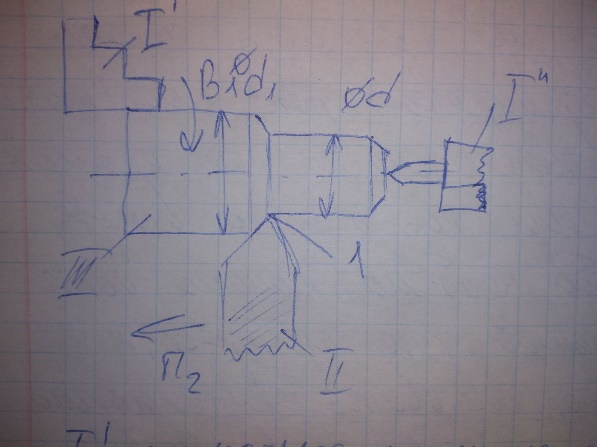
I1 – кулачковый патрон. I2 – поддерживающий центр. II – режущий инструмент. III – заготовка. П2 – поступательное движение. В – вращательное движение.
3.Понятие производящих линий, направляющая линия. Схема образования поверхности по способу копирования.
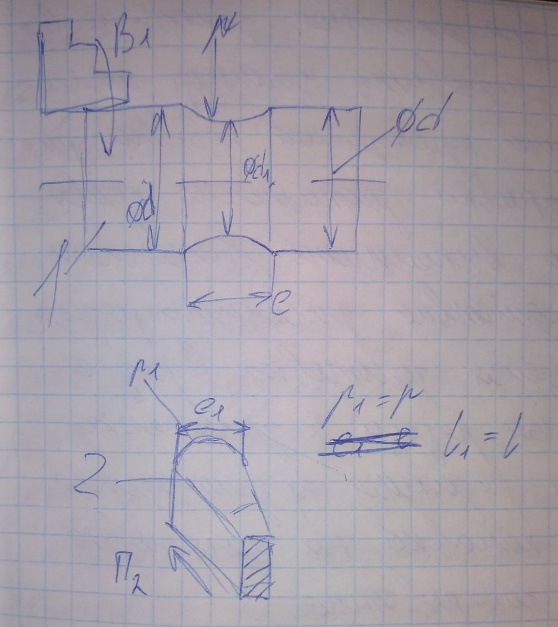
1 – обрабатываемая заготовка в кулачковом патроне.
2 – стержневой фасонный резец.
В – вращательное движение.
L1 -- ?
4. Сущность настройки станка по способу пробных проходов и промеров.
Инструмент подводится к заготовке. Рабочий включает приводы станка, выполняет обработку поверхности на диаметр первого прохода с учётом глубины t1, заканчивают обработку и выводят инструмент в исходное положение. С помощью измерительного инструмента измеряют полученный диаметр (фактический). Фактический диаметр сравнивают с расчетным. Если они не совпадают, то определяют дельта расхождения диаметров и корректируют настройку перемещения резца. Выполняют обработку на размер второго прохода. Сравнивают полученный размер и если фактический размер соответствует расчетному, то значит обработка закончена.
5. Сущность настройки станка по способу автоматического получения размеров.
Простым способом автоматического получения размеров является автоматика станка, выполняющая обработку по сигналам от взаимодействия упоров и путевых переключателей. Упор – это деталь в виде планки присоединяемая к перемещаемой части станка. На пути перемещения упора к неподвижной базовой детали станка присоединяют электро-переключатель. При взаимодействии упора и переключателя будет определяться команда для электро-привода (остановка, обратный ход). Чтобы правильно разместить взаимодействие упоров и переключателей необходимо выполнить расчёт настройки станка с учётом заданных размеров обработки, количества проходов и траектории перемещения.
6. Установочное движение понятие и схема выполнения при токарной обработке. Сущность движения врезания.
Установочное движение – это движение по установке режущего инструмента при его перемещении из исходного положения Оинструмента в точку на линии обрабатываемой поверхности с учётом глубины резания.
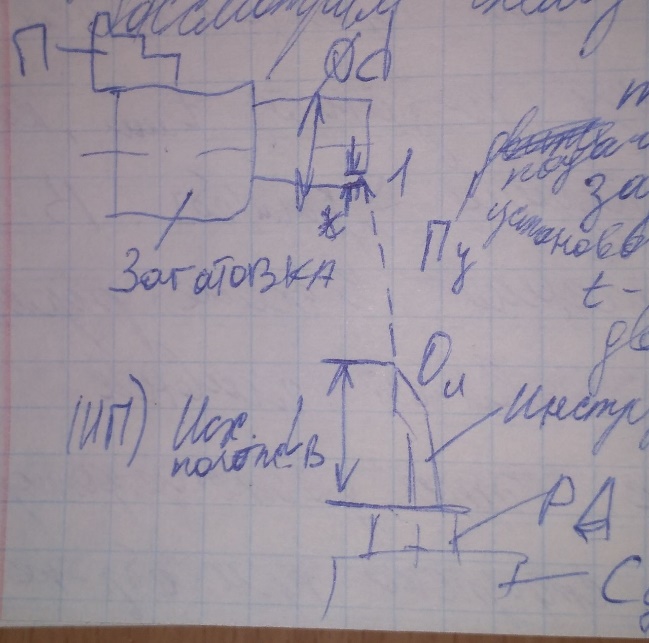
Сущность движения врезания: это движение является аналогом установочного по назначению. Однако, его выполнение имеет отличительные особенности: точка 1 находится на заготовке, поэтому инструмент перемещается из точки О в 1 с касанием поверхности; это движение выполняется при главном движении, поэтому при касании инструмента в точке 1 сразу начинается обработка, происходит быстрое переключение движения врезания на подачу обработки.
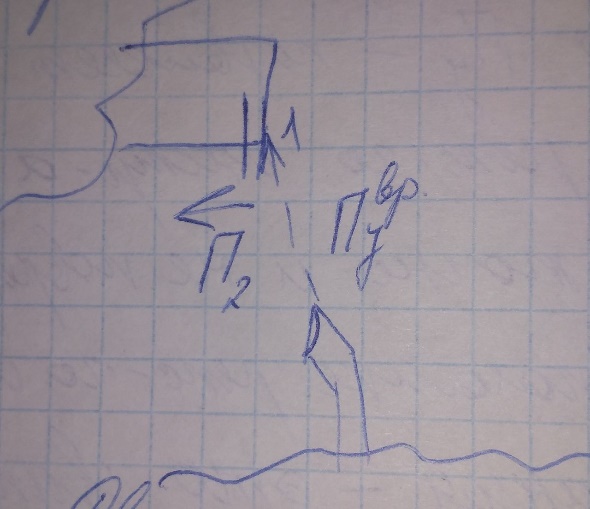
7. Движение деления: понятие и способы выполнения.
Это движение выполняемое при обработке некоторых видов поверхностей (многозаходная резьба, зубчатые колёса), когда необходимо выполнить перемещение процесса резания и обработку из одной области в другую, например: преобразование пазов на валу по методу копирования.
Способы: 1) Обработка по разметке.
2) С применением специальных устройств называемых делительными головками.
3) С помощью кинематических цепей станка называемых цепями деления.
