Файл: Курсовой проект, 56 л., 6 рис., 25 табл., 11 источников нефтяной кокс, реактор, коксонагреватель, тяжелые нефтяные остатки, гудрон.docx
ВУЗ: Не указан
Категория: Не указан
Дисциплина: Не указана
Добавлен: 11.04.2024
Просмотров: 35
Скачиваний: 0
ВНИМАНИЕ! Если данный файл нарушает Ваши авторские права, то обязательно сообщите нам.
; III - холодный кокс; IV- пары исходного продукта; V - горячий кокс; VI - кокс; VII - воздух; VIII - известняк; IX - гипс; X - печной газ; XI - котловая вода; XII - пар на электростанцию
Рисунок 2.1 ‒ Схема непрерывного коксования с интегрированным бойлером для выработки электроэнергии (привлекательный вариант использования кокса в качестве топлива)
Таблица 2.1 ‒ Сравнение выхода продуктов различных способов коксования
При термоконтактном коксовании, кроме газов газификации получают:
- большое количество топливных дистиллятов, которые становятся высококачественными компонентами моторного топлива после последующего процесса каталитического облагораживания.
- топливный газ, технологично поддающийся сероочистке, а не высокосернистый пылевидныйо кокс.
Блок коксования состоит из реактора, нагревателя кокса и фракционирующего оборудования.
В ходе техпроцесса горячее сырье (нефтяные остатки, вакуумный остаток) подается в реактор с кипящим слоем циркулирующего коксового теплоносителя, где происходит термический крекинг и образуются пары продуктов реакции и кокс.
Нагрев и крекинг сырья происходят в тонком слое на поверхности кокса.
Затем производится обеспыливание продуктов реакций в циклонных сепараторах и разделение в парциальном конденсаторе на целевые продукты (выкипают до 500-560 °С). Продукты термической деструкции (жидкие и газообразные продукты коксования сырья) отводят из реактора сверху, затем происходит закалочное охлаждение в скруббере, где улавливают механические частицы кокса.Тяжелые фракции коксования после конденсации возвращают в реактор, как циркулирующий поток, вместе с остаточной коксовой пылью и мелочью.Избыток газифицируется воздухом и паром.Более легкие фракции выводят с верха скруббера и направляют на фракционирование. Между реактором и коксонагревателем организуется циркуляция кокса с целью подвода тепла в реактор.
Принципиальная схема установки приведена на рисунке 2.2.
Сырье, предварительно нагретое в теплообменнике до температуры 300…3500 С, через встроенные по периметру реактора форсунки подается в реактор 1. На крупных установках в реакторе предусматривается до 100 форсунок. В реактор 1 из коксонагревателя 3 подаются частицы теплоносителя с температурой 620…650 0С. В реакторе процесс протекает в режиме псевдоожиженния, средняя температура составляет 510-520 0С, выделяют три стадии: нагрев и испарение; крекинг; уплотнение.
При контакте сырья с частицами теплоносителя происходит его частичное испарение. В жидкой фазе на поверхности теплоносителя протекает реакция уплотнения. В результате чего на частице кокса образуется новая коксовая корочка. В паровой фазе в основном протекают реакции распада. Парообразные продукты проходят через циклоны и поступают в абсорбер 2, который орошается флегмой (кубовым продуктом колонны 6) – самой тяжелой частью продуктов блока фракционирования. В абсорбере происходит конденсация тяжелой части газообразных продуктов, и испарение легкой части флегмы. Сконденсированные продукты в качестве рециркулята (непревращенной части сырье) возвращаются в реактор. После абсорбера парообразные продукты поступают в ректификационную колонну 6, являясь одновременно горячим орошением этой колонны. На блоке фракционирования выделяют фракции: газ (сверху колонны 11), стабильный бензин (снизу колонны 11), легкий газойль (через отпарную колонну), тяжелый газойль (снизу колонны 6).
Частицы кокса в реакторе под собственным весом попадают в отпарную зону реактора. С целью десорбции с поверхности кокса адсорбированных жидких и газообразных углеводородов им навстречу подают водяной пар.
