Добавлен: 11.04.2024
Просмотров: 178
Скачиваний: 0
ВНИМАНИЕ! Если данный файл нарушает Ваши авторские права, то обязательно сообщите нам.
-
Инструмент, применяемый при обработке на станке
Для работы на плоскошлифовальном станке 3722 применяют абразивный инструмент
К абразивным инструментам относятся круги для шлифования и заточки режущего инструмента, сегменты и бруски. Абразивные сегменты применяют для изготовления наборных шлифовальных кругов, бруски — при ручных работах и при отделочной обработке (хонинговании, суперфинишировании).
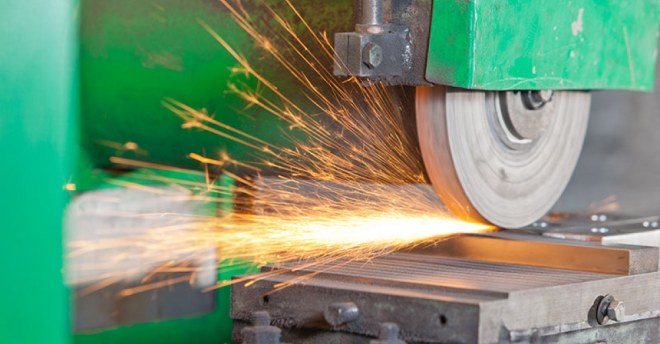
Абразивный инструмент стандартизирован по форме и размерам и характеризуется формой и размерами, материалом абразивных зерен, связующим веществом, зернистостью, твердостью и структурой.
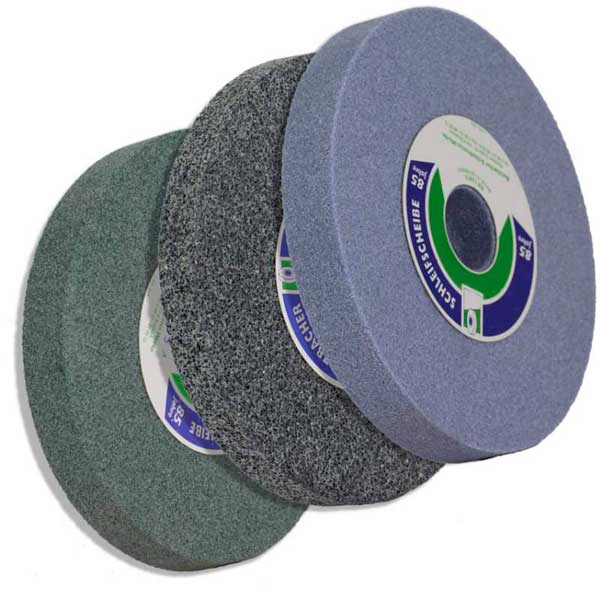
К абразивным материалам естественного происхождения относятся алмаз, применяемый наиболее широко, природный корунд, наждак и песчаник, а искусственного происхождения — синтетический алмаз, электрокорунд, карбид кремния и карбид бора. Искусственный алмаз изготовляют из графита в специальных камерах при давлении 100 000 кгс/см2 (9,8ГПа) и температуре 2500— 2300° С.
Алмазные круги на износостойкой металлической связке работают с охлаждением. Их применяют для получистовой и чистовой шлифовки наиболее точных деталей и режущих инструментов из твердого сплава.
Зернистость абразивных кругов характеризует размеры зерен. Согласно ГОСТу принято обозначение номеров зернистости по величине отверстия сита (в сотых долях миллиметра), на котором задерживается зерно основной фракции.
Зернистость шлифовального круга выбирают в зависимости от свойств обрабатываемого материала и технологических требований (шероховатости поверхности, точности и др.). При черновом шлифовании применяют шлифовальные круги с более крупным зерном, чем при чистовом. При обработке вязких металлов во избежание засаливания применяют круги большей зернистости, чем при обработке твердых и хрупких металлов.
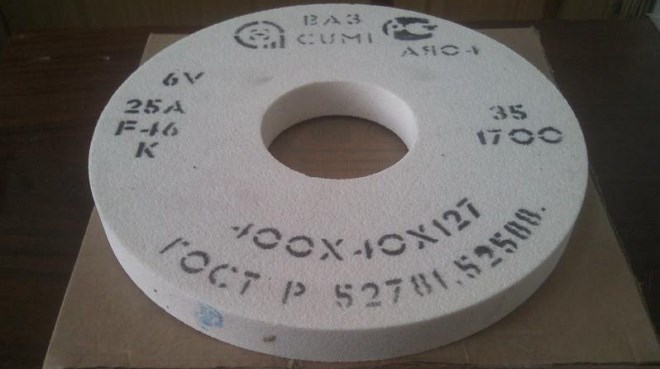
-
РАЗРАБОТКА СИСТЕМЫ ПЛАНОВО – ПРЕДУПРЕДИТЕЛЬНОГО РЕМОНТА СТАНКА
-
Основные положения системы планово-предупредительного ремонта станка.
Мероприятия по планово-предупредительному ремонту по уходу за станками и их ремонту осуществляются в установленные планом сроки. Они построены, так чтобы обеспечить долговременную работу станков с необходимыми точностью и мощностью, наименьшими простоями и низкой стоимостью работ по уходу за станками и их ремонту.
Имеются следующие системы планово-предупредительного ремонта: стандартные, после осмотровые, планово-периодические.
Система стандартных ремонтов построена так, что станки ремонтируют в заранее определенные планом сроки, причем детали, подлежащие замене по плану, заменяются при ремонта независимо от того, изношены ли они или еще пригодны для дальнейшей работы. Эту систему применяют там, где имеется некоторое количество одинаковых станков, работающих с постоянными режимами резания.
Система после осмотровых ремонтов состоит в том, что объектами планирования системы служат осмотры станков, проводимые в заранее установленные планом сроки. Ремонты станков назначают лишь в тех случаях, когда осмотром установлена потребность в них. Сроки ремонтов устанавливаются с учетом времени, необходимого для их подготовки. Система после осмотровых ремонтов широкого распространения не имеет.
Система периодических ремонтов совмещает преимущества стандартной и после осмотровой систем ремонта. При этой системе планируются определенные сроки остановки станков на ремонт и ориентировочный объем
ремонтных работ. Работы при ремонте каждого отдельного станка проводятся лишь в том объеме, какой вызван действительной потребность станка. Система периодических ремонтов позволяет планировать ремонты на длительное время и заблаговременно подготовить их, сокращая тем простой станков. Затраты на ремонт станков при периодической системе планово- предупредительного ремонта относительно невелики. Ограничена также возможность аварийных остановок станка.
-
Структура ремонтного цикла станка
Для станка 3722, выпущенного до 1967 года, класс точности П и масса 7 т структура ремонтного цикла будет иметь вид:
КР-О-TР-О-TР-О-СР-О-TР-О-TР-О-СР-О-TР-О-TР-О-КР,
где КР – капитальный ремонт; СР- средний ремонт TР – текущий ремонт; О – осмотр.
Данный цикл включает: капитальных ремонтов – 2, средних – 2; текущих – 6, осмотров - 9
-
Расчёт периодичности ремонтного цикла и величины межремонтного периода
Тр.ц. = 24000 ∙ Ком ∙ Кми ∙ Кто ∙ Кв ∙ Ку ∙ Ккм, (4.1) где 24000 ч – нормативный коэффициент, характеризующий
длительность ремонтного цикла для металлорежущего оборудования; Ком–коэффициент,учитывающийобрабатываемыйматериал:для конструкционной стали - 1,0;
Кми– коэффициент, учитывающий материал применяемогоинструмента:
абразив – 0,8;
Кто–коэффициент,учитывающийклассточностиоборудования:
повышенной точности – 1,5
Кв–
коэффициент,учитывающийвозрастоборудования(до 10 лет – 1,0, далее чем больше возраст, тем ниже значение коэффициента) - 0,7
Ку– коэффициент,учитывающийусловияэксплуатацииоборудования
для нормальных условий у = 1,0;
Ккм–коэффициент,учитывающийкатегориюмассыоборудования
вес станка до 10 т – 1,0
Тр.ц. = 24000 ∙ 1 ∙ 0,8 ∙ 1,5 ∙ 0,7 ∙ 1 ∙ 1 = 20160 ч
Fд-Годовой эффективный фонд времени, Fд – 4055 часов
Продолжительность ремонтного цикла в годах:
Тр.ц.(год) =


