Добавлен: 28.04.2024
Просмотров: 41
Скачиваний: 1
ВНИМАНИЕ! Если данный файл нарушает Ваши авторские права, то обязательно сообщите нам.
отравляют цинк-хромовые катализаторы обратимо, а медьсодержащие катализаторы – необратимо. Необходима также тщательная очистка газа от карбонила железа, который образуется в результате взаимодействия оксида углерода с железом аппаратуры. На катализаторе карбонил железа разлагается с выделением элементного железа, что способствует образованию метана.
Таким образом, процесс получения метанола является гетерогенно-каталитическим. Лимитирующая стадия – адсорбция водорода на поверхности катализатора.
5.Описание технологической схемы процесса
Рассмотрим два варианта производства метанола
5.1 Процесс при 32МПа:
Технологический процесс получения метанола из оксида углерода и водорода включает ряд операций, обязательных для любой технологической схемы синтеза. Газ предварительно очищается от карбонила железа, сернистых соединений, подогревается до температуры начала реакции и поступает в реактор синтеза метанола. По выходе из зоны катализа из газов выделяется образовавшийся метанол, что достигается охлаждением смеси, которая затем сжимается до давления синтеза и возвращается в процесс.
Технологическая схема получения метанола при давлении 32 МПа:
1, 2 – фильтры (масляный и угольный), 3 – колонна синтеза, 4 – холодильник-конденсатор, 5 – сепараторы, 6 – компрессор, 7 – сборник метанола-сырца.
Описание технологической схемы получения метанола при давлении 32 МПа.
Сжатый до 32 МПа синтез-газ очищается в масляном фильтре 1 и в угольном фильтре 2, после чего смешивается с циркуляционным газом и поступает в колонну синтеза 3.
Смещанный газ (на схеме – синтез-газ), пройдя через кольцевой зазор между катализаторной коробкой и корпусом колонны 3 (рис.11) (колонна синтеза метанола высокого давления – рис.13), поступает в межтрубное пространство теплообменника, расположенного в нижней части колонны (рис.13). В теплообменнике 1 (рис.13) газ нагревается до 330-3400 С и по центральной трубе, в которой размещен электроподогреватель 3 (рис.13), поступает в верхнюю часть колонны и проходит последовательно пять слоев катализатора 4 (рис.13).
После каждого слоя катализатора, кроме последнего, в колонну синтеза вводят определенное количество холодного циркуляционного газа (холодный байпас)
2 (рис.13)для поддержания необходимой температуры (проведение процесса синтеза метанола по ЛОТ).
После пятого слоя катализатора контактный газ направляется в теплообменник, где охлаждается до 300-385 0С 130 0С, а затем в холодильник-конденсатор типа «труба в трубе» 4 (рис.11). Здесь газ охлаждается до 30-35 0С и продукты синтеза конденсируются.
Метанол-сырец отделяют в сепараторе 5 и направляют в сборник 7, после чего выводят на ректификацию.
Газ проходит второй сепаратор 5 для выделения капель метанола, компримируется до давления синтеза турбоциркуляционным компрессором 6 и возвращается на синтез. Продувочные газы выводят перед компрессором и вместе с танковыми газами используют в качестве топлива.
6 пункт Колонна синтеза метанола
Колонна синтеза метанола при 32 МПа:
1 – теплообменник; 2 – холодный байпас; 3 –электроподогреватель; 4 - катализатор
5.2 Процесс при 5МПа:
1, 10 –турбокомпрессоры, 2 –подогреватель природного газа, 3 –реактор гидрирования сернистых соединений, 4 –адсорбер, 5 –трубчатый конвектор, 6 –котел-утилизатор, 7, 11, 12 –теплообменники, 8, 14 –холодильники-конденсаторы, 9, 15 –сепараторы, 13 –колонна синтеза, 16 –сборник.
