Файл: Введение извлекаемые запасы углеводородного сырья в Казахстане составляют в порядке 30 млрд.rtf
ВУЗ: Не указан
Категория: Не указан
Дисциплина: Не указана
Добавлен: 30.04.2024
Просмотров: 41
Скачиваний: 0
ВНИМАНИЕ! Если данный файл нарушает Ваши авторские права, то обязательно сообщите нам.
Современные процессы перегонки нефти являются комбинированными с процессами обезвоживания и обессоливания, вторичной перегонки и стабилизации бензиновой фракции: ЭЛОУ - AT, ЭЛОУ -АВТ, ЭЛОУ-АВТ-вторичная перегонка и т.д.
Диапазон мощностей отечественных установок перегонки нефти широк - от 0,5 до 8 млн. т нефти в год. До 1950 г. максимальная мощность наиболее распространенных установок AT и АВТ составляла 500-600 тыс.т/год. В 1950-60-х гг. проектировались и строились установки мощностью 1; 1,5; 2 и 3 млн т/год нефти. В 1967 г. ввели в эксплуатацию высокопроизводительную установку АВТ мощностью 6 млн т/год. Преимущества установок большой единичной мощности очевидны: высокая производительность труда и низкие капитальные и эксплуатационные затраты по сравнению с установками малой производительности.
Еще более существенные экономические преимущества достигаются при комбинировании AT и АВТ (или ЭЛОУ - AT и ЭЛОУ -АВТ) с другими технологическими процессами, такими, как газофракционирование, гидроочистка топливных и газойлевых фракций, каталитический риформинг, каталитический крекинг, очистка масляных фракций и т.д.
Надо отметить, что старые установки малой мощности подверглись модернизации с увеличением их мощности в 2 - 2,5 раза и более по сравнению с проектной.
Поскольку в эксплуатации находятся AT и АВТ довоенного и последующих поколений, отечественные установки перегонки нефти характеризуются большим разнообразием схем перегонки, широким ассортиментом получаемых фракций. Даже при одинаковой производительности ректификационные колонны имеют разные размеры, неодинаковое число и разные типы тарелок; по-разному решены схемы теплообмена, холодного, горячего и циркуляционного орошения, а также вакуумсоздающей системы. В этой связи ниже будут представлены лишь принципиальные технологические схемы отдельных блоков (секций), входящих в состав высокопроизводительных современных типовых установок перегонки нефти.
Первоначально на АНПЗ установка АТ была запроектирована фирмой «Баджер» (США) и пущена в эксплуатацию в ноябре 1945 г., как комбинированная с блоком термического крекинга.
В 1970 году в целях улучшения подготовки переработываемых нефтей и ловушечного продукта, дополнительно к имеющейся мощности по обессоливанию «Петрико» введен в эксплуатацию блок ЭЛОУ-10/6. Проектирование этого объекта было выполнено институтом КазНИИнефть. Новые мощности по электрообес-соливанию в двух сферических электродегидраторах Э-1 и Э-2, объемом по 600 м
3 каждый, способствовали улучшению качества подготовки нефти, а также увеличению производительности на блоке прямой гонки.
В 1986 г. были смонтированы и пущены в эксплуатацию для дополнительного обессоливания два горизонтальных электродегидратора типа 2ЭГ-160.
В 1986 г. из-за большого физического и морального износа, в основном насосно-печного оборудования, блок термического крекинга был выведен из эксплуатации.
В 2005 г. была произведена реконструкция установки для приема в переработку лёгкой Тенгизкой нефти наряду с Мангышлакской и Мартышинской нефтью. После проведённой реконструкции установка рассчитана на переработку от 1,8 – 2,0 млн. тонн сырой нефти в год.
Секция АТ - предназначена для разделения обессоленной и обезвоженной нефти на отдельные фракции, путем ее нагревания, испарения, фракционирования и конденсации паров дистиллятов.
На установке АТ-2 получают из обессоленной нефти следующую продукцию:
компонент автобензина (фр. НК-205оС);
сырье для установки каталитического риформинга (фр. НК-180оС);
компонент дизельного топлива (фр. 180-360оС);
мазут (фр. выше 360оС);
углеводородный газ (С1 - С4).