Длительность межремонтного периода рассчитывается по следующей формуле:
Тм.р.
= Тр.ц.(год)∗12 , (4.2)
????т+

где: Тр.ц. – длительность ремонтного цикла;
nт – количество текущих (малых) ремонтов.
nc – количество средних ремонтов;
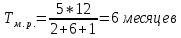
Длительность межосмотрового периода можно определить по следующей формуле:

о

где nо – количество осмотров или периодичность осмотров (текущего обслуживания).
5 ∗ 12

-
Разработка графиков ремонтов
График планово-предупредительного ремонта в таблице 2 строится на основе расчетных данных ремонтного цикла, межремонтных и межосмотровых периодов, принятой структуры ремонтного цикла для данного оборудования.
Начало ремонтного цикла 01.2003г.
Периодичность ремонтного цикла – 5 лет.
Длительность межремонтного периода – 6 месяцев.
Длительность межосмотрового периода – 3 месяца.
Вид работ | КР | О | ТР | О | ТР | О | СР | О | ТР | О | ТР | О | СР | О | ТР | О | ТР | О | КР | |||
Год | 2003 | 2004 | 2005 | 2006 | 2007 | |||||||||||||||||
Месяц | 1 | 4 | 7 | 10 | 1 | 4 | 7 | 10 | 1 | 4 | 7 | 10 | 1 | 4 | 7 | 10 | 1 | 4 | 7 |
Табл.2. Календарные даты выполнения плановых ремонтных работ
-
Расчёт трудоёмкости плановых ремонтов механической и электрической частей
Категория ремонтной сложности
Трудоемкость и материалоемкость ремонтных работ и технического обслуживания зависит от сложности, конструктивных и технологических особенностей