Файл: Курсовой проект, 56 л., 6 рис., 25 табл., 11 источников нефтяной кокс, реактор, коксонагреватель, тяжелые нефтяные остатки, гудрон.docx
ВУЗ: Не указан
Категория: Не указан
Дисциплина: Не указана
Добавлен: 11.04.2024
Просмотров: 37
Скачиваний: 0
ВНИМАНИЕ! Если данный файл нарушает Ваши авторские права, то обязательно сообщите нам.
, выделяющаяся в газовую фазу.
Уплотнение аренов протекают по цепному механизму. Например:
С6Н5 + С6Н6 С6Н5-С6Н5 + Н (1.20)
С6Н6 + НС6Н5 + Н2 (1.21)
Образовавшиеся свободные радикалы Н и фенильные взаимодействуют с молекулами ароматических углеводородов (бензола, нафталина, антрацена и т.п.) с образованием других ароматических радикалов, рекомбинация которых приводит к накоплению конденсированных молекул.
Постепенное увеличение молекулярной массы, повышение содержания углерода и потерю водорода в результате конденсации ароматических структур можно изобразить следующим образом (на примере нафталина):
Эти реакции приводят к образованию кокса.
Ниже кратко рассмотрим исходные сырье, условия протекания и полученные продукты процессов коксования [3].
1.3 Основные технологические параметры процесса
Основными параметрами термокантактного коксования являются температура, определяемое объёмной скоростью.
Температура.
В интервале температур 470-580 °С образование бензиновых и дизельных фракций протекает достаточно быстро. С ростом температуры увеличивается и степень превращения сырья. Повышение температуры до 480--500 °С ведет к усилению газо- и коксообразования и к снижению выхода бензина. Октановое число бензина возрастает.
Влияние давления.
Давление не влияет на скорость процесса, так как жидкость практически несжимаема и изменение концентрации реагирующих в ней молекул за счет изменения давления не происходит.
Термокантактное коксование проводится при температуре 470-550°С и давлении от 2 до 7 МПа. В этих условиях такие виды сырья, как бензин (имеющий критическую температуру 300°С), лигроин (примерно 350°С), керосин (примерно 410°С), газойль (примерно 475°С) и кроме того продукты реакции: газ, крекинг-бензин, крекинг-керосин и другие, имеющие низкую критическую температуру, находятся в зоне реакции в парообразном или газообразном состоянии. Часть указанных продуктов может находиться в жидкости в растворенном состоянии, но другая (большая) часть будет в газообразном и парообразном состоянии.
В зоне реакции коксования протекают и реакции уплотнения, которые зависят от давления. Увеличение давления способствует также сохранению большой доли сырья в змеевике печи в жидком состоянии. Это также способствует улучшению теплопередачи и снижению возможности местных перегревов. Повышение давления при термическом крекинге способствует уменьшению содержания непредельных углеводородов в крекинг-бензине и особенно в газе.
Тепловой эффект.
Тепловой эффект является суммой тепловых эффектов отдельных реакций процесса и зависит от степени превращения. При степени превращения 80--90 % отрицательный тепловой эффект реакции 230--290 кДж на 1 кг сырья.Объемная скорость обычно составляет от 1,5 ч-1 [ 2].
1.4 Аппаратурное оформление процесса
Для ведение процесса термокаталитического коксования необходимо аппаратурное оформление, которое позволило бы непрерывно выводить образующийся кокс из реактора. Идея непрерывного вывода кокса привела к разработке реактора с псевдоожиженным слоем кокса, выводимого в виде порошка.
Процесс непрерывного коксования идет более интенсивно, так как большая поверхность порошкообразного теплоносителя способствует улучшению контакта фаз. Хорошая летучесть такого теплоносителя дает возможность перемещения больших его масс по стоякам и создания установок большой мощности (1,8-3,0 млн. т/год по сырью).
В реакторном блоке в качестве теплоносителя циркулируют коксовые частицы, которые в результате контакта с сырьем покрываются тонким слоем вновь образующегося кокса. Некоторое количество частиц, наиболее укрупненных за счет многократного «обрастания», непрерывно выводят из системы.
При коксовании минимальная кратность циркуляции теплоносителя должна быть такой, чтобы предотвратить слипание частиц теплоносителя при контакте с сырьем.
