Файл: Разработка технологического процесса изготовления корпуса воздухоохладителя компрессора.rtf
ВУЗ: Не указан
Категория: Не указан
Дисциплина: Не указана
Добавлен: 02.02.2024
Просмотров: 30
Скачиваний: 0
ВНИМАНИЕ! Если данный файл нарушает Ваши авторские права, то обязательно сообщите нам.
Размещено на http://www.allbest.ru/
МИНИСТЕРСТВО ОБРАЗОВАНИЯ И НАУКИ РЕСПУБЛИКИ ТАТАРСТАН
Государственное автономное профессиональное образовательное учреждение «КАЗАНСКИЙ ПОЛИТЕХНИЧЕСКИЙ КОЛЛЕДЖ»
Курсовой проект
Дисциплина: Основы расчета и проектирования сварных конструкций
Тема: «Разработка технологического процесса изготовления корпуса воздухоохладителя компрессора»
Выполнил студент
Закиров А.А.
Казань 2019 г.
Введение
сварка воздухоохладитель трубокомпрессорный химический
Целью данного курсовой работы является разработка технологии сварки обечайки корпуса воздухоохладителя, который является узлом трубокомпрессорной установки и служит для размещения системы охлаждения воздуха, состоящей из трубчатых элементов. Поступающий воздух омывает трубки, по которым циркулирует вода и охлаждается. Давление воздуха в корпусе не более 2 атм.
Конструкция является ответственной, поэтому при ее изготовлении применяются только материалы высокого качества. В этой курсовой работе рассмотрим возможность серийного производства данного изделия.
Промышленные воздухоохладители используются на атомных, тепловых и гидроэлектростанциях, промышленных предприятиях, предприятиях нефтегазового и агропромышленного комплекса и предприятиях других отраслей.
В процессе работы электрической машины нагревается циркулирующий воздух, который и надо охлаждать, для эффективной и безотказной работы электрической машины. С этой задачей успешно справляются воздухоохладители, устанавливаемые в систему охлаждения.
Существует два вида охлаждения компрессоров — воздушное и жидкостное. И тот и другой тип имеет преимущества и недостатки, которые определяют сферу их применения.
Основным конструкционным элементом системы воздушного охлаждения является вентилятор, который нагнетает воздух на корпус установки. В этом случае температура снижается за счет постоянного обдува агрегата. Отличительной особенностью воздушного охлаждения является сравнительно невысокая эффективность, сужающая сферу его применения.
Жидкостное охлаждение более эффективно по сравнению с воздушным. Воздухоохладитель пропускает через себя нагретый воздух и охлаждает его водой. Далее охлажденный воздухоохладителем воздух возвращается в систему охлаждения. Этим и объясняется сфера его применения — такой тип используют в составе мощных промышленных установок (чаще всего винтовых), выделяющих много тепловой энергии.
1. Основная часть
1.1 Назначение и описание конструкции
Воздухоохладитель – неотъемлемый элемент любого холодильного оборудования. Он представляет собой агрегат, теплообменные процессы в котором происходят через стенки труб. Изготавливаются трубки, как правило, из меди или ребра алюминия. Хладагент, который находится внутри трубки, постепенно испаряется, забирая тепло в камере, а затем всасывается в компрессор.
В процессе работы электрической машины нагревается циркулирующий воздух, который и надо охлаждать, для эффективной и безотказной работы электрической машины. С этой задачей успешно справляются воздухоохладители устанавливаемые в систему охлаждения. Воздухоохладитель пропускает через себя нагретый воздух и охлаждает его водой. Далее охлажденный воздухоохладителем воздух возвращается в систему охлаждения.
Воздухоохладитель состоит из сферических трубных элементов и корпуса. Корпус представляет собой цилиндр, состоящий из обечайки. К корпусу привариваются два фланца и две горловины.
Корпус воздухоохладителя является узлом трубокомпрессорной установки и служит для размещения системы охлаждения, состоящей из трубчатых элементов. Поступающий воздух омывает трубки, по которым циркулирует вода и охлаждается. Давление воздуха в корпусе не более 2 атм.
