Файл: Курсовая работа способы измельчения сырья для производства полимерных композиционных материалов.docx
ВУЗ: Не указан
Категория: Не указан
Дисциплина: Не указана
Добавлен: 05.02.2024
Просмотров: 24
Скачиваний: 0
ВНИМАНИЕ! Если данный файл нарушает Ваши авторские права, то обязательно сообщите нам.
б-с консольным валом и головкой в виде полого конуса: 1-тарелка; 2-корпус; 3-пологий конус; 4-пружина; 5-станина; 6-шаровой подпятник
Конусная дробилка с навесным валом и головкой в облике крутого конуса – состоит из внешнего конуса 1, внутри которого расположен подвижный дробящий конус 2, поставленный на валу 9, подвешенном на сферической опоре 4. Нижний конец вала 9 бегло вмонтирован в эксцентриковый стакан 5, который получает вращение от шкива 6 сквозь зубчатую передачу 7. Благодаря наличию стакана геометрические оси внешнего и внутреннего конусов не совпадают, а имеют только совместную точку соприкосновения в пространстве подвеса. В результате этого при вращении стакана 5 ось вала 9 совершает радиальное, или гирационное качание. Совместно с валом радиальные качания совершает и дробящий конус. Он не вертится принудительно от приводного механизма машины, а лишь только катится по внутренней плоскости внешнего конуса; при приближении к нему материал измельчается, а при отдалении от него – опускается вниз к разгрузочному отверстию. Материал загружается в дробилку через воронку 3, а размельченный продукт выходит либо по наклонному желобу 8 с боковой стороны, либо под дробилку, понижая ее высоту при этом предотвращается забивание ее материалом [6].
Конусная дробилка с консольным валом и головкой в облике полого конуса (грибовидная дробилка) – отличается от описанной раньше формой головки и корпуса. Корпус 2 в виде конуса, расширяющийся в сторону, что и пологий конус 3 дробящей головки, при этом их стенки на конкретной длине параллельны и образуют узкую щель (зону параллельности). Корпус 2 связан, и станина 5 амортизируется пружинами 4, расположенными по периметру корпуса. Ведущий вал дробилки установлен консольно и опирается на шаровидный подпятник 6; на верхнем конце вала установлена тарелка 1, с которой кусочки материала равномерно сбрасываются в дробилку при качаниях вала. Степень измельчения регулируется подъемом или опусканием корпуса.
Коротко конусные дробилки с большей зоной параллельности и большим углом наклона конуса применяют для мелкого измельчения.
Плюсы конусных дробилок: высочайшая производительность непрерывности измельчения материала в одно и тоже время раздавливанием и изгибом; размеренная, уравновешенная работа; высокий уровень измельчения.
-
Валковая дробилка
Из двух параллельно находящихся гладких или же зубчатых цилиндрических валков 1 и 2,состоит валковая дробилка. Они расположены в станине 3 машины и крутятся навстречу друг другу. При вращении они захватывают поступающий сверху материал и дробят его раздавливанием.
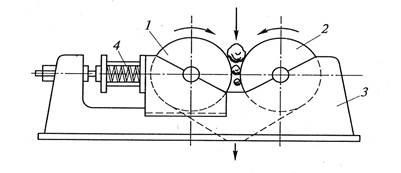
Рисунок 3 – Схема валковой дробилки
1,2-цилиндрические валки; 3-станина; 4-пружина
Чтобы предохранить валки от аварии в случае попадания в них кусков более жестких материалов валок 1 устанавливается в подвижных подшипниках и удерживается в данном положении мощью пружин 4, которые при увеличении давления дают возможность валку отступать налево. Степень измельчения валковой дробилки не больше 10 и регулируется изменением расстояния между валками. В зависимости от качеств начального материала степень измельчения составляет i = 10...15 для зубчатых и i = 3...8 для гладких валков [6].
-
Молотковые дробилки
Машины ударного воздействия применяются для измельчения малоабразивных материалов. В корпусе 1 дробилки, футерованном броневыми зубчатыми плитами 2, на горизонтальном вращающемся валу 3 надеты диски 4 с шарнирно закрепленными на них ударными молотками 5. Материал подающий через загрузочное отверстие 7, подхватывается молотками, частично разбивается ими на лету и измельчается ударом о плиты корпуса. Размельченный материал высыпается из машины через колосниковую решетку 6. Конечный размер измельчаемого материала ориентируется размером отверстий разгрузочной решетки.
Молотковые дробилки различают по количеству, по месторасположению молотков в одной или нескольких плоскостях.
