ВУЗ: Не указан
Категория: Не указан
Дисциплина: Не указана
Добавлен: 29.04.2024
Просмотров: 72
Скачиваний: 2
ВНИМАНИЕ! Если данный файл нарушает Ваши авторские права, то обязательно сообщите нам.
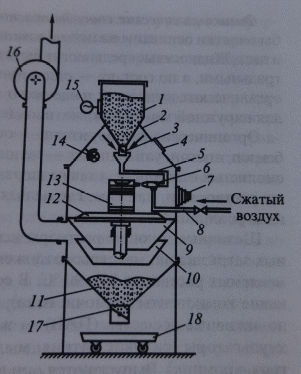
Рис.8 Установка для очистки поршней от нагара.
1-Конусная емкость для опилок деревьев; 2-Рабочая камеры; 3,17-Дисковые заслонки; 4-Смотровое окно; 5,8-гибкие рукава; 6-Инжекторные смесители; 7-Гофрированные рукава; 9,10-Конусные кольца; 11- Конусный бункер; 12- Круглого вращающего стола; 13-Размещение очищаемого объекта (поршня); 14-Электролампы; 15-Электровибратор; 16- Вытяжной вентилятор; 18- Технологическая тележка.
Перед сборкой все детали шатунно-поршневой группы должны быть чистыми и иметь состояние, соответствующее техническим условиям постановки их на двигатель.
Комплектованию этой группы уделяют серьезное внимание, добиваясь уравновешенности вращающихся масс. Масса шатуна выбивается на нижней головке, а масса поршня — на его холодильнике в правом углу.
При сборке длину поршня с шатуном регулируют прокладками между поршнем и вставкой. Линейный размер камеры сжатия у дизеля ПД1М устанавливается в пределах 4,0—5,83 мм. Регулировку этой величины производят за счет съема металла с торца крышки цилиндра.
После сборки и установки комплектов опрессовывают дизель водой давлением 0,3 МПа. Затем производят опрессовку маслом давлением 0,15 МПа, при которой проверяют поступление масла к шатунным подшипникам, к пальцам прицепных шатунов, к верхним головкам шатунов, к гидротолкателям и осям рычагов.
Подбирают комплект поршней, шатунов и пальцев по весу и по размерам:
а) подборку по весу производят в случае замены шатуна или поршня;
б) вес шатуна выбивают на нижней головке, а поршня на его холодильнике в правом углу;
в) разновес поршней на одном дизеле допускают не более 200 граммов, поршней в сборе с шатунами и пальцами не более 450 граммов.
Подгонку по весу поршней производят съёмом металла с нижней торцевой поверхности поршня, при этом высота поршня должна быть не менее 448 мм.
Уменьшение веса шатунов производить за счёт съёма металла со стержня шатуна в углублённых местах.
4. Технология контроля состояния деталей и устранения дефектов
Таблица 4.1 – Карта технических требований на дефектацию детали
| Деталь | ||||||
| ![]() | Поршень дизеля ПД1М | |||||
Номер детали | |||||||
7 | |||||||
Материал | Твердость | ||||||
Алюминиевый сплав ПС-12 (силумина) | HB = 80 – 100 | ||||||
№ позиции на эскизе | Возможные дефекты | Способ восстанов-ления дефекта, инструмент | Размеры, мм | Заключение | |||
Номиналь-ный, мм | Допус- каемый, мм | Брако-вочный, мм | |||||
| Зазор по высоте между кольцом и ручьем: у цилиндрических компрессионных колец у маслосрезывающих колец | Щуп. | 0,18-0,22 0,13-0,17 | 0,18-0,22 0,13-0,17 | более 0,30 более 0,25 | Наплавить и расточить до чертежного размера. | |
| Зазор между поршнем и цилиндровой втулкой: вверху (при измерении диаметра поршня на расстоянии 10 мм от торца) при положении поршня в верхней мертвой точке: внизу (при измерении поршня на расстоянии 10-15 мм от нижнего торца) при положении поршня в нижней мертвой точке: | Щуп, нутрометр. | 3,1-3,3 0,4-0,51 | 3,1-3,3 0,4-0,51 | более 3,4 более 0,85 | Замена цилиндрической втулки или поршня. | |
