ВУЗ: Не указан
Категория: Не указан
Дисциплина: Не указана
Добавлен: 12.04.2024
Просмотров: 8
Скачиваний: 0
ВНИМАНИЕ! Если данный файл нарушает Ваши авторские права, то обязательно сообщите нам.
min. Но в результате приработки деталей при обкатке и в начальный период работы изделия зазор в соединении увеличится, и значение/ практически будет больше 0,3.
Для этого определим наименьшую толщину масляного слоя :
hmin = (43/2)∙(1 - 0,11) = 19,135 мкм
Затем найдем запас надежности по толщине масляного слоя:
k ж.т=19,135/(1,6 + 3,2 + 2) = 2,81 > 2
Расчет показывает, что посадка по наименьшему зазору выбрана правильно, так как при Smin = 43 мкм обеспечивается жидкостное трение и создается запас надежности по толщине масляного слоя. Следовательно, табличное значение Smin = 43 мкм для выбранной посадки можно принять за SminF.
=
= 0,000978 м = 978 мкм
ψ= 0,978/160 = 0,0061
Cr = (1,16∙106∙0,00612)/(0,017∙31,4) = 80,86
χ = (80,86 + 0,964 - 0,998)/(80,86 + 0,964) = 0,988
hmin = (978/2)∙(1 - 0,969) = 9,38 мкм
k ж.т. = 5,87/(1,6 + 3,2 + 2) = 0,86 < 2
Расчеты показывают, что жидкостное трение не обеспечивается, следовательно, необходимо уменьшить функциональный зазор.
Принимаем SmaxF = 400мкм
ψ= 0,400/160 = 0,0025
Cr = (1,16∙106∙0,00252)/(0,017∙31,4) = 13,58
χ = (13,58 + 0,964 - 0,998)/(13,58 + 0,964) = 0,931
hmin = (400/2)∙(1 - 0,931) = 13,8 мкм
k ж.т. = 13,8/(1,6 + 3,2 + 2) = 2,03 > 2
Sи= (SmaxF–SminF) – (TD+ Td)== (400 - 43) - (40 + 80) = 237 мкм
Рисунок 2.1 – Схема расположения полей допусков деталей при посадке с зазором
Рассчитать и выбрать посадку с натягом для соединения вала и втулки (d = 50 мм, d1 = 20 мм, d2 = 80 мм, l =75 мм), которая работает под воздействием крутящего момента Мкр = 35 Н∙м. Запрессовка механическая. Материал обеих деталей - сталь 45.
=
=1,25∙106Па
Св =(1 + (d1/d)2)/(1 –(d1/d)2)–в = (1+(0,02/0,05)2/(1-(0,02/0,05)2)-0,3 = 1,08
СА =(1 + (d/d2)2)/(1 –(d/d2)2)+ а = (1+(0,05/0,08)2/(1-(0,05/0,08)2)+0,3 = 2,58
Nmin = pэd(Cв/Eв+ Cа/Eа) = 1,25∙106∙0,05∙((1,08/2,06∙1011) + (2,58/2,06∙1011)) = 1,11 мкм
u = 2(0,25∙10 + 0,25∙10) = 10 мкм
Принимаем ut = 0 и u4 = 0, исходя из условий задачи.
NminF = 1,11 + 10 = 11,11 мкм
рдоп1= 0,58т1(1 –(d1/d)2) = 0,58∙3,53∙108∙(1-(0,02/0,05)2)= 1,72∙108Па
рдоп2= 0,58т2(1 –(d/d2)2) = 0,58∙3,53∙108∙(1-(0,05/0,08)2)=1,25∙108Па
В качестве рдоп выбираем рдоп2 ,как наименьшее.
Nmax= pдопd((C1/E1) + (C2/E2))
Nmax = 1,25∙108∙0,05∙((1,08/2,06∙1011)+(2,58/2,06∙1011)) = 111 мкм
u =16 мкм, ut = 0, up = 0, uд = 0,78
NmaxF=Nmaxuуд+ u –ut = 111∙1 +16 = 117 мкм
Ø50H8/u8, для которой NmaxT = 109 мкм (maxF)
NminT = 31мкм (>NminF)
Определяем для выбранной посадки запас прочности соединения при сборке и при эксплуатации:
N з.э= 31 - 11 = 20 мкм
N3С = 117 - 109 = 8 мкм
Для правильно выбранной посадки запас прочности соединения при сборке N3С всегда должен быть меньше запаса прочности соединения при эксплуатации N3Э., потому что N3С нужен только в момент сборки для случая возможного снижения прочности материала деталей и увеличения силы запрессовки из-за перекоса деталей, колебания коэффициента трения и т.д.