8. Вспомогательное движение при обработке заготовки на станке, способы и назначения.
Вспомогательное движение – разные движения определённого назначения, которые выполняются при обработке заготовок на станках и реализующихся преимущественно механизмами ручного управления станком, либо специальными приводами, либо с помощью каких-либо устройств, которые могут встраиваться в станочную систему. Например: установка заготовки в приспособлении станка, подвод/отвод инструмента.
Способы и назначения: 1) Назначение вспомогательного времени на операцию обработки на основе справочника нормировщика. 2) На основе хронометража (замеров времени) при обработке заготовок на станке на определенной операции
Ёбаный рот этого тиом блять, ещё столько же надо делать
9. Назначение исполнительных движений станка по формообразованию поверхности заготовки (формообразующее движение).
Формообразующие движения – это движения, которые выполняются приводами станка для выполнения операции резания и получения заданных параметров обработки заготовки (размеров, геометрической формы, шероховатости). По назначению резания можно определить, что вращательное движение заготовки рассматривается как главное движение резания, сущность главного движения заключается в том, что оно обеспечивает образование стружки.
10. Технологические операции продольного и поперечного точения вала на токарном станке: схема и пояснение.
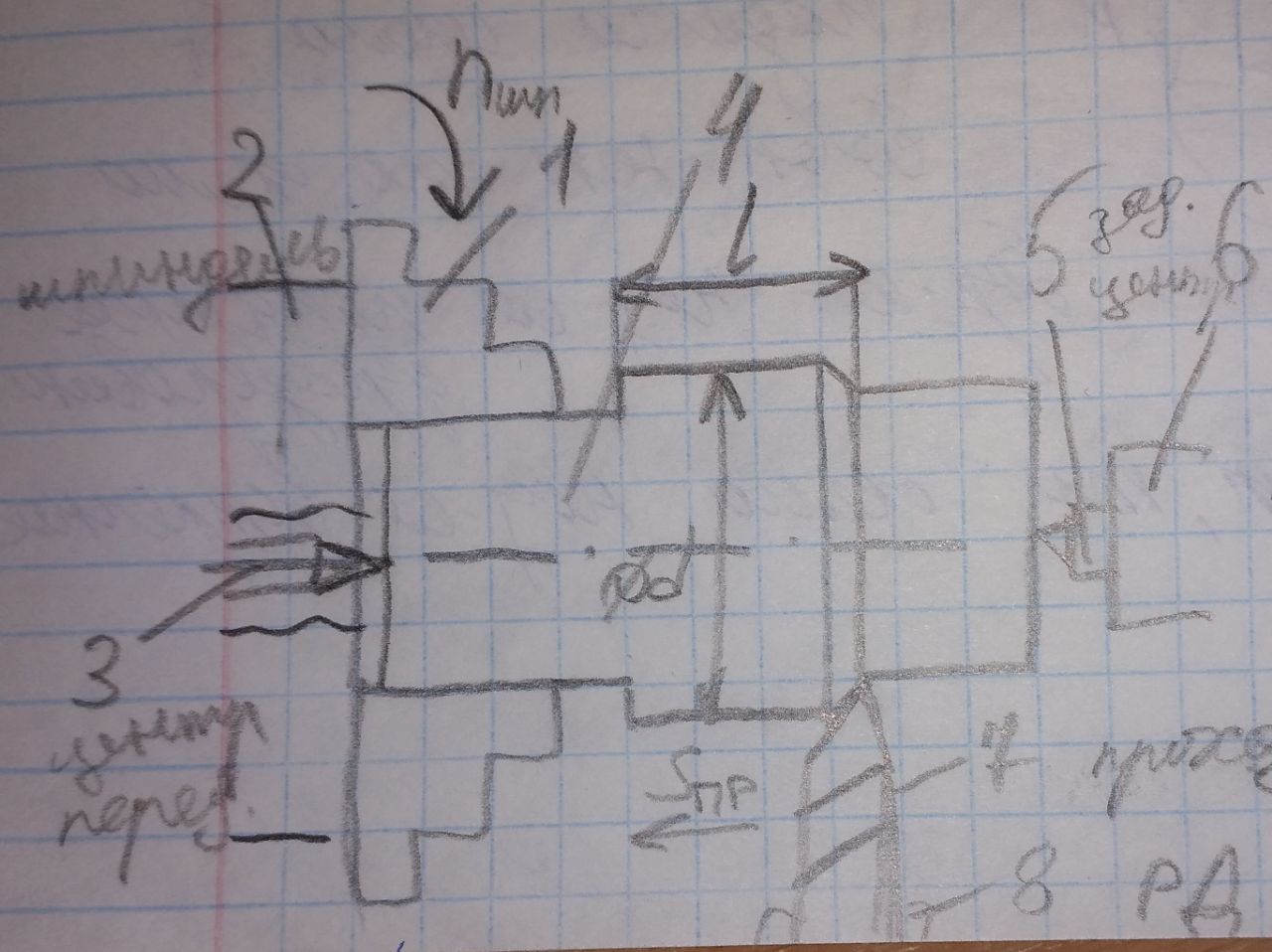
1 – трёх-кулачковый патрон; 2 – шпиндель; 3 – центр передний; 4 – заготовка; 5 – центр задний; 6 – пиноль; 7 – проходной прямой резец; 8 – резцедержатель; l – длина; Ød – диаметр заготовки; nшп – направление вращения шпинделя.
При обработке выполняется главное движение вращения заготовки и вспомогательное движение подачи инструмента.
