Файл: Разработка технологического процесса сборки ручной дуговой сварки банной печи.doc
Добавлен: 26.04.2024
Просмотров: 16
Скачиваний: 0
ВНИМАНИЕ! Если данный файл нарушает Ваши авторские права, то обязательно сообщите нам.
1.3 Технологичность сварной конструкции
Сварка банной печи выполняется ручной электродуговой сваркой
(РДС) штучными электродами . Была выбрана определённая последовательность скоса кромок а так же были подобранны инструменты для очистки шлака.
Так как эта конструкция ответственная и требует определённых нагрузок на жаропрочность, жаростойкость то эта конструкция выполняется с V – образной разделкой кромок с зазором 1-2мм. Конструкция разделки кромок обеспечивает требуемую точность при сборке, простоту и лёгкость сварки.
Данная печь имеет характер работы швов на разрыв, поэтому швы должны быть прочноплотными и должны испытывать определённую нагрузку т.к. температурный режим печи 500 -600 С.
1.4 Точность изготовления сварной конструкции
Данное изделие –печь для бани , конструкция ответственного назначения изготовляемая из жаропрочной высоколегированной стали печь относится к малогабаритным конструкциям, поэтому трудности при её изготовлении не должны возникнуть.
Печь рассчитывают на напряжения, деформации и статические нагрузки а так же должен соблюдаться технологический процесс при её изготовлении, высокое качество выполняемых работ и контроль сварных швов.
После термообработки и сварки печь не должна иметь напряжений и деформаций, толщина стали 10мм, припуск 1-2мм.
При сборке под сварку должна быть обеспечена точность сборки деталей в пределах размеров и допусков , указанных в рабочих чертежах. Чтобы обеспечить требуемую точность сборки печи нужно применить сборочно –сварочное приспособление предохраняющее конструкцию от напряжений и деформаций и не затрудняющее выполнение сварочных работ.
Детали, подлежащие сварки должны свариваться во всех пространственных положениях
Сборочно-сварочное приспособление должно быть периодически проверено (правильно ли мы закрепили деталь и т.д.).
Детали подаваемые на сборочные операции должны быть обезжиренные, хорошо зачищены и должны пройти термообработку перед сваркой.
Свариваемые кромки так же должны быть очищены от влаги, ржавчины и масла.
1.5 Требования к основным и вспомогательным материалам
Требования к материалам.
Весь поступающей металл должен иметь:
- сертификат, в котором указывается марка металла, вид проката, его размеры, количество штук, номер плавки, химический состав, физические и технологические свойства. Если сертификата нет, то металл не допускается на производство.
Детали подаваемые на сборочные и сварочные операции должны быть сухими, чистыми и выправленными. Сварочные кромки должны быть очищены от влаги, краски, ржавчины и масла.
Требования к сварочным электродам:
1)стабильное горение и хорошее формирование шва;
2)получение сварного шва заданного химического состава;
3)спокойное и равномерное расплавление электродного стержня и покрытия;
4) минимальное разбрызгивание электродного металла и высокая производительность;
лёгкая отделяемость шлака и достаточная прочность покрытия;
5) сохранение технологических и физико –химических свойств в течении определённого времени;
7) минимальная токсичность при изготовлении и сварки.
Электроды должны поставляться в пачках весом 5 кг, иметь ГОСТ, номер плавки. Так же должен быть сертификат, где указывается марка, диаметр, завод изготовитель, масса, химический состав, номер стандарта.
В данном случае при изготовлении сварной конструкции я использовал электроды ОК 68.15; тип Э -50А, ГОСТ 9466-75; аналоги (ЦЛ-41, УОНИ 13НЖ, АНБ -1), - электроды для сварки нержавеющей теплоустойчивой стали, тип покрытия –основное, электрод даёт ферритный металл шва. Обеспечивается высокая стойкость сварных соединений в сернистых газах, ток постоянный, полярность прямая, применяется во всех пространственных положениях.
Химический состав электрода %:
С | Si | Mn | Cr | Ni | Мо | Сu |
0,06 | 0,5 | 0,7 | 12,5 | 0,6 | 0,5 | 0,2 |
Механические свойства: предел текучести -390мПа; предел прочности 870мПа; относительное удлинение 25%; данные получены после термообработки при температуре 750С в течение часа.
-
Требования к качеству сварных швов
Сварка ответственных конструкций должна производится по технологическому процессу, обеспечивающему хорошее качество сварных соединений и изделия.
Для электродуговой сварки применяются электроды марки ОК 68.15. Электроды перед сваркой следует просушить, прокалить при температуре 100С.
При многослойной сварке после наложения каждого слоя, особенно корневого, необходимо защищать швы и свариваемые кромки от шлака и устранять дефекты. По окончании сварки швы и прилегающие к нему зоны должны быть зачищены от шлака, металлических брызг и грязи.
Твёрдость металла шва сварных соединений из стали марки 20Х13 выполненными ручной электродуговой сваркой должна составлять 260 HB.Требование на корозионностойкость сварного соединения должна соответствовать чертёжному проекту или технической документации.
