Файл: 3 Черновое обтачивание цилиндрических поверхностей 4 Обработка торцов и уступов.docx
ВУЗ: Не указан
Категория: Не указан
Дисциплина: Не указана
Добавлен: 08.02.2024
Просмотров: 23
Скачиваний: 0
ВНИМАНИЕ! Если данный файл нарушает Ваши авторские права, то обязательно сообщите нам.
Метчик (рис. 3.85) представляет собой закаленный винт, на котором прорезано несколько прямых или винтовых канавок, образующих режущие кромки инструмента. Канавки также обеспечивают размещение стружки, образующейся при резании стружка может выводиться из зоны резания.
Метчик состоит из двух частей – рабочей и хвостовика, на конце которого выполнен квадрат (у ручных метчиков). Рабочая часть метчика включает в себя: режущую (заборную) часть, которая обеспечивает удаление основной части припуска на обработку; калибрующую часть, осуществляющую окончательную обработку резьбы; стружечные канавки; перья (витки резьбы, разделенные стружечными канавками) и сердцевину, обеспечивающую метчику достаточную для обработки прочность и жесткость. Хвостовая часть метчика служит для закрепления его в воротке, которым производятся рабочие и холостые перемещения метчика.
Рабочую часть метчика изготавливают из инструментальных углеродистых сталей марок У11, У11А, быстрорежущей стали или твердого сплава. Выбор материала рабочей части зависит от физико-механических свойств обрабатываемой заготовки. У цельных метчиков материал хвостовой части тот же, а у метчиков, состоящих из двух частей, соединяемых сваркой, хвостовую часть изготавливают из конструкционной стали марок 45 и 40Х: Число стружечных канавок, выполненных на метчике, зависит от его диаметра (три канавки дтя метчиков диаметром до 20 мм и четыре – для метчиков диаметром свыше 20 мм).
Основную работу при нарезании резьбы выполняют режущие кромки, образованные пересечением передних поверхностей канавки с задними (затылованчыми, выполненными по архимедовой спирали) поверхностями рабочей части. Затылование задней поверхности режущих зубьев позволяет сохранить постоянным их профиль после переточки, которая осуществляется централизованно в заточных цехах.
Как правило, метчики изготовляют с прямыми канавками, однако для улучшения условий резания и получения точных и чистых резьб применяют метчики с винтовыми канавками. Угол наклона такой канавки к оси метчика составляет 8… 15°. Для получения точных и чистых резьбовых поверхностей в сквозных отверстиях при обработке мягких и вязких материалов используют бесканавочные метчики.
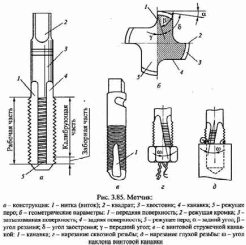
Конструкция метчиков зависит от их назначения. В соответствии с этим используют ручные (слесарные), гаечные (машинно-ручные), плашечные, маточные, сборные и специальные метчики.
По способу применения метчики делят на две группы: ручные и машинные.
Ручные (слесарные) метчики служат для нарезания резьбы вручную. Они обычно выпускаются комплектами из двух-трех штук в зависимости от диаметра обрабатываемой резьбы. В комплект входят черновой, средний и чистовой метчики, а если комплект состоит из двух метчиков, то в нем имеются черновой и чистовой метчики. Комплектование метчиков по несколько штук связано с необходимостью разделения слоя металла при нарезании резьбы на очень малые части, так как обработка выполняется в весьма сложны: условиях (затруднен отвод стружки из зоны резания). Если для нарезания резьбы применять один метчик (т.е. соединить в одном метчики и черновой и чистовой), то его длина будет чрезвычайно большой, что снизит жесткость и прочности инструмента и соответственно качество обработки резьбовой поверхности. Поэтому рабочую часть метчика делят на части, выполняя каждую из них в виде отдельного инструмента.
Для того чтобы различить метчики одного комплекта на их хвостовой части помимо обозначения размера резьбы наносят круговые риски – одну для чернового метчика, две – для среднего и три – для чистового. Заборная часть чернового метчика имеет 6… 8 витков, среднего – 3…4, а чистового – всего 1,5…2 витка. Величина срезаемого слоя металла между метчиками комплекта распределяется следующим образом: первый метчик снимает 50% резьбы, второй – 30%, а третий калибрует резьбу начисто, снимая 20% припуска.
Машинно-ручные метчики позволяют нарезать цилиндрические и конические резьбы с шагом до 3 мм в сквозных и глухих отверстиях с использованием механизированных приспособлений и стационарного оборудования, а также вручную. От ручных метчиков они отличаются значительно большими размерами хвостовика и большей длиной заборной части. При нарезании резьб в заготовках из чугуна и конструкционной стали применяется один метчик, для нарезания резьб в заготовках из высокопрочной стали используется комплект метчиков из двух штук.
Гаечные метчики (рис. 3.86) служат для нарезания резьбы на токарных станках (рис. 3.86, а) и на специальных гайконарезных автоматах (рис. 3.86. б). При использовании гаечных и машинных метчиков на станках их крепят в специальных предохранительных патронах, обеспечивающих самовыключение при перегрузке. Нарезаемые гайки при этом накапливаются на хвостовике метчика.
