ВУЗ: Не указан
Категория: Не указан
Дисциплина: Не указана
Добавлен: 05.05.2024
Просмотров: 43
Скачиваний: 0
ВНИМАНИЕ! Если данный файл нарушает Ваши авторские права, то обязательно сообщите нам.
2 и расход 1000 л/мин.
Инжекторы (струйные насосы, работающие на принципе разряжения) установленные на линиях смазки, обеспечивают увеличение количества масла для системы смазки до вступления в работу главного масляного насоса.
Для предотвращения прорыва горячего воздуха в масляную полость установлены угольные уплотнения. Уплотнение состоит из корпуса, в котором имеются угольные кольца из двух половин, прижимаемые пружинами к гребням втулки, насаженные на вал турбонасоса. Гребни врезаются в угольные кольца, обеспечивая минимальный радиальный зазор. Уплотнения установлены в расточку корпуса и прижаты захватами. В полость между угольниками и масляными уплотнениями подается охлаждающий воздух. Суммарные проточки охлаждающего и горячего воздуха отводятся вестовой трубой. Система уплотнения ЦН начинается за насосами уплотнения и работает при наличии регулятора перепада масло-газ. Давление в линии выше давления газа на 1,5-2 кг/см2.
Указатель уровня служит для контроля за уровнем масла в баке. Указатель устанавливается в отсеке чистого масла. Поплавок со штоком опускается в масла.. Падение уровня масла опасно, т.к. срывается подача масла в насос и, соответственно к узлам агрегата. Переполнение масла также не допустимо.
Система смазки и уплотнения нагнетателя
Уплотнение на покрышке колеса служит для уменьшения потерь энергии ротора, затрачиваемой на перекачку газа. Цель установки уплотнений - предотвратить утечку газа. Уплотнение по валу торцевого типа состоит из стального кольца на роторе и баббитографитового кольца в корпусе, которые приклеиваются эпоксидной смолой ко втулке корпуса. На втулку постоянно действует пружина, поджимая баббитографитовое кольцо. В камеру до уплотнения подведено масло высокого давления (давление больше давления газа на 1,5-2 атм). Масло непрерывно поступает в зазор между стальным и баббитографитовым кольцом, уплотняя вал и непрерывно уходит на регенерацию.
Опорный подшипник смазывается маслом высокого давления, которое не только смазывает, но и уплотняет вал. К опорно-упорному подшипнику масло подводится с давлением не ниже 3 атм из средней линии или системы смазки.
Правила эксплуатации системы
маслоснабжения
При эксплуатации системы маслоснабжения должны соблюдаться следующие правила:
1. Монтаж маслосистемы осуществляется по чертежам проектных организаций в соответствии со схемой маслоснабжения ГПА, с установочными чертежами и инструкциями завода-изготовителя.
После окончания монтажных работ должна быть произведена очистка и промывка напорных и сливных маслопроводов и маслобака. Маслосистема должна быть заполнена маслом через фильтрующие сетки.
2. При пуско-наладочных работах производится прокачка масла по маслосистеме, регулируется расход масла по подшипникам ГПА путем подбора дроссельных шайб, маслосистема проверяется на плотность фланцевых соединений и арматуры. При обнаружении механических примесей масло должно быть слито, промыты фильтры, трубопроводы, маслобак, подшипники, после чего маслосистема заполняется вновь.
3. В процессе эксплуатации ГПА должны контролироваться и регистрироваться температура и давление масла на входе в подшипники ГПА и температура подшипников. Уровень в баках и давление масла должны быть в установленных пределах. Уровень контролируется автоматически с соответствующей сигнализацией.
4. Температурный режим в системе охлаждения масла должен поддерживаться в пределах, оговоренных инструкцией завода-изготовителя и обеспечивать температуру подшипников ГПА не выше максимально возможных величин.
5. Масло, находящееся в системе смазки, должно заменяться свежим в установленные сроки. Независимо от сроков, указанных в инструкции завода-изготовителя, масло должно быть заменено свежим при обнаружении любого из следующих признаков:
- содержание механических примесей свыше 1,5 %;
- содержание воды в масле свыше 0,25 %;
- кислотность увеличилась свыше 1,5 КОН на 1г масла;
- температура вспышки по Бренкену снизилась до 150 0С;
- содержание кокса по Кондратову свыше 3 %.
