Файл: 1Расчет геометрических размеров рабочего пространства сверхмощных дуговых сталеплавильных печей (дсп).docx
ВУЗ: Не указан
Категория: Не указан
Дисциплина: Не указана
Добавлен: 25.04.2024
Просмотров: 24
Скачиваний: 0
ВНИМАНИЕ! Если данный файл нарушает Ваши авторские права, то обязательно сообщите нам.
днище изготавливают из немагнитной стали, причём для размещения статора ЭМП целесообразно иметь днище с двойной конусностью, чтобы углы образующих с горизонталью были 15 и 45 градусов. Такая конструкция днища позволяет иметь наименьший объём футеровки подины.
Таблица 1 Рекомендуемая толщина элементов футеровки ДСП, ёмкостью 200 т., мм.
Конструкцию огнеупорной футеровки стен ДСП обычной или повышенной мощности выбирают в зависимости от характера износа кирпичей, от формы свободного пространства и конуса корпуса. Вследствие особенности тепловой работы ДСП стены имеют не только огнеупорный (рабочий) слой толщиной Δр, определяемой длиной применяемого кирпича. Во избежание повреждения кожуха при аварийном полном разрушении рабочего слоя целесообразно применять дополнительный (арматурный) слой толщиной Δа. Для этого кожух обкладывают кирпичом на плашку (65 мм) или на ребро (115 мм).
Общая толщина футеровки стены в нижней части находим по следующей формуле:
Δст=Δр+Δа (28)
Δст=575+115=690 (мм)
Верхнюю часть стен делают меньшей толщины, поскольку с увеличением высоты снижается тепловая нагрузка футеровки. Верхнюю часть стен находим по следующей формуле:
Δст4=Δа4+Δр4 (29)
Как правило, в верхней части стен арматурный слой не выполняют, т.е. Δа4=0 мм. Тогда:
Δст4=Δр4
Δст4= (575 мм)
При известной толщине футеровки стен определяют внутренний диаметр кожуха на уровне откосов ванны по следующей формуле:
Dк=D0+2·Δcт (30)
Dк=7,007+2·0,69=8,387 (м)
И внутренний диаметр кожуха на уровне пят свода по следующей формуле:
Dк4=D4+2Δcт4 (31)
Dк4=8,555+2·0,575=9,705 (м)
Диаметр кожуха Dк является паспортной характеристикой и также может служить определяющим параметром ДСП вместимостью m0. Кожух ДСП изготавливают из котельной листовой стали толщиной Δк, исходя из ориентировочного соотношения:
Δк=Dк:200
Δк=8,387:200=0,0419 (м) Δк=41,9 (мм)
ДСП третьего поколения имеют цилиндроконический кожух. Высота конической части от уровня порога рабочего окна находим по следующей формуле:
hкк=(1:3..2:3)·((0,03..0,1)+(0,35..0,45)·D0). (32)
hкк=(1:3..2:3) · [(0.05+0.4)·7]=1,05..2,1 принимаем hкк=2 м.
Угол наклона конической части определяется по следующей формуле:
tgγ=(Dк4–Dк):2hкк (33)
tgγ=(9,696–8,38):2·2=0,329 γ=190
Угол наклона образующей конической части с вертикалью должен составлять γ=10..260.
В кожухе корпуса ДСП вырезают отверстия для рабочего окна и выпускного (сливного) отверстия. Ширина рабочего окна обычно составляет
0,25 ..0,30 диаметра рабочего пространства ДСП. Высота окна в зависимости от принятой высоты расположения свода приблизительно равна 0,8..1,2 ширины окна. Ширину рабочего окна находим по следующей формуле:
δ 0=(0,25..0,30)·D0; (34)
δ0=(0,25..0,30)7,007=1,752..2,102 (м)
h0=(0,2..0,36)·D0; (35)
h0=(0,2..0,36)7,007=1,401..2,523 (м)
Вырез для рабочего окна обрамляют водоохлаждаемой рамой; футеровку в месте выреза удерживают и защищают от повреждения П–образной водоохлаждаемой аркой. Выпускное отверстие выполняют круглым (диаметром 120..150 мм) или прямоугольным (150250 мм).