Описание технологической схемы получения метанола при давлении 5МПа
Природный газ сжимается турбокомпрессором 1 до давления 3 МПа, подогревается в подогревателе 2 за счет сжигания в межтрубном пространстве природного газа и направляется на сероочистку в аппараты 3 и 4, где последовательно осуществляется каталитическое гидрирование органических соединений серы на алюмокобальтмолибденовом катализаторе и поглощение образующегося сероводорода адсорбентом на основе оксида цинка. После этого газ смешивается с водяным паром и диоксидом углерода в соотношении СН4 : Н2О : СО2 = 1 : 3,3 : 0,24.
Смесь направляют в трубчатый конвертор 5, где на никелевом катализаторе происходит паро-углекислотная конверсия при температуре 850 - 870 0С.
Теплоту, необходимую для конверсии, получают в результате сжигания природного газа в специальных горелках. Конвертированный газ поступает в котел-утилизатор 6, где охлаждается до 280 - 290 0С. Теплоту выходящего газа используют в теплообменнике
7 для подогрева питательной воды, направляемой в котел-утилизатор. Пройдя воздушный холодильник 8 и сепаратор 9, газ охлаждается до 35-40 0С. Охлажденный конвертированный газ сжимают до 5 МПа в компрессоре 10, смешивают с циркуляционным газом и подают в теплообменники 11, 12, где он нагревается до 220-230 0С.
Нагретая газовая смесь поступает в колонну синтеза 13, температурный режим в которой регулируют с помощью холодных байпасов (проведение процесса синтеза метанола по ЛОТ). Далее газовая смесь охлаждается в холодильнике-конденсаторе 14, сконденсировавшийся метанол-сырец отделяется в сепараторе 15 и поступает в сборник 16. Циркуляционный газ возвращается на синтез, продувочные газы отдают на сжигание в трубчатую печь.
В
следствие снижения температуры синтеза при низком давлении процесс осуществляется в условиях, близких к равновесию, что позволяет увеличить производительность агрегата.
Колонна синтеза метанола при 5 МПа:
1- фарфоровые шары; 2 – катализатор
5.3 Функциональная схема производства метанола
Технологический процесс получения метанола из оксида углерода и водорода включает ряд операций, обязательных для любой технологической схемы синтеза. Газ предварительно очищается от карбонила железа, сернистых соединений, подогревается до температуры начала реакции и поступает в реактор синтеза метанола. По выходе из зоны катализа из газов выделяется образовавшийся метанол, что достигается охлаждением смеси, которая затем сжимается до давления синтеза и возвращается в процесс.
5.4 Структурная блок-схема
Потоки: 01 - свежий газ; 12 - Смесь газов; 23,34 – смесь продуктов; 31 – циркуляционный газ; 30 – отдувочный газ; 401 – метанол-ректификат; 402 – вода; 403 – эфир. Блоки: 1 – смешение; 2 – синтез; 3 – конденсация и сепарация; 4 – ректификация.
6.Расчет материального баланса ХТС
6.1 Условно-постоянная информация для расчета
Производство метанола основано на реакции:
СО + 2Н2
СН3ОН
Одновременно протекают побочные реакции:
СО + 3Н2 = СН4 + Н2О
2СО + 4Н2 = (СН3)2О + Н2О
6.2 Исходные данные для расчёта. Вариант №4.
6.3 Балансовая математическая модель
1) N01CO+N31ɣ31CO=N12CO
2) N01H2+ N31ɣ31H2= N12H2
3) N12CO(1-X)= N31ɣ31CO+ N30ɣ31CO
4) N12H2=2N12COX(ɣ403(CH3)2O+φCH3OHCO)+ N31ɣ31H2+ N30ɣ31H2+3 N12COXφCH4CO
5) (ПCH3OH ɷCH3OH)/MCH3OH = N12COXφCH3OHCO
6) N30ɣ31CH4 = (( N01H2+ N01CO)/(1- ɣ01СH4)) ɣ01СH4+ N12COXφCH4CO
7) N403 =
N12COXφ(CH3)2OCO
8)G402 = N12COXφCH4CO MH2O +
N12COXφ(CH3)2OCOMH2O – П(1-ɷCH3OH)
6.4 Соответствие переменных потокам
Таким образом, процесс получения метанола является гетерогенно-каталитическим. Лимитирующая стадия – адсорбция водорода на поверхности катализатора.