Для каждого типа ГПА должна быть установлена периодичность отбора проб и проверки качества масла. Пробы должны отбираться в соответствии с действующим стандартом.
6. Во избежание повышенного износа ГПА не разрешается применять масла марок, не соответствующих рекомендованным заводом-изготовителем.
8. Элементы системы смазки (трубопроводы, фильтры, маслоохладители, маслобак и др.) должны подвергаться периодической очистке.
9. Для каждого типа ГПА на основе заводских эксплуатационных данных устанавливаются нормы расхода масла.
10. В КЦ должна быть вывешена утвержденная схема маслосистемы КС. На схеме должны быть указаны маслопроводы, емкости, фильтры, насосы, арматура и т.п., а также допустимые максимальные и минимальные давления и температуры масла.
Расчет потребности масла на заполнение маслосистем и пуско-наладку вновь вводимых или заменяемых ГПА
Потребность масла по маркам на заполнение маслосистем вновь вводимых или заменяемых ГПА для предприятия определяется числом агрегатов и вместимостью маслосистем
где Vi- вместимость маслосистемы ГПА i-го типа;
niВ- число вновь вводимых ГПА i-го типа на планируемый период.
Безвозвратный расход масла при пусконаладочных работах не должен превышать 20% вместимости ГПА i-го типа
Суммарная потребность масла на пуско-наладку и заполнение маслосистемы ГПА i-го типа составит
Проверочный расчет маслосистемы
Проверочный расчет маслосистемы заключается в гидравлическом расчете различных участков маслосистемы с целью проверки их работоспособности.
Маслосистема КЦ-6 имеет два основных участка:
- маслопровод между маслобаком ГСМ и мерной емкостью;
- коллектор распределения масла из мерной емкости по маслобакам ГТУ.
Гидравлический расчет маслопровода
Начальные данные: длина L=177м, труба 89х4, шероховатость стенки трубы К=0,5 мм, разность геодезических отметок конца и начала маслопровода z=5.6м, марка насоса Ш8-25-5.8/2.5Б, развиваемое насосом давление Р=2,5 кг/см2 при подаче Q=5,8 м3/ч, плотность масла 20=900кг/м3, вязкости масла при t=500C 50=21.3 мм2/с, при t=200C 20=100мм2/с, местные сопротивления на маслопроводе: задвижек-2, поворотов на 900 -3, тройников на 900 -1, величина остаточного напора Ност=4м.
,
где U- показатель крутизны вискограммы, 1/ 0С,
,
1 и 2- кинематический коэффициент вязкости, мм2/с, при любой известной температуре t1 и t2,0С.
(1/ 0С),
(мм2/с).
Пересчитаем также плотность масла:
(кг/м3),
где р- коэффициент объемного расширения.
2.Определяем сумму коэффициентов местных сопротивлений m по длине маслопровода. Величина коэффициентов местных сопротивлений для различных их видов:
Задвижка 0,15
Поворот на 900 1,32
Тройник 0,32
Величина суммы коэффициентов местных сопротивлений составит:
= 4,43.
3. Переведем давление, развиваемое насосом, в напор, для более наглядного представления результатов расчета:
м.
Результаты расчета программы:
Исходные данные:
число участков N=1
длина участка, м L=177
внутренний диаметр, м D=0,081
сумма коэффициентов
местных сопротивлений SM=4.43
расчетная вязкость, мм2/с =216,7
шероховатость стенки трубы, мм К=0,5
разность геодезических отметок, м Z=3,6
остаточный напор, м Ност=4
Результаты гидравлического расчета:
Q, м3/ч Н, м
4,5 13,7
5,1 14,2
5,5 14,8
6,0 15,3
6,5 15,8
Как видно из результатов гидравлического расчета, давления, развиваемого насосом, хватает для перекачки масла до мерной емкости и, следовательно, маслопровод работоспособен.
