ВУЗ: Не указан
Категория: Не указан
Дисциплина: Не указана
Добавлен: 08.02.2024
Просмотров: 8
Скачиваний: 0
ВНИМАНИЕ! Если данный файл нарушает Ваши авторские права, то обязательно сообщите нам.
Контроль за техническим состоянием технологического оборудования:
Главный инженер несёт ответственность за общую организацию и проведение мероприятий по системе технического обслуживания и ремонта технологического оборудования. Начальник РМЦ (Ремонтно Механический Цех) несёт ответственность за организацию технического обслуживания и ремонта технологического оборудования.
Начальник ОМЭиО (Отдел механики, энергетики и оборудования) несёт ответственность за организацию работ по техническому обслуживанию электротехнического оборудования, пароводяных коммуникаций, приборов и средств автоматизации.
Старший мастер РМЦ несёт ответственность за:
-
своевременность и полноту работ по проведению технического обслуживания и ремонта в соответствии с графиком ремонта; -
своевременность предоставления заявок на запасные части и материалы, необходимые для проведения технического обслуживания.
Цеховой персонал несёт ответственность за эксплуатацию оборудования в период от предварительной до окончательной приёмки оборудования из ремонта.
Слесари-ремонтники цехов несут ответственность за качественное выполнение технического обслуживания и ремонта.
Начальники цехов и участков несут ответственность за:
-
эксплуатацию и нормальное состояние технологического оборудования, уход за ним в период между ремонтами; -
предоставление данных в ОМЭиО о перемещении технологического оборудования.
Ведущий инженер-электроник ОМЭиО несёт ответственность за учёт и паспортизацию технологического оборудования.
1.4 Сдача оборудования в ремонт
На средний и капитальный ремонт машину останавливают мастер РМЦ с разрешения начальника или мастера производственного цеха, в сроки установленные графиком. Для своевременной заготовки деталей для машины, за пять дней до ремонта составляется ведомость дефектов.
Если машина ко времени очередного планового останова на ремонт находится в хорошем состоянии, то ремонт машины переносят на ближайший срок следующего очередного планового ремонта, начальник РМЦ вместе с начальником цеха составляют акт осмотра, который утверждается главным инженером.
При составлении ведомости дефектов особое внимание уделяют тем дефектам, которые уменьшают производительность оборудования, ухудшают качество продукции. Снижают надежность и безопасность работы.
При приеме машины в ремонт оценивают качество содержания оборудования в эксплуатации. Содержание считается хорошим, если сдаваемая машина неразукомплектована, отрегулирована и находится в чистом состоянии. Содержание считается неудовлетворительным, если в машине обнаружены: поломанные или преждевременно изношенные из-за плохой смазки детали, разукомплектованные узлы и механизмы, неисправные ограждения или приспособления, которые делают работу на машине опасной.
Для оценки содержания машины в эксплуатации на предприятии применяют бальную систему, сущность которой заключается в следующем. Каждому дефекту машины, возникающему из-за плохой эксплуатации, присваивают соответствующий балл, например от одного до пяти; чем серьезней дефект, тем выше балл. Дефекты, возникающие в результате естественного износа при нормальной эксплуатации, баллами не оцениваются.
Если ответственные органы машины загрязнены, смазочные отверстия не очищены, не смазаны, то независимо от других дефектов дается оценка «плохо».
Пользуясь этой шкалой применительно к любому классу машин, устанавливают подробные по дефектные и по детальные оценки в баллах. Перечень дефектов с соответствующими оценками вноситься в ведомость дефектов. Оценку качества эксплуатации и состоянии машины, поступающей в ремонт. Дают по сумме балов: чем больше баллов, тем ниже оценка. Существует три оценки: отличная, хорошая и плохая. Для швейного оборудования: отлично - до 10 баллов, хорошо - до 20 баллов, плохо - более 20 баллов.
1.5 Организация рабочего места слесаря-ремонтника
Организация рабочего места слесаря-ремонтника обеспечивает удобство и безопасность работ, связанных с ремонтом машин и механизмов, и для окружающих рабочих мест, связанных с выпуском продукции, помогает соблюдению технологической дисциплины, повышает производительность, снижает утомляемость и обеспечивает снижение стоимости ремонта.
Рабочим местом является зона, на которой располагается верстак и все вспомогательное оборудование и приспособления, используемые при ремонте.