5.Описание технологической схемы процесса
Рассмотрим два варианта производства метанола
5.1 Процесс при 32МПа:
Технологический процесс получения метанола из оксида углерода и водорода включает ряд операций, обязательных для любой технологической схемы синтеза. Газ предварительно очищается от карбонила железа, сернистых соединений, подогревается до температуры начала реакции и поступает в реактор синтеза метанола. По выходе из зоны катализа из газов выделяется образовавшийся метанол, что достигается охлаждением смеси, которая затем сжимается до давления синтеза и возвращается в процесс.
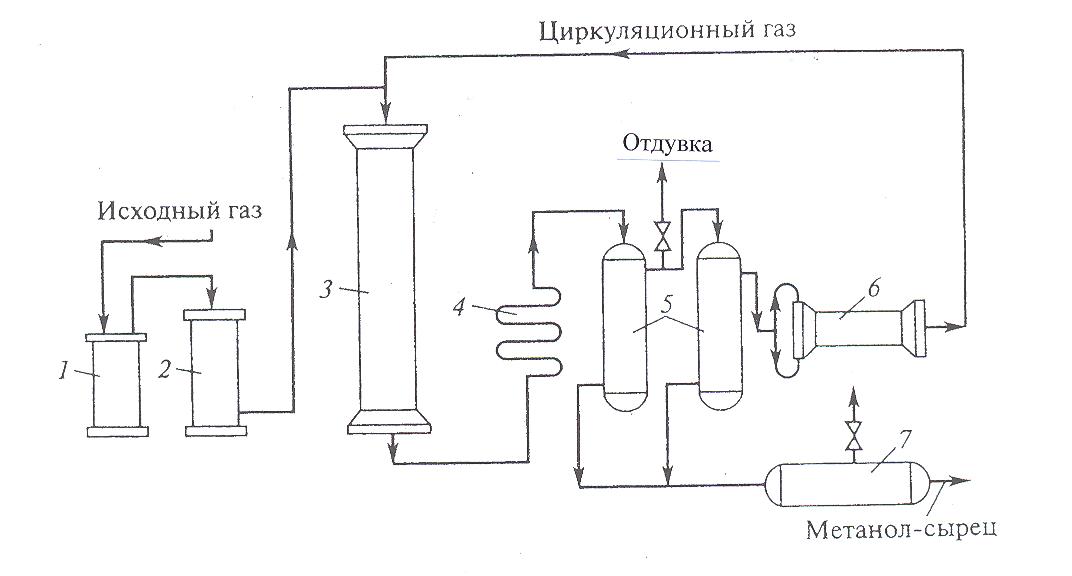
Технологическая схема получения метанола при давлении 32 МПа:
1, 2 – фильтры (масляный и угольный), 3 – колонна синтеза, 4 – холодильник-конденсатор, 5 – сепараторы, 6 – компрессор, 7 – сборник метанола-сырца.
Описание технологической схемы получения метанола при давлении 32 МПа.
Сжатый до 32 МПа синтез-газ очищается в масляном фильтре 1 и в угольном фильтре 2, после чего смешивается с циркуляционным газом и поступает в колонну синтеза 3.
Смещанный газ (на схеме – синтез-газ), пройдя через кольцевой зазор между катализаторной коробкой и корпусом колонны 3 (рис.11) (колонна синтеза метанола высокого давления – рис.13), поступает в межтрубное пространство теплообменника, расположенного в нижней части колонны (рис.13). В теплообменнике 1 (рис.13) газ нагревается до 330-3400 С и по центральной трубе, в которой размещен электроподогреватель 3 (рис.13), поступает в верхнюю часть колонны и проходит последовательно пять слоев катализатора 4 (рис.13).
После каждого слоя катализатора, кроме последнего, в колонну синтеза вводят определенное количество холодного циркуляционного газа (холодный байпас)
2 (рис.13)для поддержания необходимой температуры (проведение процесса синтеза метанола по ЛОТ).