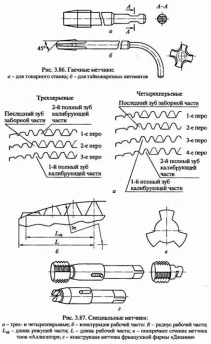
Специальные метчики (рис. 3.87) составляют большую группу, в которую входят ненормализованные конструкции метчиков, предназначенных для определенных условий эксплуатации. К ним относятся метчики с профилем поперечного сечения, показанным на рис. 3.87, в. Такие метчики под названием «Аллигатор» выпускает одна из французских фирм. Благодаря повышенной прочности и жесткости такие метчики позволяют обрабатывать за один проход резьбы в высокопрочных материалах. На рис. 3.87, г представлен метчик с механическим соединением рабочей части и хвостовика французской фирмы «Джаним».
Металлорежущий инструмент. Плашки

Плашка – резьбонарезной инструмент предназначенный для нарезания наружной резьбы вручную или на металлорежущем станке (обычно за один проход). В процессе резания плашка и заготовка совершают 2 относительных движения: вращение вокруг продольной оси резьбы и продольную подачу (равную шагу резьбы); при этом плашка, навинчиваясь на заготовку, нарезает резьбу режущими перьями. Плашка требует принудительной подачи на 1—2 шага только при врезании, дальнейшее осевое движение может происходить самоподачей (самозатягиванием).
По наружной форме плашки бывают круглые, квадратные, шестигранные, трубчатые и др. По конструкции различают плашки цельные, разрезные и раздвижные. Существуют плашки к резьбонарезным головкам и слесарным клуппам, резьба которыми нарезается за нескольких проходов. Наиболее распространена круглая плашка, имеющая, подобно гайке, центральное отверстие с резьбой, вокруг которого расположено 3—6 гладких отверстий, пересекающих центральное отверстие для образования зубьев плашки и канавок для отвода стружки. Трубчатые плашки применяются на токарно-револьверных станках и автоматах, где облегчены условия выхода стружки. Низкие скорости резания обусловлены плохим теплоотводом от узких режущих перьев. Плашки изготовляются, как правило, из инструментальной стали и быстрорежущей стали.
Типы резьб: M, G, Rc, K, Tr, UNF, UNJF, BSW/BSF, BSP, NPT, NPTF, BSPTr, NGT.
Нарезание резьбы плашками
Стружечные отверстия плашки играют ту же роль, что и канавки у метчика. Процессы образования резьбы плашкой и метчиком аналогичны. При навинчивании плашки на обрабатываемую деталь поверхность последней становится винтовой; срезаемая стружка выходит через стружечные отверстия, которые поэтому должны иметь достаточные размеры.
Нарезание резьбы круглой плашкой производится за один проход. Плашка режет своей конической заборной частью. Заборные части имеют с обеих сторон инструмента, что дает возможность после затупления одной заборной части перевернуть плашку и работать второй стороной. Средняя часть плашки с резьбой полного профиля является калибрующей.
Условия работы режущих кромок у плашки неблагоприятные. Тонкие режущие перья недостаточно прочны и плохо отводят тепло. Удаление стружки и подача в зону резания охлаждающей жидкости затруднены небольшими размерами стружечных отверстий. Поэтому для получения более качественной резьбы без срыва витков рекомендуется работать с малой скоростью резания.
В производственных условиях скорость резания обычно не рассчитывают по формуле, а принимают из справочных (нормативных) таблиц.
Сверлильный станок
Классификация сверлильных станков
Сверлильные станки делятся на следующие типы:
-
Вертикально-сверлильные станки; -
Одношпиндельные полуавтоматы; -
Многошпиндельные полуавтоматы; -
Координатно-расточные станки; -
Радиально-сверлильные станки; -
Горизонтально-расточные; -
Алмазно-расточные; -
Горизонтально-сверлильные станки; -
Разные сверлильные.
Модели станков обозначают буквами и цифрами. Первая цифра обозначает, к какой группе относится станок, вторая - к какому типу, третья и четвертая цифры характеризуют размер станка или обрабатываемой заготовки. Буква, стоящая после первой цифры, означает, что данная модель станка модернизирована (улучшена). Если буква стоит в конце, то это означает, что на базе основной модели изготовлен отличный от него станок.
Например, станок модели 2Н118 - вертикально-сверлильный, максимальный диаметр обрабатываемого отверстия 18мм, улучшен по сравнению со сверлильными станками моделей 2118 и 2А118. Станок модели 2Н118А также вертикально-сверлильный, диаметр обрабатываемого отверстия 18мм, но он автоматизирован и предназначен для работы в условиях мелкосерийного и серийного производства.
В зависимости от области применения различают универсальные и специальные сверлильные станки. Находят широкое применение и специализированные сверлильные станки для крупносерийного и массового производства, которые создаются на базе универсальных станков путем оснащения их многошпиндельными сверлильными и резьбонарезными головками и автоматизации цикла работы.
Из всех сверлильных станков можно выделить следующие основные типы универсальных станков: одно- и многошпиндельные вертикально-сверлильные; радиально-сверлильные; горизонтально-сверлильные для глубокого сверления.
Сверлилый станок с ручным управлением
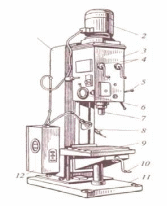
Рис. 1. Вертикально-сверлильный станок:
1 - колонна (станина); 2 - электродвигатель; 3 - сверлильная головка; 4 - рукоятки переключения коробок скоростей и подач; 5 - штурвал ручной подачи; 6 - лимб контроля глубины обработки