После десорбции частицы кокса пневмотранспортом транспортируют в коксонагреватель 3. Там нагрев кокса происходит также в псевдожиженном слое с подачей горячего воздуха, нагретого в топке 4. Балансовое количество кокса из коксонагревателя поступает в холодильник-классификатор 5 (происходит классификация по размеру частиц). Крупная фракция выводится как товарный продукт снизу классификатора. Мелкая фракция возвращается в коксонагреватель. Нагретые частицы из коксонагревателя направляются в реактор. Дымовые газы из коксонагревателя 3 проходят сдвоенные циклоны, систему очистки, котлы-утилизаторы (12) и выбрасываются в атмосферу через дымовую трубу 13.
Реактор коксования представляет собой аппарат сложной конструкции и переменного сечения. Псевдоожиженный слой кокса размещен в конической и цилиндрической части аппарата. Коническая форма способствует уменьшению расхода пара на псевдоожижение. Внизу имеется отпарная секция, в нее подают снизу водяной пар для отпаривания порошкообразного кокса-теплоносителя от углеводородных продуктов коксования. Верхняя часть реактора имеет суженное сечение, верхняя часть заполнена парами продуктов коксования, содержащими некоторое количество коксовых частиц, удаление которых происходит в циклонах. Сужение верхней части реактора обуславливает увеличение скорости паров над слоем, что позволяет уменьшить вторичные реакции разложения, повысить концентрацию частиц в парах, предотвращается закоксовывание циклонов.
1 - парциальный конденсатор (скруббер); 2-реактор; 3 - коксонагреватель;
4 - топка; 5 - вепаратор-холодильник кокса; 6 - ректификационная колонна;
7 - конденсатор; 8 - компрессор; 9 - холодильник; 10 - газосепаратор;
11 - стабилизатор; 12- отпарная колонна; 13 - котел-утилизатор.
Рисунок 2.2 ‒ Принципиальная схема установки термоконтактного коксования
3 Характеристика качества целевых продуктов, катализаторов, побочных продуктов
Характеристика качество исходного сырья, целевых продуктов, катализаторов, приведены в таблице 3.1.
Таблица 3.1 - Характеристика качество исходного сырья, целевых продуктов, катализаторов
4 Технологические расчеты процесса и основных аппаратов
Исходные данные:
- производительность установки по сырью равна 1 000 000 т в год;
- установка работает 330 дней в году;
- кратность циркуляции коксового теплоносителя равна 8;
- плотность кипящего слоя – 450 кг/м3.
Принимаем следующие параметры работы реактора установки термоконтактного коксования:
- температура в слое 530 °С;
- абсолютное давление над слоем 0,18 МПа;
- расход пара на отпарку кокса 0,2% на циркулирующий кокс;
-кратность циркуляции кокса 7,0;
- продолжительность пребывания кокса в реакторе 7 мин;
- скорость движения паров над слоем кокса 0,5 м/с.
4.1 Материальный баланс
Расчет материального баланса начинаем с анализа действующих установок. Массовые выходы продуктов установки термоконтактного коксования, принимаем из средних выходов действующих установок. Рассчитываем массовые выходы продуктов для заданной мощности.
Рисунок 2.1 ‒ Схема непрерывного коксования с интегрированным бойлером для выработки электроэнергии (привлекательный вариант использования кокса в качестве топлива)
Таблица 2.1 ‒ Сравнение выхода продуктов различных способов коксования
Выход, % масс. | Замедленное коксование | Термокантактное коксование | Коксования с паром |
Газ | 9,2 | 11,8 | 11,8 |
Бензин | 13,1 | 11,5 | 11,5 |
Легкий газойль | 29,3 | 14,5 | 14,5 |
Тяжелый газойль | 15,1 | 32,1 | 32,1 |
Кокс | 33,3 | 23,7 | 0,8 |
Топливный газ | - | - | 19,3 |
При термоконтактном коксовании, кроме газов газификации получают:
- большое количество топливных дистиллятов, которые становятся высококачественными компонентами моторного топлива после последующего процесса каталитического облагораживания.
- топливный газ, технологично поддающийся сероочистке, а не высокосернистый пылевидныйо кокс.
Блок коксования состоит из реактора, нагревателя кокса и фракционирующего оборудования.
В ходе техпроцесса горячее сырье (нефтяные остатки, вакуумный остаток) подается в реактор с кипящим слоем циркулирующего коксового теплоносителя, где происходит термический крекинг и образуются пары продуктов реакции и кокс.
Нагрев и крекинг сырья происходят в тонком слое на поверхности кокса.