Производственные технологические схемы газореагентного хозяйства (ГРХ) базируются в основном на оборудовании, выведенных из эксплуатации газофракционирующей установки и установки сернокислотного алкилирования.
Блок газореагентного хозяйства предназначен для следующих целей:
- сбор, компаундирование и упорядоченная раздача топливных газов на
ЭЛОУ АТ- 2 и ТЭЦ завода;
- слив, хранение, приготовление растворов едкого натра необходимых
концентраций и раздача приготовленных растворов на технологические
установки завода.
В производственный объект входят:
- блок распределения топливных газов (проект фирмы «Баджер», США, 1945г.);
- блок слива, хранения и раздачи натра едкого на технологические установки завода (проект фирмы «Баджер», США, 1945г).
Для обеспечения высокоэффективных показателей работы установок по переработке нефти на них необходимо подавать нефть с содержанием солей не более 4 мг/л и воды 0,1 %. Поэтому получаемую с промыслов нефть подвергают доочистке на нефтеперерабатывающих заводах. Необходимость такой тщательной подготовки нефти к переработке диктуется следующими обстоятельствами. Наличие в нефти воды приводит к резкому снижению производительности установок, повышенному расходу энергии для её испарения и конденсации. При этом ухудшается четкость ректификации. Наличие солей и механических примесей вызывает эррозию и засорение труб печей и теплообменников, понижает коэффициент теплопередачи и повышает зольность мазутов и гудронов. Кроме того, наличие в нефти растворённых солей вызывает коррозию аппаратуры и оборудования из-за образования соляной кислоты, которая выделяется в свободном состоянии при гидролизе некоторых хлористых солей, особенно хлористого магния:
MgCl2 + H2O = MgOHCl + HCl
Коррозия бензиновых конденсаторов и холодильников усиливается при переработке сернистых солей, особенно в присутствии водяных паров. Вначале в присутствии влаги образуется сернистое железо в виде защитной плёнки:
Fe + H2 S = FeS + H2 ,
а затем, в присутствии соляной кислоты оно превращается в хлорное железо:
FeS + 2HCl = FeCl2 + H2 S,
которое растворяется в воде, оголяя слой железа, вступает в реакцию с сероводородом и т.д.
1.2 Описание технологической схемы установки
Подготовленная обессоленная и обезвоженная нефть с ЭЛОУ-10/6 направляется через теплообменники подогрева нефти Т-21, Т-22, Т-23, Т-24, где нагревается за счёт тепла потока КГФ, далее проходит через теплообменники Т-25, Т-26, Т-41, Т-42 где нагревается за счёт тепла мазута.
Подогретая до температуры 130-165оС обессоленная и обезвоженная нефть на входе на установку разделяется на три потока:
- I поток нефти проходит через теплообменники Т-13, Т-14, Т-15, (где нагревается за счёт тепла I циркуляционного орошения ЦО, при переработке тяжёлых нефтей), далее проходит через теплообменник Т-16, где нагревается за счёт тепла мазута;
- II поток нефти проходит через теплообменники Т-27/1, Т-27/2, Т-28/1, Т-28/2, где нагревается за счёт тепла II-ЦО, и теплообменники Т-29, Т-30, где нагревается за счёт тепла мазута. На II потоке существует схема подогрева нефти в теплообменнике Т-30 за счёт тепла II-ЦО. Данная схема используется при переработке нефти Тенгизского месторождения.
- III поток нефти проходит через теплообменники Т-31, Т-32, Т-33, Т-34, Т-35, Т-37, где нагревается за счёт тепла мазута.
Температура подогрева нефти контролируется на щите в операторной поз.41-ТIО-114, 115,116. Расход нефти по потокам контролируется приборами поз.41-FI- 430, 431, 432.