После пятого слоя катализатора контактный газ направляется в теплообменник, где охлаждается до 300-385 0С 130 0С, а затем в холодильник-конденсатор типа «труба в трубе» 4 (рис.11). Здесь газ охлаждается до 30-35 0С и продукты синтеза конденсируются.
Метанол-сырец отделяют в сепараторе 5 и направляют в сборник 7, после чего выводят на ректификацию.
Газ проходит второй сепаратор 5 для выделения капель метанола, компримируется до давления синтеза турбоциркуляционным компрессором 6 и возвращается на синтез. Продувочные газы выводят перед компрессором и вместе с танковыми газами используют в качестве топлива.
6 пункт Колонна синтеза метанола
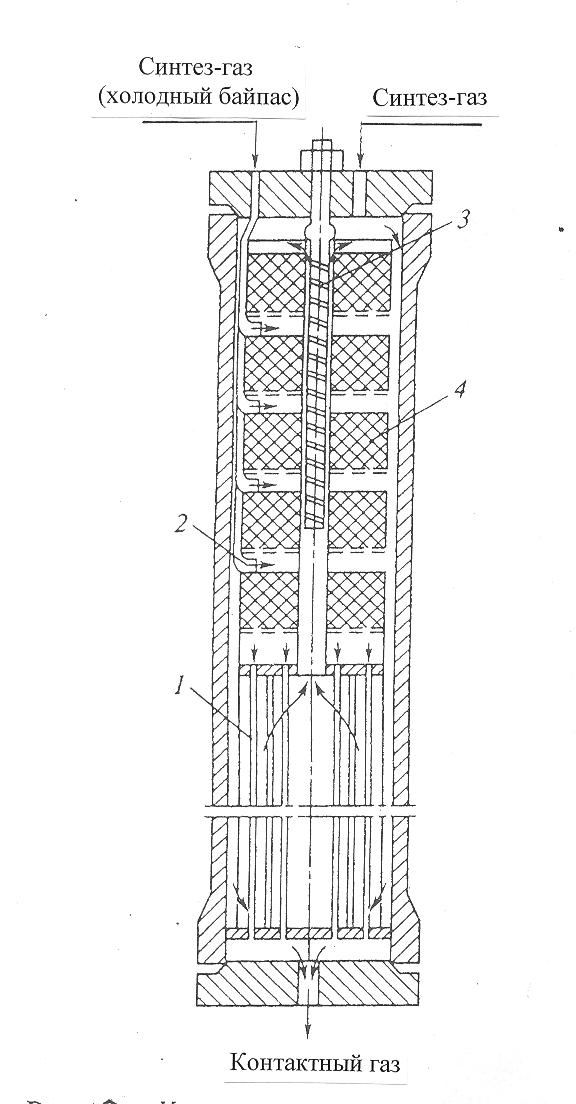
Колонна синтеза метанола при 32 МПа:
1 – теплообменник; 2 – холодный байпас; 3 –электроподогреватель; 4 - катализатор
5.2 Процесс при 5МПа:
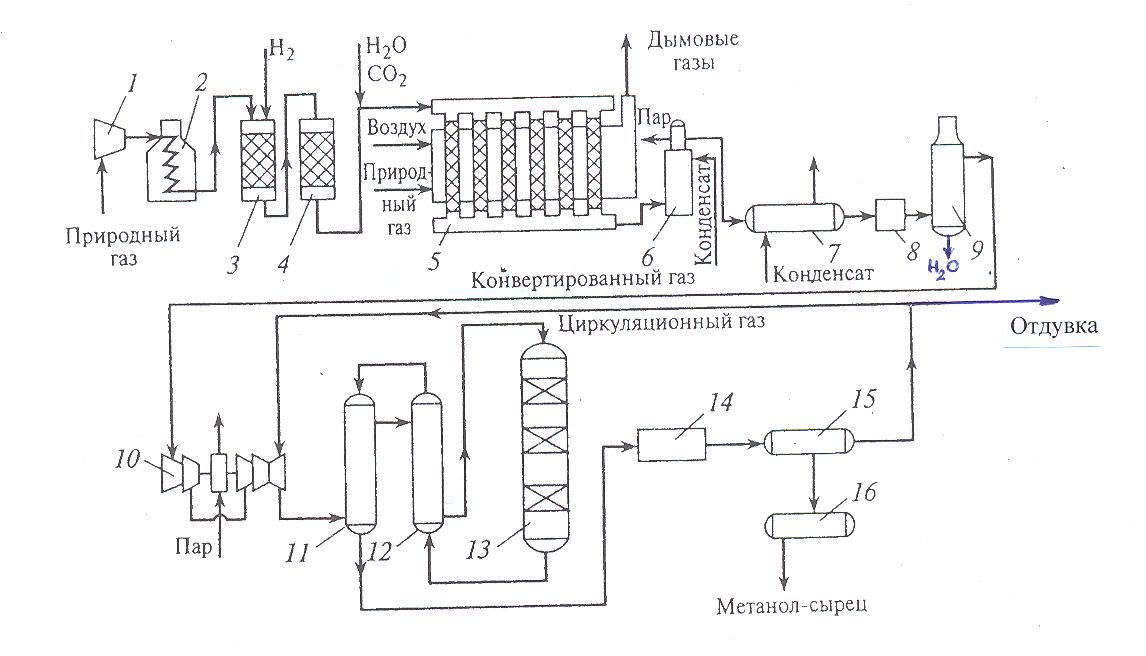
1, 10 –турбокомпрессоры, 2 –подогреватель природного газа, 3 –реактор гидрирования сернистых соединений, 4 –адсорбер, 5 –трубчатый конвектор, 6 –котел-утилизатор, 7, 11, 12 –теплообменники, 8, 14 –холодильники-конденсаторы, 9, 15 –сепараторы, 13 –колонна синтеза, 16 –сборник.
Описание технологической схемы получения метанола при давлении 5МПа
Природный газ сжимается турбокомпрессором 1 до давления 3 МПа, подогревается в подогревателе 2 за счет сжигания в межтрубном пространстве природного газа и направляется на сероочистку в аппараты 3 и 4, где последовательно