Затем производится обеспыливание продуктов реакций в циклонных сепараторах и разделение в парциальном конденсаторе на целевые продукты (выкипают до 500-560 °С). Продукты термической деструкции (жидкие и газообразные продукты коксования сырья) отводят из реактора сверху, затем происходит закалочное охлаждение в скруббере, где улавливают механические частицы кокса.Тяжелые фракции коксования после конденсации возвращают в реактор, как циркулирующий поток, вместе с остаточной коксовой пылью и мелочью.Избыток газифицируется воздухом и паром.Более легкие фракции выводят с верха скруббера и направляют на фракционирование. Между реактором и коксонагревателем организуется циркуляция кокса с целью подвода тепла в реактор.
Принципиальная схема установки приведена на рисунке 2.2.
Сырье, предварительно нагретое в теплообменнике до температуры 300…3500 С, через встроенные по периметру реактора форсунки подается в реактор 1. На крупных установках в реакторе предусматривается до 100 форсунок. В реактор 1 из коксонагревателя 3 подаются частицы теплоносителя с температурой 620…650 0С. В реакторе процесс протекает в режиме псевдоожиженния, средняя температура составляет 510-520 0С, выделяют три стадии: нагрев и испарение; крекинг; уплотнение.
При контакте сырья с частицами теплоносителя происходит его частичное испарение. В жидкой фазе на поверхности теплоносителя протекает реакция уплотнения. В результате чего на частице кокса образуется новая коксовая корочка. В паровой фазе в основном протекают реакции распада. Парообразные продукты проходят через циклоны и поступают в абсорбер 2, который орошается флегмой (кубовым продуктом колонны 6) – самой тяжелой частью продуктов блока фракционирования. В абсорбере происходит конденсация тяжелой части газообразных продуктов, и испарение легкой части флегмы. Сконденсированные продукты в качестве рециркулята (непревращенной части сырье) возвращаются в реактор. После абсорбера парообразные продукты поступают в ректификационную колонну 6, являясь одновременно горячим орошением этой колонны. На блоке фракционирования выделяют фракции: газ (сверху колонны 11), стабильный бензин (снизу колонны 11), легкий газойль (через отпарную колонну), тяжелый газойль (снизу колонны 6).
Частицы кокса в реакторе под собственным весом попадают в отпарную зону реактора. С целью десорбции с поверхности кокса адсорбированных жидких и газообразных углеводородов им навстречу подают водяной пар.
После десорбции частицы кокса пневмотранспортом транспортируют в коксонагреватель 3. Там нагрев кокса происходит также в псевдожиженном слое с подачей горячего воздуха, нагретого в топке 4. Балансовое количество кокса из коксонагревателя поступает в холодильник-классификатор 5 (происходит классификация по размеру частиц). Крупная фракция выводится как товарный продукт снизу классификатора. Мелкая фракция возвращается в коксонагреватель. Нагретые частицы из коксонагревателя направляются в реактор. Дымовые газы из коксонагревателя 3 проходят сдвоенные циклоны, систему очистки, котлы-утилизаторы (12) и выбрасываются в атмосферу через дымовую трубу 13.
Реактор коксования представляет собой аппарат сложной конструкции и переменного сечения. Псевдоожиженный слой кокса размещен в конической и цилиндрической части аппарата. Коническая форма способствует уменьшению расхода пара на псевдоожижение. Внизу имеется отпарная секция, в нее подают снизу водяной пар для отпаривания порошкообразного кокса-теплоносителя от углеводородных продуктов коксования. Верхняя часть реактора имеет суженное сечение, верхняя часть заполнена парами продуктов коксования, содержащими некоторое количество коксовых частиц, удаление которых происходит в циклонах. Сужение верхней части реактора обуславливает увеличение скорости паров над слоем, что позволяет уменьшить вторичные реакции разложения, повысить концентрацию частиц в парах, предотвращается закоксовывание циклонов.