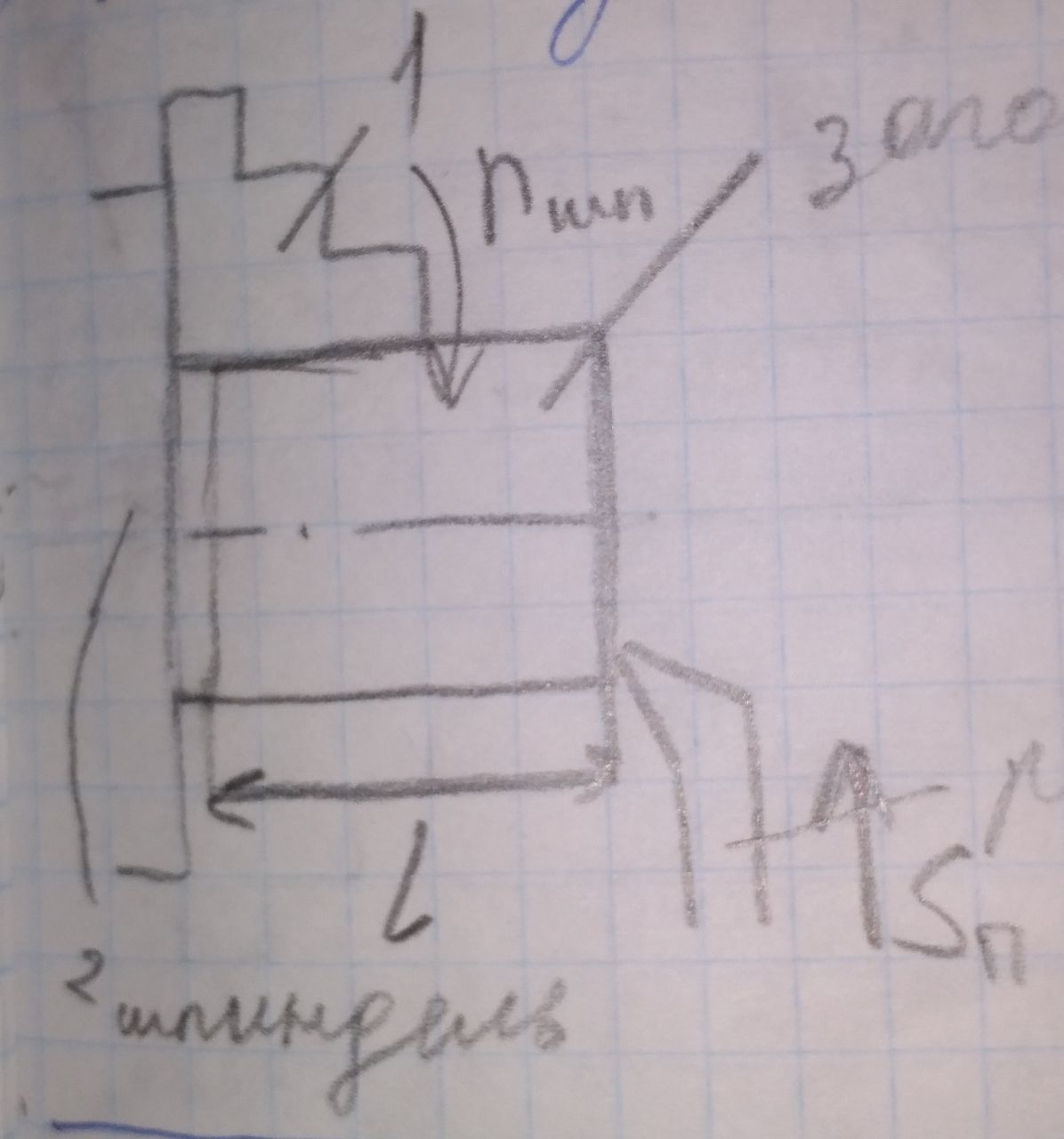
1 – трёх-кулачковый патрон; 2 – шпиндель; 3 – заготовка; 4 – подрезной резец.
11. Технологические операции расстачивания отверстий и канавки во втулке на токарном станке: схема и пояснение.
При обработке выполняется главное движение вращения заготовки и вспомогательное движение подачи инструмента.
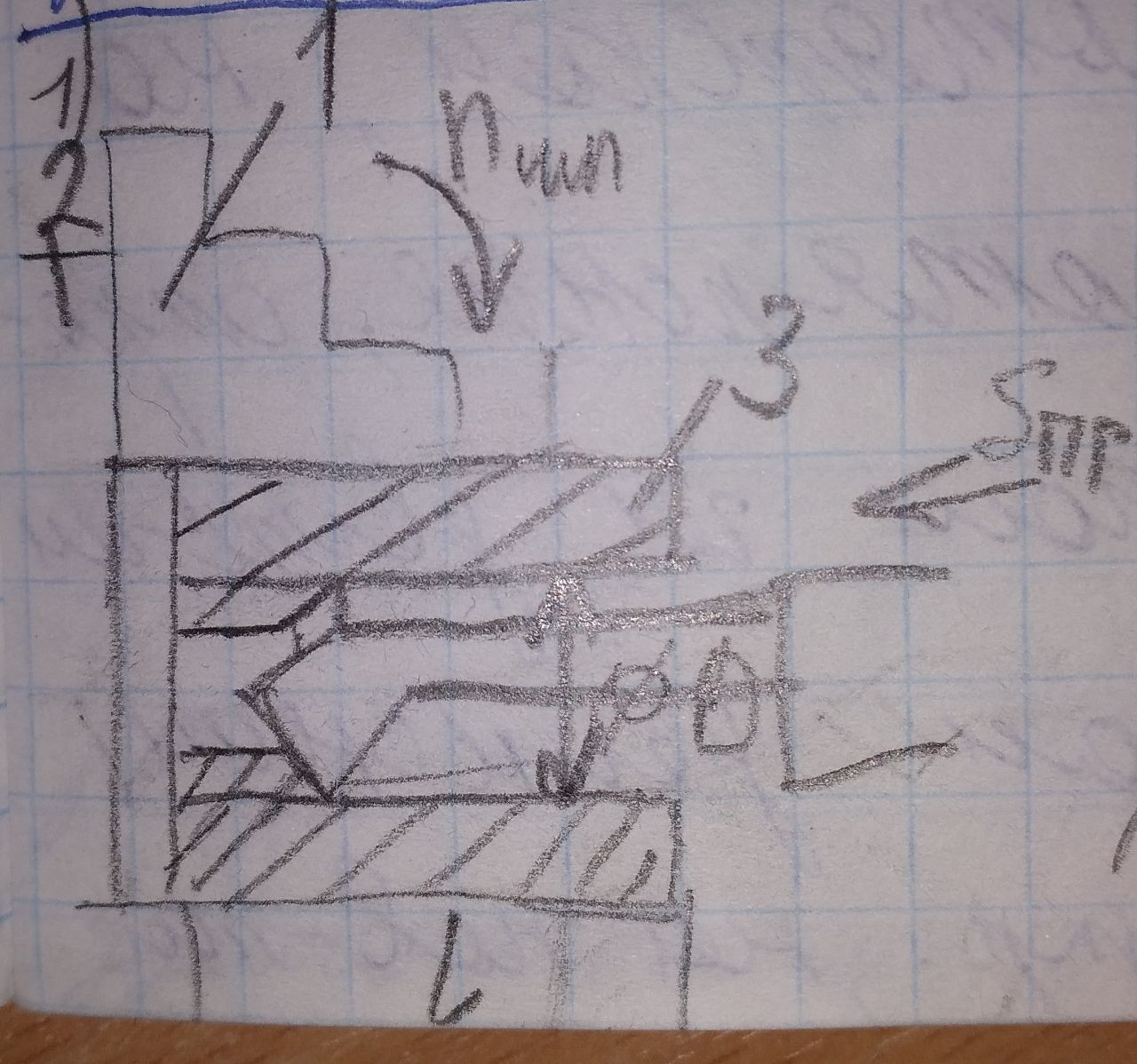
1 – трёх-кулачковый патрон; 2—шпиндель; 3 – заготовка; 4 – расточной проходной резец.