Также имеется возможность подачи 2-3% щелочного раствора на вход теплообменника Т-21 от ДН-6, ДН-7, (для снижения рН дренажной воды в К-1). Подогретая до температуры 160-220оС нефть, (в зависимости от перерабатываемой нефти) объединяется и одним потоком поступает на 22-ю тарелку эвапоратора К-1. Эвапоратор К-1 оборудован 29-ю тарелками колпачкового типа.
В эвапораторе К-1 из нефти выделяется газ и часть бензина. В линию острого орошения К-1 для снижения коррозии шлёмовой линии и верха К-1 подаётся ингибитор коррозии «Додиген-481».
Пары бензина и газ по шлёмовой линии поступают в холодильники-конденсаторы воздушного охлаждения ХВО-6, ХВО-7, ХВО-10, далее в доохладители Х-3, Х-4, где охлаждаются до температуры ниже 40-45оС (поз.41-ТIO-230) и поступают в газоводосепаратор Е-1, где происходит разделение на газ, бензин и воду.
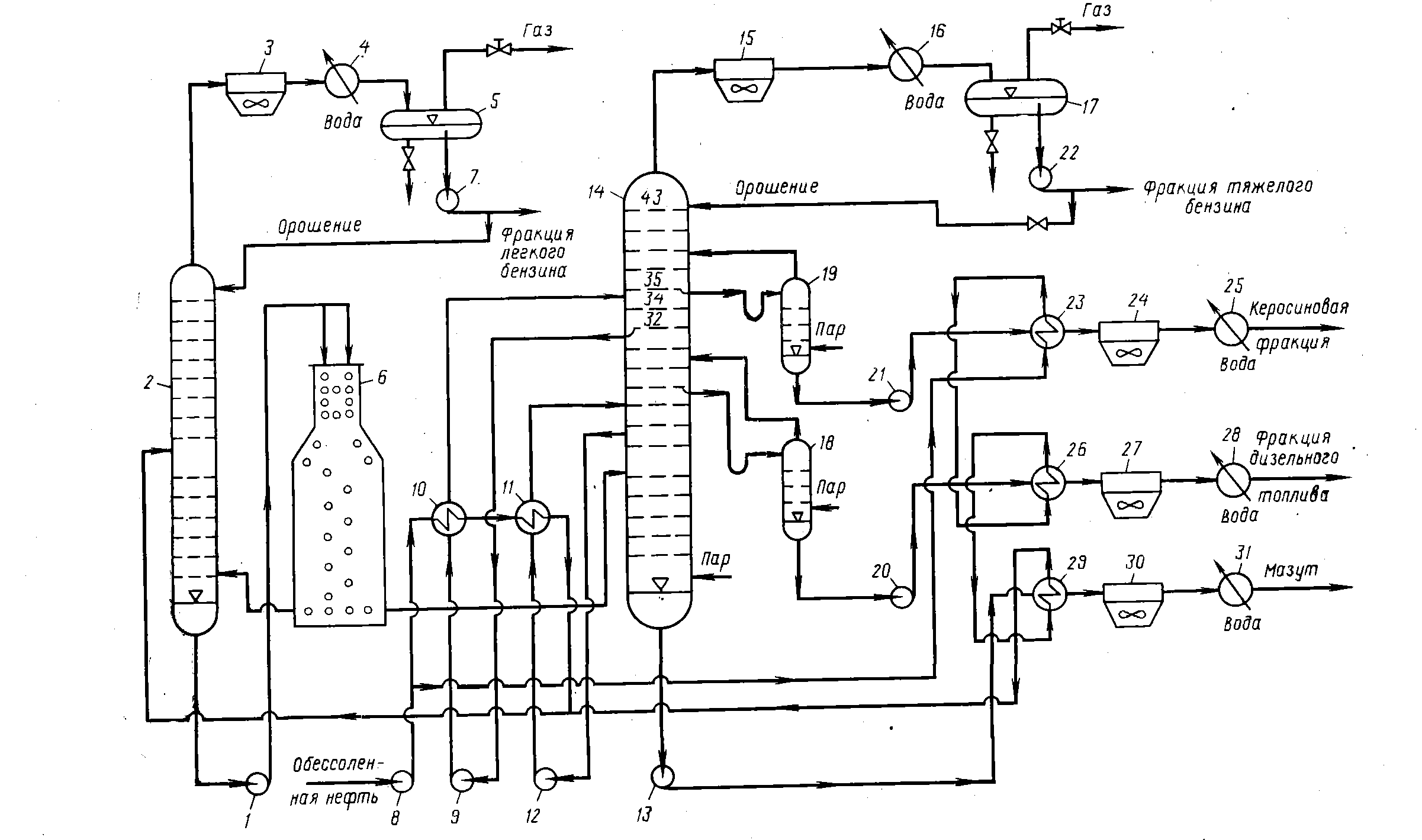
Рисунок 1. Технологическая схема атмосферной перегонки нефти
конденсатор холодильник перегонка нефть
Газ через клапан регулятор давления поз. 41-РIC-231 направляется в газоотделитель А-5, где происходит конденсация лёгких фракций бензина за счёт падения давления. Далее газ проходит через теплообменник Т-38, где подогревается до температуры 65-75
оС за счёт тепла отходящего пара с обогрева приборов КИПиА печи П-1 и направляется на печи П-1 и П-2 как топливный газ.