осуществляется каталитическое гидрирование органических соединений серы на алюмокобальтмолибденовом катализаторе и поглощение образующегося сероводорода адсорбентом на основе оксида цинка. После этого газ смешивается с водяным паром и диоксидом углерода в соотношении СН4 : Н2О : СО2 = 1 : 3,3 : 0,24.
Смесь направляют в трубчатый конвертор 5, где на никелевом катализаторе происходит паро-углекислотная конверсия при температуре 850 - 870 0С.
Теплоту, необходимую для конверсии, получают в результате сжигания природного газа в специальных горелках. Конвертированный газ поступает в котел-утилизатор 6, где охлаждается до 280 - 290 0С. Теплоту выходящего газа используют в теплообменнике
7 для подогрева питательной воды, направляемой в котел-утилизатор. Пройдя воздушный холодильник 8 и сепаратор 9, газ охлаждается до 35-40 0С. Охлажденный конвертированный газ сжимают до 5 МПа в компрессоре 10, смешивают с циркуляционным газом и подают в теплообменники 11, 12, где он нагревается до 220-230 0С.
Нагретая газовая смесь поступает в колонну синтеза 13, температурный режим в которой регулируют с помощью холодных байпасов (проведение процесса синтеза метанола по ЛОТ). Далее газовая смесь охлаждается в холодильнике-конденсаторе 14, сконденсировавшийся метанол-сырец отделяется в сепараторе 15 и поступает в сборник 16. Циркуляционный газ возвращается на синтез, продувочные газы отдают на сжигание в трубчатую печь.