Основные данные:
Корпус
-
Габаритные размеры 1200х1754х1000 мм; -
общий вес конструкции 868 кг; -
Программа производства 750 штук в год.
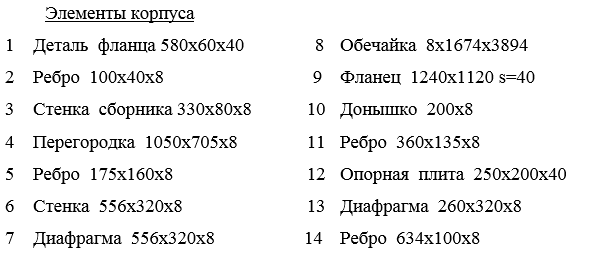
1.2 Выбор сварочных материалов и технические условия на них
Выбор материала в значительной степени определяет, как прочностные характеристики проектируемого изделия, так и технологические возможности последующего процесса его изготовления.
При выборе материалов для сварных конструкций необходимо учитывать не только его исходные свойства, но и его технологическую свариваемость – возможность получения сварного соединения требуемого качества из данного материала, с применением существующих технических средств, при наименьших затратах труда и времени.
В данной работе была выбрана сталь марки 12ХМ. Сталь 12ХМ обладает высокой жаропрочностью. Предназначена для эксплуатации в широком диапазоне температур, а именно от -40 до +5600 С. Но чаще применяется от +275 до +560
0С. Главные преимущества, которыми обладает сталь: достаточно низкая стоимость при высокой технологичности изготовления сварных конструкций, производстве отливок, а также использовании его как одного из биметаллов. Марка стали 12ХМ дает возможность уменьшения толщины листа, что соответственно способствует снижению веса конструкции.
Таблица № 1. Химический состав стали 12ХМ
C | Si | Mn | Ni | S | P | Cr | Mo | Cu |
0,09 % | 0,3 % | 0,7 % | 0,25 % | 0,025 % | 0,03 % | 0,6 % | 0,6 % | 0, 2 % |
1.3 Выбор способа сварки
Сталь 12ХМ обладает достаточно хорошей свариваемостью и выбор способов сварки очень широк. Используем как автоматическую дуговую сварку под флюсом, так и ручную дуговую сварку для проварки трудносвариваемых мест в корпусе воздухоохладителя. Для обеспечения наилучшей защиты металла шва от внешней среды и обеспечения глубокого проплавления и мелкозернистой структуры применяют автоматическую сварку под слоем флюса. Высокая тепловая концентрация энергии позволяет вести сварку с малой энергоемкостью процесса.
Механизм дуговой сварки под флюсом (ДСПФ) заключается в следующем: как электрод, так и металл основы расплавляются под слоем флюса. Данный слой защищает расплавленный металл от загрязнения и аккумулирует теплоту в точке соединения. Расплавленный флюс, поднимаясь через ванну, раскисляет и очищает расплавленный металл. В дальнейшем он образует защитную шлаковую оболочку и сохраняет наплавленный сварной шов.
Для автоматической сварки под флюсом применяют непокрытую электродную проволоку, а для защиты сварочной ванны и дуги от воздуха используют флюс. Перемещение и подача электродной проволоки полностью механизированы, а процессы зажигания дуги и заварки кратера в конце шва автоматизированы.
В ходе автоматической дуговой сварки под флюсом дуга проходит между основным металлом и проволокой. Металлическая ванна жидкого металла и столб дуги со всех сторон тщательно закрыты слоем флюса толщиной примерно 30 – 35 мм. Благодаря тому, что часть флюса расплавляется, вокруг дуги появляется газовая полость, а на поверхности расплавленного металла – ванна жидкого шлака. Во время сварки под флюсом происходит глубокое проплавление основного металла. Очень быстрое движение электрода вдоль заготовки и действие мощной дуги способствуют оттеснению расплавленного металла в противоположную направлению сварки сторону. Производительность по сравнению с ручной сваркой увеличивается в 5—12 раз. При сварке под флюсом ток по электродной проволоке проходит только в ее вылете (место от токоподвода до дуги). Поэтому можно использовать повышенные (25—100 А/мм
2) по сравнению с ручной дуговой сваркой (10—20 А/мм2) плотности сварочного тока без опасения значительного перегрева электрода в вылете в отслаивания обмазки, как в покрытом электроде.