Рисунок 3.1 – Схема расположения полей допусков деталей при посадке с натягом
Величина зазора после сборки должна быть в пределах у2(±0,06) мм. Требуется назначить допуски и предельные отклонения на составляющие размеры.
Рисунок 4.1 – Схема задания
Замыкающим звеном является зазор У2 = А0.
Строим схему размерной цепи и определяем, какие составляющие звенья будут увеличивающими и уменьшающими.
Рисунок 4.2 – Схема размерной цепи
Решение удобно расположить в виде таблицы:
Таблица 1
Записываем в колонку 1 номинальные значения составляющих звеньев. Затем в колонку 2 выписываем значения единиц допуска i из таблицы 8.7 методических указаний для всех составляющих размеров.
Полагая, что все составляющие размеры размерной цепи равноточные (способ равноточных допусков), т.е. должны выполняться по одному квалитету:
ТАi = аi∙i,
где аi – количество единиц допуска, находим среднее количество единиц допуска аср для каждого составляющего размера по формуле:
аср = ТА0/ Σ ii
Величина ТА0 задана по условиям задачи.
Таким образом, аср = 120/4,92 = 24,4 единиц.
Затем находим по таблице 8.8 методических указаний квалитет, количество единиц допуска которого наиболее близко к расчетному. Для 8 квалитета (IT8) а = 25. Значит, назначаем допуски на составляющие размеры по этому квалитету. Выписываем значения допусков из таблицы 1.8 [2] и заносим их в колонку 3.
Сумма допусков составляющих звеньев получилась меньше допуска замыкающего звена. Чтобы уравнение удовлетворялось, необходимо изменить (в данном случае уменьшить) допуск одного из составляющих звеньев. Уменьшим допуск звена А3:
TA3 = ТА0 – (ТА1 + ТА2 + ТА4) = 120 – (46 + 22+ 33) = 19 мкм
Теперь определим номинальный размер и предельные отклонения замыкающего звена У2 = A0, а затем назначим отклонения составляющих звеньев. По уравнению:
А0 = ΣАiув – ΣАiум
А0 = (20+32+7) – 56 = 3 мкм.
Из условия задачи известно, что А0max = +0,06 мм А0min = -0,06 мм. Значит, предельные отклонения замыкающего звена: EsA0 = +60 мкм, EiA0 = -60 мкм.
Размеры А1, А2, А4 являются охватываемыми, и их отклонения назначаются в «минус». Размер А3 охватывающий, его отклонение назначаем в «плюс». Записываем принятые размеры и отклонения в колонку 4.
Рассчитаем верхнее и нижнее отклонение размера А3:
EsА0 = ΣEsАiув – ΣEiАiум
EiА0 = ΣEiАiув – ΣEsАiум
+60 = (-22 + EiA3 – 33) –(-46)
EiA3 = 60 + 22 + 33 - 46 = 69 мкм
-60 = (0 +0 + EsA3)- 0)
EsA3 = -60 мкм.
Записываем расчетные отклонения размера А3 в колонку 4. Производим окончательную проверку:
ТА0 = ΣТАi
ТА0 = 120 мкм.
Решение расположим в виде таблицы:
Таблица 2
В колонку 1 заносим номинальные размеры составляющих звеньев. В колонку 2 выписываем значение единицы допуска i для каждого составляющего размера из табл. 8.5 методических указаний. В колонку 3 – значение i2.
Определим среднее количество единиц допуска:
аср = ТА0/√∑ ????2= 120/√8,42= 41,35 ед.
По таблице 8.6 методических указаний определяем квалитет, количество единиц допуска которого близко к расчетному. Для IT10 а =64 ед. допуска. Выбираем 10 квалитет. Допуски составляющих размеров находим в таблице1.8 и записываем в колонку 4, а в колонку 5 записываем значения квадратов допусков и подсчитываем их сумму.
Σ(ITi)2 = 34820 > ITA02 = 14400 мкм
Т.к. √34820= 186,6 мкм, что превышает допуск замыкающего звена, нужно уменьшить допуск каких-либо составляющих звеньев. Можно уменьшить допуск одного или нескольких звеньев. Уменьшим, например, допуск звена А3 и А1.