Теплоноситель, в качестве которого обычно применяется кокс, представляет собой порошок из частиц округлой формы диаметром 0,075-0,3 мм. Он непрерывно циркулирует через систему реактор 1 - коксонагреватель 2. Оба аппарата работают в режиме «кипящего слоя». Псевдоожижение слоя кокса-теплоносителя в реакторе происходит за счет подачи в низ аппарата водяного пара, а также паров и газов, образующихся в процессе коксования. В коксонагревателе 2 псевдоожижение достигается подачей воздуха, при этом часть кокса сгорает, а остальная его масса нагревается до 600-620 °С.
Реактор коксования представляет собой аппарат сложной конструкции с переменным сечением
А-А - границы уровня слоя; 1- зоны паровой фазы; 2- переходный конус;
3,4 - зона кипящего слоя; 5- отпарная секция;
6- циклоны;7- скруббер
Рисунок 1.1 ‒ Реактор коксования с порошкообразным коксом
Псевдоожиженный слой кокса размещается в конической 4 и цилиндрической 3 частях аппарата. Нижняя коническая часть аппарата служит для уменьшения расхода пара на псевдоожижение слоя. Внизу аппарата имеется отпарная секция 5, куда подается водяной пар для отпарки от кокса углеводородов. В отпарной секции для увеличения пути кокса располагаются полки.
Сужение верхней части реактора обеспечивает увеличение скорости паров над слоем, что позволяет снизить реакции вторичного разложения паров, повысить концентрацию кокса в парах, который механически воздействует на устья циклонов и предотвращает их закоксовывание. Реактор изнутри футерован торкретбетоном толщиной 200 мм. Коксопроводы установки имеют диаметр примерно 1 м, для предохранения от эррозии их подобно аппаратам реакторного блока футеруют изнутри торкретбетоном. Для улавливания коксовой пыли на верху реактора устанавливаются двухступенчатые циклонные сепараторы, откуда пары реакции поступают в скруббер 7.
1- распределительная решетка;2- сливной колодец; 3-циклон;
4- линия ввода кокса; 5- сборная камера и вывод дымовых газов;
6- кипящий слой
Рисунок 1.2 ‒ Коксонагреватель
Коксонагреватель проще по конструкции. Псевдоожиженный слой созда-ется подачей воздуха (в период пуска нагретого в топке под давлением) под распределительную решетку 1. Во время разогрева кокснепрерывно циркулирует между коксонагревателем и реактором через линии пневмотранспорта для того, чтобы желаемую температуру приобрела вся масса кокса. Для сокращения продолжительности разогрева кокса служат форсунки жидкого топлива, размещенные изнутри по окружности аппарата.
После предварительного разогрева системы с помощью топки под давлением зажигают эти форсунки, и разогрев продолжают до тех пор, пока не будет достигнута температура самовоспламенения кокса. После этого температура слоя в коксонагревателе начнет быстро возрастать, и расход топлива со стороны станет излишним. При сгорании кокса наряду с СО2 образуется продукт неполного окисления - СО. В условиях коксонагревателя возможно догорание его в СО2, сопровождающееся значительным выделением тепла. Для снижения температуры на верху коксонагревателя предусмотрена подача пара, а также впрыск парового конденсата. Кокс циркулирует между реактором и коксонагревателем по U-образным линиям пневмотранспорта. Транспортирующим агентом служит водяной пар. Для улавливания коксовой пыли используют двухступенчатые циклоны 3, после которых дымовые газы поступают в котел-утилизатор [ 2].
2 Выбор и обоснование технологии осуществления процесса
Непрерывное коксование в кипящем слое кокса-теплоносителя нацелено на максимальный выход дистиллятов из низкокачественных остатков. Поскольку в кокс переходят практически все металлы исходного сырья, а также сера и другие гетероатомы, кокс в этом случае является побочным продуктом.
При сопоставлении выходов продуктов замедленного и непрерывного способа коксования видно, что при значительно меньшей выходе кокса при коксовании в кипящем слое процесс; позволяет практически весь кокс в топливный газ.