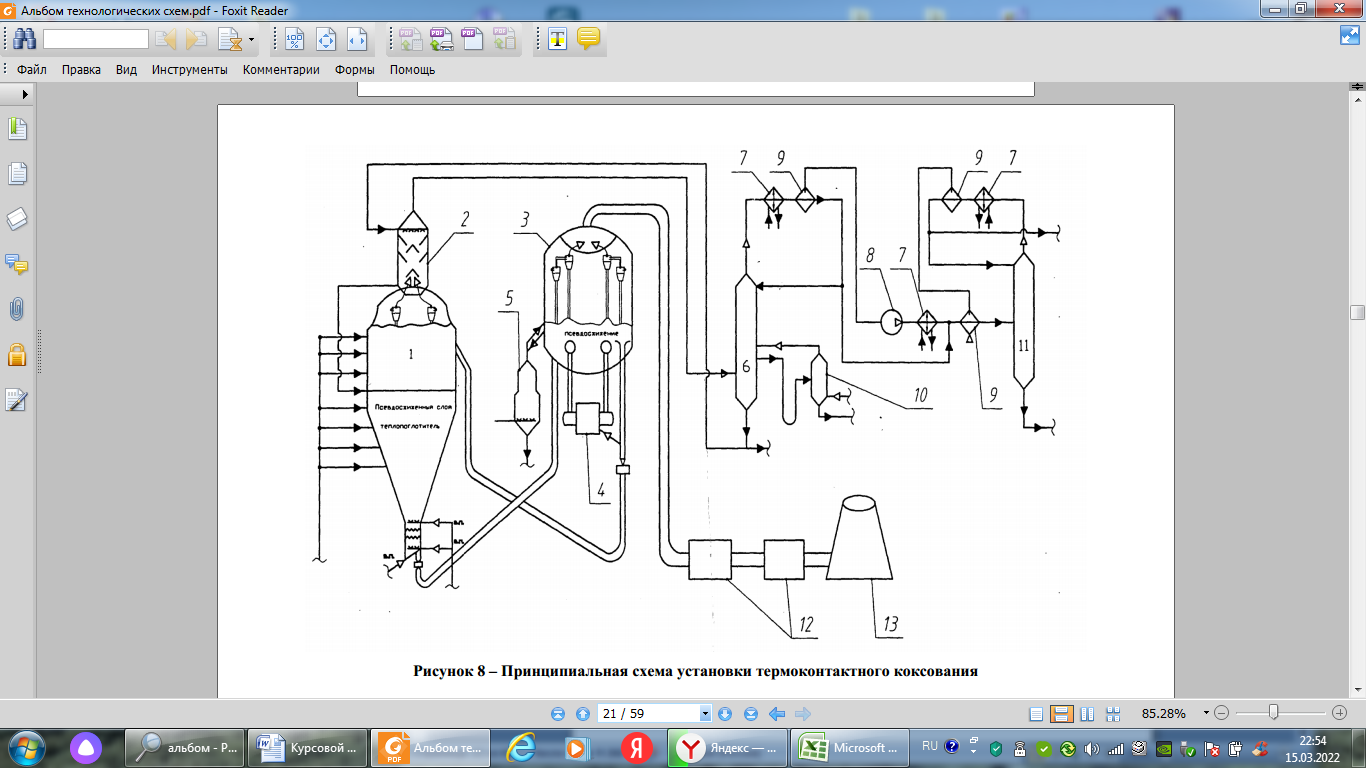
1 - парциальный конденсатор (скруббер); 2-реактор; 3 - коксонагреватель;
4 - топка; 5 - вепаратор-холодильник кокса; 6 - ректификационная колонна;
7 - конденсатор; 8 - компрессор; 9 - холодильник; 10 - газосепаратор;
11 - стабилизатор; 12- отпарная колонна; 13 - котел-утилизатор.
Рисунок 2.2 ‒ Принципиальная схема установки термоконтактного коксования
3 Характеристика качества целевых продуктов, катализаторов, побочных продуктов
Характеристика качество исходного сырья, целевых продуктов, катализаторов, приведены в таблице 3.1.