Он будет равен:
TA0 =√∑(????????????2)
=
= 44,6 мкм
Занесем принятые значения допусков звеньев в колонку 6.
Теперь назначим отклонения звеньев А1, А2, А4, в «минус», т.к. они являются охватываемыми, а для звена А3 произведем расчет отклонений.
EcAi = (EsAi + EiAi)/2 EsAi = EcAi + (TAi/2)
EiAi = EcAi – (TAi/2)
EcA0 = ΣЕсАiув – ΣЕсАiум
Рассчитаем середины полей допусков звеньев:
ЕсА0 = (600 + (-600))/2 = 0 мкм
ЕсА2 = (0 – 58)/2 = – 29 мкм
ЕсА3 = (0 – 44,6)/2 = – 22,3 мкм
ЕсА4 = (0 – 84)/2 = – 42 мкм
ЕсА1 = (ЕсА2 +ЕсА3+ ЕсА4) - ЕсА0
ЕсА1 = (-29-22,3–42) -0 = -93,3 мкм.
Рассчитаем верхнее и нижнее отклонение звена А1:
ЕsА1 = -93,3 + (44,6/2) = -71 мкм;
EiА1 =-93,3 – (44,6/2) = -115,6 мкм
Занесем назначенные и рассчитанные отклонения звеньев в колонку 7.
Сравнивая колонку 7 таблицы 2. с колонкой 4 таблицы 1, мы видим, что теоретико-вероятностный метод позволяет назначать менее жесткие допуски составляющих звеньев при таком же допуске конечного звена. Иначе говоря, этот метод является более экономичным.
-
Поэтому проверим, обеспечивается ли для выбранной посадки (Ø160Н7/f7, SminT = 43 мкм, SmaxT = 123мкм) при Smin жидкостное трение.
Для этого определим наименьшую толщину масляного слоя :
hmin = (43/2)∙(1 - 0,11) = 19,135 мкм
Затем найдем запас надежности по толщине масляного слоя:
k ж.т=19,135/(1,6 + 3,2 + 2) = 2,81 > 2
Расчет показывает, что посадка по наименьшему зазору выбрана правильно, так как при Smin = 43 мкм обеспечивается жидкостное трение и создается запас надежности по толщине масляного слоя. Следовательно, табличное значение Smin = 43 мкм для выбранной посадки можно принять за SminF.
-
Теперь определим наибольший функциональный зазор при t = 50 °С:


-
Проверим, обеспечивается ли при этом зазоре жидкостное трение. Найдем х, hmin, кж.т.:
ψ= 0,978/160 = 0,0061
Cr = (1,16∙106∙0,00612)/(0,017∙31,4) = 80,86
χ = (80,86 + 0,964 - 0,998)/(80,86 + 0,964) = 0,988
hmin = (978/2)∙(1 - 0,969) = 9,38 мкм
k ж.т. = 5,87/(1,6 + 3,2 + 2) = 0,86 < 2
Расчеты показывают, что жидкостное трение не обеспечивается, следовательно, необходимо уменьшить функциональный зазор.
Принимаем SmaxF = 400мкм
ψ= 0,400/160 = 0,0025
Cr = (1,16∙106∙0,00252)/(0,017∙31,4) = 13,58
χ = (13,58 + 0,964 - 0,998)/(13,58 + 0,964) = 0,931
hmin = (400/2)∙(1 - 0,931) = 13,8 мкм
k ж.т. = 13,8/(1,6 + 3,2 + 2) = 2,03 > 2
-
Запас на износ:
Sи= (SmaxF–SminF) – (TD+ Td)== (400 - 43) - (40 + 80) = 237 мкм
-
Строим схему полей допусков для посадки с зазором с указанием SminT, SmaxT, SminF, SmaxF, Sи.

Рисунок 2.1 – Схема расположения полей допусков деталей при посадке с зазором
-
РАСЧЕТ ПОСАДКИ С НАТЯГОМ
Рассчитать и выбрать посадку с натягом для соединения вала и втулки (d = 50 мм, d1 = 20 мм, d2 = 80 мм, l =75 мм), которая работает под воздействием крутящего момента Мкр = 35 Н∙м. Запрессовка механическая. Материал обеих деталей - сталь 45.