Толщина Δсв кирпичной футеровки свода определяется длиной применяемых огнеупорных кирпичей – периклазохромитовых, высокоглинозёмистых или динасовых. Стрела подъёма hпс сферического (купольного) свода, выбираемая с учётом строительной прочности футеровки.
Определяет радиус сферы свода по следующей формуле:
rсф.св=0,5·(0,25·Dсв2+hпс2):hпс, (36)
где Dсв–диаметр свода, практически равный Dк4.
hсв=kсв·D0 (35)
где
hп.с. - стрела подъема кирпичной футеровки над уровнем пят сферического свода (или секции);
- условие рационального расположения свода по теплотехническим условиям.
hсв=0,6·7,007=4,204 (м)
Наибольшая строительная прочность периклазохромитовых сводов достигается при стреле подъема (
):(
) диаметра свода Dсв
hп.с= hсв- hст =4,204-2,452=1,752 (м) (36)
Свод ДСП опирается на песчаный затвор корпуса, размер которого характеризуют диаметром кожуха Dк
, поэтому Dсв
Dк
и hп.с.= kп.с.∙Dк
rсф.св=0,5(0,25∙9,7052+1,7522):1,752=7,596 (м).
1.4 Определение диаметра графитированного расходуемого электрода
В футеровке свода необходимо выполнить ряд отверстий различного диаметра для размещения трёх электродов, патрубка газоотсоса, различных технологических устройств – кислородная фурма, механизированный пробоотборник, загрузочная воронка для подачи шлакообразующих материалов.
Диаметр расходуемого электрода определяется по следующей формуле:
(37)
где dэл–диаметр расходуемого электрода, см;
Iсила тока, проходящего по электроду, А;
ρудельное электрическое сопротивление электрода при 500°С. Для графитированных электродов марки ЭГОО ρ=8..10 Ом/мм2м;
kкоэффициент пропорциональности. Для графитированных электродов k=2,1 (Вт/см2).
Для расчёта силы тока, протекающего по электроду, определяем кажущуюся мощность печного трансформатора по следующей формуле:
Рк=(110·Dкн3,32):τ, (38)
где Рк – кажущаяся мощность печного трансформатора, кВА; τ–время плавки, ч; Dкн – наружный диаметр кожуха на уровне откосов ванны ,м, определяется по следующей формуле:
Dкн=Dк+Dк:100 (39)
Dкн=8,38+0,0838=8,4638 (м)
Рк=(110·7,04983,32):τ=66050 (кВА)
Значение Рк принято по ГОСТ 7260-70. Из этой формулы находим время плавки:
(ч)
Верхняя ступень вторичного напряжения печного трансформатора определяется по формуле:
Uл=
(40)
где Uэл –верхняя ступень вторичного напряжения, В.
Uл=
=606,339 (В)
В этом случае сила тока, проходящего через электрод, определяется по формуле:
I=(1000·Рк):(1,73·Uл) (41)
I=(1000·66050):(1,73·606,339)=62966,741 (А)
=875,517 (мм)
Согласно ГОСТ 4426–80 принимаем: dэл=700 (мм)
Диаметр распада электрода определяется по формуле:
Dp=(0,2..0,3)·D0 (42)
Dр=(0,2..0,3)· 7,007=1,401..2,102 (м).
Диаметр отверстия под электрод определяется по формуле:
D=dэл+(20..40 мм) (43)
D=700+30=730 (мм)
Полученные размеры рабочего пространства ДСП должны соответствовать размерам действующих печей по ГОСТ 720670. При выборе и расчёте электрической цепи и диаметра электрода ДСП средняя плотность тока и допустимый рабочий ток выбирается по ГОСТ 4426 80, а основные технические характеристики электропечных трансформаторов по ГОСТ 20247 81.