Большим достоинством непрерывного коксования является возможность вести процесс на установках высокой мощности с пропускной способностью по сырью до 7 и более тыс. т в сутки (более 2 млн т в год).Установки ежедневно выдают до 1600 т порошкообразного кокса. При этом габариты аппаратов реакторного блока для такой установки невелики: внутренний диаметр реактора - 8,9 м, а нагревателя - 13,7 м. Наивысшая точка установки расположена на высоте 76 м от уровня земли. Избыточное тепло продуктов сгорания кокса используют в мощном котле-утилизаторе, где получают до 200 т в час пара высокого давления. Сама установка расходует вдвое меньше пара, чем производит. Отходящие из коксонагревателя газы обычно направляются в СО-бойлер для утилизации тепла с целью выработки электроэнергии. Схема такой установки приведена на рисунке 2.1.
Большим достоинством технологии непрерывного коксования в кипящем слое коксовых частиц является также возможность удовлетворения потребности в технологическом тепле за счет сжигания собственного кокса (что устраняет необходимость во внешних источниках топлива), а также довольно простая процедура выгрузки кокса из системы (в отличие от установок замедленного коксования).
Дальнейшим развитием технологии явилось добавление процесса термокантактного коксования процесс, который позволяет почти полностью превратить низкокачественные тяжелые остатки в газ и дистиллятные продукты.
Металлы сырья концентрируются в мелких частицах получаемого кокса и извлекаются. Технология получения ценных металлов (ванадий, никель) из золы кокса освоена в некоторых странах (Канаде, США, Венесуэле). При содержании ванадия в сырье 200 мг/кг его концентрация в коксе
Потоки: I - сырье; II - продукты в колонну вторичной перегонки
Уплотнение аренов протекают по цепному механизму. Например:
С6Н5 + С6Н6 С6Н5-С6Н5 + Н (1.20)
С6Н6 + НС6Н5 + Н2 (1.21)
Образовавшиеся свободные радикалы Н и фенильные взаимодействуют с молекулами ароматических углеводородов (бензола, нафталина, антрацена и т.п.) с образованием других ароматических радикалов, рекомбинация которых приводит к накоплению конденсированных молекул.
Постепенное увеличение молекулярной массы, повышение содержания углерода и потерю водорода в результате конденсации ароматических структур можно изобразить следующим образом (на примере нафталина):
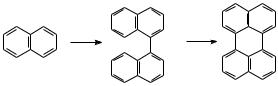
нафталин | динафтил | перилен |
Эти реакции приводят к образованию кокса.
Ниже кратко рассмотрим исходные сырье, условия протекания и полученные продукты процессов коксования [3].
1.3 Основные технологические параметры процесса
Основными параметрами термокантактного коксования являются температура, определяемое объёмной скоростью.
Температура.
В интервале температур 470-580 °С образование бензиновых и дизельных фракций протекает достаточно быстро. С ростом температуры увеличивается и степень превращения сырья. Повышение температуры до 480--500 °С ведет к усилению газо- и коксообразования и к снижению выхода бензина. Октановое число бензина возрастает.
Влияние давления.
Давление не влияет на скорость процесса, так как жидкость практически несжимаема и изменение концентрации реагирующих в ней молекул за счет изменения давления не происходит.
Термокантактное коксование проводится при температуре 470-550°С и давлении от 2 до 7 МПа. В этих условиях такие виды сырья, как бензин (имеющий критическую температуру 300°С), лигроин (примерно 350°С), керосин (примерно 410°С), газойль (примерно 475°С) и кроме того продукты реакции: газ, крекинг-бензин, крекинг-керосин и другие, имеющие низкую критическую температуру, находятся в зоне реакции в парообразном или газообразном состоянии. Часть указанных продуктов может находиться в жидкости в растворенном состоянии, но другая (большая) часть будет в газообразном и парообразном состоянии.
В зоне реакции коксования протекают и реакции уплотнения, которые зависят от давления. Увеличение давления способствует также сохранению большой доли сырья в змеевике печи в жидком состоянии. Это также способствует улучшению теплопередачи и снижению возможности местных перегревов. Повышение давления при термическом крекинге способствует уменьшению содержания непредельных углеводородов в крекинг-бензине и особенно в газе.
Тепловой эффект.
Тепловой эффект является суммой тепловых эффектов отдельных реакций процесса и зависит от степени превращения. При степени превращения 80--90 % отрицательный тепловой эффект реакции 230--290 кДж на 1 кг сырья.Объемная скорость обычно составляет от 1,5 ч-1 [ 2].
