Файл: Курсовая работа способы измельчения сырья для производства полимерных композиционных материалов.docx
ВУЗ: Не указан
Категория: Не указан
Дисциплина: Не указана
Добавлен: 05.02.2024
Просмотров: 23
Скачиваний: 0
ВНИМАНИЕ! Если данный файл нарушает Ваши авторские права, то обязательно сообщите нам.
Курсовая работа
«СПОСОБЫ ИЗМЕЛЬЧЕНИЯ СЫРЬЯ ДЛЯ ПРОИЗВОДСТВА ПОЛИМЕРНЫХ КОМПОЗИЦИОННЫХ МАТЕРИАЛОВ»
СОДЕРЖАНИЕ
Введение 2
1Полимерные композиционные материалы 3
2Измельчение 5
2.1Дробление 5
2.2Помол 6
2.3Резка 7
2.4Пилы 7
3Измельчающее оборудование 8
3.1Щёковые дробилки 8
3.2Конусные дробилки 10
3.3Валковая дробилка 12
3.4Молотковые дробилки 12
3.5Дезинтегратор 13
3.6Барабанные мельницы 14
3.7Коллоидные измельчители 16
3.8Бегуны 16
4.9Криогенное измельчение 17
4Степень измельчения, прочность и хрупкость 19
Заключение 20
В настоящее время ПКМ широко используется. Для них подбирают агрегаты для измельчения. Выбор оборудования огромный: дробилки разных видов, бегуны, мельницы, измельчители, так как у них разный принцип действия и объем. Чтобы выбрать, нужно учитывать главные качества ПКМ – это прочность, хрупкость и степень измельчения. 20
Список использованной литературы 21
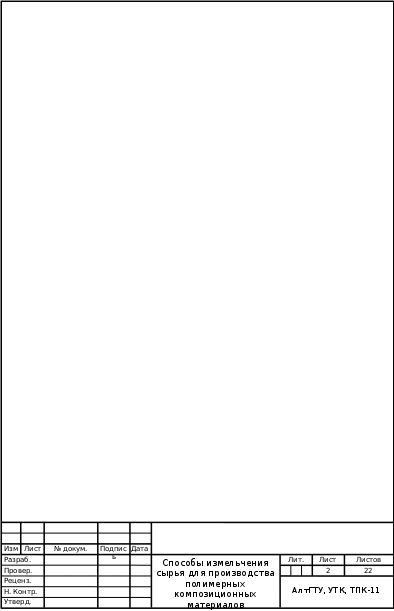
Введение
В настоящее время полимерные композиционные материалы (ПКМ) находят широкое использование. ПКМ – это гетерогенные системы, которые состоят из двух или более элементов, кроме того одни из элементов выступают армирующими составляющими, а другие – связующими их полимерными матрицами.
Для хорошей реализации всего комплекса свойств ПКМ надо сделать крепкое взаимодействие матрицы и волокна по всей площади их контакта. Добиться такового абсолютно непросто, например как это взаимодействие находится в зависимости от большого количества моментов и, в частности, от состава связывающего, строения волокна, технологии изготовления композиционного материала.
Для ПКМ подбирают оборудование для измельчения. Это довольно сложно, ведь его не мало. Это и измельчители, и дробилки, и бегуны, и мельницы.
Самое главное, что важно для ПКМ – это степень измельчения, хрупкость материала, а также прочность. От прочности материала зависит, какое будет изделие.
-
Полимерные композиционные материалы
ПКМ называются подобные материалы, у каких матрицей является полимер, образованный на базе какого-либо связывающего (смолы и т. п.).
Механические, физические и химические характеристики полимеров зависят от их внутреннего строения и физического состояния. При разработке полимерных композиционных материалов начальные полимерные материа¬лы могут употребляться в чистом виде (порошки, гранулы, листы, пленки) либо в качестве связывающих, армированных композиционных материалов.
Полимерное связующее представляет собой двух- или же многокомпонентную систему, состоящую из синтетической смолы и отвердителей или же организаторов, катализаторов, ускорителей отверждения. От полимерной матрицы находятся в зависимости теплостойкость и гидростойкость, стойкость к агрессивным средам, прочностные, диэлектрические и другие свойства ПКМ [1].
По типу матриц композиционные материалы разделяют на три класса:
-
Полимерные; -
Металлические; -
Керамические.
Наполнитель как один из компонент играет ведомую роль в формировании ведущих данных композиционных материалов. Наполнение – это сочетание полимеров с жесткими, водянистыми или же газообразными препаратами, которые сравнительно размеренно распределяются в размере возникающей композиции и имеют точно воплощенную границу раздела с нескончаемой полимерной фазой (матрицей).