2 Специальная часть
2.1 Дуговая печь для выплавки синтетических шлаков.
Синтетическим (от английского synthetic – искусственный) называют предназначенный для обработки стали в ковше шлак, который получают вне сталеплавильного агрегата.
Синтетические шлаки выплавляют в электропечах, циклонных плавильных установках и других агрегатах. Жидкий шлак в необходимом количестве сливают в сталеразливочный ковш, который подают под выпуск. В процессе выпуска струя падающего в ковш металла эмульгирует шлак и металл с последующим разделением фаз. В результате эмульгирования резко увеличивается площадь поверхности раздела шлак-металл и скорость протекающих реакций. Результаты обработки определяются высотой падения струи металла, массой металла и шлака, физическими характеристиками и составом шлака и др. Обычно при расходах синтетического шлака 30 – 50 кг/т такая обработка позволяет в ходе выпуска плавки получать степень десульфурации стали равную 30 – 70%. Наиболее эффективная десульфурация металла наблюдается при выпуске плавки из крупнотоннажных агрегатов.
Первоначально для внепечной десульфурации стали были разработаны известково-глиноземистые шлаки состава, % масс.: 50 – 55 CaO, 37 – 43 Al2O3, < 7 SiO2, < 7 MgO, < 0,5 FeO. Для выплавки синтетических шлаков такого состава требовались дефицитные материалы с низким содержанием кремнезема.
Впоследствии была показана возможность эффективной десульфурации стали известково-шамотными шлаками состава, % масс.: 48 – 56 CaO, 6 – 10 MgO, 18 – 22 SiO2, 12 – 16 Al2O3, 0,5 CaF2, < 0,5 FeO.
Широкое использование синтетических шлаков сдерживалось отсутствием возможности размещения в существующих сталеплавильных цехах обору-дования для их выплавки. В связи с этим была разработана технология десульфурации стали в ковше самоплавкими шлаковыми смесями состава, % масс.: 12 – 14 алюминиевый порошок или алюминиевая стружка; 21 – 24 натриевая селитра; 20 флюоритовый концентрат; известь – остальное. Необходимое количество самоплавкой шлаковой смеси загружали в чугуновозный ковш и поджигали. Полученный таким способом жидкий шлак переливали из чугуновозного ковша в сталеразливочный и подавали под выпуск.
Использование самоплавких шлаковых смесей существенно упростило технологию получения синтетических шлаков. Однако, после нескольких крупных пожаров в отделениях подготовки смесей металлургические предприятия СССР от их использования отказались.
В настоящее время для внепечной десульфурации стали успешно используют твердые шлакообразующие смеси из 10 – 30% плавикового шпата и извести. По ходу выпуска плавки смесь вместе с раскислителями и легирующими загружают в ковш, при этом плавление смеси обычно завершается в течение 1 – 2 минут.
Особенность этой технологии заключается в том, что однородный шлак получается при наполнении второй половины ковша, когда мощность перемешивания стали и шлака падающей в ковш струей металла значительно уменьшается. В связи с этим десульфурирующая способность шлака используется не полностью. Поэтому после выпуска плавки целесообразно проводить дополнительное перемешивание шлака и металла продувкой в ковше аргоном.
Для повышения эффективности десульфурации стали на выпуске из сталеплавильного агрегата применяются предварительно переплавленные легкоплавкие шлаковые смеси. Примером может служить рафинирующая смесь ИРС-2 производства ОАО «НПП «Техмет» (г. Донецк) состава, % масс.: < 3 C, 53 – 60 CaOобщ, < 6 MgO, < 16 SiO2, 4 – 8 F, 4 – 6 (Na2O + K2O), 10 – 18 Al2O3, < 0,5 S, < 1,5 P2O5, < 2 MnO, < 3 FeO. Основность смеси, рассчитанная как отношение концентраций CaO и SiO2, обычно составляет не менее 3,5. Температура плавления смеси не превышает 1320 – 1350оС.
