Добавлен: 16.03.2024
Просмотров: 15
Скачиваний: 0
ВНИМАНИЕ! Если данный файл нарушает Ваши авторские права, то обязательно сообщите нам.
Технологические свойства порошка определяют насыпная плотность, текучесть, прессуемость и формуемость. Насыпная плотность — это масса единицы объема порошка при свободном заполнении объема. Текучесть порошка характеризует скорость заполнения единицы объема и определяется массой порошка, высыпавшегося через отверстие заданного диаметра в единицу времени. Под прессуемостью порошка понимают свойство порошка, приобретать при прессовании определенную плотность в зависимости от давления, а под формуемо- стью — свойство порошка сохранять заданную форму, полученную после уплотнения при минимальном давлении.
Целью формования порошка является придание заготовкам из порошка формы, размеров, плотности и механической прочности, необходимых для последующего изготовления изделий. Формование включает следующие операции: отжиг, классификацию, приготовление смеси, дозирование и формование.
Отжиг порошков применяют в целях повышения их пластичности и прессуемости за счет восстановления остаточных окислов и снятия наклепа. Нагрев осуществляют в защитной среде (восстановительной, инертной или вакууме) при температуре 0,4—0,6 Тпл металла порошка.
Классификация порошков — это процесс разделения порошков по величине частиц. Классификацию частиц размером более 40 мкм производят в проволочных ситах, более мелких порошков — на воздушных сепараторах.
В производстве для изготовления изделий используют смеси порошков разных металлов. Наиболее часто применяют механическое смешивание компонентов в шаровых мельницах и смесителях. Смешивание без измельчения проводят в барабанных, лопастных, центробежных, конусных смесителях и установках.
При приготовлении шихты некоторых металлических порошков высокой прочности (вольфрама, карбидов металлов) для повышения формуемости в смесь добавляют пластификаторы — вещества, смачивающие поверхность частиц.
Формование порошков — технологическая операция по образованию из свободно насыпанного порошка тела с заданными формой, размерами, плотностью и прочностью. Формование порошков осуществляют прессованием в глухую матрицу, изостатическим и динамическим прессованием, шликерным, мундштучным, вибрационным и другими методами.
Процесс уплотнения порошкового материала в отличие от деформирования компактного материала сопровождается значительным изменением объема прессуемого тела. На начальной стадии уплотнение происходит за счет перемещения частиц порошка и их более плотной упаковки, на последующих этапах — в результате упругой и пластической деформации частиц или их хрупкого разрушения (в зависимости от свойств деформируемых порошков). Прочность заготовки с повышением давления прессования увеличивается и обеспечивается за счет механического сцепления частиц и сил межатомных и межмолекулярных связей. На практике снижение трения порошка о стенку матрицы, а следовательно, улучшение условий процесса прессования достигается применением смазки и другими технологическими приемами. Уплотнение производят на гидравлических или механических прессах, давление прессования составляет 200—1000 МПа в зависимости от свойств порошка и назначения изделия. Детали пресс-форм выполняют из высокоуглеродистых легированных сталей (инструментальных сталей), твердых сплавов. Стойкость стальных пресс-форм составляет 1—50, пресс-форм из твердых сплавов — до 500 тыс. прессовок.