-
Определяем рэ :


-
Определяем коэффициенты Ламе:
Св =(1 + (d1/d)2)/(1 –(d1/d)2)–в = (1+(0,02/0,05)2/(1-(0,02/0,05)2)-0,3 = 1,08
СА =(1 + (d/d2)2)/(1 –(d/d2)2)+ а = (1+(0,05/0,08)2/(1-(0,05/0,08)2)+0,3 = 2,58
-
Определяем Nmin :
Nmin = pэd(Cв/Eв+ Cа/Eа) = 1,25∙106∙0,05∙((1,08/2,06∙1011) + (2,58/2,06∙1011)) = 1,11 мкм
-
Находим поправки к расчетному натягу и определяем NminF:
u = 2(0,25∙10 + 0,25∙10) = 10 мкм
Принимаем ut = 0 и u4 = 0, исходя из условий задачи.
NminF = 1,11 + 10 = 11,11 мкм
-
Определяем допустимое удельное давление на контактирующих поверхностях:
рдоп1= 0,58т1(1 –(d1/d)2) = 0,58∙3,53∙108∙(1-(0,02/0,05)2)= 1,72∙108Па
рдоп2= 0,58т2(1 –(d/d2)2) = 0,58∙3,53∙108∙(1-(0,05/0,08)2)=1,25∙108Па
В качестве рдоп выбираем рдоп2 ,как наименьшее.
-
Определяем величину наибольшего натяга Nmax:
Nmax= pдопd((C1/E1) + (C2/E2))
Nmax = 1,25∙108∙0,05∙((1,08/2,06∙1011)+(2,58/2,06∙1011)) = 111 мкм
-
Находим поправки к наибольшему натягу и определяем NmaxF :
u =16 мкм, ut = 0, up = 0, uд = 0,78
NmaxF=Nmaxuуд+ u –ut = 111∙1 +16 = 117 мкм
-
Выбираем табличную посадку по наибольшему функциональному натягу NmaxF, при которой создавался бы запас прочности соединения и запас прочности деталей:
Ø50H8/u8, для которой NmaxT = 109 мкм (
NminT = 31мкм (>NminF)
Определяем для выбранной посадки запас прочности соединения при сборке и при эксплуатации:
N з.э= 31 - 11 = 20 мкм
N3С = 117 - 109 = 8 мкм
Для правильно выбранной посадки запас прочности соединения при сборке N3С всегда должен быть меньше запаса прочности соединения при эксплуатации N3Э., потому что N3С нужен только в момент сборки для случая возможного снижения прочности материала деталей и увеличения силы запрессовки из-за перекоса деталей, колебания коэффициента трения и т.д.
-
Строим схему расположения полей допусков выбранной посадки:
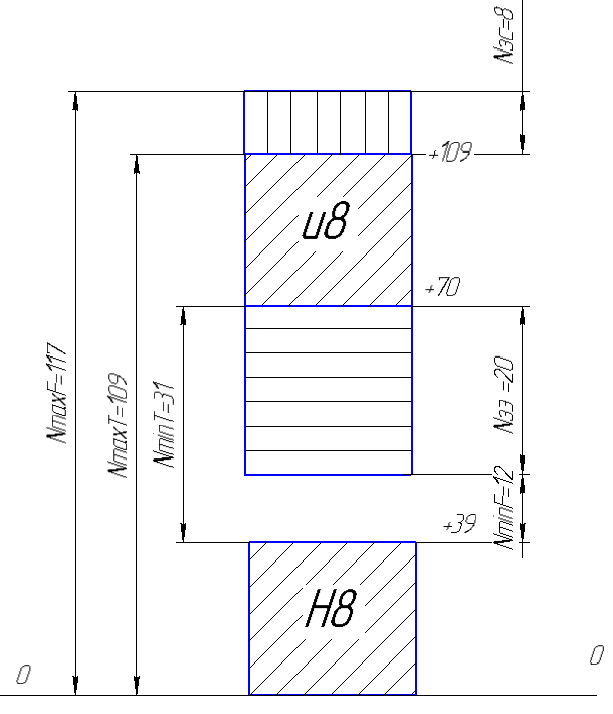
Рисунок 3.1 – Схема расположения полей допусков деталей при посадке с натягом
-
РАСЧЕТ РАЗМЕРНОЙ ЦЕПИ
Величина зазора после сборки должна быть в пределах у2(±0,06) мм. Требуется назначить допуски и предельные отклонения на составляющие размеры.

Рисунок 4.1 – Схема задания
-
Расчет методом максимума-минимума
Замыкающим звеном является зазор У2 = А0.
Строим схему размерной цепи и определяем, какие составляющие звенья будут увеличивающими и уменьшающими.