| Овальность и конусность отверстий под поршневой палец. | Нутромер | 0,0-0,02 | 0,0-0,03 | более 0,08 | Замена поршневого пальца | |
| Натяг при запрессовке заглушек поршневого пальца | Микрометр, нутрометр. | 0,04-0,11 | 0,04-0,11 | 0,04-0,08 | Заглушку по наружному диаметру наплавить газосваркой электродами из силумина ПС-12 и обработать до необходимого размера. | |
| Овальность направляющей частя поршня (при снятом поршневом пальце) | Микрометр | 0,0-0,03 | 0,0-0,03 | более 0,35 | Наплавить, расточить до чертежного размера. Заменить поршневый палец. | |
| Зазор между поршневым пальцем и отверстием поршня | Щуп. | 0,05 | 0,05 | более 0,15 | Заменить палец или подшипник | |
| Натяг поршневого пальца в отверстии поршня | Щуп, микрометр | 0,01 | 0,01 | более 0,02 | Замена поршневого пальца | |
| Высота конусной части канавки по измерительной окружности (первых двух канавок) 0 градации I градации II градации | Щуп. | 4,3+0,03 4,3+0,03 - - | 4,3+0,03 4,3+0,03 4,9+0,03 5,5+0,03 | - - - - | Расточить до чертежного размера. | |
| Высота цилиндрических ручьев поршня для остальных компрессионных колец: 0 градации I градации II градации | Щуп. | 5+0,02 - - | 5+0,02 5,6+0,02 6,2+0,02 | - - - | Расточить до чертежного размера. | |
| Для маслосрезывающих колец: 0 градации I градации II градации | Щуп. | 8+0,02 - - | 8+0,02 8,4+0,02 8,8+0,02 | - - - | Расточить до чертежного размера. | |
| Утопание трапецеидального кольца в ручье относительно поверхности поршня: | Приспособление с индикатором | 0,0-0,23 | 0,0-0,23 | более 1,0 | Замена трапецеидального кольца | |
| Зазор в замке колец: у цилиндрических компрессионных колец у маслосрезывающих колец у трапецеидальных | Щуп. | 1,8-2,2 1,6-1,8 1,8-2,0 | 1,8-2,2 1,6-1,8 1,8-2,0 | более 5,0 более 3,5 более 5,0 | Расточить до чертежного размера. | |
| Зазор в замке колец, находящихся в свободном состоянии: у компрессионных (у всех) у маслосрезывающих | Щуп. | 32-42 32-42 | 32-42 32-42 | менее 25 менее 25 | Расточить до чертежного размера. | |
| Высота кромки у маслосрезыва-ющего кольца | штангенциркуль | 0,5 | 0,5-1,0 | более 1,5 | Восстановить кромку проточкой кольца на станке до чертежных размеров |
Таблица 4.2 – Способы восстановления в зависимости от дефекта
Способы восстановления деталей | ||
с механическими повреждениями | с изношенными поверхностями | с повреждениями ан-тикоррозийного по-крытия |
Замена | шлифовка | гальванические покрытия |
Заключение.
В контрольной работе был рассмотрен вопрос о неисправностях шатунно-поршневой группы дизеля ПД1М, решение устранение неисправности, технологию контроля состояния деталей устранение дефектов шатунно-поршневой группы дизеля ПД-1М.
Список литературы.
-
Кузьмичев Е.Н. Технология производства и ремонта подвижного состава: метод. пособие по выполнению контрольных работ / Е.Н. Кузьмичев., Д.Н. Никитин –– Хабаровск: Изд-во ДВГУПС. – 19 с. -
Кокошинский, И.Г. Справочник по ремонту тепловозов / И.Г. Кокошинский, В.А, Горбатюк, Е.Г. Стеценко. – М.: Транспорт, 1976.– 304 с. -
Рахматуллин М.Д. Технология ремонта тепловозов. – М.: Транспорт, 1983. – 319 с. -
Правила технического обслуживания и текущего ремонта тепловозов ТЭМ1, ТЭМ2, ТЭМ2А. – М.: Транспорт, 1980. – 134 с. -
Руководство по ТО и ТР тепловозов ТЭМ2. – М.:ОАО «РЖД», 2004.- 135 с.