Файл: Забайкальский институт железнодорожного транспорта филиал Федерального государственного бюджетного образовательного учреждения высшего образования Иркутский государственный университет путей сообщения.docx
Добавлен: 26.04.2024
Просмотров: 33
Скачиваний: 1
ВНИМАНИЕ! Если данный файл нарушает Ваши авторские права, то обязательно сообщите нам.
3 Приемы монтажа плат навесного монтажа с помощью шаблонов и печатных плат
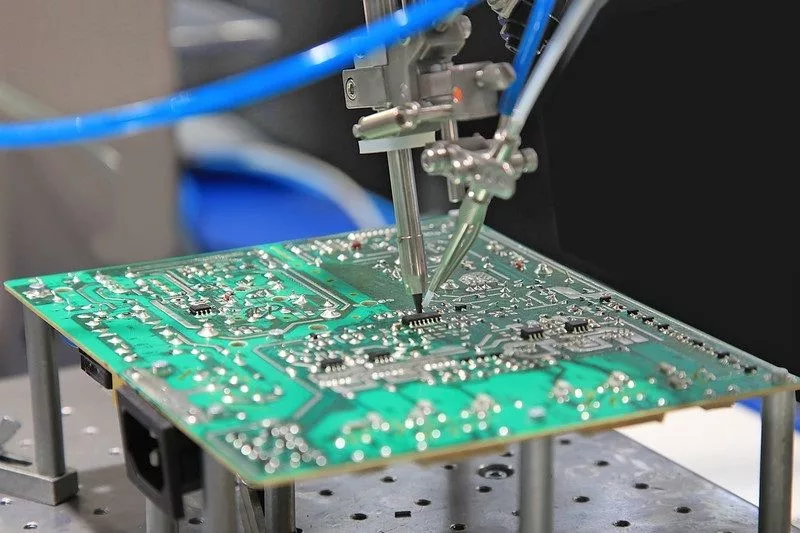
Рисунок 4 – монтаж навесных элементов на печатных платах
Виды монтажа навесных элементов на печатных платах.
Навесные элементы (МС, ЭРЭ, элементы коммутации и пр.) могут размещаться по одну или обе стороны ПП. Число МС и ЭРЭ, устанавливаемых на плату, может достигать десятков и сотен штук. В зависимости от вида внешних выводов МС и ЭРЭ их монтаж на поверхность ПП делят на штыревой, планарный и поверхностный. Установка МС и ЭРЭ на ПП проводится в зависимости от типа производства ручным, механизированным, полуавтоматическим или автоматическим способом. Однако вне зависимости от способа монтажа необходимо выполнение следующих операций: комплектация элементов, устанавливаемых на плату, подготовка элементов к монтажу, установка элементов на плату и их фиксация, пайка, защита и контроль готового модуля.
Комплектация устанавливаемых на ПП элементов: количество различных элементов по номиналам и типоразмерам определяется на основе спецификации, исходя из объема выпуска изделия в течение определенного периода. Закупаемые МС и ЭРЭ складируют на центральном заводском складе, откуда по заявкам их доставляют на цеховой склад или участок комплектации и далее на рабочие места.
Подготовка элементов к монтажу включает рихтовку (исправление формы выводов), формовку (придание выводам определенной формы), обрезку и лужение выводов.
При неплотном монтаже и небольшой партии ПП установку навесных элементов можно выполнять вручную по монтажному чертежу. В остальных случаях используют средства автоматизации и механизации. Чтобы установленные на ПП навесные элементы не выпали или не сдвинулись со своих мест при последующей транспортировке, необходимо их фиксировать на поверхности ПП. Надежным, но трудоемким способом фиксации осевых выводов является их подгибка с обратной стороны платы, или фиксация элементов за счет упругих свойств выводов, имеющих зиг-формовку. Микросхемы с планарными выводами фиксируют на плате приклеиванием или припайкой диагональных контактов. В случае применения МС со штыревыми выводами конической формы выводы при установке заклиниваются в монтажных отверстиях и надежно удерживаются перед пайкой.
Элементы для поверхностного монтажа фиксируют путем приклейки на предварительно нанесенную паяльную пасту, на которой они устанавливаются и удерживаются. В зависимости от типа производства и объема выпуска ЭВМ пайка элементов осуществляется вручную паяльником, групповыми и автоматизированными способами.
Ручную пайку выполняют паяльником на монтажном столе, снабженным системой локального удаления газов. Паяльник используют в опытном, ремонтном производствах, при исправлении брака и при установке небольшого числа элементов, которые невозможно припаять другими способами.
Для серийного производства рекомендуется использовать более производительные групповые способы пайки, когда все соединения подвергаются пайке одновременно.
Примером группового способа является пайка погружением, когда ПП с установленными на ней навесными элементами погружают в ванну с расплавленным припоем.
