Файл: 1 Разработать схему технологического процесса восстановительного ремонта детали 3.docx
Добавлен: 10.04.2024
Просмотров: 44
Скачиваний: 0
ВНИМАНИЕ! Если данный файл нарушает Ваши авторские права, то обязательно сообщите нам.
СОДЕРЖАНИЕ
1 Разработать схему технологического процесса восстановительного ремонта детали
1.1 Характеристика детали и условий ее работы
1.2 Выбор способов восстановления детали
2 Разработать план технологических операций по восстановлению детали
2.3 Выбор оборудования приспособления и инструмента
3 Определить основное время на заварку шлицев вала ведущего коробки передач автомобиля ГАЗ-24
4 Определить штучное время на заварку шлицев вала ведущего коробки передач автомобиля ГАЗ – 24
5 Разработать проект цеха (отделения, участка, места) восстановления детали (по заданию 4)
5.3 Планировка оборудования и рабочих мест
5.4 Организация транспортировки детали
Содержание
Введение 1
1 Разработать схему технологического процесса восстановительного ремонта детали 3
1.1 Характеристика детали и условий ее работы 3
1.2 Выбор способов восстановления детали 8
2 Разработать план технологических операций по восстановлению детали 9
2.1 Исходные данные 9
2.2 Выбор и обоснование способов восстановления ведущий вала 9
2.3 Выбор оборудования приспособления и инструмента 12
3 Определить основное время на заварку шлицев вала ведущего коробки передач автомобиля ГАЗ-24 13
4 Определить штучное время на заварку шлицев вала ведущего коробки передач автомобиля ГАЗ – 24 15
5 Разработать проект цеха (отделения, участка, места) восстановления детали (по заданию 4) 16
5.1 Расчет количества оборудования 17
5.2 Расчет площади 18
5.3 Планировка оборудования и рабочих мест 18
5.4 Организация транспортировки детали 18
5.5 Организация технического контроля 18
Список использованных источников 19
Введение
Ремонт автомобилей является объективной необходимостью, которая обусловлена техническими и экономическими причинами.
Во-первых, потребность народного хозяйства в автомобилях частично удовлетворяется путем эксплуатации отремонтированных автомобилей. Во-вторых, ремонт обеспечивает дальнейшее использование тех элементов автомобилей, которые не полностью изношены. В результате сохраняется значительный объем прошлого труда. В-третьих, ремонт способствует экономии материалов идущих на изготовление новых автомобилей. При восстановлении деталей расход материалов в 20…30 раз ниже, чем при их изготовлении.
Многочисленные исследования показали, что первый капитальный ремонт, как правило, по всем слагающим экономической эффективности затрат общественного труда выгоднее приобретения нового автомобиля. Это объясняется двумя возможными обстоятельствами:
- фактические затраты на первый капитальный ремонт большинства видов машин и оборудования не превышает 30-40 % их балансовой стоимости, повторные же ремонты обходятся значительно дороже;
- большинство видов машин подвергаются первому капитальному ремонту, как правило, до наступления морального износа.
Общее число деталей в современных автомобилях составляет тысячи наименований. Однако число деталей, лимитирующих их срок службы до капитального ремонта, не превышает нескольких десятков наименований. Задача заключается в том, чтобы повысить долговечность этих деталей до уровня обеспечивающего наибольшую долговечность автомобиля.
Наряду с поиском путей и методов повышения надежности, которая закладывается в конструкцию автомобиля при проектировании и внедряется в сфере производства, необходимо изыскать пути и методы для решения этой же задачи в сфере эксплуатации и ремонта. От того, как разумно будет использоваться ресурс автомобилей в эксплуатации, зависит действительный срок его службы до капитального ремонта.
Авторемонтное производство, получив значительное развитие, еще не в полной мере, реализует свои потенциальные возможности. По своей эффективности, организационному и технологическому уровню оно еще отстает от основного производства автомобилестроения. Качество ремонта остается низким, стоимость высокой, уровень механизации достигает лишь 25…40 %, вследствие чего производительность труда в два раза ниже, чем в автомобилестроении. Авторемонтное предприятие (АРП) оснащены в основном универсальным оборудованием большой степени изношенности и малой точностью. Это негативные стороны современного состояния авторемонтного производства и определяют пути его развития.
Целью данного курсового проекта является разработка технологического процесса восстановления вала коробки передач Газ- 24.