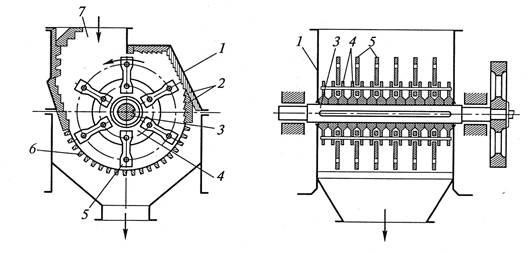
Рисунок 4 – Схема молотковой дробилки
1-корпус; 2-зубчатые плиты; 3-вал; 4-диск; 5-молоток; 6-колоснковая решетка; 7-загрузочное отверстие
-
Дезинтегратор
Состоит из 2-ух дисков 1 и 2, закрепленных на соосных валах 5 и 9. Диски вращаются в обратных направлениях от шкивов 6 и 8. На дисках по концентрическим окружностям находятся пальцы (била) 3. Каждый ряд пальцев 1-ого диска находится с маленьким зазором между 2-мя рядами пальцев другого диска [6].
В дезинтегратор материал поступает с боковой стороны через питатель 4 и дробится ударами быстровращающихся пальцев. Размельченный материал выходит через разгрузочный конус 7.
Плюсы дезинтеграторов – это простота и компактность прибора, высокая производительность и степень измельчения материала, надежность в работе.
Недостатки – быстро изнашиваются закрепленные пальцы; много пыли;большие затраты энергии.
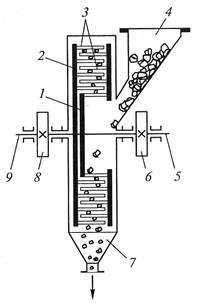
Рисунок 5 – Схема дезинтегратора
1,2-диски; 3-пальцы;4-питатель; 5,9-соосные валы; 6,8-шкивы; 7-разгрузочный конус
-
Барабанные мельницы
Самые известные машины это- барабанные мельницы, которые применяются для грубого, среднего, тонкого и сверхтонкого измельчения. Они относятся к машинам ударно-истирающего процесса и разделяются на мельницы с вращающимся барабаном, вибрационные и центро6ежныe [6].
Вращающаяся барабанная мельница – представляет собой крутящийся барабан 1, в который помещены дробящие тела, т. е. шары 2 и измельчаемый материал. При вращении барабана шары и материал под воздействием трения и центробежной силы поднимаются до определенной высоты, а за тем падают и скатываются вниз. От этого происходит измельчение материала.
Крутящиеся барабанные мельницы работают как периодически, так и беспрерывно.
Эти мельницы работают только если влажность измельчаемого материала меньше 5 %. Если влага измельчаемого материала 8...15 % мельница перестает работать так как материал будет налипать на шары. Но если будет 20 ... 30 % и выше, мельница возобновит работу, даже еще лучше, чем когда вещества сухие.
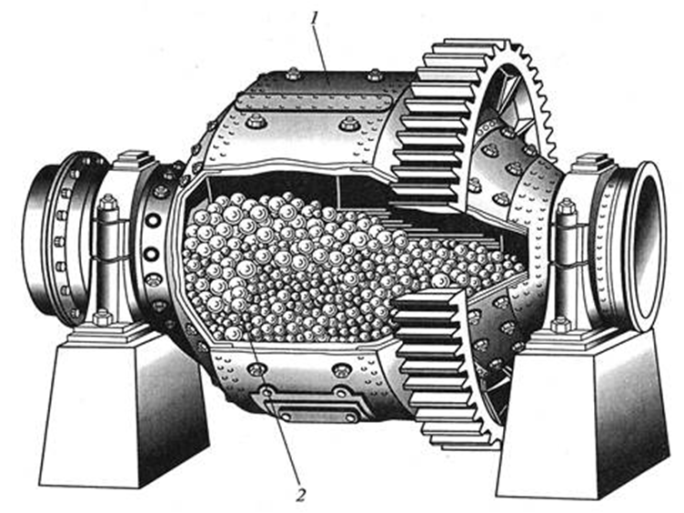
Рисунок 6 – Барабанная мельница
1-барабан; 2-шары
Шаровые мельницы универсальны. У них равномерная степень измельчения. Долговременный период работы. Надежность, защищенность и простота в обслуживании [6].
Недостатки шаровых мельниц – очень большие и тяжелые; невысокий КПД; изнашивание шаров и загрязнение материала продуктами изнашивания, шум во время работы.
-
Коллоидные измельчители
Измельчают изделия размером менее микрона и обязательно влажным способом.
Коллоидный измельчитель состоит из корпуса с коническим гнездом и ротор. Между конической поверхностью корпуса и поверхностью ротора обязательно есть зазор для подачи суспензии, который равен долям мм, в нем твердые частички стираются [6].
-
Бегуны
Используют для маленького и тонкого дробления материалов податливых пород средней твердости. Бегуны разделяются по главным признакам:
По способу действия: периодического и непрерывного.