Широкое распространение в электросталеплавильных, мартеновских и конверторных печах технологии обработки жидкой стали, в ковше синтетическими шлаками вызвало необходимость создания специальной шлакоплавильной электропечи.
Таблица 1 Рекомендуемая толщина элементов футеровки ДСП, ёмкостью 200 т., мм.
Элемент футеровки | Толщина элементов футеровки ДСП, мм |
Подина: | |
Теплоизоляционный слой | 180 |
Рабочий слой (набивной) | 150 |
Общая толщина | 905 |
Стены: | |
Арматурный слой | 115 |
Рабочий слой | 460 |
Нижняя часть | 460 |
Верхняя часть | 380 |
Свод | 380 |
Конструкцию огнеупорной футеровки стен ДСП обычной или повышенной мощности выбирают в зависимости от характера износа кирпичей, от формы свободного пространства и конуса корпуса. Вследствие особенности тепловой работы ДСП стены имеют не только огнеупорный (рабочий) слой толщиной Δр, определяемой длиной применяемого кирпича. Во избежание повреждения кожуха при аварийном полном разрушении рабочего слоя целесообразно применять дополнительный (арматурный) слой толщиной Δа. Для этого кожух обкладывают кирпичом на плашку (65 мм) или на ребро (115 мм).
Общая толщина футеровки стены в нижней части находим по следующей формуле:
Δст=Δр+Δа (28)
Δст=575+115=690 (мм)
Верхнюю часть стен делают меньшей толщины, поскольку с увеличением высоты снижается тепловая нагрузка футеровки. Верхнюю часть стен находим по следующей формуле:
Δст4=Δа4+Δр4 (29)
Как правило, в верхней части стен арматурный слой не выполняют, т.е. Δа4=0 мм. Тогда:
Δст4=Δр4
Δст4= (575 мм)
При известной толщине футеровки стен определяют внутренний диаметр кожуха на уровне откосов ванны по следующей формуле:
Dк=D0+2·Δcт (30)
Dк=7,007+2·0,69=8,387 (м)
И внутренний диаметр кожуха на уровне пят свода по следующей формуле:
Dк4=D4+2Δcт4 (31)
Dк4=8,555+2·0,575=9,705 (м)
Диаметр кожуха Dк является паспортной характеристикой и также может служить определяющим параметром ДСП вместимостью m0. Кожух ДСП изготавливают из котельной листовой стали толщиной Δк, исходя из ориентировочного соотношения:
Δк=Dк:200
Δк=8,387:200=0,0419 (м) Δк=41,9 (мм)
ДСП третьего поколения имеют цилиндроконический кожух. Высота конической части от уровня порога рабочего окна находим по следующей формуле:
hкк=(1:3..2:3)·((0,03..0,1)+(0,35..0,45)·D0). (32)
hкк=(1:3..2:3) · [(0.05+0.4)·7]=1,05..2,1 принимаем hкк=2 м.
Угол наклона конической части определяется по следующей формуле:
tgγ=(Dк4–Dк):2hкк (33)
tgγ=(9,696–8,38):2·2=0,329 γ=190
Угол наклона образующей конической части с вертикалью должен составлять γ=10..260.
В кожухе корпуса ДСП вырезают отверстия для рабочего окна и выпускного (сливного) отверстия. Ширина рабочего окна обычно составляет
0,25 ..0,30 диаметра рабочего пространства ДСП. Высота окна в зависимости от принятой высоты расположения свода приблизительно равна 0,8..1,2 ширины окна. Ширину рабочего окна находим по следующей формуле:
δ 0=(0,25..0,30)·D0; (34)
δ0=(0,25..0,30)7,007=1,752..2,102 (м)
h0=(0,2..0,36)·D0; (35)
h0=(0,2..0,36)7,007=1,401..2,523 (м)
Вырез для рабочего окна обрамляют водоохлаждаемой рамой; футеровку в месте выреза удерживают и защищают от повреждения П–образной водоохлаждаемой аркой. Выпускное отверстие выполняют круглым (диаметром 120..150 мм) или прямоугольным (150250 мм).