1 Разработать схему технологического процесса восстановительного ремонта детали
1.1 Характеристика детали и условий ее работы
Ведомый подвижный конус (шкив) с помощью подшипников (только уже девяти шариков) опирается на ведомый вал вариатора. Ведущий вал состоит из подвижного и неподвижного конуса. Ход подвижного конуса также составляет 22 мм.
Необходимое нажимное усилие для создания силы трения между металлическим ремнем и конусами шкива формируется нажимными тарелками и пружиной в управляющих полостях подвижного конуса.
До снятия подвижного конуса с ведомого вала проверим сжатым воздухом масляный канал вала и уплотнители подвижного конуса (нижний снимок). К торцу вала подсоединяем переходник и подаем сжатый воздух и наблюдаем откуда может сочится воздух. Движение подвижного конуса мы наблюдать не можем, т. к. преодолеть сопротивление пружины ножным насосом не возможно, необходимо до 60 атм.
Повышение крутящего момента при помощи шестеренчатой передачи иллюстрирует схема, показанная на рис.
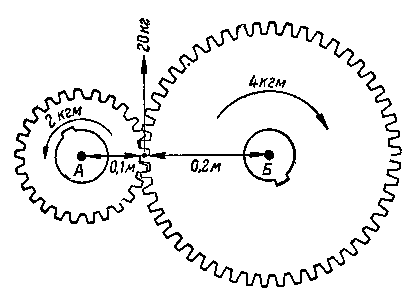
Схема передачи крутящего момента через шестерни: А – ведущий вал; Б – ведомый вал
Допустим, что крутящий момент ведущего вала А равен 2 кгм. Тогда окружная сила на зубьях шестерни вала будет равна крутящему моменту, деленному на радиус шестерни (0,1 м), т. е. 20 кг (2:0,1). С такой силой зубья малой шестерни вала А давят на зубья большей шестерни ведомого вала Б. Чтобы найти крутящий момент ведомого вала Б, надо силу, действующую на зубья шестерни этого вала, умножить на плечо ее действия, т. е. на радиус, равный в данном примере 0,2 м. Отсюда крутящий момент ведомого вала Б составит 4 кгм (20*0,2).
Следовательно, крутящий момент на ведомом валу увеличивается во столько раз, во сколько раз радиус (или число зубьев) ведомой шестерни больше радиуса (числа зубьев) ведущей. Здесь шестерни разных размеров могут рассматриваться как рычаги разной длины.
Отношение числа зубьев (или числа оборотов) ведомой шестерни к числу зубьев (или числу оборотов) ведущей шестерни называется передаточным числом. Если, например, ведомая шестерня имеет 20 зубьев, а ведущая 10, то передаточное число будет равно 20/10=2. Следовательно, если передаточное число больше единицы, ведомый вал вращается медленнее ведущего, а если меньше единицы, то быстрее его; во столько же раз изменится (увеличится или уменьшится) и крутящий момент.
Снимаем подвижный конус для проверки состояния девяти шариков и пазов на вале. Откручиваем гайку (1), снимаем сьемником ведущую шестерню (2) и шестерню механизма блокировки ведомого механизма (3).
Поступаем также как и с ведущим валом, ударяем торцом о мягкую доску и извлекаем подвижный конус и девять шариков. Визуально проверяем состояние шариков и пазов на вале. Пазы должны быть чистые без сколов по краям. Шарики круглые без вмятин (не квадратные).
Не круглые шарики и сколы в пазах являются основной причиной обрыва металлического ремня из-за заклинивания подвижных конусов ведущего и ведомого вала.
Надо резко трогаться с места, резко тормозить, чтобы подвижные конусы работали на смятие шариков и получались сколы в пазах валов.
Назначение коробки передач – изменять крутящий момент, подводимый к ведущим колесам, и направление вращения колес (задний ход). Кроме того, коробка передач позволяет разобщать коленчатый вал двигателя с карданным валом (а значит и с ведущими колесами) при работе двигателя на холостом ходу (при запуске, прогреве, движении накатом и т. д.).
Для самостоятельного движения автомобиля необходимы два условия:
1) к ведущим колесам должен быть подведен от двигателя крутящий момент, достаточный для вращения колес при имеющихся силах сопротивления движению автомобиля;
2) между ведущими колесами и полотном дороги должно быть достаточное по величине сцепление (т. е. сила трения), чтобы колеса не могли проскальзывать относительно дороги (буксовать).