Гидравлический расчет коллектора
Исходные данные: количество участков-2;
характеристика первого участка: длина L=88м; труба 89х4; разность геодезических отметок конца и начала участка z=-1,5м; местные сопротивления на участке: задвижек-2, поворотов на 90
0-1, тройников-5, фильтр-1;
характеристика второго участка: длина L=1,5м; труба 57х4; разность геодезических отметок конца и начала участка z=0,5м; местные сопротивления на участке: задвижек-2, поворотов на 900-1, тройник-1; шероховатость стенки трубы К=0,5мм; плотность масла 20=900 кг/м3; вязкость масла при температурах t1=500C и t2=200C cоответственно 50=21,3 мм2/с и 20=100мм2/с; величина остаточного напора Ност=0,2м.
За длину первого участка принято расстояние до самого дальнего от мерной емкости ГПА как наиболее неблагоприятный случай для расчета
m
Задвижка 0,15
Поворот на 900 1,32
Тройник 0,32
Фильтр 2,2
Для первого участка:
m=2*0,15+1,32+0,32*5+2,2=6,63
Для второго участка:
m=2*0,15+1,32+0,32=1,94
Результаты расчета:
Исходные данные:
число участков N=2
1 участок
длина, м L=88
внутренний диаметр, м D=0,081
сумма коэффициентов местных сопротивлений SM=6,63
2 участок
длина, м L=1,5
внутренний диаметр, м D=0,041
сумма коэффициентов местных сопротивлений SM=1,94
расчетная вязкость, мм2/с =216,7
шероховатость стенки трубы, мм К=0,1
разность геодезических отметок, м Z=-1,5
остаточный напор, м Ност=0,3
Результаты гидравлического расчета:
Q, м3/ч Н, м
1,5 -0,6
2,0 -0,2
2,5 0,1
3,0 0,4
3,5 0,8
4,0 1,1
4. Построим характеристику самоточечного коллектора:
Как видно из характеристики, работа коллектора в самоточечном режиме возможна до тех пор, пока расход не достигнет значения Q=2,3 куб.м/ч (в этом случае потери напора в трубопроводе сравняются с гидростатическим напором масла в мерной емкости). Так как объем маслобака ГТУ V=2м3, то можно вычислить минимальное время его наполнения:
Литература
Инжекторы (струйные насосы, работающие на принципе разряжения) установленные на линиях смазки, обеспечивают увеличение количества масла для системы смазки до вступления в работу главного масляного насоса.
Для предотвращения прорыва горячего воздуха в масляную полость установлены угольные уплотнения. Уплотнение состоит из корпуса, в котором имеются угольные кольца из двух половин, прижимаемые пружинами к гребням втулки, насаженные на вал турбонасоса. Гребни врезаются в угольные кольца, обеспечивая минимальный радиальный зазор. Уплотнения установлены в расточку корпуса и прижаты захватами. В полость между угольниками и масляными уплотнениями подается охлаждающий воздух. Суммарные проточки охлаждающего и горячего воздуха отводятся вестовой трубой. Система уплотнения ЦН начинается за насосами уплотнения и работает при наличии регулятора перепада масло-газ. Давление в линии выше давления газа на 1,5-2 кг/см2.
Указатель уровня служит для контроля за уровнем масла в баке. Указатель устанавливается в отсеке чистого масла. Поплавок со штоком опускается в масла.. Падение уровня масла опасно, т.к. срывается подача масла в насос и, соответственно к узлам агрегата. Переполнение масла также не допустимо.
Система смазки и уплотнения нагнетателя
Уплотнение на покрышке колеса служит для уменьшения потерь энергии ротора, затрачиваемой на перекачку газа. Цель установки уплотнений - предотвратить утечку газа. Уплотнение по валу торцевого типа состоит из стального кольца на роторе и баббитографитового кольца в корпусе, которые приклеиваются эпоксидной смолой ко втулке корпуса. На втулку постоянно действует пружина, поджимая баббитографитовое кольцо. В камеру до уплотнения подведено масло высокого давления (давление больше давления газа на 1,5-2 атм). Масло непрерывно поступает в зазор между стальным и баббитографитовым кольцом, уплотняя вал и непрерывно уходит на регенерацию.
Опорный подшипник смазывается маслом высокого давления, которое не только смазывает, но и уплотняет вал. К опорно-упорному подшипнику масло подводится с давлением не ниже 3 атм из средней линии или системы смазки.