Толщина Δсв кирпичной футеровки свода определяется длиной применяемых огнеупорных кирпичей – периклазохромитовых, высокоглинозёмистых или динасовых. Стрела подъёма hпс сферического (купольного) свода, выбираемая с учётом строительной прочности футеровки.
Определяет радиус сферы свода по следующей формуле:
rсф.св=0,5·(0,25·Dсв2+hпс2):hпс, (36)
где Dсв–диаметр свода, практически равный Dк4.
hсв=kсв·D0 (35)
где


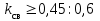
hсв=0,6·7,007=4,204 (м)
Наибольшая строительная прочность периклазохромитовых сводов достигается при стреле подъема (


hп.с= hсв- hст =4,204-2,452=1,752 (м) (36)
Свод ДСП опирается на песчаный затвор корпуса, размер которого характеризуют диаметром кожуха Dк




rсф.св=0,5(0,25∙9,7052+1,7522):1,752=7,596 (м).
1.4 Определение диаметра графитированного расходуемого электрода
В футеровке свода необходимо выполнить ряд отверстий различного диаметра для размещения трёх электродов, патрубка газоотсоса, различных технологических устройств – кислородная фурма, механизированный пробоотборник, загрузочная воронка для подачи шлакообразующих материалов.
Диаметр расходуемого электрода определяется по следующей формуле:
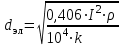
где dэл–диаметр расходуемого электрода, см;
Iсила тока, проходящего по электроду, А;
ρудельное электрическое сопротивление электрода при 500°С. Для графитированных электродов марки ЭГОО ρ=8..10 Ом/мм2м;
kкоэффициент пропорциональности. Для графитированных электродов k=2,1 (Вт/см2).
Для расчёта силы тока, протекающего по электроду, определяем кажущуюся мощность печного трансформатора по следующей формуле:
Рк=(110·Dкн3,32):τ, (38)
где Рк – кажущаяся мощность печного трансформатора, кВА; τ–время плавки, ч; Dкн – наружный диаметр кожуха на уровне откосов ванны ,м, определяется по следующей формуле:
Dкн=Dк+Dк:100 (39)
Dкн=8,38+0,0838=8,4638 (м)
Рк=(110·7,04983,32):τ=66050 (кВА)
Значение Рк принято по ГОСТ 7260-70. Из этой формулы находим время плавки:
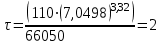
Верхняя ступень вторичного напряжения печного трансформатора определяется по формуле:
Uл=

где Uэл –верхняя ступень вторичного напряжения, В.
Uл=

В этом случае сила тока, проходящего через электрод, определяется по формуле:
I=(1000·Рк):(1,73·Uл) (41)
I=(1000·66050):(1,73·606,339)=62966,741 (А)
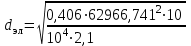
Согласно ГОСТ 4426–80 принимаем: dэл=700 (мм)
Диаметр распада электрода определяется по формуле:
Dp=(0,2..0,3)·D0 (42)
Dр=(0,2..0,3)· 7,007=1,401..2,102 (м).
Диаметр отверстия под электрод определяется по формуле:
D=dэл+(20..40 мм) (43)
D=700+30=730 (мм)
Полученные размеры рабочего пространства ДСП должны соответствовать размерам действующих печей по ГОСТ 720670. При выборе и расчёте электрической цепи и диаметра электрода ДСП средняя плотность тока и допустимый рабочий ток выбирается по ГОСТ 4426 80, а основные технические характеристики электропечных трансформаторов по ГОСТ 20247 81.
2 Специальная часть
2.1 Дуговая печь для выплавки синтетических шлаков.
Синтетическим (от английского synthetic – искусственный) называют предназначенный для обработки стали в ковше шлак, который получают вне сталеплавильного агрегата.
