Файл: Забайкальский институт железнодорожного транспорта филиал Федерального государственного бюджетного образовательного учреждения высшего образования Иркутский государственный университет путей сообщения.docx
Добавлен: 26.04.2024
Просмотров: 32
Скачиваний: 1
ВНИМАНИЕ! Если данный файл нарушает Ваши авторские права, то обязательно сообщите нам.
2. Фторполимеры обладают самым низким поверхностным натяжением среди всех существующих конформных покрытий. Именно это свойство придают поверхности отталкивающие свойства.
Поверхностное натяжение определяет степень смачиваемости поверхности. Если на поверхность нанести каплю жидкости, то угол образовавшейся капли-сферы будет характеризовать степень смачиваемости. Чем меньше угол, тем лучше растекание жидкости. Поэтому водоотталкивающие поверхности должны иметь максимально больший угол контакта. Для фторполимерных жидкостей он составляет 105 градусов для воды и 65 градусов для гексадекана.
При контакте с покрывным материалом (особенно после 15-минутной температурной выдержки при 100°С) определенные фторполимеры перестраивают свою микроструктуру для минимизации разницы в поверхностной энергии между покрытием и подложкой. Это обеспечивает хорошую адгезию покрытия к практически любым материалам, включая медь, эпоксидку, стеклоткань.
3. Растворимость фторполимеров составляет 11,4 Дж/см.куб. Максимально приближенный к этому значению растворитель серии 7100 производства 3М пока достигает 11,6 Дж/см.куб. при условии сохранения следующей пропорции: 2% фторполимера и 98% растворителя 7100. Поэтому некоторые производители фторполимерных покрытий (например, Nordson) использует именно растворитель производства 3М 7100.
4. Отличная долгосрочная стабильность фторполимерного покрытия объясняется силой связи C-F. Благодаря этому материал обладает высокой диэлектрической способностью и изоляционными свойствами (40кВ/мм), а также сохраняет стабильные влагозащитные свойства при многократных долговременных циклах изменения температуры и влажности. Этим обеспечивается долгосрочная защита печатных плат.
Топология печатной платы.
На плате могут располагаться компоненты, которые не подлежат обработке защитными покрытиями, это могут быть соединители, контактные ламели, потенциометры или другие элементы управления. Обычно такие компоненты располагаются по краям платы и требуют использовать маскирующих материалов.
Однако жидкость 1700 можно использовать и для печатных плат с предустановленными на них разъемами. Если контакты разъемы являются ножевыми, то в результате сочленения ответной части слой пленки будет легко удален и контакт восстановлен. Материал имеет малую механическую прочность, поэтому легко удаляется простым трением, что устраняет необходимость в маскировании таких компонентов, как переключатели, разъемы, пьезоэлектрические излучатели.
Кроме того, жидкость 1700 можно удалить с помощью растворителя (7100).
Ремонтопригодность.
Если узел требует ремонта, то критичным вопросом является простота удаления покрытия. Важное преимущество покрытия 1700 – это возможность доработки платы даже после нанесения защитного слоя. Слой пленки очень тонкий и без дополнительной очистки можно проводить пайку и выпайку компонентов с нанесенным покрытием Novec 1700.
Методы нанесения.
Нанести жидкость 1700 можно различным способом. При этом любой способ обеспечит точность нанесения, повторяемость и селективность. Она не требует высокотемпературной обработки, при необходимости ее можно легко удалить. Способы нанесения:
– погружение;
– распыление;
– капельный метод;
– капиллярный метод;
– нанесение кистью.
Нанесение методом погружения позволяет покрыть самые узкие места платы и компоненты нестандартной формы. При разной скорости подачи платы образуется разная толщина покрытия. Для уменьшения испарения рекомендуется использовать узкие резервуары с высокими бортами.
Нанесение методом распыления может выполняться вручную или селективно при помощи роботизированного оборудования. Автоматизированный способ позволит экономней использовать жидкость и наносить ее более равномерно с учетом геометрии поверхности.
Капельный метод позволяет точно контролировать расход материала при сохранении ручного метода нанесения.
Нанесение кистью использовать не рекомендуется по причине перекрестного загрязнения раствора. На волоски кисти могут попадать частицы с печатной платы. Также, будет сложно контролировать количество наносимого раствора.
Контроль нанесения покрытия.
Добавим несколько слов о технологическом процессе и контроле качества. Первый вопрос, с которым придется столкнуться технологу и мастерам – это отличие обработанных плат от необработанных. Решение задачи заключается в использовании различного типа маркировки. На черные корпуса микросхем можно наносить точечные пятна раствора, которые будут видны невооруженным глазом.
