Файл: 3. Оборудование для размалывания формовочных материалов Пескометные установки.docx
ВУЗ: Не указан
Категория: Не указан
Дисциплина: Не указана
Добавлен: 03.02.2024
Просмотров: 36
Скачиваний: 0
ВНИМАНИЕ! Если данный файл нарушает Ваши авторские права, то обязательно сообщите нам.
Тонкостенные (толщина стенки 5…20 мм) формы изготовляют из песчано-смоляной смеси: мелкозернистого кварцевого песка или другого огнеупорного зернистого материала и термореактивной синтетической смолы (3…7 %). В качестве связующего чаще всего используют фенолформальдегидные смолы (СФ-12, СФ-15 и др.) с добавкой уротропина в количестве 8… 12 % от содержания смолы. Песчано-смоляную смесь готовят перемешиванием песка и измельченной порошкообразной смолы с добавкой растворителя (холодный способ) или при температуре 100… 120 °C (горячий способ), в результате чего смола обволакивает (плакирует) зерна песка. Затем комки смеси дополнительно дробятся до получения отдельных зерен, плакированных смолой, смесь загружается в бункер. Формовка производится по металлическим моделям.
Оболочковая форма состоит из двух полуформ с горизонтальной или вертикальной плоскостью разъема. Процесс изготовления оболочек из песчано-смоляной термореактивной смеси включает в себя следующие последовательные операции (рис. 1):
-
Металлическая модельная плита очищается, на нее пульверизатором наносится разделительный состав, облегчающий снятие оболочки. -
Модельная плита нагревается в электрической печи до температуры 200…220 °C. -
Плита 2 устанавливается над бункером 1 моделью вниз и закрепляется (рис. 1, я). Бункер переворачивают на 180°, и формовочная смесь 3 падает на нагретую модельную плиту (рис. 1, б). При выдержке в течение 20…30 с смола плавится и, обволакивая тонкой пленкой мелкие зерна песка, образует оболочку толщиной 8 мм. -
Бункер возвращают в исходное положение, и непрореагировавшая формовочная смесь падает на его дно (рис. 1, в). -
Снятую с бункера модельную плиту с непрочной оболочкой отправляют в электрическую печь, где нагревают до температуры 400 °C. Здесь смола в течение 90… 180 с полимеризуется и необратимо твердеет, образуя прочную оболочковую полуформу. -
Готовая оболочковая полуформа 4 снимается (рис. 1, г). с модельной плиты 6.с помощью толкателей 5. -
По такой же технологии изготавливают вторую полуформу. -
Стержни 8 формуют в нагретых стержневых ящиках 7 (рис. 1, д) центробежным способом (можно еще и свободной засыпкой, бункерным и.пескодувным способами). -
В одной из полуформ 9 (рис. 1,. е) на стержневые знаки устанавливают стержень, закрывают второй полуформой, скрепляют их скобами, струбцинами или склеивают по плоскости разъема. -
Собранную оболочковую форму 10 помещают в металлический ящик, засыпают крупным песком или чугунной дробью и заливают металлом. К моменту полной кристаллизации металла отливки смола из смеси выгорает, форма и стержни разупрочняются и легко разрушаются, освобождая отливку 11 при выбивке (рис. 1, ж).
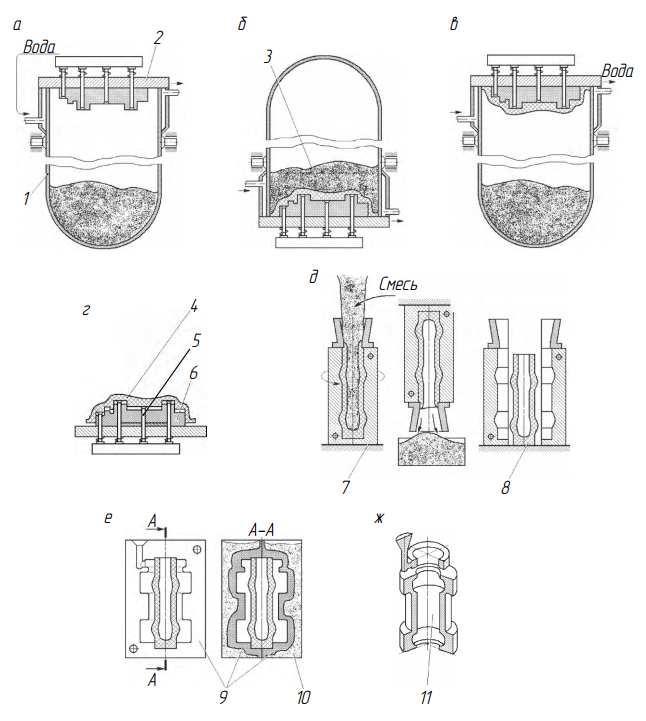
Рис. 1. Схема процесса литья в оболочковую форму
При производстве форм и стержней применяют три вида оборудования:
-
для приготовления песчано-смоляных смесей; -
для изготовления форм и стержней; -
для склеивания полуформ.