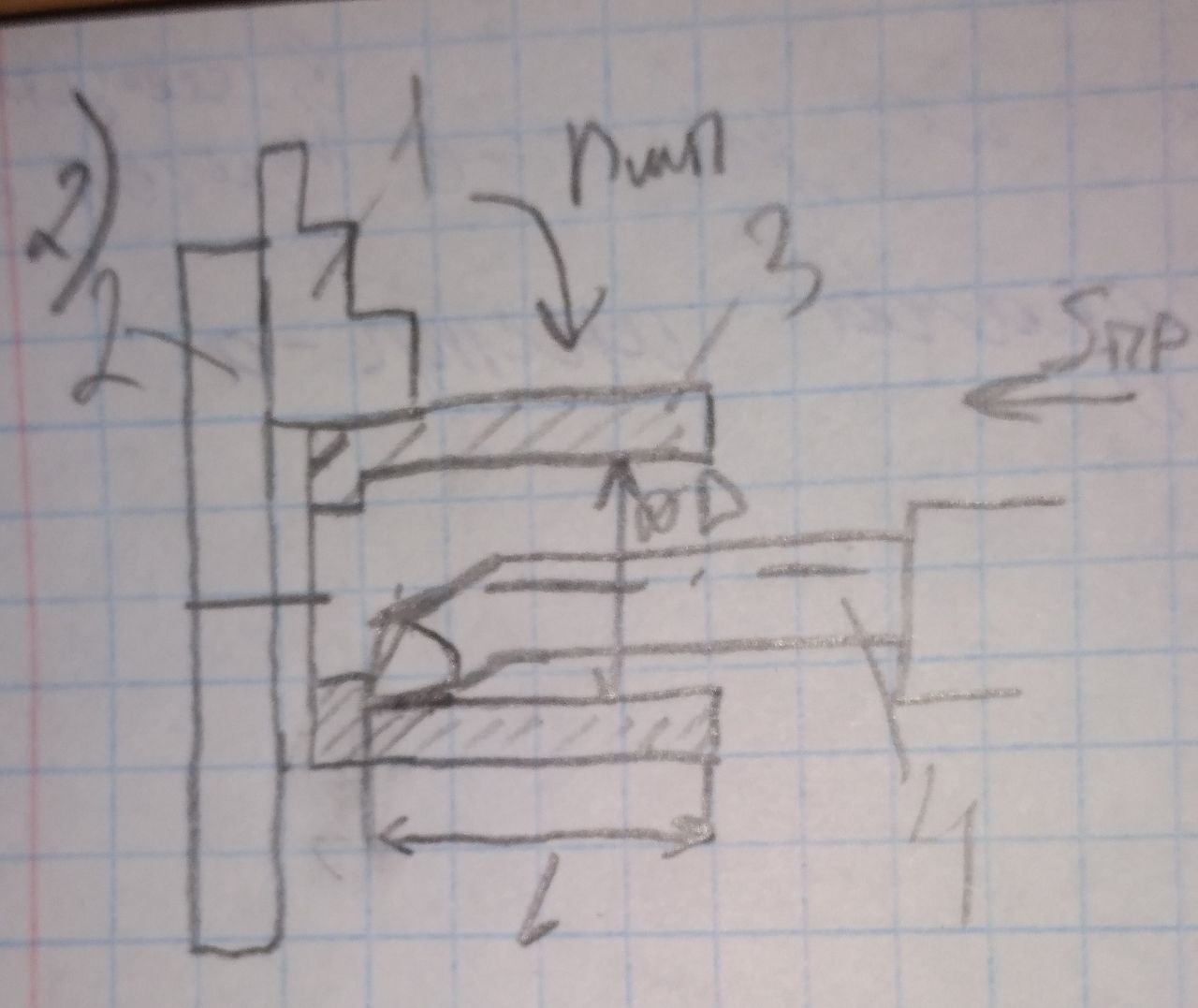
1 – трёх-кулачковый патрон; 2 – шпиндель; 3 – заготовка; 4 – проходной упорный расточной резец.
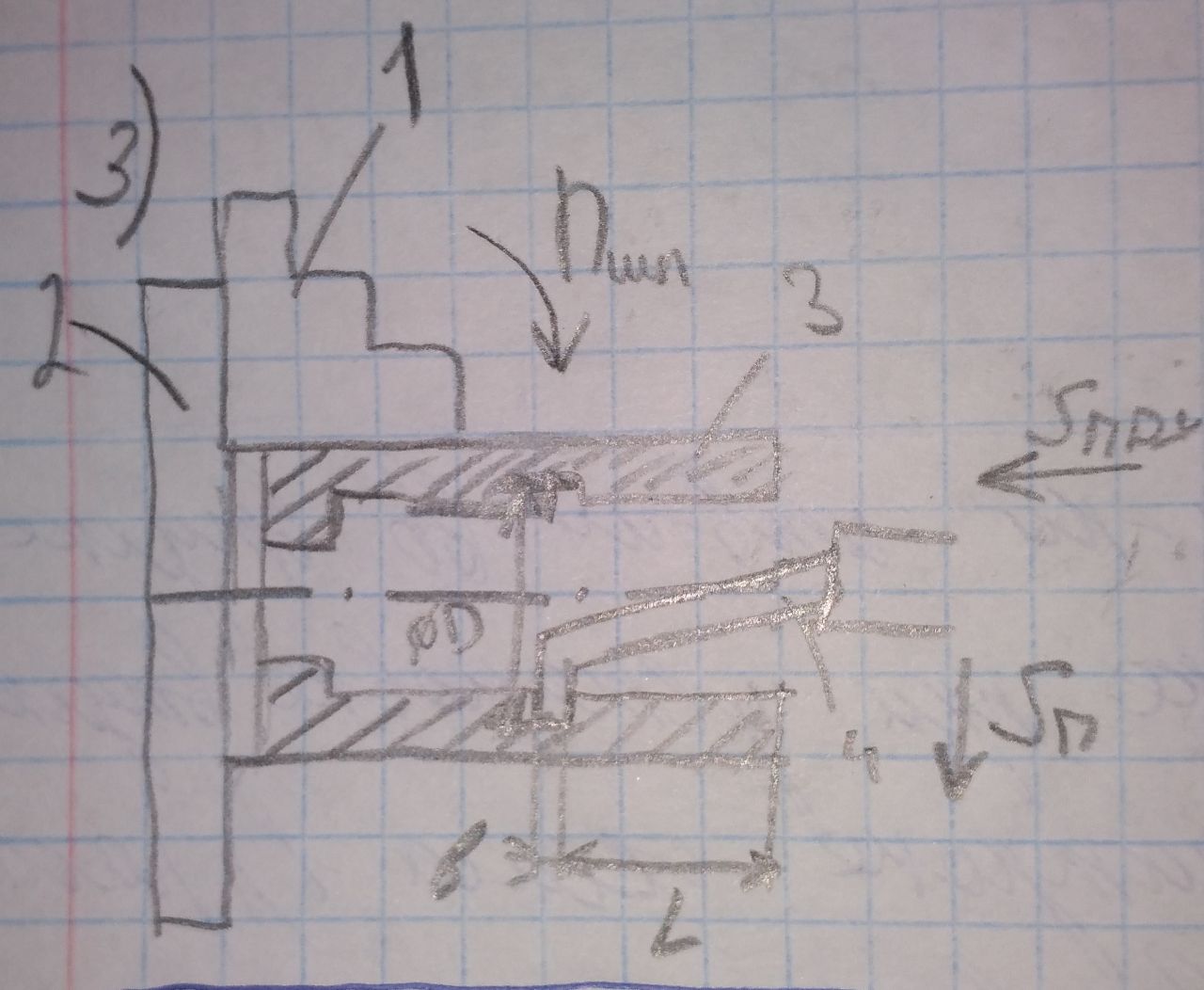
1 – трёх-кулачковый патрон; 2 – шпиндель; 3 – заготовка; 4 – расточной канавочный резец.