Использование больших сварочных токов, резко повышает глубину проплавления основного металла И появляется возможность сварки металла повышенной толщины без разделки кромок. При сварке с разделкой кромок уменьшается угол разделки и увеличивается величина их притупления, т. е. уменьшается количество электродного металла, необходимого для заполнения разделки. Металл шва обычно состоит приблизительно на 2/3 из переплавленного основного металла (при ручной дуговой сварке соотношение обратное). В результате вышесказанного растут скорость и производительность сварки. Под флюсом сваривают металл толщиной 2 - 60 мм при скорости однодуговой сварки до 0,07 км/ч. Применение многодуговой сварки позволяет повысить ее скорость до 0,3 км/ч.
Высокое качество металлов шва и сварного соединения достигается за счет надежной защиты расплавленного металла от взаимодействия с воздухом, его металлургической обработки и легирования расплавленным шлаком. Наличие шлака на поверхности шва уменьшает скорость кристаллизации металла сварочной ванны и скорость охлаждения металла шва В результате металл шва не имеет пор, содержит пониженное количество неметаллических включений. Улучшение формы шва и стабильности его размеров, особенно глубины проплавления, обеспечивает постоянные химический состав и другие свойства па всей длине шва. Сварку под флюсом применяют для изготовления крупногабаритных резервуаров, строительных конструкций, труб и т.д. из сталей, никелевых сплавов, меди, алюминия, титана и их сплавов.
Экономичность процесса определяется снижением расхода сварочных материалов за счет сокращения потерь металла на угар и разбрызгивание (не более 3 %, а при ручной сварке достигают 15%), отсутствием потерь на огарки. Лучшее использование тепла дуги при сварке под флюсом по сравнению с ручной сваркой уменьшает расход электроэнергии на 30—40 %. Повышению экономичности способствует и снижение трудоемкости работ по разделке кромок под сварку, зачистке шва от брызг и шлака. Сварка выполняется с применением специальных автоматов или полуавтоматов. Условия работы позволяют сварщику обходиться без щитков для защиты глаз и лица. Повышаются общий уровень и культура производства.
Преимущества ручной дуговой сварки
-
возможность сварки в любых пространственных положениях; -
возможность сварки в местах с ограниченным доступом; -
сравнительно быстрый переход от одного свариваемого материала к другому; -
возможность сварки самых различных сталей благодаря широкому выбору выпускаемых марок электродов; -
простота и транспортабельность сварочного оборудования.
Недостатки ручной дуговой сварки
-
низкие КПД и производительность по сравнению с другими технологиями сварки; -
качество соединений во многом зависит от квалификации сварщика; -
вредные условия процесса сварки.
2. Технологический раздел
2.1 Выбор и обоснование выбора методов и способов сборки
Для изготовления корпуса воздухоохладителя выбираем стандартный лист 2500х4000х8мм ГОСТ 19903-74 и гильотинными ножницами отрезаем необходимые размеры, т. е. 1674х3897мм.
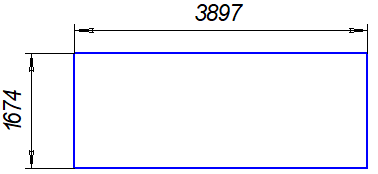
Рисунок 1. Лист изделия
Согласно ГОСТ 14115-85 изготавливаются ребра жесткости, благодаря плазменной резке.
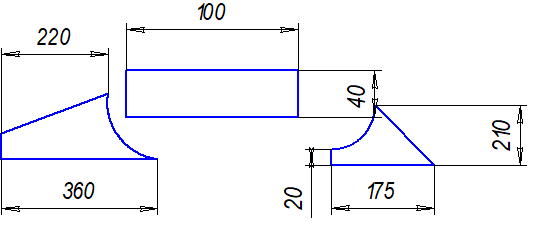
Рисунок 2. Ребра жесткости
Подготавливаются донышко и стенка сборника. Стенку сборника выбираем согласно ГОСТ 8696-74, а донышко получаем за счет плазменной резки.