Для приготовления смесей применяют все типы смесителей. Они должны обеспечивать получение однородных смесей при отсутствии нагрева. Приготовление плакированных смесей, при котором требуется подогрев, можно производить любыми смесителями с устройствами для дальнейшего охлаждения готовой смеси.
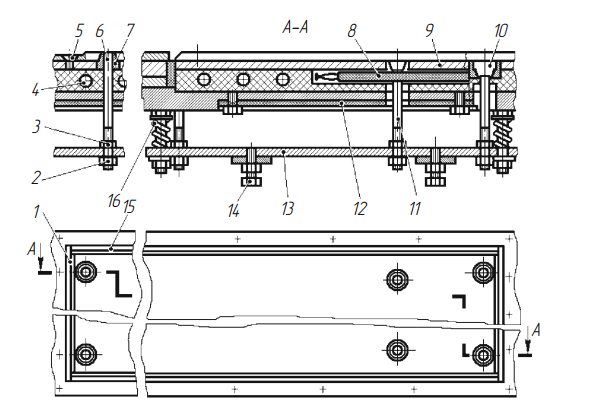
Рис. 2. Конструкция типовой модельной плиты
1. Модельное оборудование подготовки кокильного литья
У типовой модельной плиты для литья в оболочковые формы (рис. 2) металлические модели крепятся к плите 9. Прижимная плита 12 объединяет элементы конструкции в одно целое. Плита выталкивателей 13 удерживает выталкиватели 6 и 11, которые крепятся гайками 2 и 3, а также возвратные пружины 16, упоры 14. Планки торцевые 15 и боковые 1 ограничивают полуформу по периметру и предотвращают отслаивание незатвердевшей оболочки при подъеме с бункера; они крепятся винтами 5. Модели фиксаторов — центрирующих выступов 10 и углублений 7 — запрессованы в плиту 9. В плиту встраиваются трубки охлаждения 4 и термопара 8.
Оборудование для изготовления форм и стержней бывает одно- и многопозиционным, ручным, механизированным и автоматическим с различной производительностью. Подача формовочной смеси может выполняться несколькими методами. Пескодувный метод заполнения формы и уплотнения песчано-смоляной смеси является лучшим.
Схема пескострельной головки приведена на рис. 3. Стержневой ящик 10 устанавливают на столе 1, который, поднимаясь, прижимает его к надувной плите 3. Сжатый воздух из резервуара 7 через резко открываемый дутьевой клапан 8 поступает в песко- стрельный резервуар б, отчего давление в нем мгновенно повышается и воздух, ударно действуя на порцию песчано-смоляной смеси, выталкивает ее через конусную насадку 2 в нагретый стержневой ящик, благодаря чему в нем формируется и затвердевает стержень. Поступающий через прорези 5 на боковой поверхности гильзы сжатый воздух уменьшает трение смеси о стенки резервуара 6. Избыточный воздух из ящика 10 выходит через щелевидные отверстия 9, предусматриваемые в надувной плите или в ящике. Насадки 4 подбирают в зависимости от конфигурации и стержневого ящика.