Таблица 3.1 - Характеристика качество исходного сырья, целевых продуктов, катализаторов
| № п/п | Наименование сырья, материалов реагентов, катализаторов, полуфабрикатов, готовой продукции | Номер государственного или отраслевого стандарта, технических условий, стандарта предприятия | Показатели качества, подлежащие проверке | Норма по нормативному документу | Область применения готовой продукции | ||||
| 1 | 2 | 3 | 4 | 5 | 6 | ||||
| Сырье | |||||||||
| 2 | Гудрон | | Плотность при 20 ºС, г/см3 | 1,03 | Сырье для производства кокса | ||||
| Коксуемость, % масс. | До 16,2 | ||||||||
| Содержание, % масс. - серы | До 3,34 | ||||||||
| Фракционный состав: - до 400 ºС выкипает, % масс. - до 500 ºС выкипает, % масс | 29 | ||||||||
| Получаемые продукты: | |||||||||
| 3 | Жирный газ коксования | | -Н2S % масс. -∑С5 % масс.и выше, % масс. | До 10,62 14,24 | На получение пропан-пропиленовой и бутан-бутиленовой фракции | ||||
4 | Нестабильный бензин | | - конец кипения, не выше, ºС | 180 | На установку гидроочистки, как компонент бензина | |||||
1 | 2 | 3 | 4 | 5 | 6 | |||||
5 | Легкий газойль | | Фракционный состав: - 50 % выкипает при температуре, ºС, не выше | 28 | На установку гидроочистки, как компонент дизельного топлива | |||||
- 96 % выкипает при температуре, ºС, не выше | 360 | |||||||||
Массовая доля серы, % масс. | Не нормируется | |||||||||
Плотность при 20 ºС, кг/м³ | 880 | |||||||||
Температура вспышки, определяемая в закрытом тигле, ºС, не ниже | 30 | |||||||||
Йодное число | Не нормируется | |||||||||
6 | Тяжелый газойль | | Температура вспышки, определяемая в закрытом тигле, ºС, не ниже | 110 | Как компонент моторного и котельного топлива | |||||
| | |||||||||
Массовая доля серы, % масс. | Не нормируется | |||||||||
Коксуемость по Кондрансону, % масс. | Не нормируется | |||||||||
Плотность при 20 ºС, кг/м3 | 960 | |||||||||
7 | Кокс | ТУ 0258-004-05766540-2008 | Массовая доля общей влаги, %, не более | 3,0 не является браковочным показателем и служит для расчета с потребителями | Для использования в алюминевой промышленности, для сжигания в топках котлов электростанций и специально оборудованных котельных | |||||
Зольность, %, не более | 1,0 | |||||||||
Массовая доля серы, %, не более | 5,0 | |||||||||
Массовая доля летучих веществ, %, не более | 10 |
4 Технологические расчеты процесса и основных аппаратов
Исходные данные:
- производительность установки по сырью равна 1 000 000 т в год;
- установка работает 330 дней в году;
- кратность циркуляции коксового теплоносителя равна 8;
- плотность кипящего слоя – 450 кг/м3.
Принимаем следующие параметры работы реактора установки термоконтактного коксования:
- температура в слое 530 °С;
- абсолютное давление над слоем 0,18 МПа;
- расход пара на отпарку кокса 0,2% на циркулирующий кокс;
-кратность циркуляции кокса 7,0;
- продолжительность пребывания кокса в реакторе 7 мин;
- скорость движения паров над слоем кокса 0,5 м/с.
4.1 Материальный баланс
Расчет материального баланса начинаем с анализа действующих установок. Массовые выходы продуктов установки термоконтактного коксования, принимаем из средних выходов действующих установок. Рассчитываем массовые выходы продуктов для заданной мощности.
Показатель | Расход | |||||
% | т/год | т/сутки | кг/час | кг/сек | ||
Сырье | ||||||
Гудрон | 98,43 | 1000000,00 | 3030,30 | 126262,63 | 35,07 | |
Водяной пар | 1,57 | 15950,42 | 48,33 | 2013,94 | 0,56 | |
Итого | 1000 | 1015950,42 | 3078,64 | 128276,57 | 35,63 | |
Продукты | ||||||
Сухой газ | 4,92 | 49984,76 | 151,47 | 6311,21 | 1,75 | |
Жирный газ | 12,8 | 130041,65 | 394,07 | 16419,40 | 4,56 | |
Стабильный бензин | 17,72 | 180026,41 | 545,53 | 22730,61 | 6,31 | |
Легкий газойль | 19,69 | 200040,64 | 606,18 | 25257,66 | 7,02 | |
Тяжелый газойль | 24,6 | 249923,80 | 757,34 | 31556,04 | 8,77 | |
Кокс | 18,7 | 189982,73 | 575,71 | 23987,72 | 6,66 | |
Водяной пар | 1,57 | 15950,42 | 48,33 | 2013,94 | 0,56 | |
Итого | 100 | 1015950,42 | 3078,64 | 128276,57 | 35,63 |