Перед пайкой места, не подлежащие пайке, закрываются термостойкой эпоксидной маской, наносимой через трафарет, или приклеиванием отштампованных пленочных масок. На места пайки наносится спирто-канифолевый флюс. Перед погружением платы в ванну с расплавленным припоем с его поверхности следует удалить оксидную (шлаковую) пленку. Существуют механические, химические способы удаления пленки и очистки поверхности.
Цикл пайки погружением, следующий: плату, опускают на поверхность припоя, где происходит прогрев мест пайки — в течение 2...4 с, затем на ПП накладываются колебания в течение 3...5с, частота колебаний составляет около 100 Гц, амплитуда — 0,1…0,3 мм. За счет этого улучшается растекаемостьприпоя и он проникает в зазор между выводом и монтажным отверстием. Происходит оплавление припоем мест пайки. Затем ПП поднимают из ванны и припой затвердевает.
Пайка погружением является производительным способом, так как при этом способе можно проводить пайку сразу нескольких плат. Недостатком этого способа является сложность качественного удаления пленки с поверхности припоя, что приводит к некачественному пропаю. Кроме того, возможен и термоудар, несмотря на защитную маску. Существуют другие варианты пайки погружением, в которых устраняют присущие пайке погружением недостатки: применение керамической маски, пайка в нейтральной среде и т. д.
Широкое распространение нашел другой групповой способ пайки, называемый пайка волной припоя. В этом случае на поверхности расплавленного припоя электромагнитным, механическим или гидродинамическим способами создается волна, над которой и проводят ПП в процессе пайки. Печатные платы с установленными на них элементами проходят последовательно над волной припоя, при этом обеспечивается пайка выводов к контактным площадкам. Скорость перемещения платы должна быть такой, чтобы от соприкосновения соединения с волной и выхода из нее обеспечивалась качественная пайка; припой хорошо растекался в зазор между выводом и монтажным отверстием и не образовывались наплывы и сосульки на поверхности пайки. Платы устанавливают и крепят в специальные рамки, которые перемещаются транспортером. Места, не подлежащие пайке, закрываются защитной маской.
Движение плат под углом устраняет выброс припоя на обратную сторону через зазоры в монтажных отверстиях и уменьшает вероятность образования припойных сосулек. Перед пайкой поверхность плат обрабатывают пеной спирто-канифольного флюса. После пайки остатки флюса удаляют.
Пайка погружением и пайка волной припоя используется при штыревом монтаже.
При поверхностном монтаже осуществляют групповую пайку с использованием припойных (паяльных) паст. Паяльные пасты наносятся на контактные площадки ПП трафаретным способом. Навесные элементы устанавливаются на пасту, которая их фиксирует и удерживает от смещения. Далее в инфракрасной печи проводится общий нагрев ПП и осуществляется пайка.
Наиболее часто применяемые для электрического монтажа ЭВМ мягкие припои представляют из себя оловянно-свинцовые сплавы с добавками других металлов. Наиболее широко применяют припои ПОС-40, ПОС-61.
Припой ПОС-40 – почти 40% олова, почти 60% свинца и небольшое количество примесей (сурьма, индий, никель), температура плавления 2350C, температура пайки 2500C.
Припой ПОС-61 – 61% олова, 38% свинца, 0.8% сурьмы; температура плавления 1830C, температура пайки до 2400C.
Флюс – неметаллический материал, который создает предпосылки для прочной связи паяемых материалов.
По составу флюсы подразделяются на три типа:
-
Кислотные; -
Коррозионно-активные; -
Канифольные и канифольно-активированные.
Первая и вторая группа флюсов характеризуется тем, что их остатки вызывают коррозию. Сильно активные флюсы содержат хлористые соли – хлориды цинка, аммония и т.п.
Одним из наиболее широко применяемых компонентов низкотемпературных флюсов является канифоль. Она имеет низкую температуру плавления, легко растворяется во многих органических растворителях, не оказывает коррозионного действия на металлы. Как флюс канифоль относительно слабо активна, если применяется без каких-либо добавок. При перегреве канифоль темнеет, в ней происходят химические реакции, и она частично теряет флюсующую способность.
Типичный состав флюса для электроники – канифоль 20…25%, салициловая кислота 5%, этиловый или изопропиловый спирт.
Пайку твердыми припоями обычно проводят в атмосфере водорода без флюсов. В качестве твердых припоев используют сплавы на основе серебра, золота, железа, меди, никеля, цинка и др. Твердые припои обеспечивают прочные и чистые швы, высокую электропроводность соединения, используются для пайки трансформаторов, разъемов.
4 Защита мест соединения от коррозии
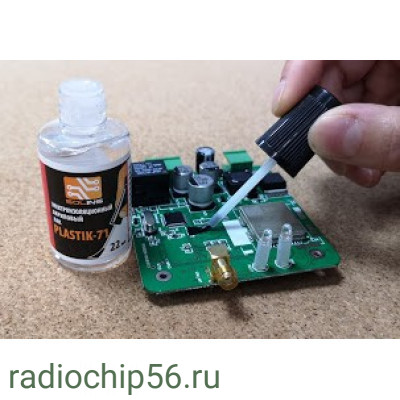
Рисунок 5 –Защита печатных плат от коррозии
Новая эра защитных покрытий.