Если покрытие наносится на светлые участки и такая маркировка не очевидна, то покрытие можно увидеть под микроскопом или методом сравнения двух плат.
Тем не менее, такие визуальные и экспериментальные методы дают возможность увидеть просто факт наличия покрытия, но качество его нанесения не контролируется. Поэтому в качестве основного метода контроля рекомендуется использовать спектрометр (для моделей без УФ-добавок).
Еще один способ определить наличие нанесения – это тест на несмачиваемость масла. Высохшее покрытие будет отталкивать жидкости, минеральные масла, парафиновое масло и гексадекан. Такой тест можно также проводить при приемке печатных плат.
Толщина покрытия.
Традиционные конформные покрытия имеют толщину слоя в 25 микрон и выше. Покрытия 3М значительно тоньше. При нанесении методом погружения толщина покрытия может варьироваться от 0.1 до 1.3 микрон или от 1 до 6 микрон. При однократном покрытии распылением толщина слоя составит 1-6 микрон. Можно наносить несколько слоев для увеличения толщины защитного покрытия.
Тонкость покрытия имеет несколько преимуществ:
– электрический контакт можно осуществлять непосредственно через покрытие, устраняя необходимость в маскировании;
– превосходное покрытие сложных геометрических рельефов;
– улучшение термопрофиля при эксплуатации платы – тонкое покрытие не удерживает тепло.
5 Проверка работоспособности схем
Контроль и испытание печатных плат предназначены для определения качества изготовленных изделий, под которым понимают степень их соответствия требованиям чертежа, технических условий, отраслевых и государственных стандартов. Готовая продукция подлежит сертификации, согласно действующему законодательству.
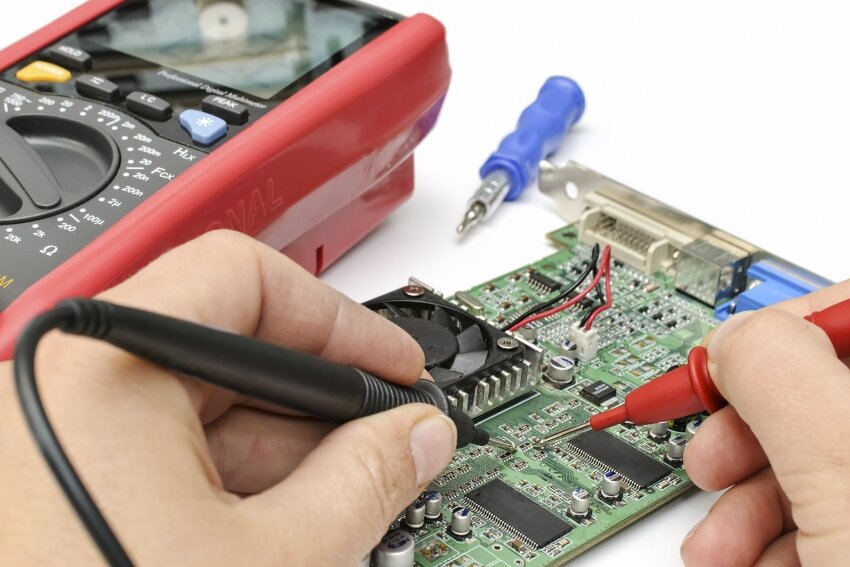
Рисунок 6 – испытание печатных плат
На повышение качества влияют:
-
Входной контроль исходных материалов и технологических сред; -
Строгое соблюдение режимов и последовательности операций процесса производства; -
Использование автоматизированного технологического оборудования со встроенными средствами активного контроля; -
Организация объективного пооперационного и выходного контроля; -
Проведение испытаний; -
Организация системы управления качеством.
Входному контролю подвергается каждая партия поступающего на производство диэлектрика, фоторезиста, трафаретной печатной краски. Особое внимание уделяется технологическим свойствам материалов. Проверяются и постоянно корректируются электрофизические и химические параметры используемых технологических сред на операциях травления, металлизации.
Операционный контроль качества проводится после наиболее ответственных технологических операций. Число контрольных точек определяется совершенством и стабильностью процесса. Тщательно проверяется качество фотошаблонов и сетчатых трафаретов, монтажных отверстий, межслойных соединений. На этих операциях стремятся использовать автоматизированное технологическое оборудование с системами управления и контроля. Высокая надежность операционного контроля сводит к минимуму число дефектных изделий на выходном контроле.
Основными видами выходного контроля ПП являются:
-
Контроль внешнего вида; -
Инструментальный контроль геометрических параметров и оценка точности выполнения отдельных элементов, совмещения слоев; -
Проверка металлизации отверстий и их устойчивости к токовой нагрузке; -
Определение целостности токопроводяших цепей и сопротивления изоляции.