При передаче крутящего момента от главной передачи к ведущим колесам в точках соприкосновения шин ведущих колес с дорогой появляется окружная касательная сила, которая направлена в сторону, противоположную движению автомобиля. По закону равенства действия и противодействия окружная сила вызывает появление равной ей, но направленной в противоположную сторону силы, называемой касательной реакцией. Эта реакция является силой трения шин ведущих колес о дорогу, она также приложена в точках соприкосновения дороги с шинами, но направлена в противоположную окружной силе сторону – в сторону движения автомобиля. Эта реакция называется тяговой силой.
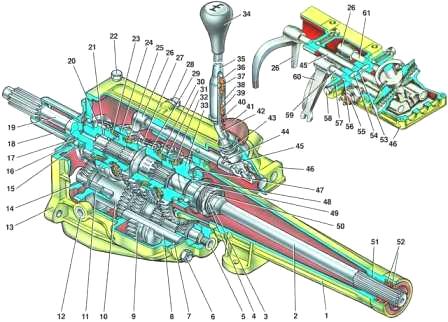
1 – удлинитель картера коробки передач; 2 – вторичный вал; 3 – стопорное кольцо; 4 – упорная шайба; 5 – резьбовая пробка; 6 – гайка; 7 – штифт; 8 – ось промежуточной шестерни заднего хода; 9 – промежуточная шестерня заднего хода; 10 – блок шестерен; 11 – игольчатый подшипник; 12 – маслозаливная пробка; 13 – картер коробки передач; 14 – ось блока шестерен; 15 – катушка зажигания; 16 – стопорное кольцо; 17 – стопорное кольцо; 18 – крышка подшипника первичного вала с направляющей втулкой; 19 – первичный вал; 20 – маслоотражатель; 21 – передний роликовый насыпной подшипник вторичного вала; 22 – болт; 23 – блокирующее кольцо синхронизатора шестерни 4‑й передачи; 24 – синхронизатор 3‑й и 4‑й передач; 25 – блокирующее кольцо синхронизатора шестерни 3‑й передачи; 26 – вилка переключения 3‑й и 4‑й передач; 27 – шестерня 3‑й передачи; 28 – болт; 29 – шестерня 2‑й передачи; 30 – блокирующее кольцо синхронизатора шестерни 2‑й передачи; 31 – синхронизатор 1‑й и 2‑й передач; 32 – блокирующее кольцо синхронизатора шестерни 1‑й передачи; 33 – шестерня 1‑й передачи; 34 – рукоятка; 35 – верхняя часть рычага переключения передач; 36 – упорный конус; 37 – верхняя подушка рычага; 38 – распорная втулка; 39 – нижняя подушка рычага; 40 – запорная втулка; 41 –
уплотнитель верхней крышки; 42 – нижняя часть рычага переключения передач; 43 – пружина рычага; 44 – штифт; 45 – шток включения 3‑й и 4‑й передач; 46 – крышка коробки передач; 47 – стопорное кольцо; 48 – регулировочная шайба; 49 – задний подшипник вторичного вала; 50 – ведущая шестерня привода спидометра; 51 – сталеалюминиевая втулка; 52 – сальник; 53 – стопорный палец штоков; 54 – стопорный плунжер штоков; 55 – выключатель света заднего хода; 56 – шарик
1.2 Выбор способов восстановления детали
деталь технологический восстановление
Дефекты:
-
Износ шлицев по толщине -
Износ шейки под шариковый подшипник коленчатого вала
3. Износ поверхности конус вала
Возможные способы устранения:
по дефекту 1:
- наплавить
по дефекту 2:
- хромировать
по дефекту 3
– Хромирование.
– Железнение.
При анализе способов устранения каждого дефекта выявлены два способа, пригодных для устранения этих дефектов: хромирование, вибродуговая наплавка. Оба способа являются общими для каждого дефекта.
Для выбора конкретного способа восстановления используются конструктивные и технологические характеристики деталей, учитывающие несколько важных признаков: форму, размеры, толщину покрытия, твердость поверхности, коэффициент износостойкости, характер действующих нагрузок, коэффициент технико-экономической эффективности. На основании этих признаков определены возможные способы восстановления деталей и удельные показатели технического уровня технологии, экономической эффективности и технического уровня детали после восстановления, на основании которых и осуществляется выбор технологии.
2 Разработать план технологических операций по восстановлению детали
2.1 Исходные данные
Операция 015. Наплавка
ГОСТ 4543-71.
Деталь - вал ведущий коробки передач
Материал – Сталь 30 ХГТ
Твердость - 59.65 НRCэ
Способ установления дефекта и средства контроля:
Калибр ролики Штангенциркуль Радиусные шаблоны