Правила эксплуатации системы
маслоснабжения
При эксплуатации системы маслоснабжения должны соблюдаться следующие правила:
1. Монтаж маслосистемы осуществляется по чертежам проектных организаций в соответствии со схемой маслоснабжения ГПА, с установочными чертежами и инструкциями завода-изготовителя.
После окончания монтажных работ должна быть произведена очистка и промывка напорных и сливных маслопроводов и маслобака. Маслосистема должна быть заполнена маслом через фильтрующие сетки.
2. При пуско-наладочных работах производится прокачка масла по маслосистеме, регулируется расход масла по подшипникам ГПА путем подбора дроссельных шайб, маслосистема проверяется на плотность фланцевых соединений и арматуры. При обнаружении механических примесей масло должно быть слито, промыты фильтры, трубопроводы, маслобак, подшипники, после чего маслосистема заполняется вновь.
3. В процессе эксплуатации ГПА должны контролироваться и регистрироваться температура и давление масла на входе в подшипники ГПА и температура подшипников. Уровень в баках и давление масла должны быть в установленных пределах. Уровень контролируется автоматически с соответствующей сигнализацией.
4. Температурный режим в системе охлаждения масла должен поддерживаться в пределах, оговоренных инструкцией завода-изготовителя и обеспечивать температуру подшипников ГПА не выше максимально возможных величин.
5. Масло, находящееся в системе смазки, должно заменяться свежим в установленные сроки. Независимо от сроков, указанных в инструкции завода-изготовителя, масло должно быть заменено свежим при обнаружении любого из следующих признаков:
- содержание механических примесей свыше 1,5 %;
- содержание воды в масле свыше 0,25 %;
- кислотность увеличилась свыше 1,5 КОН на 1г масла;
- температура вспышки по Бренкену снизилась до 150 0С;
- содержание кокса по Кондратову свыше 3 %.
Для каждого типа ГПА должна быть установлена периодичность отбора проб и проверки качества масла. Пробы должны отбираться в соответствии с действующим стандартом.
6. Во избежание повышенного износа ГПА не разрешается применять масла марок, не соответствующих рекомендованным заводом-изготовителем.
-
Масло от поставщика принимается при наличии паспорта на него.
8. Элементы системы смазки (трубопроводы, фильтры, маслоохладители, маслобак и др.) должны подвергаться периодической очистке.
9. Для каждого типа ГПА на основе заводских эксплуатационных данных устанавливаются нормы расхода масла.
10. В КЦ должна быть вывешена утвержденная схема маслосистемы КС. На схеме должны быть указаны маслопроводы, емкости, фильтры, насосы, арматура и т.п., а также допустимые максимальные и минимальные давления и температуры масла.
Расчет потребности масла на заполнение маслосистем и пуско-наладку вновь вводимых или заменяемых ГПА
Потребность масла по маркам на заполнение маслосистем вновь вводимых или заменяемых ГПА для предприятия определяется числом агрегатов и вместимостью маслосистем
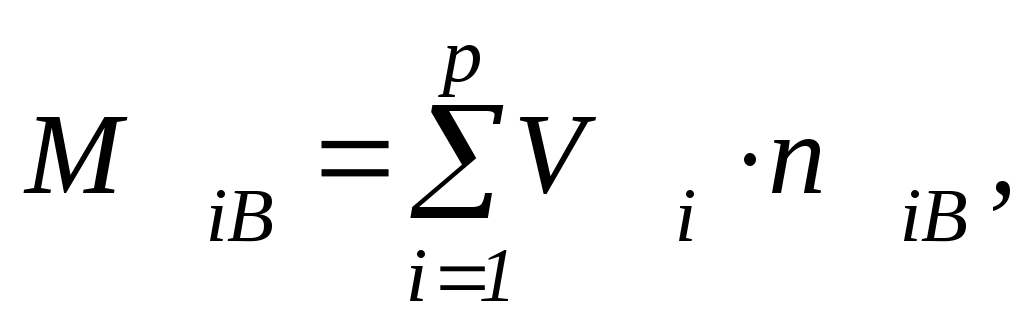
где Vi- вместимость маслосистемы ГПА i-го типа;
niВ- число вновь вводимых ГПА i-го типа на планируемый период.