1.4 Аппаратурное оформление процесса
Для ведение процесса термокаталитического коксования необходимо аппаратурное оформление, которое позволило бы непрерывно выводить образующийся кокс из реактора. Идея непрерывного вывода кокса привела к разработке реактора с псевдоожиженным слоем кокса, выводимого в виде порошка.
Процесс непрерывного коксования идет более интенсивно, так как большая поверхность порошкообразного теплоносителя способствует улучшению контакта фаз. Хорошая летучесть такого теплоносителя дает возможность перемещения больших его масс по стоякам и создания установок большой мощности (1,8-3,0 млн. т/год по сырью).
В реакторном блоке в качестве теплоносителя циркулируют коксовые частицы, которые в результате контакта с сырьем покрываются тонким слоем вновь образующегося кокса. Некоторое количество частиц, наиболее укрупненных за счет многократного «обрастания», непрерывно выводят из системы.
При коксовании минимальная кратность циркуляции теплоносителя должна быть такой, чтобы предотвратить слипание частиц теплоносителя при контакте с сырьем.
Теплоноситель, в качестве которого обычно применяется кокс, представляет собой порошок из частиц округлой формы диаметром 0,075-0,3 мм. Он непрерывно циркулирует через систему реактор 1 - коксонагреватель 2. Оба аппарата работают в режиме «кипящего слоя». Псевдоожижение слоя кокса-теплоносителя в реакторе происходит за счет подачи в низ аппарата водяного пара, а также паров и газов, образующихся в процессе коксования. В коксонагревателе 2 псевдоожижение достигается подачей воздуха, при этом часть кокса сгорает, а остальная его масса нагревается до 600-620 °С.
Реактор коксования представляет собой аппарат сложной конструкции с переменным сечением
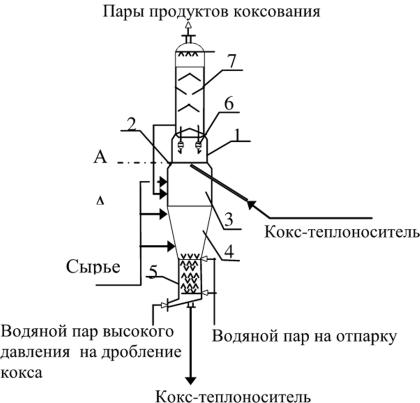
А-А - границы уровня слоя; 1- зоны паровой фазы; 2- переходный конус;
3,4 - зона кипящего слоя; 5- отпарная секция;
6- циклоны;7- скруббер
Рисунок 1.1 ‒ Реактор коксования с порошкообразным коксом
Псевдоожиженный слой кокса размещается в конической 4 и цилиндрической 3 частях аппарата. Нижняя коническая часть аппарата служит для уменьшения расхода пара на псевдоожижение слоя. Внизу аппарата имеется отпарная секция 5, куда подается водяной пар для отпарки от кокса углеводородов. В отпарной секции для увеличения пути кокса располагаются полки.
Сужение верхней части реактора обеспечивает увеличение скорости паров над слоем, что позволяет снизить реакции вторичного разложения паров, повысить концентрацию кокса в парах, который механически воздействует на устья циклонов и предотвращает их закоксовывание. Реактор изнутри футерован торкретбетоном толщиной 200 мм. Коксопроводы установки имеют диаметр примерно 1 м, для предохранения от эррозии их подобно аппаратам реакторного блока футеруют изнутри торкретбетоном. Для улавливания коксовой пыли на верху реактора устанавливаются двухступенчатые циклонные сепараторы, откуда пары реакции поступают в скруббер 7.
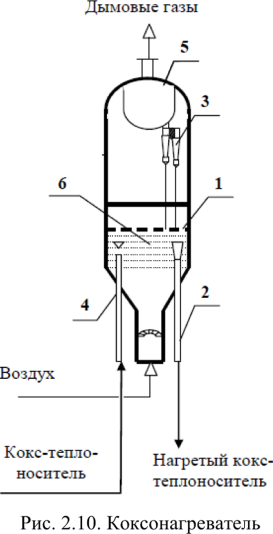
1- распределительная решетка;2- сливной колодец; 3-циклон;
4- линия ввода кокса; 5- сборная камера и вывод дымовых газов;
6- кипящий слой
Рисунок 1.2 ‒ Коксонагреватель
Коксонагреватель проще по конструкции. Псевдоожиженный слой созда-ется подачей воздуха (в период пуска нагретого в топке под давлением) под распределительную решетку 1. Во время разогрева кокснепрерывно циркулирует между коксонагревателем и реактором через линии пневмотранспорта для того, чтобы желаемую температуру приобрела вся масса кокса. Для сокращения продолжительности разогрева кокса служат форсунки жидкого топлива, размещенные изнутри по окружности аппарата.