В сварных соединения не допускаются следующие дефекты: холодные трещины, подрезы, пористость наружной поверхности шва, прожоги.
-
Требование к квалификации сварщика
Все рабочие, допускаемые к изготовления сварной конструкции должны пройти соответствующие квалификационные испытания. Эти испытания должны повторяться два раза в год, по этому распоряжением по цеху создаётся специальная комиссия, которая проверяет теоретическую подготовку и практические навыки всех специалистов. Практическая подготовка у сварщиков включает в себя умение практически качественно выполнять сварку соответствующего изделия и соединений.
Сварка печи должна осуществляться сварщиком 3-4 разряда, которые прошли аттестацию и все испытания, так как эта конструкция малоответственная.
2.ТЕХНОЛОГИЧЕСКИЙ ПРОЦЕСС ИЗГОТОВЛЕНИЯ СВАРНОЙ КОНСТРУКЦИИ
2.1 Расчленение конструкции на узлы и подузлы
Эскиз печки
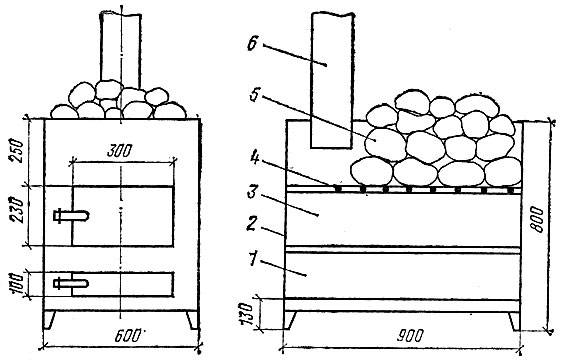
Собираемая печь расчленяется технологом на отдельные детали , более простые по форме имеющий общий вес , чтобы обеспечить удобство работы , простоту и минимальные деформации и напряжения после сварки.
В технологическом процессе подробно описывается порядок сборки и сварке деталей и узлов печи в целом.
Сборка и сварка некоторых деталей может осуществляться вручную, а другие детали и узлы свариваются по возможности при помощи специальных сборочно-сварочных приспособлений. После сборки (перед сваркой) конструкция должна контролироваться ОТК – отделом технического контроля.
Сварку данного изделия производить (РДС) ручной дуговой сваркой плавящимся электродом.
После сварки данное изделие должно подвергаться термообработке и визуальному контролю сварных швов на наличие дефектов.
Прежде всего, необходимо изготовить топку. Ее размеры каждый определяет сам, но профессионалы советуют при ширине 0.5 метра делать такую же высоту.
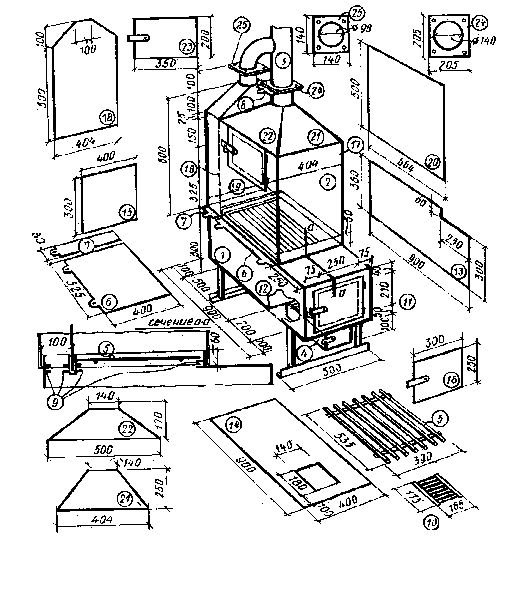
Типовой чертеж печи для бани из металла предполагает, что топка будет состоять из двух секций. В первой из них происходит сжигание топлива, а вторая нужна для сбора золы. Учитывая это, их разделяют решеткой и делают отдельные дверцы.
Стоит отметить, что окно секций для сбора золы часто используют для создания тяги, которая необходима для горения.
Если чертеж банной печи из металла предполагает размещение каменки, то верхнюю часть топки также изготавливают из решетки
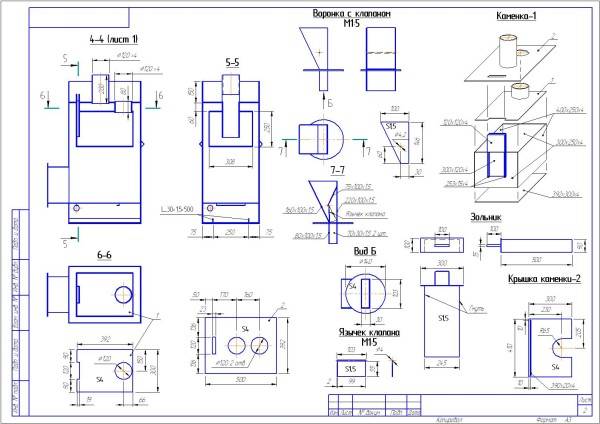
2.2 Заготовительные операции
Существуют следующие виды заготовительных операций:
- правка;
- разметка;
- резка;
- обработка кромок;
- гибка и очистка под сварку.