12. Технологические операции сверления отверстия на сверлильном станке: схема и пояснение. Виды свёрл.
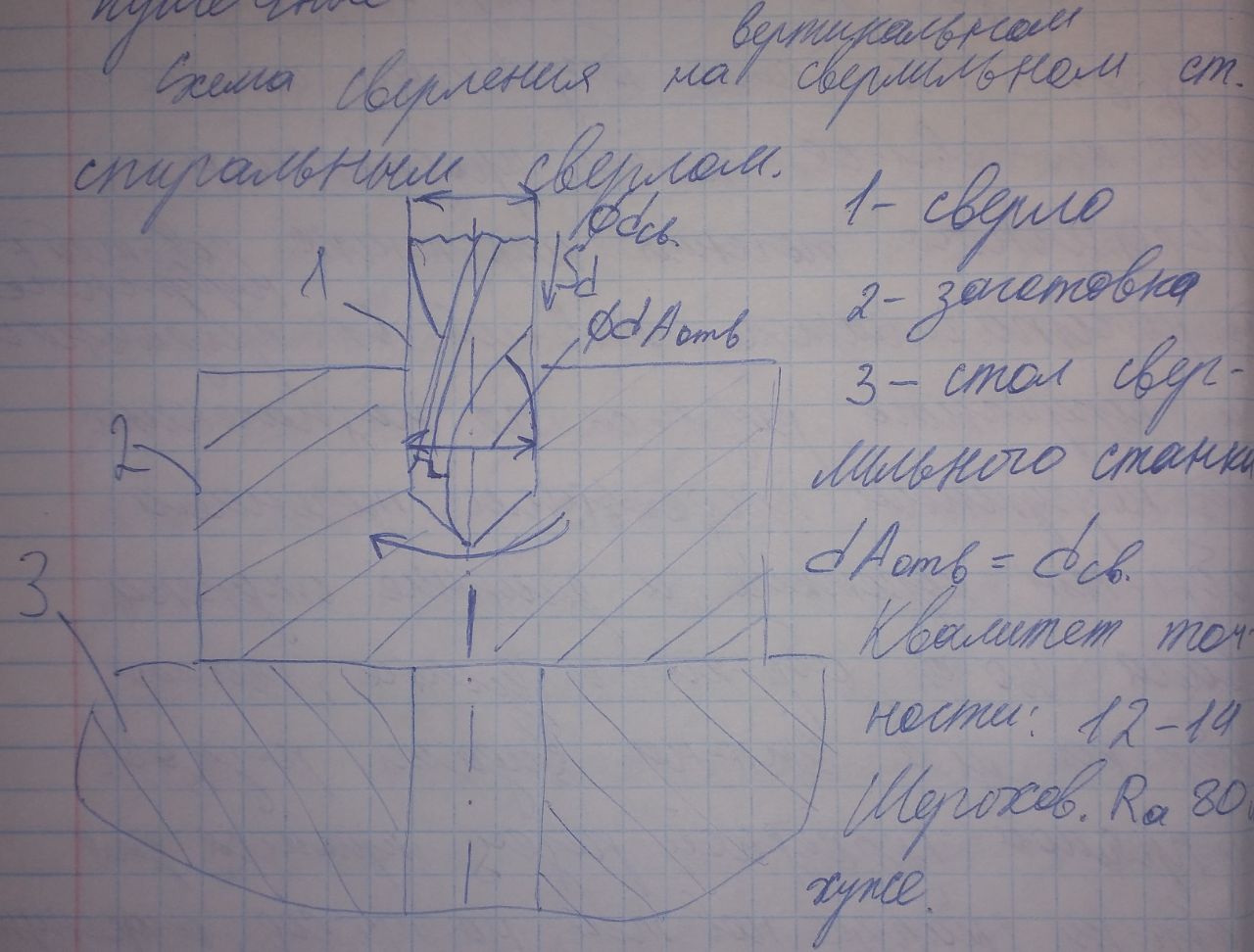
Виды свёрл: спиральное двулезвийное, кольцевое, пушечное.
13. Технологические операции зенкерования и развертывания на сверлильном станке: схема и пояснение.
Зенкерование рассматривается операция получистовой обработки при высокой производительности обработки поверхности (как же он заебал с этой тафтологией). Высокая производительность связана с быстротой срезания слоев за счёт увеличения числа лезвий.
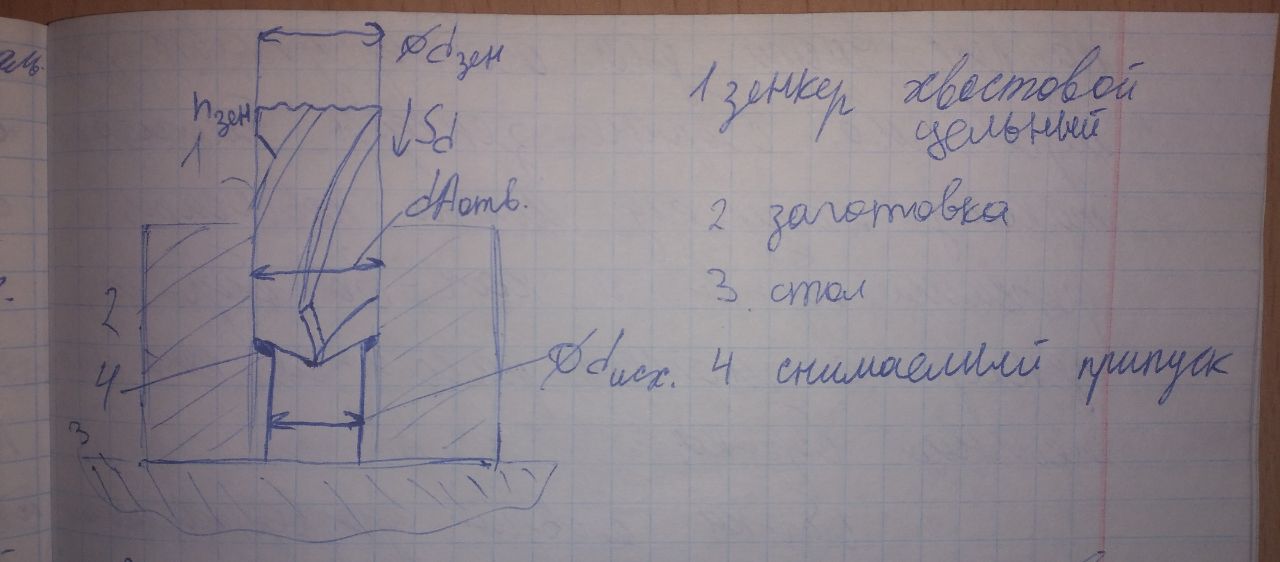
Развёртывание – это операция отделочной финишной обработки отверстий, которая завершает процесс достижения требуемых параметров точности и шероховатости, обеспечивая ИТ 7-8, Ra 10-5. Обработка выполняется по схеме сверления инструментом, который выполняет вращательно-поступательное движение при неподвижной заготовке.