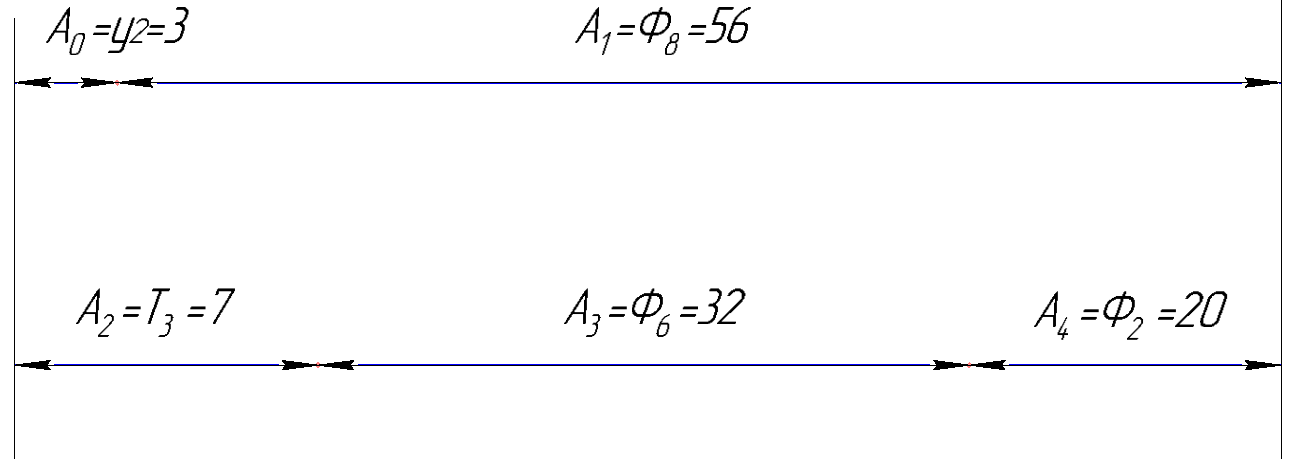
Рисунок 4.2 – Схема размерной цепи
Решение удобно расположить в виде таблицы:
Таблица 1
Аiном,мм | i,мкм | ITAi, мкм | Аi (принятое),мм |
А1 = 56← | 1,86 | 46 | 56-0,046 |
А0= 3 | - | - | - |
А2 = 7→ | 0,9 | 22 | 7-0,022 |
А3 = 32 → | 1,56 | 39 (19) | ![]() |
А4= 20→ | 1,31 | 33 | 20-0,033 |
Σ | 4,92 | 140(120) | |
Записываем в колонку 1 номинальные значения составляющих звеньев. Затем в колонку 2 выписываем значения единиц допуска i из таблицы 8.7 методических указаний для всех составляющих размеров.
Полагая, что все составляющие размеры размерной цепи равноточные (способ равноточных допусков), т.е. должны выполняться по одному квалитету:
ТАi = аi∙i,
где аi – количество единиц допуска, находим среднее количество единиц допуска аср для каждого составляющего размера по формуле:
аср = ТА0/ Σ ii
Величина ТА0 задана по условиям задачи.
Таким образом, аср = 120/4,92 = 24,4 единиц.
Затем находим по таблице 8.8 методических указаний квалитет, количество единиц допуска которого наиболее близко к расчетному. Для 8 квалитета (IT8) а = 25. Значит, назначаем допуски на составляющие размеры по этому квалитету. Выписываем значения допусков из таблицы 1.8 [2] и заносим их в колонку 3.
Сумма допусков составляющих звеньев получилась меньше допуска замыкающего звена. Чтобы уравнение удовлетворялось, необходимо изменить (в данном случае уменьшить) допуск одного из составляющих звеньев. Уменьшим допуск звена А3:
TA3 = ТА0 – (ТА1 + ТА2 + ТА4) = 120 – (46 + 22+ 33) = 19 мкм
Теперь определим номинальный размер и предельные отклонения замыкающего звена У2 = A0, а затем назначим отклонения составляющих звеньев. По уравнению:
А0 = ΣАiув – ΣАiум
А0 = (20+32+7) – 56 = 3 мкм.
Из условия задачи известно, что А0max = +0,06 мм А0min = -0,06 мм. Значит, предельные отклонения замыкающего звена: EsA0 = +60 мкм, EiA0 = -60 мкм.