Р
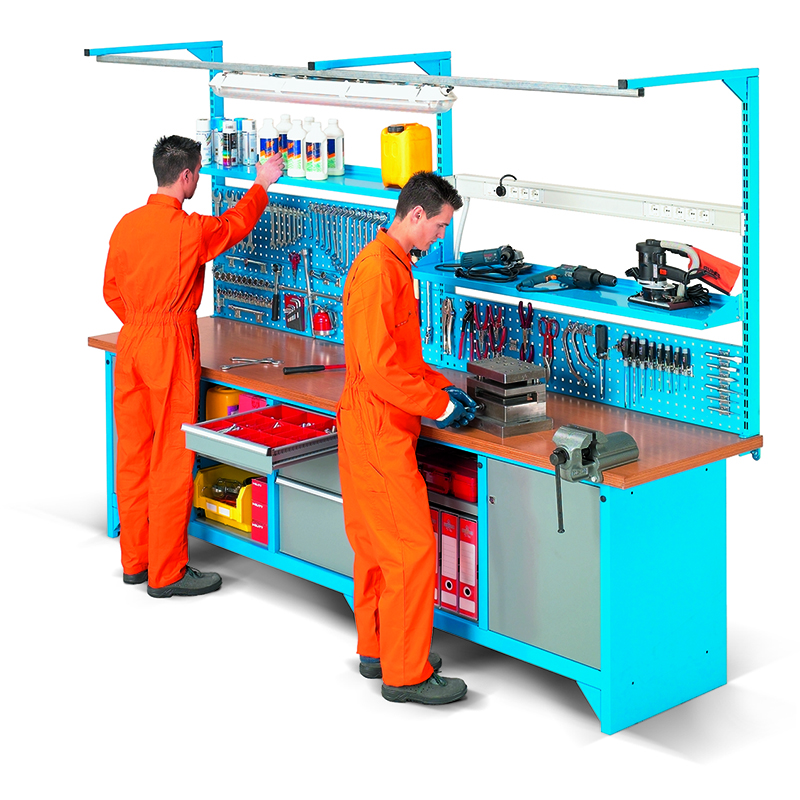
азличают постоянные рабочие места (в ремонтной мастерской или на обслуживаемом производственном участке) и временные – возле ремонтируемого станка, машины и т.п. Временные рабочие места разделяют на временные возле станка, находящегося в плановом (длительном) ремонте, и кратковременные у механизма, находящегося в текущем обслуживании. В зависимости от этого при организации рабочих мест используются различные средства, приспособления и предъявляются несколько различные требования.
Рисунок 4 – Рабочее место слесаря
Постоянное рабочее место слесаря-ремонтника должно иметь достаточные размеры для удобного размещения оборудования, приспособлений и инструментов.
Временное рабочее место слесаря-ремонтника организуется у ремонтируемого станка, машины и т.п. (на рабочем месте оператора). Поэтому технологическая оснастка, которая может препятствовать ремонту или может быть повреждена, должна быть снята со станка и убрана для сохранности. Рядом со станком необходимо освободить зону для организации рабочего места слесаря, включая подходы и, при необходимости, подъезды.
Временное рабочее место оснащается передвижными (на колесиках) верстаком, стеллажом и другими необходимыми для разборки и ремонта станка средствами. Как правило, временное рабочее место должно быть отделено от окружающей территории передвижными защитными устройствами.
По окончании ремонтных работ для проверки работы станка все приспособления, технологическая оснастка, инструменты и принадлежности оператора должны быть установлены на прежние места.
Кратковременное рабочее место слесаря-ремонтника организуется на период текущего обслуживания станка на рабочем месте оператора. В этом случае убираются только те приспособления, инструмент и технологическая оснастка и оргоснастка оператора, которые мешают при работе слесаря. В качестве оргоснастки для работы слесаря-ремонтника используется переносный ящик с инструментом. Ящик не должен быть тяжелым и громоздким, и в нем размещается инструмент первой необходимости. Очень часто для этих целей используются ящики с откидными крышками или выдвижными полками, что позволяет более удобно разместить инструмент. Во всех случаях рабочая зона станка должна быть доступной для работы слесаря-ремонтника.
1.6 Технологический процесс ремонта машины
Разборка – это зеркальное отражение сборки машины. Деталь, установленная при сборке последней, будет сниматься первой при разборке. При разборке машину разбирают на сборочные единицы, а их на детали. В зависимости от ремонта разборка бывает полной и частичной.
Перед разборкой парных деталей, которые располагаются определенным образом, необходимо нанести определенную метку.
Разбираться должна только та сборочная единица или тот механизм, который подлежит ремонту, так как подетальная разборка ведет к нарушению прирабатываемости и плотности соединений деталей. Для промывания деталей существуют следующие способы: ручная промывка, в моечных камерах в одно-, двух- и трехкамерных моечных машинах.
При разборке и сборке оборудования применяют следующий инструмент: стальные молотки с деревянной ручкой, специальные «мягкие» молотки, универсальные отвертки, универсальные и специальные гаечные ключиразличных конструкций, сверлильные электро и пневмомашины, электрошаберы, электрогайковерты, резьбонарезатели, электроножницы.
Производственный процесс ремонта оборудования состоит из подготовительных, основных технологических и сопутствующих процессов.
Технологические процессы ремонта, несмотря на большое разнообразие оборудования, обычно представляются в общей структуре производственного процесса в такой последовательности:
1) приемка в ремонт;
2) наружная очистка и мойка оборудования;
3) разборка оборудования на агрегаты, сборочные единицы и детали;
4) мойка сборочных единиц и деталей;
5) контроль и дефектовка деталей;
6) ремонт деталей;
7) комплектование сборочных единиц и агрегатов;
8) сборка, регулировка, обкатка и испытание агрегатов;
9) сборка, регулировка, обкатка и испытание оборудования целиком;
10) окраска оборудования;
11) сдача отремонтированного оборудования в эксплуатацию.
Разборка оборудования является начальным этапом производственного процесса ремонта. Правильная организация и высокое качество выполнения разборочных работ оказывают значительное влияние на продолжительность, трудоемкость и качество ремонта.
В зависимости от характера износа и повреждения деталей оборудования и номенклатуры деталей, требующих дефектации, ремонта или замены, разборка может быть частичная (с различной глубиной) или полная. Частичная разборка имеет место при текущем и среднем ремонтах, полная – при капитальном ремонте.