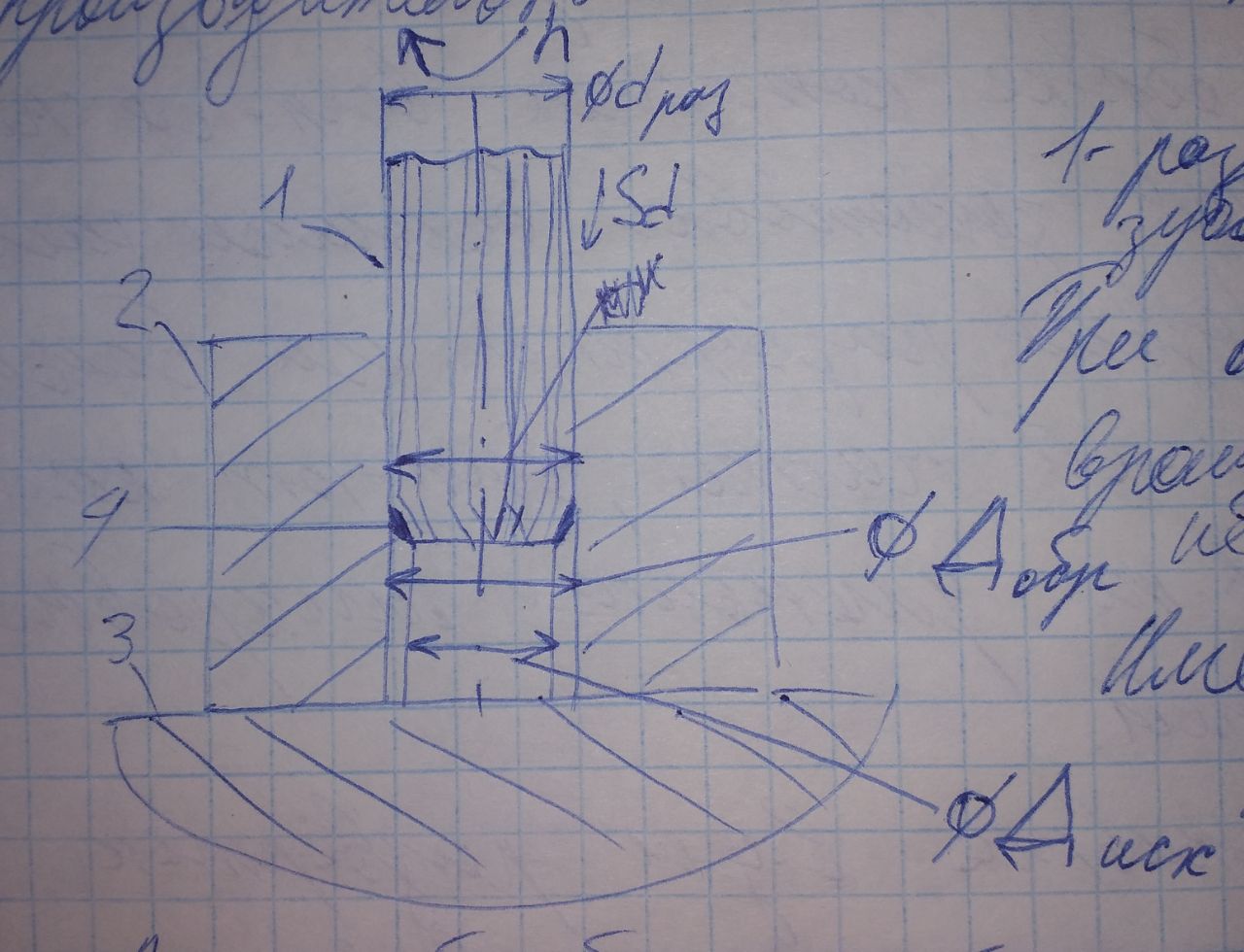
1 – развертка прямозубая цельная, при обработке выполняет вращательное движение и подачу; dраз – диаметр развертки; 2 – заготовка с исходным диаметром dисх ; после обработки образуется dобр ; 3 – стол станка; 4 – снимаемый припуск.
14. Технологические операции фрезерования на горизонтальном фрезерном станке: схема и пояснение. Виды фрез.
Ω мне кста зашёл новый рагнарёк
Фрезерование – процесс обработки резанием с помощью многозубового режущего инструмента фрезы на станках фрезерной группы.