Механические автоматы предназначены для изготовления деталей простой формы типа гладких втулок с односторонним буртом с высокой чистотой поверхностей и размерами 2-го и 3-го классов точности, причем после прессования и спекания изделия в основном не требуют механической обработки; возможно получение изделия сложной конфигурации, в том числе из различных смесей металлов; изделия, обладающие повышенными свойствами износоустойчивости, твердости и жаропрочности. Внешний вид механических прессов приведен на рис. 1, их основные характеристики — в табл. 2
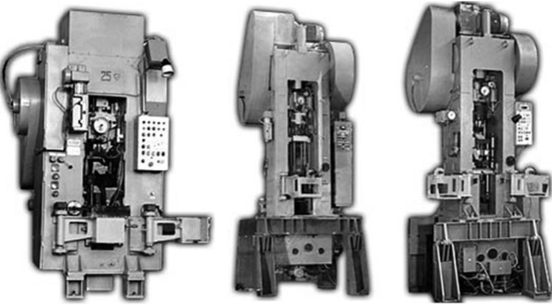
Рисунок 1 - Механические порошковые прессы
Номинальное усилие, кН | 250 | 630 | 1 000 |
Высота засыпки порошка в матрицу, мм | 0-90 | 0-140 | 0-180 |
Наибольший путь прессования, мм | 63 | 100 | 125 |
Наибольший размер изделия в плане (диаметр описанной окружности), мм | 63 | 100 | 125 |
Регулируемая частота ходов | 12-40 | 10-32 | 9-25 |
Ход ползуна, мм | 130+1,5 | 200±2 | 220+2,2 |
Величина регулировки положения пуансона, мм | 60 | 140 | 180 |
Ход центрального стержня, мм | 90 | 100 | 120 |
Габарит автомата (слева — направо), мм | 1 500± 15 | 1 920± 19 | 2 350±25 |
Габарит автомата (спереди — назад), мм | 1 400± 14 | 1 630± 16 | 2 100+20 |
Габарит автомата (высота), мм | 2 800±28 | 4 870±48 | 5 680±55 |
Высота над уровнем пола, мм | 2 800±28 | 3 740±37 | 4 480145 |
Масса автомата, кг | 3 600±70 | 9 500+100 | 12 250130 |
Таблица 2 - Основные технические характеристики механических прессов
В процессе формования различают три стадии уплотнения порошков:
активное уплотнение, при котором происходит перераспределение частиц, разрушение мостиков, упаковка частиц порошка становится более плотной;
-
появление упругих напряжений на контактных поверхностях при неизменной плотности порошковой массы; -
дальнейшее уплотнение в результате пластической деформации частиц порошка и некоторого хрупкого их разрушения, когда напряжение в контактных участках превышает предел текучести.
Вибрационное уплотнение основано на уплотнении металлических порошков при наложении вибрации при засыпке и утряске порошка в пресс-форме или в процессе формования, что позволяет значительно снизить усилие прессования и повысить равномерность распределения плотности по объему тела. Положительное влияние вибрации на процесс уплотнения связано с разрушением начальных межчастичных связей и повышением взаимоподвижности частиц.
Уплотнение порошков при этом осуществляется при статических давлениях 0,5—5,0 МПа, продолжительность уплотнения — не более 30 с. Для уменьшения трения между частицами порошка при вибродеформации используют смазки (глицерин, вазелин и другие в количестве 0,5— 1,5% по объему).
Шликерное формование заключается в заполнении шликером (устойчивой суспензией порошка) пористой формы, которая обеспечивает возможность удаления жидкости из шликера. В процессе удаления жидкости из шликера, например, сушкой на воздухе в сушильных шкафах при температуре 110—150 °С, на стенках формы формуется заготовка. В качестве жидкой фазы используют воду, спирт, четыреххлористый углерод и т.п.
Мундштучное прессование (рис. 2) заключается в продавливании порошковой смеси через отверстие, придающее заготовке заданную форму и размеры поперечного сечения. Его используют для получения прутков, уголков, труб и др.
Прессование в закрытой пресс-форме (рис. 3) выполняют по одно- или двухсторонней схеме. В этом процессе до 80% полезного усилия пресса расходуется на преодоление сил трения порошка о стенки пресс-формы, что предопределяет неравномерность распределения плотности и свойств по объему тела. Обычно этот метод используют для формования изделий простой формы: втулок, колец и др. с отношением
H/D <1 при высоте их Н <20 мм.
Изостатическое формование заключается в уплотнении металлического порошка в эластичной или деформируемой оболочке в условиях всестороннего сжатия. Этим методом получают прессовки с большим отношением длины к диаметру (ширине) с тонкими стенками и равномерной плотностью. Разработано много разновидностей этого метода.