Конденсат лёгких фракций бензина по мере накопления в газоотделителе А-5 откачивается поршневыми насосами Р1-1 и Р1-1а в линию бензинов с установки.
Уровень конденсата в А-5 контролируется прибором поз.41-LI- 628, выведенный на дисплей монитора в операторную АТ. Отстоенная в газоводосепараторе Е-1 вода через клапан регулятор уровня поз. 1 на первоначальной стадии пуска сбрасывается в канализацию, но после введения в эксплуатацию секции очистки сернистых вод (установка производства серы), вода с Е-1, через клапан регулятор 41-LY-907 направляется в Е-102, откуда забирается насосами Н-102а, и Н-102в и перекачивается на установку очистки сернистых вод.
Сконденсированная бензиновая фракция из Е-1 насосами Н-28, Н-28а подаётся на острое орошение колонны К-1 для регулирования температурного режима верха колонны. Избыток бензина через клапан регулятор уровня Е-1 поз. 41-LIC-627 откачивается с установки.
Параметры работы эвапоратора К-1 контролируются следующими приборами:
-
давление верха – поз.41-PI- 245; -
давление низа – поз.41-PI- 246; -
уровень низа – поз. 41-LIC- 611;
поз. 41-LI- 611А (шаровый уровень)
-
температура низа – поз.41-TI- 3605; -
температура верха – поз. 41-TIC-27, клапан которого находится на линии острого орошения К-1.
Полуотбензиненная нефть с низа колонны К-1 насосами Н-9, Н-10 прокачивается через теплообменники Т-39 и Т-40, где нефть нагревается за счёт 2-го Ц.О. и мазута соответственно, а далее прокачивается через печи подогрева нефти П-1, П-2. Давление на линии нагнетания насосов Н-9, Н-10 контролируется на дисплее монитора в операторной приборами поз.41-PIC- 257, 258.
В четырёхпоточных шестипролётных вертикальных печах П-1, П-2, оборудованных 18-ю форсунками марки ГДК-2,5 каждая, нефть проходит 4-мя потоками конвекционную зону, затем каждый поток проходит боковой экран, потолочный (радиантная зона) и поступает в трансферную линию.
Расходы потоков регулируются на дисплее монитора в операторной:
-
печь П-1 – поз. 41-FIC- 53а, 54а, 55а, 56а; -
печь П-2 – поз. 41-FIC- 437б, 438б, 439б, 440б,
Температура нефти контролируется на выходе из печи П-1 поз.41-TI- 1101, 1102, 1103, 1104 и из печи П-2 поз.41-TI- 4509, 4510, 4511, 4512 по потокам, регулируется температура нефти на выходе из П-1 поз.41-TIC- 15а, из П-2 поз.41-TIC- 44.
Нагретая до температуры 360-385оС нефть в парожидкостной фазе поступает в ректификационную колонну К-2 на 6-ю тарелку.