1 – цилиндрическая фреза многозубая с шириной В, зубья фрезы являются острозаточенными винтовыми с наклоном зуба ω; 2 – оправка (приспособление для размещения фрезы относительно обработанной заготовки); 3 – фрезерный шпиндель; 4 – консоль (стойка) (в нее устанавливается правый хвостовик); 5 – стол; 6 – заготовка; t – глубина резания; Sг – горизонтальная подача.
Виды фрез: цилиндрические, дисковые, угловые, фасонные.
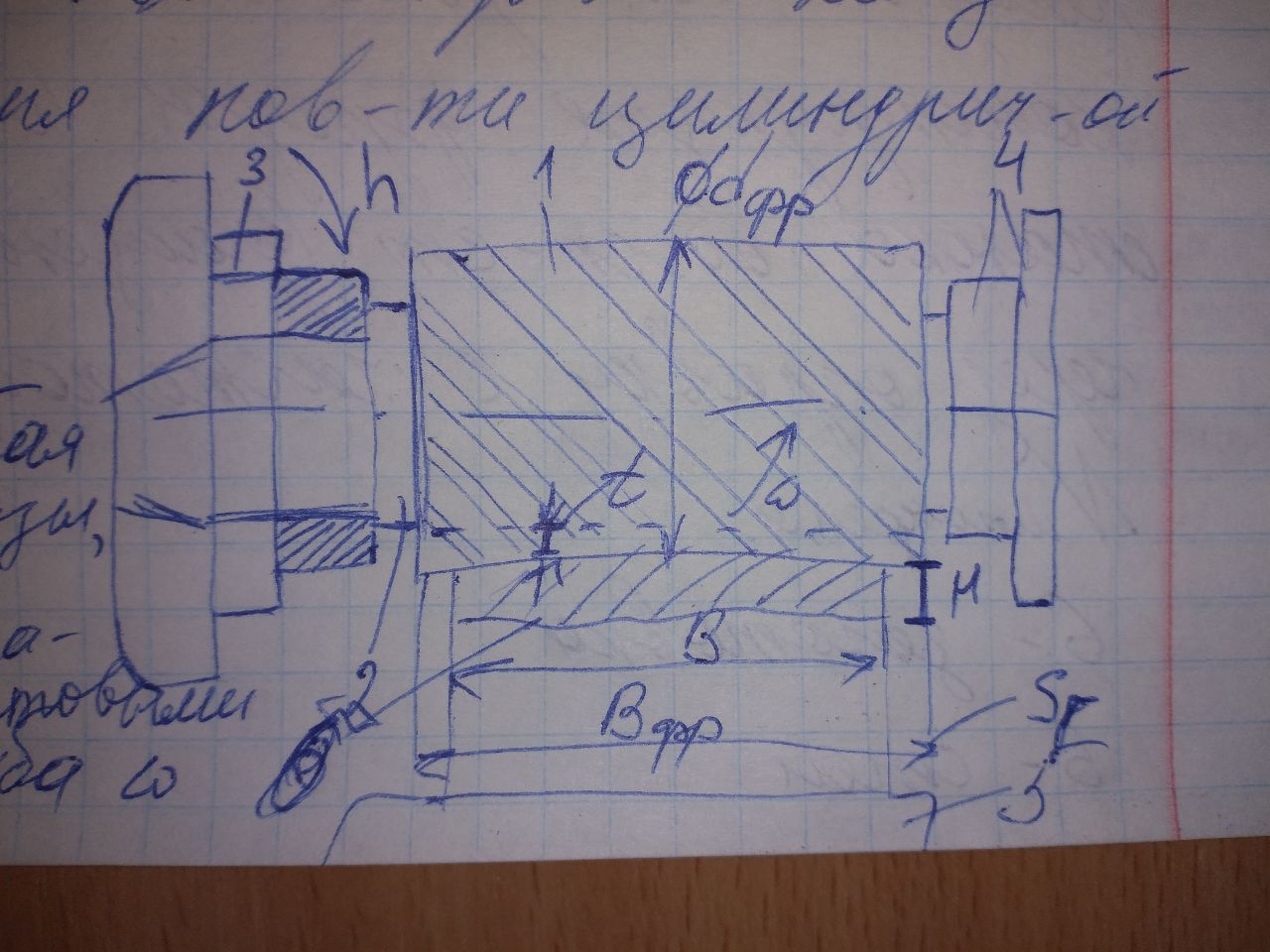
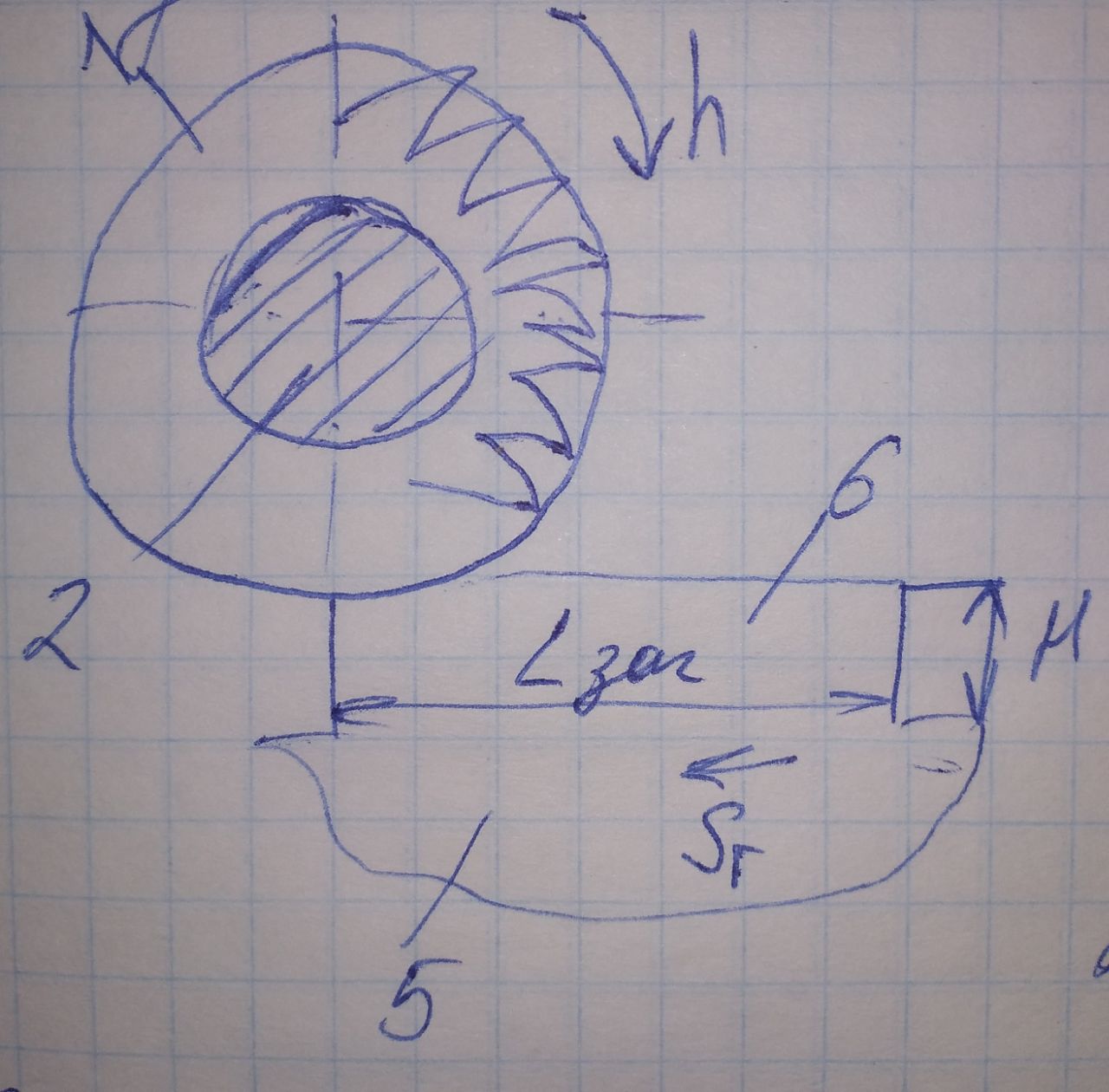
15. Технологические операции круглого шлифования поверхности вала на круглошлифовальном полуавтомате. Схема и пояснение.