Наполнители пользуют для улучшения эксплуатационных качеств композиционных материалов (прочности, жесткости, теплостойкости), придания им различных своеобразных качеств и понижения цены. От наполнителя в большой степени находятся в зависимости технологические качества композитов и способности их переработки в изделия. К безупречному наполнителю предъявляются особенные требования, которые в одном наполнители соединять довольно непросто:
-
Высокая прочность; -
Высокая степень физико-механических свойств; -
Низкое водопоглощение; -
Хорошая смачиваемость; -
Отсутствие вредоносных примесей; -
Низкая стоимость; -
Высокая химическая выносливость и термостойкость; -
Негорючесть; -
Доступность предания конкретных формы и величин частиц; -
Хорошая диспергируемость.
Наполнители обязаны отлично сочетаться с полимером или же диспергироваться в нем с образованием однородной композиции. Они не обязаны менять собственные свойства при хранении, переработке и использования. Когда один наполнитель не соответствует всем требованиям, то в композиционный материал вводят немного наполнителей. Нередко вводятся наполнители различных видов и составов. Подбором которые соответствуют наполнителей можно регулировать химическую выносливость, теплостойкость, тепло- и электропроводность, плотность и другие параметры композиционных материалов [2].
-
Измельчение
Под измельчением подразумевается механизм разрушения кусков твердого материала до заданных величин, которые необходимы для промышленного использования продукта измельчения.
-
Дробление
Дробление полимерных отходов — это измельчение и сокращение формы и размера материала, а также гомогенизация струи сырья; в то же время — это шаг переработки для дальнейшего применения материала. От разновидности форм, величин и своеобразных особых качеств пластмасс, которые поступают на размельчение (пленки, контейнеры, бутылки, канистры и т. д.), зависит и разновидность дробилок. Принципиально верно выбрать оснащение для резки конкретных материалов. Частицы раздробленной массы классифицируются по величине следующим образом измельчения:
-
Грубое: > 20 мм; -
Среднее: от 1 мм до 20 мм; -
Тонкое: от 20 мкм до 1 мм; -
Самое тонкое: < 20 мкм.
Измельчение происходит механическим способом на режущих, ударных и прессовальных машинах. Измельчительная техника зависит от качества пластмасс, которые нужно переработать. Чтобы добиться нужного объёма частиц, важно учитывать:
-
Твердость; -
Аффектацию к теплу; -
Упругость [4].
-
Помол
При «помоле» начальным материалом считается продукт, возникающий при дроблении. В итоге помола величина частиц конечного изделия оформляет 0,1-0,3мм. Нужно обозначить, собственно что помол применяется гораздо пореже, чем дробление и используется в ведущем в процессах получения композиционных материалов, к примеру ПВХ-композиций, порошка вулканизованной резины, а еще в процессах получения различных полимерных консистенций, в которых потребуется не плохое распределение разнородных составляющих в процессе смешения. Помол по сравнению с дроблением представляет собой гораздо намного затратный процесс, как капитальных, так и эксплуатационных расходов. Для помола используют мельницы. По системе и принципу действия различают следующие главные типы мельниц:
-
Барабанные; -
Ролико-маятниковые; -
Молотковые; -
Мельницы на подобии «Аэрофол»; -
Вибрационные; -
Струйные[5].
-
Резка
Основную часть полимерных отходов составляют термопласты – это довольно эластичные материалы, и потому сдвиговая резка, ударное воздействие, давление здесь не эффективны. В то время как резка справляется с этим великолепно. Для резки профилей, пленок и других полимерных отходов используются мельницы, измельчители, гильотинные резаки и пилы. А для жесткой резки тюков, пленочных рулонов и других больших объектов используется гильотинный резак. Часто эти машины используются для подготовительной резки перед обработкой с поддержкой иной резательно-измельчительной техники. Режущее напряжение может достигать 200-300кН. Измельчитель с режущими роликами (резаки и измельчители с дисковыми холодным оружием, резаки с 2-мя режущими роликами) – это машины, которые имеют параллельно находящиеся ролики с наточенными зубьями для разрыва. Ролики вертятся нерасторопно, но имеют большой вращающий момент. В машине может находиться, в зависимости от системы, до 6 параллельных валов с роликами. Величина частиц измельченного материала зависит от количества острых зубьев, их высоты и ширины роликов.