По технологическому назначению:
-
Для измельчения и смешивания и только перемешивания; -
Для брикетирования сырьевой смеси; -
Бегуны с металлическими катками и чашей; -
Бегуны с каменными катками и чашей.
По конструктивному оформлению:
-
Неподвижная чаша; -
Вращающаяся чаша; -
С верхним приводом; -
С нижним приводом.
При нижнем приводе дольше разборка и больше времени занимает починка, но масса не загрязняется. Катки опираются на материал собственной массой с добавочным гидравлическим, пневматическим или же с пружинным нажатием[7].
По способу разгрузки:
-
Ручная разгрузка; -
Продавливание через решетку; -
Центробежная разгрузка; -
Разгрузка по опускающемуся в чашу отвалу.
В бегунах с вращающимися катками вокруг вертикальной оси центробежные силы пытаются сорвать катки, и если центральный вал не уравновешен то он может согнуться.
Плюсы бегунов:
можно разгружать сразу большие куски материала;
легко регулировать тонкость измельчения;
становятся более пластичными глинистые материалы.
Недостатки бегунов:
большой размер;
сложный ремонт;
большой расход энергии.
-
Криогенное измельчение
Размольный стакан постоянно охлаждается жидким азотом при поддержке интегрированной системы замараживания как до и во время измельчения. Благодаря этому образец делается хрупким и летучие составляющие сберегаются. Жидкий азот перемещается в системе охлаждения и постоянно восполняется при помощи системы самодействующего заполнения в числе строго подходящем для поддержания температуры -196°С [7].
Мощное действие удара и трения ведет к отличной эффективности измельчения. Система автоматического заполнения исключает прямой контакт с жидким азотом и делает работу с мельницей очень безопасной. Ее универсальность (криогенное, а также сухое и мокрое измельчение при комнатной температуре) делает CryoMill безупречной мельницей для проб объемом до 20 мл.
Достоинства:
1. Мощное криогенное измельчение при помощи сил удара и трения, скорость до 30 Гц;
2. Три различных типа измельчения (криогенное, а также сухое и мокрое при комнатной температуре);
3. Закрытая система автоматического заполнения исключает любой контакт пользователя с жидким азотом для абсолютной безопасности работы;
4. Размольные стаканы с завинчивающейся крышкой для измельчения без потери вещества;
5. Широкий выбор добавочных принадлежностей, в том числе разные системы подачи жидкого азота, размольные стаканы и шары различного размера, которые выполнены из разных материалов, адаптеры для пробирок;
6. Малое потребление жидкого азота;
7.Ясно структурированный интерфейс встроенного программного обеспечения, встроенная память для хранения до девяти вариантов параметров измельчения;
8. Программируемые циклы охлаждения и измельчения (от 10 с до 99 мин);
9. Возможно измельчение в керамических размольных стаканах [7].
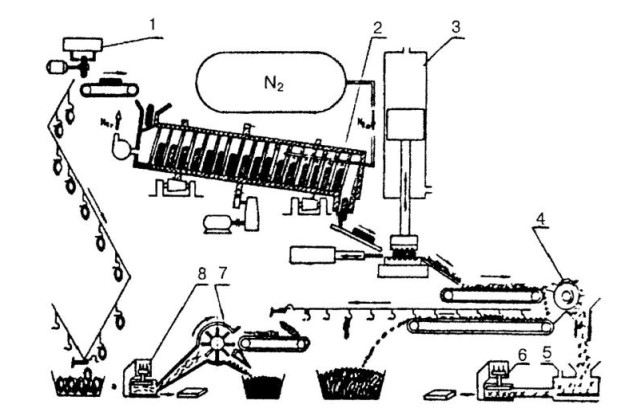
Рисунок 7 – Схема криогенного дробления изношенных покрышек
1-универсальная борторезка; 2-охлаждающая камера; 3-молот; 4-железоотделитель шкивной; 5-обжиговая печь; 6-пресс пакетирования металла; 7-роторный измельчитель; 8-пресс пакетирования текстиля
-
Степень измельчения, прочность и хрупкость
Степень измельчения – отношение среднего объема частиц начального материала к средней величине размельченного материала. По объемам (дисперсности) возникающих частиц отличаются 5 классов измельчения от большого до коллоидного. По объему (крупности) размельченного продукта различают: грубое (300-100 мм); среднее (100-25 мм); мелкое (25-1 мм).
«Чем меньше степень измельчения, тем выше прочность»
Прочность – свойство твердого материала сопротивляться разрушению под воздействием внешних нагрузок. Обычно прочность твердых материалов оценивается пределом прочности при сжатии[6].
Хрупкость – свойство твердого материала рушиться без заметных пластических деструкций. По количеству ударов, выдерживаемых образцами, твердые материалы разделят на: очень хрупкие (до 2); хрупкие (2…5); вязкие (5…10); очень вязкие (более 10).