Безвозвратный расход масла при пусконаладочных работах не должен превышать 20% вместимости ГПА i-го типа
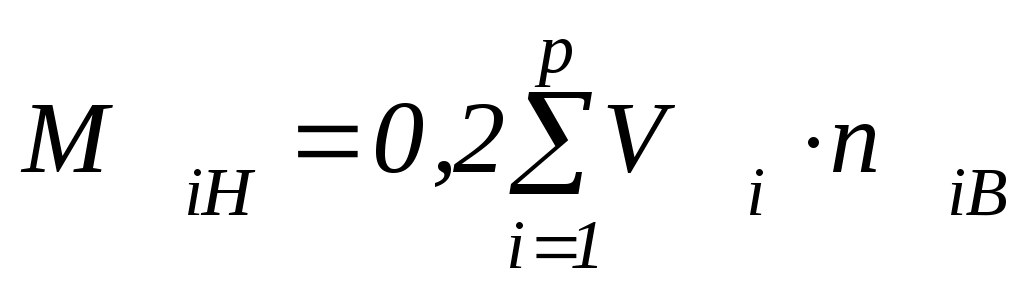
Суммарная потребность масла на пуско-наладку и заполнение маслосистемы ГПА i-го типа составит
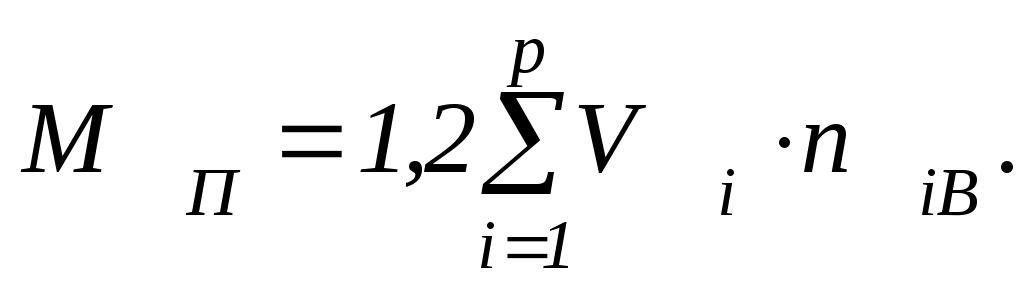
Проверочный расчет маслосистемы
Проверочный расчет маслосистемы заключается в гидравлическом расчете различных участков маслосистемы с целью проверки их работоспособности.
Маслосистема КЦ-6 имеет два основных участка:
- маслопровод между маслобаком ГСМ и мерной емкостью;
- коллектор распределения масла из мерной емкости по маслобакам ГТУ.
Гидравлический расчет маслопровода
Начальные данные: длина L=177м, труба 89х4, шероховатость стенки трубы К=0,5 мм, разность геодезических отметок конца и начала маслопровода z=5.6м, марка насоса Ш8-25-5.8/2.5Б, развиваемое насосом давление Р=2,5 кг/см2 при подаче Q=5,8 м3/ч, плотность масла 20=900кг/м3, вязкости масла при t=500C 50=21.3 мм2/с, при t=200C 20=100мм2/с, местные сопротивления на маслопроводе: задвижек-2, поворотов на 900 -3, тройников на 900 -1, величина остаточного напора Ност=4м.