Размеры А1, А2, А4 являются охватываемыми, и их отклонения назначаются в «минус». Размер А3 охватывающий, его отклонение назначаем в «плюс». Записываем принятые размеры и отклонения в колонку 4.
Рассчитаем верхнее и нижнее отклонение размера А3:
EsА0 = ΣEsАiув – ΣEiАiум
EiА0 = ΣEiАiув – ΣEsАiум
+60 = (-22 + EiA3 – 33) –(-46)
EiA3 = 60 + 22 + 33 - 46 = 69 мкм
-60 = (0 +0 + EsA3)- 0)
EsA3 = -60 мкм.
Записываем расчетные отклонения размера А3 в колонку 4. Производим окончательную проверку:
ТА0 = ΣТАi
ТА0 = 120 мкм.
-
Расчет теоретико-вероятностным методом
Решение расположим в виде таблицы:
Таблица 2
Аiном, мм | i, мкм | i2 мкм2 | IT12, мкм | (IT)2 мкм2 | TAi,мкм принятое | Аi,мм принятое |
А1 = 56← | 1,86 | 3,46 | 120 | 14400 | 44,6 | ![]() |
А2 = 7 → | 0,9 | 0,81 | 58 | 3364 | 58 | 7-0,058 |
А3 = 32→ | 1,56 | 2,43 | 100 | 10000 | 44,6 | ![]() |
А4 = 20 → | 1,31 | 1,72 | 84 | 7056 | 84 | 20-0,084 |
А0 = 3 | | | | | | |
Σ | | 8,42 | | 34820 (14400) | | |
В колонку 1 заносим номинальные размеры составляющих звеньев. В колонку 2 выписываем значение единицы допуска i для каждого составляющего размера из табл. 8.5 методических указаний. В колонку 3 – значение i2.
Определим среднее количество единиц допуска:
аср = ТА0/√∑ ????2= 120/√8,42= 41,35 ед.
По таблице 8.6 методических указаний определяем квалитет, количество единиц допуска которого близко к расчетному. Для IT10 а =64 ед. допуска. Выбираем 10 квалитет. Допуски составляющих размеров находим в таблице1.8 и записываем в колонку 4, а в колонку 5 записываем значения квадратов допусков и подсчитываем их сумму.
Σ(ITi)2 = 34820 > ITA02 = 14400 мкм
Т.к. √34820= 186,6 мкм, что превышает допуск замыкающего звена, нужно уменьшить допуск каких-либо составляющих звеньев. Можно уменьшить допуск одного или нескольких звеньев. Уменьшим, например, допуск звена А3 и А1.
Он будет равен:
TA0 =√∑(????????????2)



Занесем принятые значения допусков звеньев в колонку 6.
Теперь назначим отклонения звеньев А1, А2, А4, в «минус», т.к. они являются охватываемыми, а для звена А3 произведем расчет отклонений.
EcAi = (EsAi + EiAi)/2 EsAi = EcAi + (TAi/2)
EiAi = EcAi – (TAi/2)
EcA0 = ΣЕсАiув – ΣЕсАiум
Рассчитаем середины полей допусков звеньев:
ЕсА0 = (600 + (-600))/2 = 0 мкм
ЕсА2 = (0 – 58)/2 = – 29 мкм
ЕсА3 = (0 – 44,6)/2 = – 22,3 мкм
ЕсА4 = (0 – 84)/2 = – 42 мкм
ЕсА1 = (ЕсА2 +ЕсА3+ ЕсА4) - ЕсА0
ЕсА1 = (-29-22,3–42) -0 = -93,3 мкм.
Рассчитаем верхнее и нижнее отклонение звена А1:
ЕsА1 = -93,3 + (44,6/2) = -71 мкм;
EiА1 =-93,3 – (44,6/2) = -115,6 мкм
Занесем назначенные и рассчитанные отклонения звеньев в колонку 7.
Сравнивая колонку 7 таблицы 2. с колонкой 4 таблицы 1, мы видим, что теоретико-вероятностный метод позволяет назначать менее жесткие допуски составляющих звеньев при таком же допуске конечного звена. Иначе говоря, этот метод является более экономичным.
СПИСОК ИСПОЛЬЗОВАННЫХ ИСТОЧНИКОВ
-
ГОСТ 24853-81 «Калибры гладкие для размеров до 500 мм. Допуски». -
ГОСТ 25346-2013 «Основные нормы взаимозаменяемости. Характеристики изделий геометрические. Система допусков на линейные размеры. Основные положения, допуски, отклонения и посадки».