В
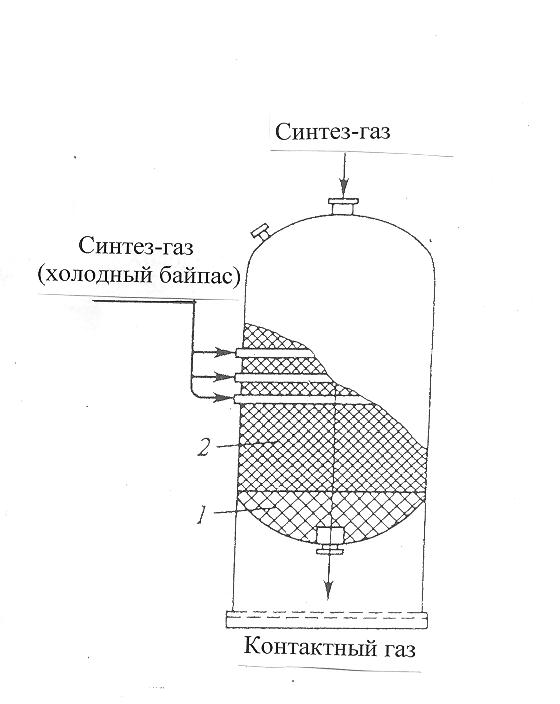
Колонна синтеза метанола при 5 МПа:
1- фарфоровые шары; 2 – катализатор
5.3 Функциональная схема производства метанола
Технологический процесс получения метанола из оксида углерода и водорода включает ряд операций, обязательных для любой технологической схемы синтеза. Газ предварительно очищается от карбонила железа, сернистых соединений, подогревается до температуры начала реакции и поступает в реактор синтеза метанола. По выходе из зоны катализа из газов выделяется образовавшийся метанол, что достигается охлаждением смеси, которая затем сжимается до давления синтеза и возвращается в процесс.
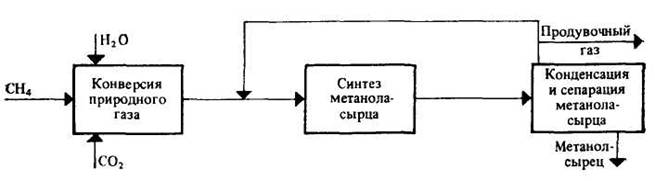
5.4 Структурная блок-схема
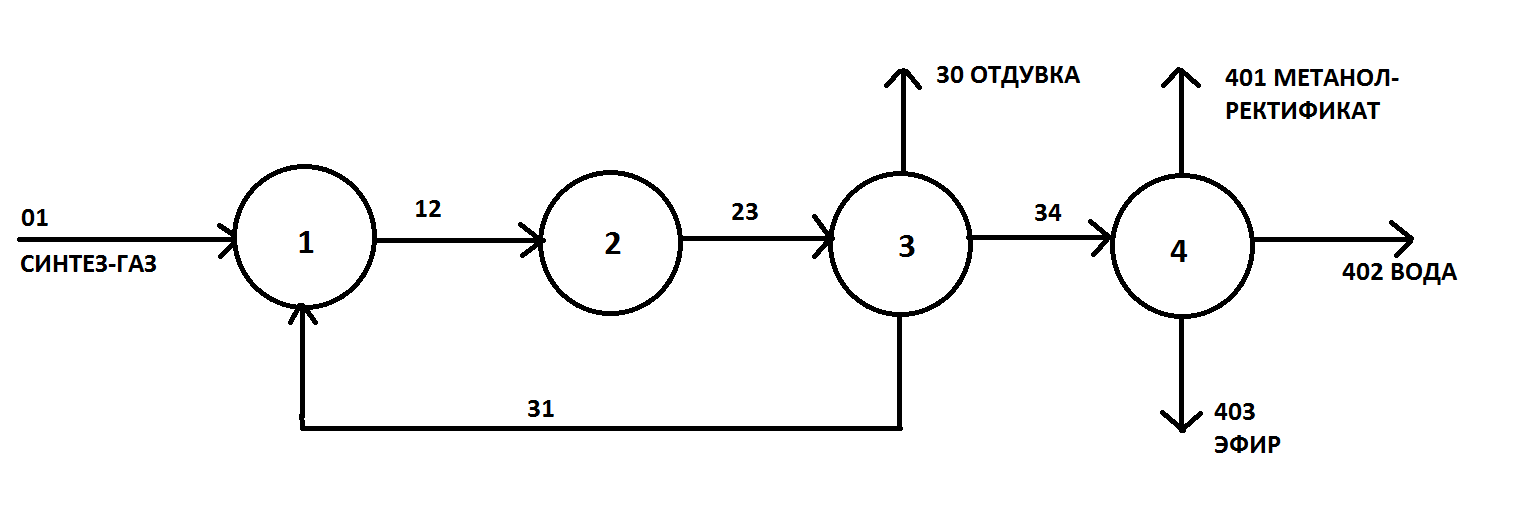
Потоки: 01 - свежий газ; 12 - Смесь газов; 23,34 – смесь продуктов; 31 – циркуляционный газ; 30 – отдувочный газ; 401 – метанол-ректификат; 402 – вода; 403 – эфир. Блоки: 1 – смешение; 2 – синтез; 3 – конденсация и сепарация; 4 – ректификация.