-
Пилы
Для резки пластмасс используются дисковые полотна из быстрорежущей стали или полотен с концевыми вставками из жестких металлов. Из-за маленькой теплопроводимости ПМ нужно обязательно при механической обработке обеспечить отвод тепла вместе со щепками или опилками. Термопласты недопустимо нагревать выше 60°С, а реактопласты — выше 150°С. Охладительные системы обязательно должны быть инертными по отношению к обрабатываемому материалу. Наилучшим способом для измельчения больших отходов являются пилы. Они используются для подготовительного измельчения любого вторсырья до переработки. С предоставленной задачей успешно справляется измельчитель или же например именуемые молотилки для пластика. Полимерные отходы неоднородны: это и полимерная пленка, ПЭТ бутылки, корпусные детали. Они различаются по механическим качествам и способы измельчения их разные. Пленку, к примеру, легко разрезать, но ударной методикой ее не размельчить. А вот ABS пластик, который чаще всего встречается в корпусных деталях, дробят ударным способом. От толщины сырья зависит выбор метода измельчения. В соответствии с этим, и молотилки для ПВХ отходов и ПЭ имеют ряд конструктивных индивидуальностей в зависимости от предназначения [5].
-
Измельчающее оборудование
-
Щёковые дробилки
Используется для измельчения крупных кусков материала. Дробилка состоит из неподвижной 1 и подвижной 2 щек, шарнирно подвешенной на оси 3. При качании она то близится к недвижимой щеке, то отдаляется от нее. Перемещения эти происходят при вращение вала 4, сообщающего возвратно-поступательное перемещение шатуну 11, соединенному с распорными плитами 10. Плиты шарнирно объединены с подвижной щекой 2 и распорными клиньями 6 и 7, допускающими менять ширину выпускной щели, а значит, и степень измельчения материала.
Измельчение твердого материала, подаваемого сверху, происходит во время сближения подвижной и неподвижной щек. При прохождении между ними внизу размер частиц измельченного продукта уменьшается. Движение подвижной щеки в момент холостого хода происходит под воздействием собственного веса и тяги 9 с пружиной 8 [6].
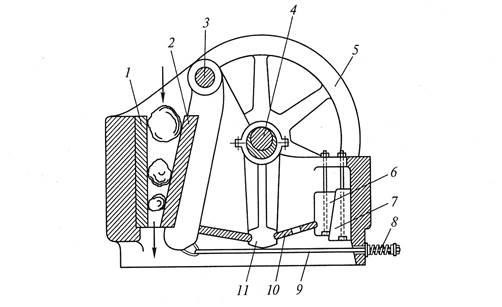
Рисунок 1 – Схема щековой дробилки
1,2-неподвижная и подвижная щеки; 3-ось; 4-вал; 5-маховик; 6,7-распорные клинья; 8-пружина; 9-тяга; 10-распорная плита; 11-шатун
Так как цикл работы щековой дробилки состоит из периодов измельчения (с расходом энергии) и холостого хода (без расходов энергии), нагрузка на приводной двигатель является неравномерной. И с целью выравнивания нагрузки вал 4 снабжен 2-мя маховиками 5, аккумулирующими энергию при холостом ходе и отдающими ее при рабочем ходе.
Плюсы щековых дробилок – простота и надежность конструкции, широкая область применения, компактность и легкость обслуживания.
Недостатки – периодический характер воздействия дробящего механизма и неуравновешенность передвигающегося материала, вызывают грохот и вибрацию.
-
Конусные дробилки
Используется для большого, среднего и маленького измельчения, они выделяются постоянным воздействием на дробимый материал дробящей поверхностью. Чаще всего используются 2 конусные дробилки [6].
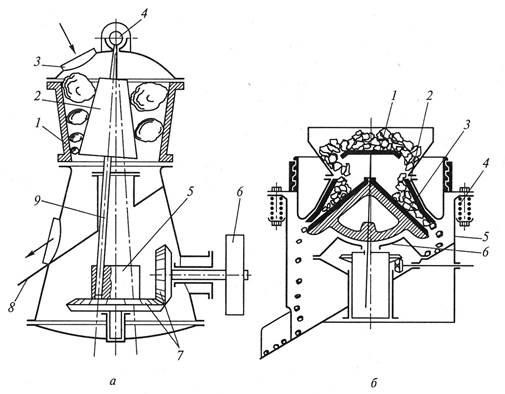
Рисунок 2 – Схемы конусных дробилок
а-с подвешенным валом и головкой в виде крутого конуса: 1-наружный конус; 2-подвижный конус; 3-воронка; 4-сферическая опора; 5-эксцентриковый стакан; 6-шкив; 7-зубчатая передача; 8-желоб; 9-вал;