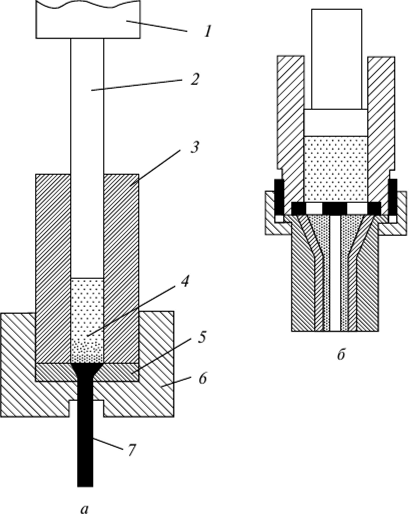
Рисунок 2 - Схема «мундштучного» прессования прутков (а) и труб (б):
1 — плунжер пресса; 2 — пуансон; 3 — стальной стакан; 4 — порошок; 5 — конус; 6 — матрица; 7 — спрессованная заготовка
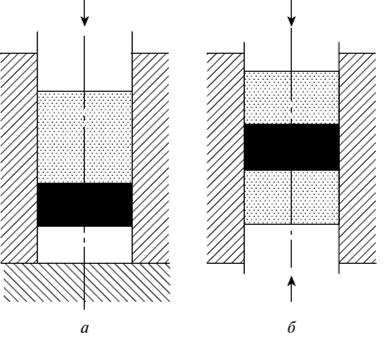
Рисунок 3 - Схемы одностороннего (а) и двухстороннего (б) прессования
Гидростатическое прессование применяют для получения металлокерамических заготовок, к которым не предъявляют высоких требований по точности. При гидростатическом прессовании (рис. 4) порошок засыпают в эластичную оболочку (рис. 5), которую помешают в рабочую камеру; крышку аппарата герметически закрывают и в камере создают требуемое давление жидкости. Гидростатическим прессованием получают изделия самой разнообразной формы массой от нескольких грамм до нескольких сотен килограмм. Давление жидкости в гидростатах создают от 100 до 1200 МПа. Давление жидкости достигает 3000 МПа, что обеспечивает получение заготовок высокой прочности и плотности. При гидростатическом прессовании отпадает необходимость в применении дорогостоящих пресс-форм. Габаритные размеры изготовляемых заготовок зависят от конструкции герметизированной камеры.
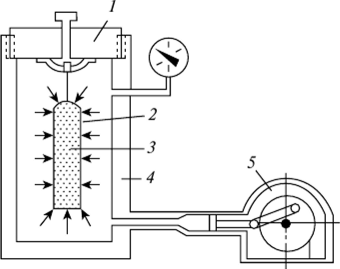
Рисунок 4 - Установка для гидростатического формования порошка:
-
1 — крышка гидростата; 2 — эластичная оболочка; 3 — порошок; -
4 — камера прессования; 5 — насос высокого давления
Другим вариантом формования при всестороннем обжатии является газостатическое прессование под действием газа (гелий, аргон и др.) под определенным давлением. В большинстве случаев такому прессованию подвергают предварительно уплотненную заготовку.
Прокатка порошков — один из наиболее производительных и перспективных способов переработки металлокерамических материалов.
Полуфабрикаты в виде листов, полос, лент и фольги получают методом прокатки порошков. При этом порошок поступает в зазор между двумя вращающимися ватками и уплотняется в полосу, которая затем подвергается спеканию и возможной последующей обработке давлением. Прокаткой порошков получают также двух- и трехслойные, полосы и ленты. В этом случае лента проходит через проходную печь для спекания, а затем поступает на прокатку, обеспечивающую заданную ее толщину. Прокаткой получают ленты из различных материалов (пористых, твердосплавных, фрикционных и др.). За счет применения бункеров с перегородкой изготовляют ленты из различных материалов (двухслойные). Прокаткой из металлических порошков изготовляют ленты толщиной 0,02—3,0 мм и шириной до 300 мм. Применение валков определенной формы позволяет получить прутки различного профиля, в том числе и проволоку диаметром от 0,25 мм до нескольких миллиметров. Для прокатки порошков применяют, как правило, двухвалковые станы; станы кварто используют на завершающей отделочной стадии прокатки тонких лент или для горячей прокатки бес- пористых лент (рис. 6).