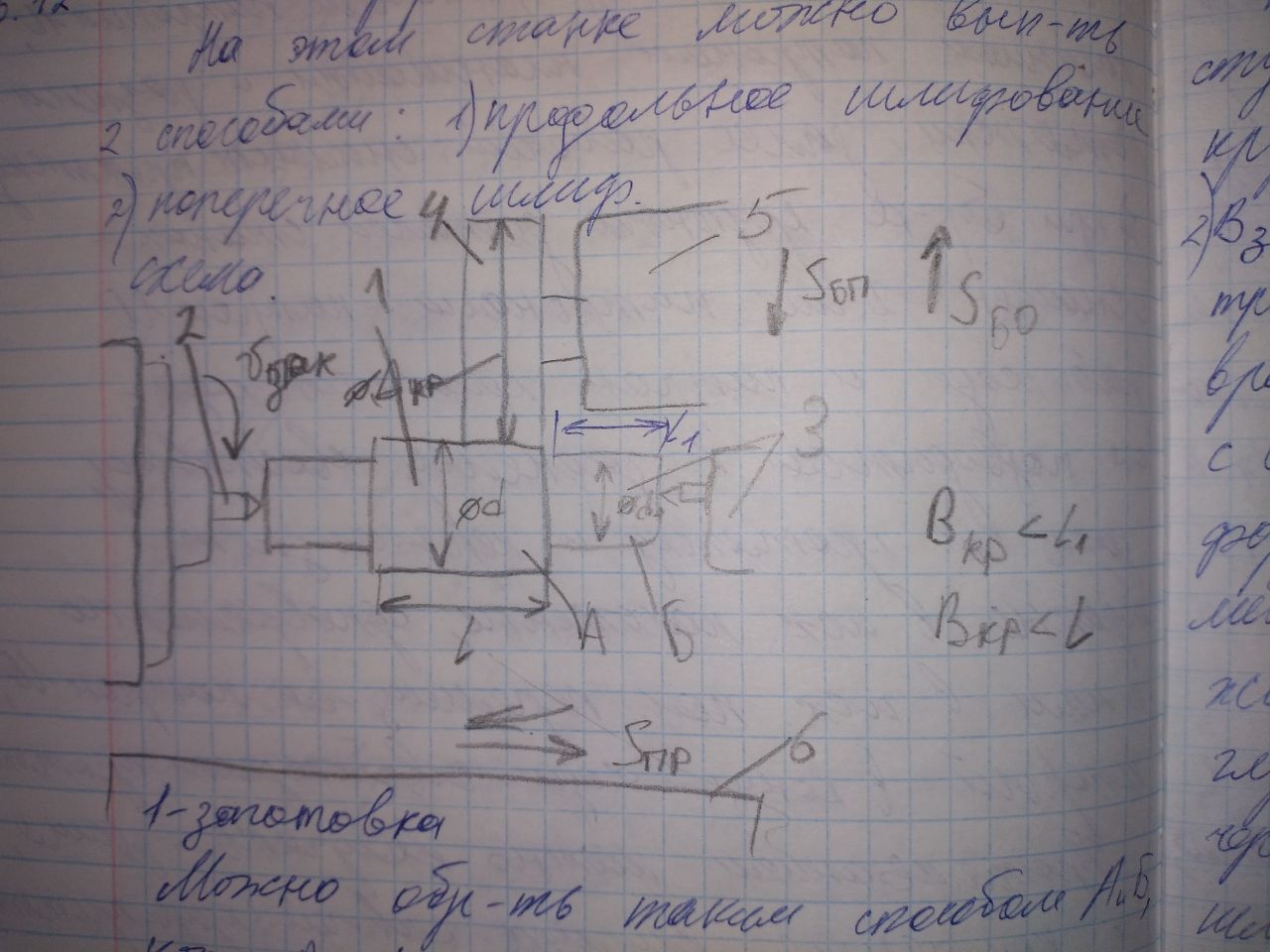
1 – заготовка; 2 – передняя бабка и передний центр с поводком; 3 – задняя бабка и задний центр; 4 – шлифовальный круг; 5 – шлифовальная бабка; 6 – стол шлифовального станка с передней и задней бабкой.
При шлифовании выполняется:
-
Главное вращательное движение круга, измеряется [м/с]; -
Вращение заготовки [м/мин] – это движение обеспечивает траекторию кругового направления для получения высокой точности изделия; -
Sпр продольная подача стола либо одного направления, либо режима выхаживания. Этот режим связан с глубиной припуска, позволяет выполнять через проходы черновое, получистовое и чистовое шлифование, что обеспечивает 6-7 квалитет.
16. Технологические операции протягивания отверстия на протяжном станке: схема и пояснение. Виды протяжек.
Принцип протягивания заключается в том, что заготовку размещают на планшайбе станка и закрепляют, внутри заготовки размещают протяжку и закрепляют, включают станок, сначала идёт рабочий ход вперед – снимается припуск и достигается точность 7-8 квалитета и шероховатость Ra 125063, а потом холостой ход обратно, станок выключают, снимают протяжку и обработанную заготовку.
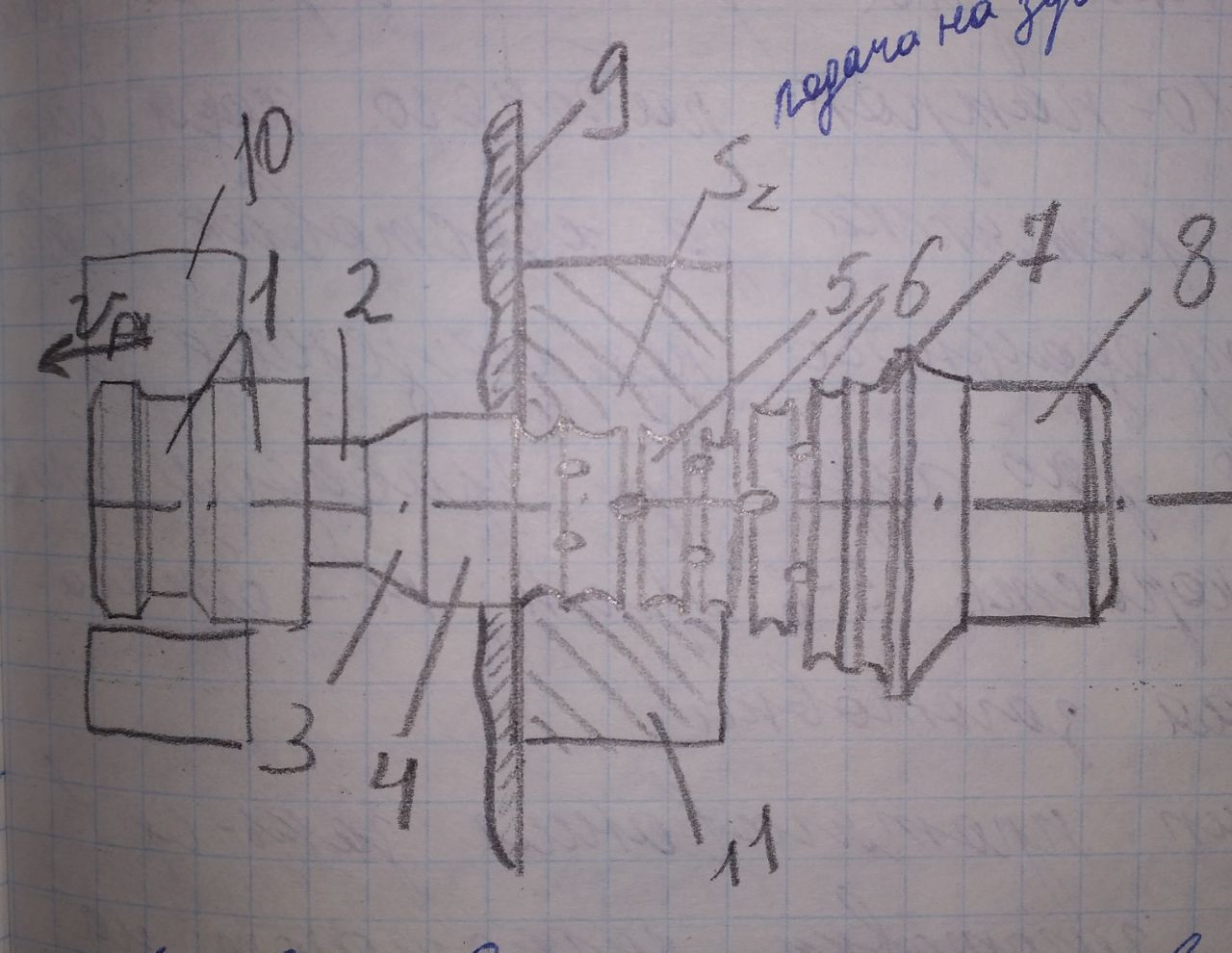