-
Принимаем температуру масла tм=50С (как наихудший случай) и пересчитываем вязкость масла по формуле Рейнольдса-Филонова:
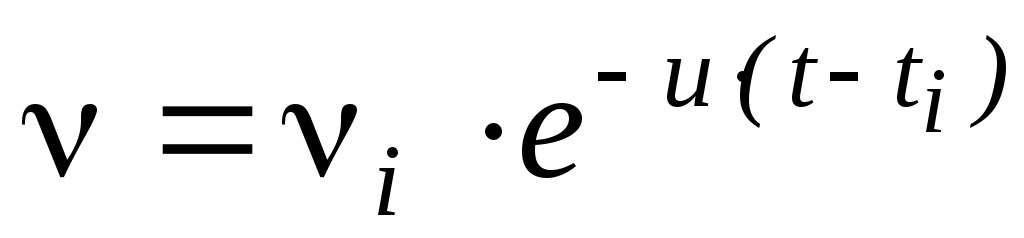
где U- показатель крутизны вискограммы, 1/ 0С,
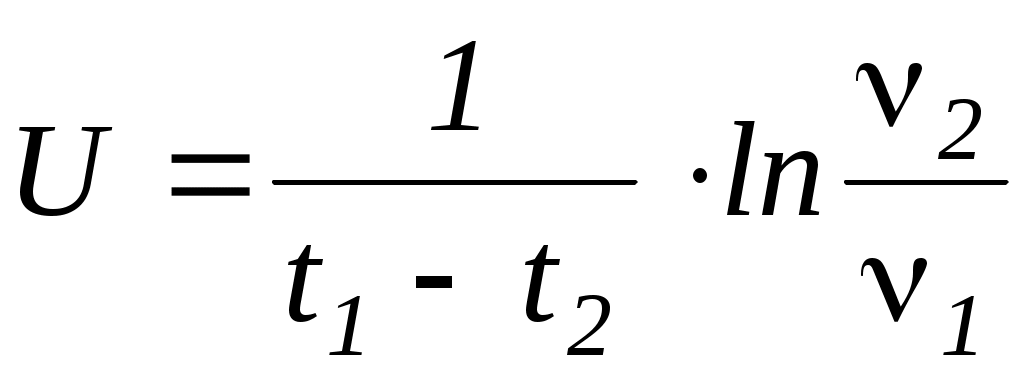
1 и 2- кинематический коэффициент вязкости, мм2/с, при любой известной температуре t1 и t2,0С.


Пересчитаем также плотность масла:

где р- коэффициент объемного расширения.
2.Определяем сумму коэффициентов местных сопротивлений m по длине маслопровода. Величина коэффициентов местных сопротивлений для различных их видов:
Задвижка 0,15
Поворот на 900 1,32
Тройник 0,32
Величина суммы коэффициентов местных сопротивлений составит:

3. Переведем давление, развиваемое насосом, в напор, для более наглядного представления результатов расчета:
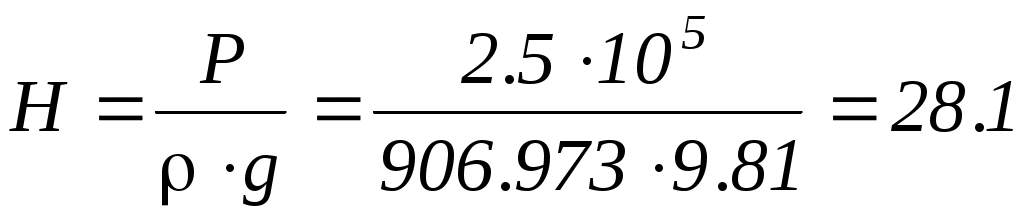
-
Гидравлический расчет произведем на ЭВМ с применением программы paket1.
Результаты расчета программы:
Исходные данные:
число участков N=1
длина участка, м L=177
внутренний диаметр, м D=0,081
сумма коэффициентов
местных сопротивлений SM=4.43
расчетная вязкость, мм2/с =216,7
шероховатость стенки трубы, мм К=0,5
разность геодезических отметок, м Z=3,6
остаточный напор, м Ност=4
Результаты гидравлического расчета:
Q, м3/ч Н, м
4,5 13,7
5,1 14,2
5,5 14,8
6,0 15,3
6,5 15,8
Как видно из результатов гидравлического расчета, давления, развиваемого насосом, хватает для перекачки масла до мерной емкости и, следовательно, маслопровод работоспособен.
Гидравлический расчет коллектора
Исходные данные: количество участков-2;
характеристика первого участка: длина L=88м; труба 89х4; разность геодезических отметок конца и начала участка z=-1,5м; местные сопротивления на участке: задвижек-2, поворотов на 90
0-1, тройников-5, фильтр-1;
характеристика второго участка: длина L=1,5м; труба 57х4; разность геодезических отметок конца и начала участка z=0,5м; местные сопротивления на участке: задвижек-2, поворотов на 900-1, тройник-1; шероховатость стенки трубы К=0,5мм; плотность масла 20=900 кг/м3; вязкость масла при температурах t1=500C и t2=200C cоответственно 50=21,3 мм2/с и 20=100мм2/с; величина остаточного напора Ност=0,2м.