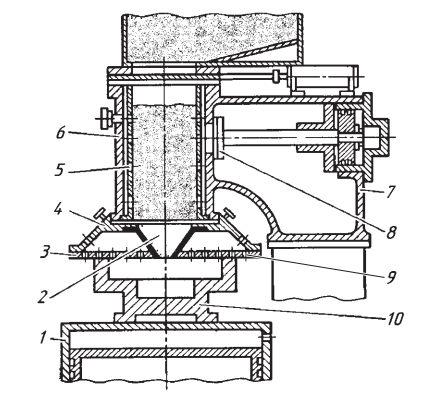
Рис. 3. Схема пескострельной головки
Однопозиционную полуавтоматическую пескодувную машину (рис. 4) применяют для изготовления стержней в нагреваемых ящиках размером до 700 х 550 х х 350 мм с вертикальным разъемом в цехах серийного и массового производства. Части нагреваемого стержневого ящика 7 соединяются с помощью цилиндра 2. На ящик при срабатывании цилиндра 3 опускается надувная головка 4, с помощью цилиндра 5 открывается шиберная заслонка, и песчано-смоляная смесь из бункера 6, находящегося в момент надува под давлением, по трубопроводу 7 заполняет рабочую полость ящика. Система отсоса 8 удаляет излишки песчано-смоляной смеси по трубопроводу 9 через сито 10 в приемный бункер 11. По окончании отвердевания стержня в момент раскрытия стержневого ящика срабатывают толкательная система и стержень. Предварительно просеянная песчано-смоляная смесь автоматически загружается в бункер 6. Температура нагрева стержневого ящика и выдержка после заполнения смесью и отвердевания обеспечивается автоматически.
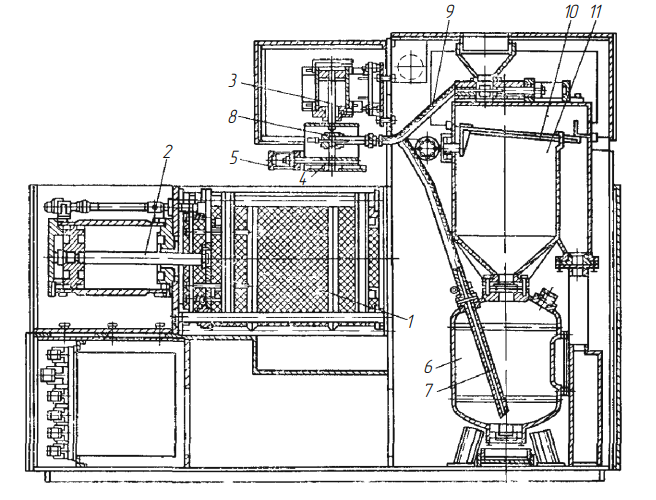
Рис. 4. Схема пескодувных машин моделей 91873, 91874, 91875
В двухпозиционной машине УКФ-2 (рис. 5) для изготовления оболочковых форм механизированы основные трудоемкие операции и контроль технологических параметров процесса (температура нагрева, выдержка модельного комплекта под смесью, отверждение оболочек, их снятие с модели). Машина имеет электрические печи 2 и 5, смонтированные на общей станине 1. Печи закрываются автоматическими заслонками 6. Посередине смонтирован поворотный бункер 8 для формовочной смеси с поворотным механизмом 9, работающим от пневмоцилиндров. С обеих сторон от бункера находятся два стола для съема готовых оболочек.
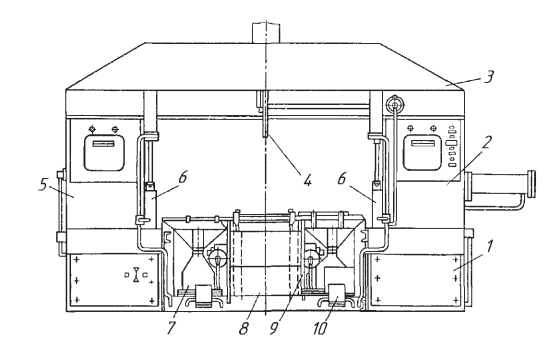
Рис. 5. Двухпозиционная машина УКФ-2 для производства оболочковых форм
Съем производится с помощью управляемых ножными пневмокранами 10 пневмогидравлических цилиндров 7. Модельная плита над бункером повачивается пневматическим подъемником 4. Машина закрыта общим вытяжным кожухом 3.Реклама
Производительность. машины — 40 полуформ в час при размерах плит 400.×.600 мм. Вместимость бункера — 80 кг.