Современная электроника становится более портативной и чрезвычайно сложной, чем когда-либо. Плотность монтажа повышается, прочность компонентов снижается по причине их малогабаритности. В связи с этим остро встает вопрос по защите печатных узлов от таких загрязнений, как влага, сульфаты (сера), наслоения пыли и грязи. Без должной защиты чувствительные компоненты быстро коррозируют, что приводит к коротким замыканиям, ухудшениям рабочих параметров и поломке устройств.
Для защиты поверхности монтажного основания и компонентов от внешних факторов окружающей среды, таких как влага, повышенная температура, пыль, отпечатки пальцев, загрязнения, химические и механические воздействия, электромиграция используются различные типы покрытий (некоторые из них называют конформными покрытиями). Такая защита помогает предотвратить коррозию, утечку тока или появление плесени и, следовательно, позволяет увеличить срок службы оборудования и повысить его надежность. Конформные покрытия обладают отличной адгезией, практически незаметны и повторяют форму печатного узла.
При выборе защитного покрытия учитывается множество факторов: условия эксплуатации конечного прибора, особенности топология платы и используемых комплектующих, диэлектрическая прочность покрытия, ремонтопригодность и возможность модификации платы после нанесения покрытия.
Существующие покрытия.
Конформные покрытия производятся на основе акрила, парилена, силикона, уретана и имеют различные методы нанесения, такие как погружение, распыление, нанесение кистью, струйный облив. Дальнейшее отверждение может происходить под воздействием УФ-облучения, сушки в шкафу или другими методами.
Традиционные методы покрытий хорошо себя зарекомендовали, однако они были созданы для элементной базы прошлого поколения. Современные печатные узлы характеризуются малым шагом выводов, использованием сложных корпусов, высокой плотностью расположения компонентов. Для элементов с миниатюрным форм-фактором покрытия типа эпоксидных или силиконовых могут оказаться слишком тяжелыми и создавать неблагоприятные механические напряжения. Полиуретановые покрытия являются более универсальными, но их не ремонтопригодность и необходимость маскирования создают излишние технологические проблемы.
Для решения вышеперечисленных проблем компания 3М предлагает покрытие нового поколения на основе фторполимеров. Этот специальный класс защитных жидкостей – NovecElectronicGradeCoatings – представляет собой прозрачные жидкости малой вязкости и с низким поверхностным натяжением. Активным веществом таких жидкостей являются фторированные полимеры в сегрегированных гидрофторэфирных растворителях.
Свойства фторполимеров
Фторполимер – это полимер на основе фторированного углеводорода с сильными фторуглеродистыми связями. Фтор во фторполимере электрически отрицателен и практически не связывается с другими материалами. Это и придает фторполимеру уникальные свойства отталкивания, поэтому первое популярное применение фторполимеров – это антипригарные покрытия.
Фторполимерные покрытия для электроники.
Для электронной промышленности фторполимеры также обладают набором привлекательных свойств. Во-первых, они вообще не имеют свойств липкости, во-вторых, они сильно уменьшают трение и противодействуют коррозии. Также, фторполимеры выдерживают воздействие очень высоких температур, являются отличными изоляторами (не проводят электричество), не поглощают влагу. В результате, применение фторполимерных покрытий значительно увеличивает срок эксплуатации электронных изделий.
Такие покрытия предназначены для оборудования, требующего очень высокой надежности, где необходима стойкость к водомасляным жидкостям и силикону, стойкость к микробиологическим атакам, сверхнизкая диэлектрическая константа, сверхнизкий коэффициент миграции ионов и способность выдерживать атмосферные воздействия.
Разберем основные свойства защитных покрытий для печатных плат на основе фторполимеров.
1. Фтор имеет самую высокую электроотрицательность среди всех химических элементов. При объединении с полимерной цепью атомы фтора значительно укрепляют ее, поскольку расстояние углеродофторных связей очень мало и достаточно сильно (477 кДж/моль). Это химическое свойство обеспечивает стойкость покрытия к химическим воздействиям и отличную термостабильностьфтормолимеров.
Способность фторполимеров отталкивать нежелательные химические воздействия тестировалась на многомолекулярном спирте, хлорфениле и соли себациновой кислоты. Тест проводился методом погружения в течение 19 часов при температуре 100°С. После этого поверхность покрытия изучалась под электронным микроскопом. Другой тест определял способность покрытия к миграции металлов (в результате которой образуются дендриты), для этого его погрузили в загрязненную среду 1014Na+/кв.см. при влажности 95% и термоциклировании от 100 до -10°С. Следов миграции после 100 циклов продолжительностью 4 часа на цикл обнаружено не было. Для сравнения кремнийорганические покрытия (типа силиконовых) показали следы миграции уже после 8 циклов.