Синтетические шлаки выплавляют в электропечах, циклонных плавильных установках и других агрегатах. Жидкий шлак в необходимом количестве сливают в сталеразливочный ковш, который подают под выпуск. В процессе выпуска струя падающего в ковш металла эмульгирует шлак и металл с последующим разделением фаз. В результате эмульгирования резко увеличивается площадь поверхности раздела шлак-металл и скорость протекающих реакций. Результаты обработки определяются высотой падения струи металла, массой металла и шлака, физическими характеристиками и составом шлака и др. Обычно при расходах синтетического шлака 30 – 50 кг/т такая обработка позволяет в ходе выпуска плавки получать степень десульфурации стали равную 30 – 70%. Наиболее эффективная десульфурация металла наблюдается при выпуске плавки из крупнотоннажных агрегатов.
Первоначально для внепечной десульфурации стали были разработаны известково-глиноземистые шлаки состава, % масс.: 50 – 55 CaO, 37 – 43 Al2O3, < 7 SiO2, < 7 MgO, < 0,5 FeO. Для выплавки синтетических шлаков такого состава требовались дефицитные материалы с низким содержанием кремнезема.
Впоследствии была показана возможность эффективной десульфурации стали известково-шамотными шлаками состава, % масс.: 48 – 56 CaO, 6 – 10 MgO, 18 – 22 SiO2, 12 – 16 Al2O3, 0,5 CaF2, < 0,5 FeO.
Широкое использование синтетических шлаков сдерживалось отсутствием возможности размещения в существующих сталеплавильных цехах обору-дования для их выплавки. В связи с этим была разработана технология десульфурации стали в ковше самоплавкими шлаковыми смесями состава, % масс.: 12 – 14 алюминиевый порошок или алюминиевая стружка; 21 – 24 натриевая селитра; 20 флюоритовый концентрат; известь – остальное. Необходимое количество самоплавкой шлаковой смеси загружали в чугуновозный ковш и поджигали. Полученный таким способом жидкий шлак переливали из чугуновозного ковша в сталеразливочный и подавали под выпуск.
Использование самоплавких шлаковых смесей существенно упростило технологию получения синтетических шлаков. Однако, после нескольких крупных пожаров в отделениях подготовки смесей металлургические предприятия СССР от их использования отказались.
В настоящее время для внепечной десульфурации стали успешно используют твердые шлакообразующие смеси из 10 – 30% плавикового шпата и извести. По ходу выпуска плавки смесь вместе с раскислителями и легирующими загружают в ковш, при этом плавление смеси обычно завершается в течение 1 – 2 минут.
Особенность этой технологии заключается в том, что однородный шлак получается при наполнении второй половины ковша, когда мощность перемешивания стали и шлака падающей в ковш струей металла значительно уменьшается. В связи с этим десульфурирующая способность шлака используется не полностью. Поэтому после выпуска плавки целесообразно проводить дополнительное перемешивание шлака и металла продувкой в ковше аргоном.
Для повышения эффективности десульфурации стали на выпуске из сталеплавильного агрегата применяются предварительно переплавленные легкоплавкие шлаковые смеси. Примером может служить рафинирующая смесь ИРС-2 производства ОАО «НПП «Техмет» (г. Донецк) состава, % масс.: < 3 C, 53 – 60 CaOобщ, < 6 MgO, < 16 SiO2, 4 – 8 F, 4 – 6 (Na2O + K2O), 10 – 18 Al2O3, < 0,5 S, < 1,5 P2O5, < 2 MnO, < 3 FeO. Основность смеси, рассчитанная как отношение концентраций CaO и SiO2, обычно составляет не менее 3,5. Температура плавления смеси не превышает 1320 – 1350оС.
Широкое распространение в электросталеплавильных, мартеновских и конверторных печах технологии обработки жидкой стали, в ковше синтетическими шлаками вызвало необходимость создания специальной шлакоплавильной электропечи.