Пневмосхема машины УКФ-2 приведена на рис. 6. Сжатый воздух поступает из магистрали через влагоотделитель 16 и масло- уловитель 17 к пневмоэлектрическому крану 25, который. подает его к.сдвоенным пневмоцилиндрам 9 и 23, поворачивающим бункер на 180° и обратно.(поворот осуществляется рейками, находящимися на штоке цилиндров, и зубчатым колесом, укрепленным на оси бункера).
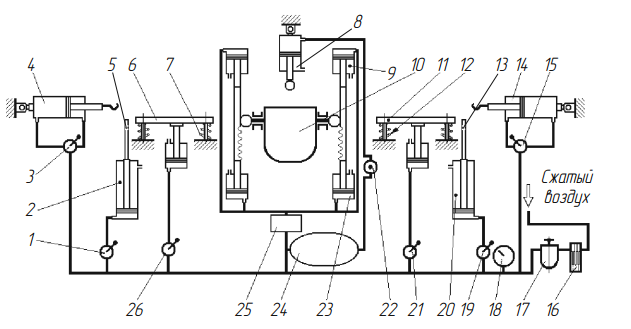
Рис. 6. Пневматическая схема машины УКФ-2 для производства оболочковых форм
Краном 25 управляют с.помощью кнопок «Пуск» и «Стоп» на пульте Одновременно сжатый воздух поступает к ножным пневмокранам 21 и 26, поднимающим плиту с толкателями 6, возвращаемую в.исходное положение пружинами 7 в левой части машины, и плиту 11 с пружинами 12 в правой части. Через ресивер 24 и кнопочный кран 22 осуществляется работа пневмосъемника 8, поворачивающего модельную плиту над бункером 10. Пневмокраны двойного действия 15 и 3 питают цилиндры 14 и 4, перемещающие модельные плиты из зоны бункера в электропечи. Одноходовые краны 1 и 19 питают пневмоцилиндры 2 и 20, которые поднимают заслонки 5 и 13 электропечей. Давление воздуха в магистрали контролируется манометром 18.
Для склеивания оболочковых полуформ и стержней используются устройства, сдавливающие полуформы по контуру клеевого шва с помощью пневмоцилиндров, пружин, пневматической диафрагмы. Пресс для склеивания с помощью пружин (рис. 7) имеет станину 8 с двумя стойками 12, стол 7, подвижную траверсу 3, неподвижную траверсу 2 с пневмоцилиндром 1, откидной стол 5 и пневмокраны 10 и 9 для управления прессом. Стол и подвижная траверса имеют сменные штыри 6 и 4 с пружинами, между которыми зажата оболочковая форма при склеивании. К штырям 4 подвижной траверсы присоединены резиновые шланги для подачи к местам склейки углекислого газа. Штыри в подвижную траверсу устанавливают согласно контуру склеиваемой формы.
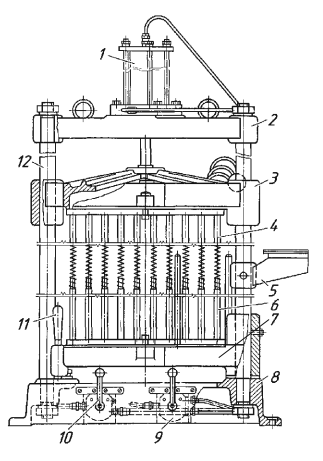
Рис. 7. Пресс для склеивания оболочковых полуформ
Стол 7 за рукоятку 11 выводят из-под подвижной траверсы. На пружины штырей стола кладут половину формы со стержнями, затем на поверхность склеивания наносят слой жидкого стекла и накладывают верхнюю половину формы. Стол с собранной формой подводят под подвижную траверсу, которая, опускаясь, сжимает оболочковую форму. Краном 10 включают подачу углекислого газа, продувка его продолжается 15…30 с. Поворотом крана 9 подвижную траверсу отводят в исходное положение, выдвигают стол и снимают с него склеенную форму. Производительность пресса — 80 форм в час при габаритных размерах склеиваемых форм 400 х 500 мм и давлении воздуха в сети привода 0,5…0,6 МПа.