Разрыв токопроводящих цепей обусловливается следующими причинами:
-
Подтравливанием печатных проводников, -
Наличием глубоких царапин на поверхности исходного материала, -
Возникновением внутренних напряжений при прессовании, -
Некачественной подготовкой поверхности отверстий перед металлизацией.
Устранить такие дефекты сложно, а на внутренних слоях практически невозможно. Несовмещение слоев при прессовании МПП вызывается избыточным давлением, непараллельностью плит пресса. Дефект не устраняется.
Геометрические параметры ПП:
-
Толщина, -
Диаметр отверстий, -
Расстояние между их центрами, -
Величина коробления, -
Габаритные размеры, -
Смещение отверстий относительно центраконтролируются с помощью стандартизованных инструментов для измерения линейных размеров.
Проверку металлизации монтажных отверстий проводят разрушающим или неразрушающим методом. При разрушающем методе изготавливают микрошлиф и по нему определяют толщину слоя, равномерность распределения металлизации, структуру покрытия, его пористость, наличие трещин, качество срастания с элементами печатного монтажа. Но длительность приготовления образцов ограничивает применение этого метода этапом отработки ТП. Экспрессную проверку качества металлизации проводят измерением омического сопротивления контактного перехода при подаче тока 1 А.
Калибровочный график и экспериментальные результаты изменения сопротивления от толщины слоя металлизации приведены на рисунке 7. Границей качественного и некачественного соединений является значение 500 мкОм, которое уточняется для каждого монтажного перехода. Разработанное программируемое оборудование позволяет измерять сопротивление в диапазоне 40...2000 мкОм с точностью ±1%. Время Контроля одного отверстия составляет 1 с.
Схема четырехзондового метода контактирования при измерении сопротивления металлизированного перехода | Зависимость сопротивления от толщины слоя металлизации отверстия в МПП толщиной 2мм |
![]() 3 - токовые электроды; 4- электроды напряжения | ![]() 1 - сопротивление отверстий с трещиной 0,7 мм на половину окружности; 2 - теоретическая кривая |
Рисунок 7 – Калибровочный график и экспериментальные результаты изменения сопротивления от толщины слоя металлизации
Калибровочный график и экспериментальные результаты изменения сопротивления от толщины слоя металлизации приведены на рисунке. Границей качественного и некачественного соединений является значение 500 мкОм, которое уточняется для каждого монтажного перехода. Разработанное программируемое оборудование позволяет измерять сопротивление в диапазоне 40...2000 мкОм с точностью ±1%. Время Контроля одного отверстия составляет 1 с.
Периодические испытания ПП и МПП проводятся с целью подтверждения их эксплуатационных характеристик, правильности выполнения ТП и соответствия конструкторской документации не реже одного раза в шесть месяцев. Для контроля случайным образом выбираются платы, прошедшие приемосдаточные испытания в количестве: 5 плат при опытном и мелкосерийном производстве и 10 плат при серийном производстве. В объем испытании входят:
-
Многократные изгибы ГПП и ГПК (ГПП должны выдерживать5-кратный цикл изгибов радиусом 10±0,5 мм, а ГПК - 150-кратный цикл изгибов радиусом 3±0,5 мм на 90° в обе стороны от исходного положения); -
Перепайка (5-10) отверстий и (5 - 10) контактных площадок, проверка паяемости (1-2 платы); -
Проверка омического сопротивления металлизированных отверстий (3 шт.) и их устойчивости к кратковременной токовой перегрузке; -
Проверка в нормальных климатических условиях целостности электрических цепей и сопротивления изоляции (но не менее чем на 5 парах проводников, в том числе цепей питания); -
Контроль внешнего вида, целостности соединений и сопротивления изоляции после воздействия климатических факторов, устанавливаемых в зависимости от группы жесткости испытаний по соответствующему стандарту.
Типовые испытания проводятся для определения эффективности внесенных изменений в конструкцию и технологию ПП. Программа испытаний составляется предприятием, изготавливающим ПП, и согласовывается с разработчиком.
Заключение
Прохождение учебной практики является важным элементом учебного процесса по подготовке специалиста в представленной области. Во время её прохождения будущий специалист применяет полученные знания, умения и навыки на практике.
В настоящее время кардинальным путем снижения объемов и стоимости технического обслуживания электрооборудования, численности обслуживающего и ремонтного персонала осуществляется переход от предупредительного принципа, жесткой регламентации ремонтного цикла и периодичности проведения ремонтов к обслуживанию на основе нормативов планово-предупредительных ремонтов.