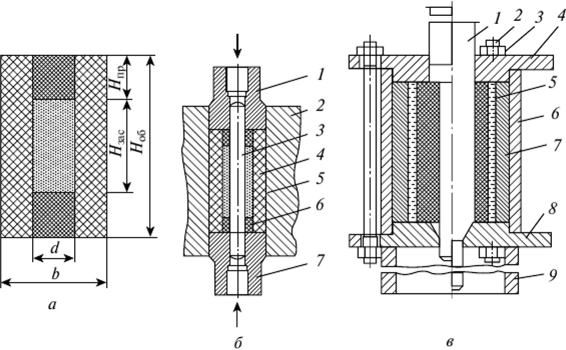
Рисунок 5 - Толстостенные эластичные оболочки для прессования порошков: а — для прессования цилиндров; б — для прессования втулок: 1 — верхний пуансон; 2 — матрица; 3 — стержень; 4 — порошок; 5 — толстостенная оболочка; 6 — пробка; 7 — нижний пуансон; в — с внутренним обжатием: 1 — оправка; 2 — шпилька; 3 — гайка; 4 — крышка; 5 — эластичная оболочка; 6— корпус; 7— матрица; 8— поддон; 9— кольцо
Прокатка - порошок непрерывно поступает из бункера в зазор между валками (рис. 6). При вращении валков 2 происходит обжатие и вытяжка порошка в ленту или полосу определенной толщины. Процесс прокатки может быть совмещен со спеканием и окончательной обработкой получаемых заготовок.
В промышленности применяют также схемы вертикальной прокатки порошков (рис. 7, а), в том числе в вакууме (рис. 7, б).
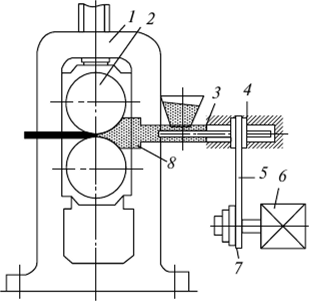
Рисунок 6 - Схема прокатки порошка на стане:
1 — станина; 2 — рабочие валки; 3 — шнек; 4 — муфта; 5 — клиновой ремень; 6— электродвигатель; 7— шкив; 8 — камера
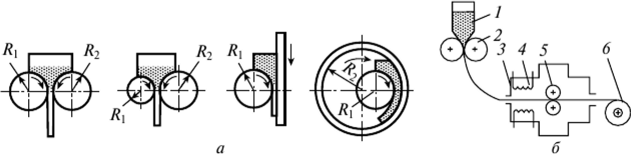
Рисунок 7 - Схемы вертикальной прокатки порошков (а) и схема процесса прокатки порошков титана:
1 — бункер; 2 — прокатные валки; 3 — вакуумная камера; 4 — печь спекания; 5 — стан горячей прокатки; 6 — моталка
Импульсное формование - уплотнение порошка при этом производится ударными волнами; в качестве источника энергии применяют взрывчатые вещества, сжатые газы, импульсное электромагнитное поле и др. При взрывном прессовании возможны разные способы создания нагрузки на порошковое тело: непосредственным воздействием продуктов взрыва на порошок; через жидкую или сыпучую среду; через пуансон и т.д. Некоторые схемы прессования взрывом плоских и осесимметричных (сплошных и полых) заготовок из порошков приведены на рис. 7
Перспективным является гидродинамическое прессование, обеспечивающее деформацию порошка в условиях всестороннего сжатия давлением пороховых газов (рис. 8). Этим методом получают изделия сложной формы, крупные фильтры, заготовки из тугоплавких металлов и сплавов и другие изделия.