6.Расчет материального баланса ХТС
6.1 Условно-постоянная информация для расчета
Производство метанола основано на реакции:
СО + 2Н2

Одновременно протекают побочные реакции:
СО + 3Н2 = СН4 + Н2О
2СО + 4Н2 = (СН3)2О + Н2О
6.2 Исходные данные для расчёта. Вариант №4.
№ | Содержание информации | Условное обозначение | Единица измерения | Принятое значение | | |||||
1 | Содержание СО в циркуляционном газе | ɣ31CO | Мольные доли | 0,12 | | |||||
2 | Содержание Н2 в циркуляционном газе | ɣ31H2 | Мольные доли | 0.74 | | |||||
3 | Содержание инертных примесей в циркуляционном газе | ɣ31CH4 | Мольные доли | 0,14 | | |||||
4 | Содержание инертных примесей в свежем газе | ɣ01СH4 | Мольные доли | 0,04 | | |||||
5 | Общая конверсия СО | X | Мольные доли | 0.2 | | |||||
6 | Доля СО, превратившегося в СН3OH | φCH3OHCO | Доли | 0,95 | | |||||
7 | Доля СО, превратившегося в (СН3)2О | φ(CH3)2OCO | Доли | 0,03 | | |||||
8 | Доля СО, превратившегося в СН4 | φCH4CO | Доли | 0,02 | ||||||
9 | Базис расчета | П | Кг СН4ОН ректификата | 1500 |
6.3 Балансовая математическая модель
1) N01CO+N31ɣ31CO=N12CO
2) N01H2+ N31ɣ31H2= N12H2
3) N12CO(1-X)= N31ɣ31CO+ N30ɣ31CO
4) N12H2=2N12COX(ɣ403(CH3)2O+φCH3OHCO)+ N31ɣ31H2+ N30ɣ31H2+3 N12COXφCH4CO
5) (ПCH3OH ɷCH3OH)/MCH3OH = N12COXφCH3OHCO
6) N30ɣ31CH4 = (( N01H2+ N01CO)/(1- ɣ01СH4)) ɣ01СH4+ N12COXφCH4CO
7) N403 =

8)G402 = N12COXφCH4CO MH2O +

6.4 Соответствие переменных потокам
Наименование потока | Условное обозначение | Обозначение переменной | Размерность | Значение по расчёту |
Количество СО в исходном газе | N01CO | X1 | кмоль | 57,343 |
Поток циркуляционного газа | N31 | X2 | кмоль | 1567,780 |
Количество СО после смешения | N12CO | X3 | кмоль | 245,477 |
Количество Н2 в исходном газе | N01H2 | X4 | кмоль | 150,036 |
Количество Н2 после смешения | N12H2 | X5 | кмоль | 1310,192 |
Отдувка | N30 | X6 | кмоль | 68,734 |
Количество (СН3)2О на выходе из ректификационной колонны | N403 | X7 | кмоль | 0,736 |
Количество воды на выходе из ректификационной колонны | G402 | X8 | кг | 23,430 |