За длину первого участка принято расстояние до самого дальнего от мерной емкости ГПА как наиболее неблагоприятный случай для расчета
-
Произведем расчет при температуре масла +50С, т.е. вязкость масла будет 278=216,7мм2/с. -
Определим сумму коэффициентов местных сопротивлений по длине участков коллектора. Величина их, на различных участках составляет:
m
Задвижка 0,15
Поворот на 900 1,32
Тройник 0,32
Фильтр 2,2
Для первого участка:
m=2*0,15+1,32+0,32*5+2,2=6,63
Для второго участка:
m=2*0,15+1,32+0,32=1,94
-
Гидравлический расчет произведем на ЭВМ с применением программы paket1.
Результаты расчета:
Исходные данные:
число участков N=2
1 участок
длина, м L=88
внутренний диаметр, м D=0,081
сумма коэффициентов местных сопротивлений SM=6,63
2 участок
длина, м L=1,5
внутренний диаметр, м D=0,041
сумма коэффициентов местных сопротивлений SM=1,94
расчетная вязкость, мм2/с =216,7
шероховатость стенки трубы, мм К=0,1
разность геодезических отметок, м Z=-1,5
остаточный напор, м Ност=0,3
Результаты гидравлического расчета:
Q, м3/ч Н, м
1,5 -0,6
2,0 -0,2
2,5 0,1
3,0 0,4
3,5 0,8
4,0 1,1
4. Построим характеристику самоточечного коллектора:
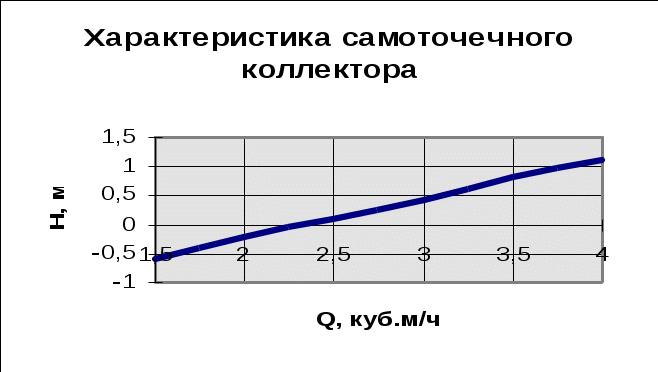
Как видно из характеристики, работа коллектора в самоточечном режиме возможна до тех пор, пока расход не достигнет значения Q=2,3 куб.м/ч (в этом случае потери напора в трубопроводе сравняются с гидростатическим напором масла в мерной емкости). Так как объем маслобака ГТУ V=2м3, то можно вычислить минимальное время его наполнения:
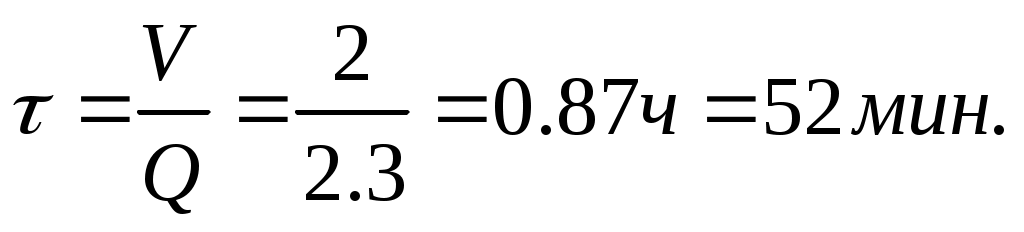
Литература
-
Машинист технологических компрессоров. Суринович В.К., Борщенко Л.И. М.: Недра, 1986г. -
Трубопроводный транспорт нефти и газа. Под редакцией Юфина В.А. М.: Недра, 1978г. -
Эксплуатация газопроводов Западной Сибири. Крылов Г.В. и др. М.: Недра, 1985г. -
Справочник по проектированию магистральных трубопроводов. Под ред. Дерцакяна А.К. М.: Недра, 1977г. -
Газотурбинные перекачивающие установки. Ревзин В.С. М.: Недра, 1986г. -
Турбинные установки и эксплуатация турбин. Денисов В.М., Попков В.Г., Ященко Ю.Г. М.: Машиностроение, 1971г. -
Документация по АВГ масла. -
Документация по неполнонапорному нагнетателю.