33. Гидропрессовая установка, работающая от насосного привода
Гидравлические прессы позволяют получать изделия весьма сложной формы, этот метод обеспечивает получение наиболее сложных профилей, таких как оребренные трубы для теплообменных аппаратов, строительные профили (профили рам из легких сплавов).
Гидравлические прессы позволяют получить весьма высокие точность и качество поверхности, так как практически они определяются качеством матрицы, точность и шероховатость поверхностей которой может быть достигнута в процессе изготовления. Конечно, в процессе работы матрица изнашивается, что ухудшает вышеуказанные параметры изделия.
Гидравлические прессы широко используются для получения формованных, вытянутых и гнутых деталей из листа, для холодной объемной штамповки, правки разнообразных изделий, пакетирования и брикетирования отходов. Действие гидравлического пресса основано на ряде физических законов, в частности на законе Паскаля, устанавливающем, что давление на жидкость передается во все стороны с одинаковой силой. Если поместить в каждый из сообщающихся сосудов разного диаметра (рис. 4) по плунжеру, то, на основании этого закона, а также исходя из условий равновесия, можно написать: р = P1/F1 = P2/F2, откуда P2 = P1(F2/F1), где р – давление жидкости в системе сообщающихся сосудов, Па (кгс/см2); Р1 и Р2 – усилия, приложенные соответственно к малому и большому плунжерам, Н (кгс); F1, F2 – соответственно площади малого и большого плунжеров, м2 (см2). Таким образом, в рассматриваемой системе можно получить выигрыш в силе во столько раз, во сколько площадь большого плунжера превышает площадь малого.
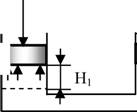
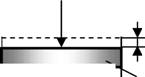
Рис. 4 Принципиальная схема гидравлического пресса
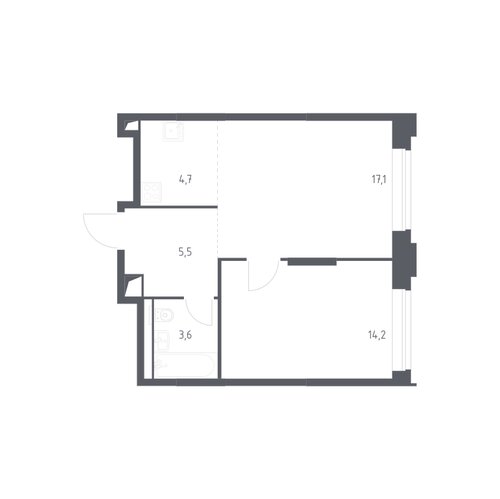
Элементы этой принципиальной схемы можно найти в том или другом виде в любом гидравлическом прессе: роль малого плунжера выполняет поршень гидравлического насоса, подающего жидкость, а роль большого плунжера - рабочий плунжер пресса. Усилие, развиваемое прессом, определяется произведением давления жидкости на сумму площадей рабочих плунжеров. Согласно другим физическим законам, в замкнутой гидравлической системе (например, в рассмотренной нами) перемещение одного плунжера вызывает такое перемещение другого плунжера, что объем жидкости в системе остается постоянным, поскольку жидкости практически несжимаемы. Если малый плунжер пройдет большое расстояние Hi, то большой плунжер переместится всего лишь на Н2 (см. рис. 4): Hi = H2(F2/Fi). Следовательно, в гидравлическом прессе, выигрывая в силе, столько же раз проигрывают в пути. Этот вывод полностью согласуется с законом постоянства энергии. Количество энергии, подведенное к малому плунжеру, равно количеству энергии, полученной на большом плунжере (здесь не учитываются потери в гидравлической системе пресса). Сказанное можно выразить иначе. Для этого надо перемножить написанные выше уравнения для усилия и пути, в результате получим Р1Н1 = Р2Н2. Приведенные соотношения раскрывают некоторые характерные черты гидравлических прессов.