Так как печка состоит из листов, трубы и уголков, то необходимо перед сваркой выполнить следующие операции:
-
Правка листов
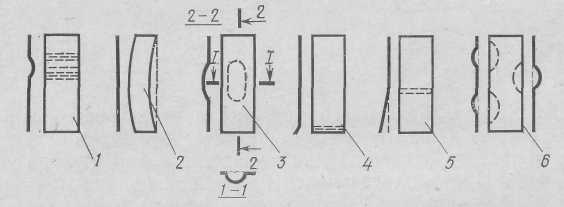
Виды деформаций листовой стали: 1- волнистость; 2- серповидность в плоскости; 3- местные выпучины;4- заломленные кромки; 5- местная погнутость; 6- волнистость поперёк части листа.
Листовой прокат требует правки в там случае, если его поставляют в неправленом виде, а так же если деформации возникли при транспортировании. Наиболее часто встречающиеся виды деформаций показано на рис 1.
Правка осуществляется созданием местной пластической деформации и обычно производится в холодном состоянии для устранения волнистости листов и полос толщиной 0,5 – 30мм применяют многовалковые машины. Исправление достигается многократным изгибом, при пропускании листов между ними и верхними рядами валков расположенных в шахматном порядке рис 2,а.
Правку мелко – и среднесортового, а так же профильного проката производят на роликовых машинах (рис 2, б), работающее по той же схеме что и листоправильные.

Схемы правки листовых и профильных элементов:
а- на листоправильных вальцах; б – в углоправильных вальцах; в – на прессе.
В случае необходимости создания более значительных деформаций правка и гибка стали должна производится в горячем состоянии после нагрева до 900°С для стали классов С 52, С60. Деформирование при высокой температуре сопровождается процессом кристаллизации, и пластические свойства металла не снижаются.
2) Разметка – операция по перенесению формы и размеров изделия на заготовку.
Для разметки применяются следующие инструменты:
1-чертилка – стержень из инструментальной стали, закаленный в острозаточенный, средняя часть его утолщена для удобного держания в руке.
2-Линейки – обычные, стальные, масштабные или со скошенными рабочими кромками, обеспечивающие большую точность разметки.
3-Угольники – обычные слесарные и с Т – образной полкой; последние более производительны и удобны в работе.
4- Разметочные циркули – для нанесения дуг и окружностей, деления отрезков на части, перенесения размеров и т.п. Так же применяются штангенциркули с точностью 0,05мм.
5-кернеры – для закрепления разметочных линий путём накернивания и для наметки центров отверстий.
6- молотки - для кернения весом 100 -150гр
Для пространственной разметке применяются более сложные инструменты:
1-рейсмусы – различных конструкций, являющиеся основным инструментом при пространственной разметке.
2-разметочные плиты – массивная чугунная плита тщательно простроганная , с высокой точностью взаимоперпендикулярности верхней плоскости и боковых сторон. Служит для установки деталей и рейсмуса при разметке.
2) Резка
Резка деталей с прямолинейными кромками из листов до 40мм, как правило производится на гильотинных ножницах (рис 3,а). Разрезаемый лист 2 заводится между верхнем 4 ножами до упора 5 и зажимается прижимом 3. Верхний нож , нажимая на лист, производит скалывание.
Схема резки на ножницах различных типов
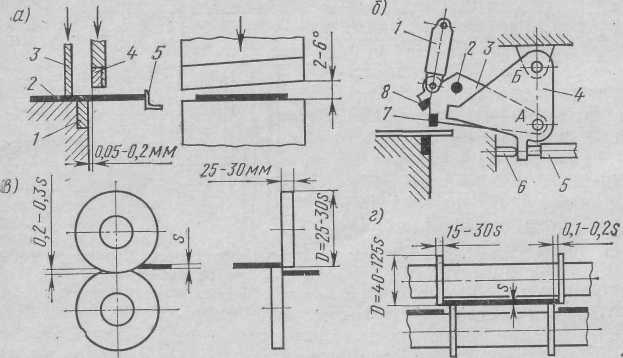
Прямой рез со скосом кромки под сварку можно получить, используя специальные ножницы (рис 3.б).
Дисковые ножницы (рис 3 в) позволяет осуществлять вырезку листовых деталей непрямолинейными кромками толщиной 20 -25мм.
Для поперечной резке фасонного проката применяют пресс- ножницы с фотонными ножами или дисковые пилы.
Ручную и полуавтоматическую резку листов проводят по разметке, автоматическую- с помощью копирных устройств, по масштабному чертежу или на машинах с программным управлением.
3)Обработка кромок
Механическую обработку кромок на станках производят: а) для обеспечения требуемой точности сборки; б) для обработки фасок сложного очертания; в) для удаления металла кромок, обрезанных ножницами или с помощью термической резки, когда это считается необходимым. При обработке длинных