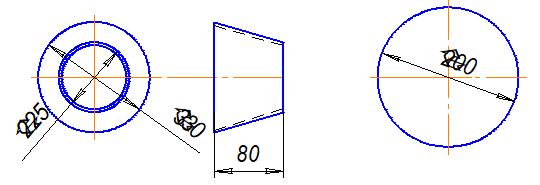
Рисунок 3. Стенка сборника и донышка
На гильотинных ножницах нарезаем диафрагмы для горловины и отрезается стенка 556х320х8.
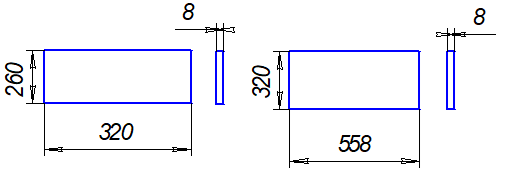
Рисунок 4. Диафрагма
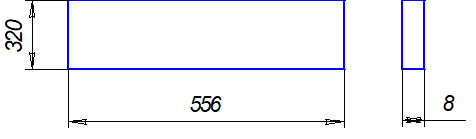
Рисунок 5. Стенка
Согласно ГОСТ 12820-80 выбираем фланец 640х640х40мм и сверлильным станком нарезаем в нем отверстия.
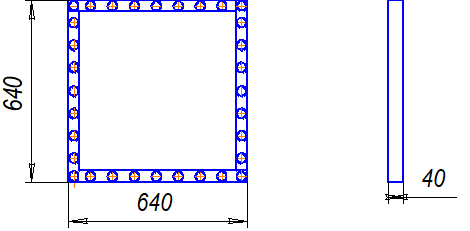
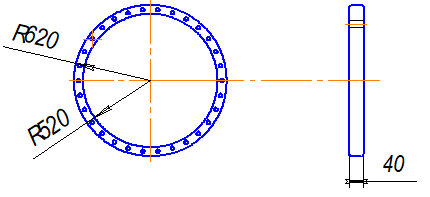
Рисунок 6. Фланец
Для корпуса воздухоохладителя изготавливается перегородка. Используются гильотинные ножницы и плазменная резка и валцевание листа для обечайки.
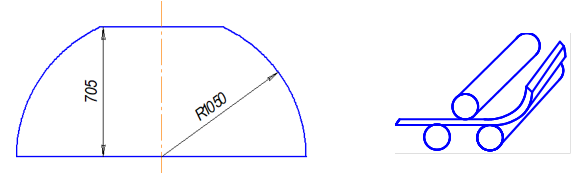
Рисунок 7. Перегородка и вальцовка
Стяжка обечайки струбциной и вырезка отверстий для горловины плазменной резкой.
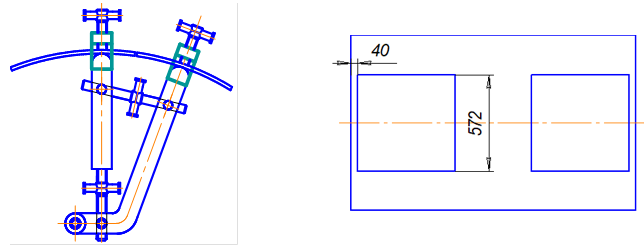
Рисунок 8. Стяжка обечайки и вырезка отверстий
2.2 Выбор сварочного и вспомогательного оборудования
Для выполнения корпуса воздухоохладителя в данной работе используются следующие виды оборудования:
-
источник питания ВДМ – 6303 С, универсальный сварочный конвертор КСУ – 320; -
аппарат для плазменной резки Powermax 30; -
колонна Mini с роликовыми вращателями для сварки продольных и кольцевых швов обечаек; -
вальцовочный станок Epple E – RBM 2.050 – 30; -
гильотины Yangli, сверлильный станок с магнитной основой.