После предварительного разогрева системы с помощью топки под давлением зажигают эти форсунки, и разогрев продолжают до тех пор, пока не будет достигнута температура самовоспламенения кокса. После этого температура слоя в коксонагревателе начнет быстро возрастать, и расход топлива со стороны станет излишним. При сгорании кокса наряду с СО2 образуется продукт неполного окисления - СО. В условиях коксонагревателя возможно догорание его в СО2, сопровождающееся значительным выделением тепла. Для снижения температуры на верху коксонагревателя предусмотрена подача пара, а также впрыск парового конденсата. Кокс циркулирует между реактором и коксонагревателем по U-образным линиям пневмотранспорта. Транспортирующим агентом служит водяной пар. Для улавливания коксовой пыли используют двухступенчатые циклоны 3, после которых дымовые газы поступают в котел-утилизатор [ 2].
2 Выбор и обоснование технологии осуществления процесса
Непрерывное коксование в кипящем слое кокса-теплоносителя нацелено на максимальный выход дистиллятов из низкокачественных остатков. Поскольку в кокс переходят практически все металлы исходного сырья, а также сера и другие гетероатомы, кокс в этом случае является побочным продуктом.
При сопоставлении выходов продуктов замедленного и непрерывного способа коксования видно, что при значительно меньшей выходе кокса при коксовании в кипящем слое процесс; позволяет практически весь кокс в топливный газ.
Большим достоинством непрерывного коксования является возможность вести процесс на установках высокой мощности с пропускной способностью по сырью до 7 и более тыс. т в сутки (более 2 млн т в год).Установки ежедневно выдают до 1600 т порошкообразного кокса. При этом габариты аппаратов реакторного блока для такой установки невелики: внутренний диаметр реактора - 8,9 м, а нагревателя - 13,7 м. Наивысшая точка установки расположена на высоте 76 м от уровня земли. Избыточное тепло продуктов сгорания кокса используют в мощном котле-утилизаторе, где получают до 200 т в час пара высокого давления. Сама установка расходует вдвое меньше пара, чем производит. Отходящие из коксонагревателя газы обычно направляются в СО-бойлер для утилизации тепла с целью выработки электроэнергии. Схема такой установки приведена на рисунке 2.1.
Большим достоинством технологии непрерывного коксования в кипящем слое коксовых частиц является также возможность удовлетворения потребности в технологическом тепле за счет сжигания собственного кокса (что устраняет необходимость во внешних источниках топлива), а также довольно простая процедура выгрузки кокса из системы (в отличие от установок замедленного коксования).
Дальнейшим развитием технологии явилось добавление процесса термокантактного коксования процесс, который позволяет почти полностью превратить низкокачественные тяжелые остатки в газ и дистиллятные продукты.
Металлы сырья концентрируются в мелких частицах получаемого кокса и извлекаются. Технология получения ценных металлов (ванадий, никель) из золы кокса освоена в некоторых странах (Канаде, США, Венесуэле). При содержании ванадия в сырье 200 мг/кг его концентрация в коксе
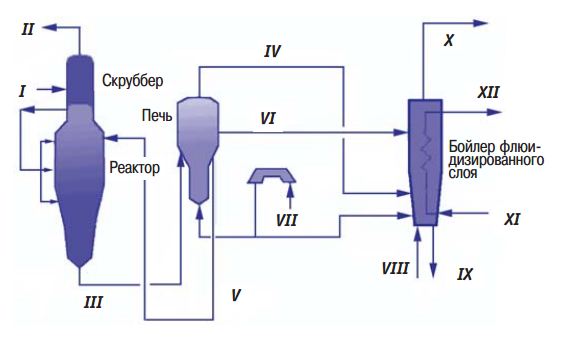
Потоки: I - сырье; II - продукты в колонну вторичной перегонки