Файл: Отчет по учебной практике пм 01 Ведение технологического процесса на установках категории.docx
Добавлен: 16.03.2024
Просмотров: 38
Скачиваний: 0
ВНИМАНИЕ! Если данный файл нарушает Ваши авторские права, то обязательно сообщите нам.
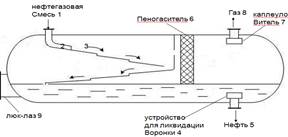
Рис. №4 двухфазный сепаратор.
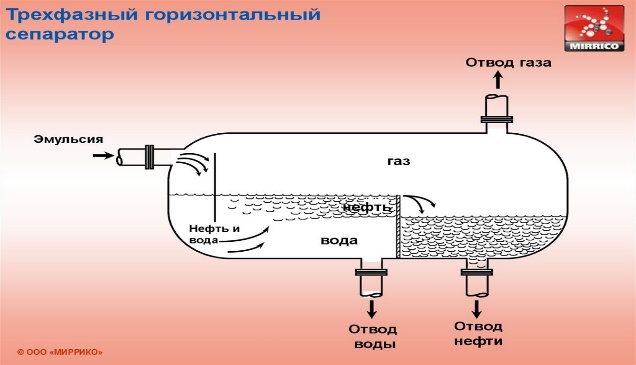
Рис. №5 трехфазный сепаратор.
2.4. Описание и принцип работы электородегидратора.
Электродегидраторы используются в составе технологических установок по подготовке нефти к транспорту на нефтедобывающих и перерабатывающих предприятиях. Данное оборудования является наиболее эффективным для получения товарной нефти за счет ее глубокого обезвоживания и обессоливания, так как при ее обработке применяются электрический ток. Конструктивно электродегидраторы представляют собой цилиндрическую емкость с эллиптическими днищами на седловых опорах. Внутри корпуса размещаются электроды, которые находятся в подвешенном состоянии. Вход нефтяной эмульсии осуществляется через входной штуцер с распределяющим устройством. Выход воды и нефти осуществляется через разные выходные штуцеры. Работа электродегидраторов заключается в подаче тока высокого напряжения на два заземленных и два высокопотенциальных электрода. Между электродами при подаче тока образуется электрическое поле. Под действием тока высокого напряжения капли нефти укрупняются и оседают на днище. Для того, чтобы деэмульгировать нефтяную эмульсию, в жидкость вводится деэмульгатор. Система электропитания (высоковольтный источник питания и изолятор) размещается сверху корпуса. В корпусе также располагаются люк-лаз, штуцеры и патрубки для входа и выхода нефтяной эмульсии, отделившейся воды, дренажа, а также установки технологического оборудования - уровнемера, манометра, термопары, предохранительного клапана. В электродегидратор подается нефть, смешанная с промывочной водой. Внутри капли воды, содержащиеся в рабочей среде, объединяются с каплями промывочной воды, отделяются и оседают с последующим выводом через специальный штуцер.
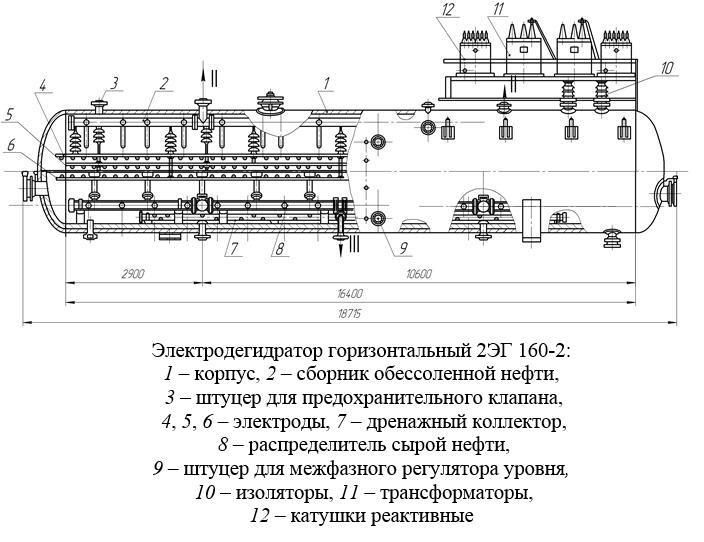
Рис. №6 Электродегидратор
2.5. Описание и принцип работы ректификационной колонны с ситчатой тарелкой.
Ректификация — это метод разделения смеси на чистые компоненты, осуществляемый путем многократного чередования процессов испарения жидкой фазы и конденсации паров.
Физическая сущность процесса заключается в двустороннем массо- и теплообмене между неравновесными потоками пара и жидкости при высокой турбулизации поверхности контактирующих фаз. В результате массообмена пар обогащается низкокипящими, а жидкость - высококипящими компонентами. При определенном числе контактов можно получить пары, состоящие в основном из низкокипящих компонентов и жидкость, состоящую в основном из высококипящих компонентов.
Процесс ректификации можно проводить, в простейшем случае, в многоступенчатой установке. В первой ступени такой установки испаряется исходная смесь. На вторую ступень поступает на испарение жидкость, оставшаяся после отделения паров первой ступени. В третьей ступени испаряется жидкость, поступившая из второй ступени (после отбора из последней паров). Аналогично может быть организован процесс многократной конденсации, при котором на каждую следующую ступень поступают для конденсации пары, оставшиеся после отделения от них жидкости (конденсата) в предыдущей ступени.
При достаточно большом числе ступеней таким путем можно получить жидкую или паровую фазу с достаточно высокой концентрацией компонента, которым она обогащается. Однако, выход этой фазы будет достаточно мал по отношению к ее количеству в исходной смеси. Кроме того, такие установки громоздки и их эксплуатация сопровождается большими потерями тепла в окружающую среду.
Значительно более экономичное, полное и четкое разделение смесей на компоненты достигается путем проведения процессов ректификации в более компактных аппаратах – ректификационных колоннах
Колонна с ситчатыми тарелками представляет собой вертикальный цилиндрический корпус с горизонтальными тарелками, в которых равномерно по всей поверхности просверлено значительное число отверстий диаметром 1-5 мм. Для слива жидкости и регулирования ее уровня на тарелке служат переливные трубки, нижние концы которых погружены в стаканы.
Газ проходит сквозь отверстия тарелки и распределяется в жидкости в виде мелких струек и пузырьков. При слишком малой скорости газа жидкость может просачиваться через отверстия тарелки на нижерасположенную, что должно привести к существенному снижению интенсивности массопередачи. Поэтому газ должен двигаться с определенной скоростью и иметь давление, достаточное для того, чтобы преодолеть давление слоя жидкости.
Ситчатые тарелки отличаются простотой устройства, легкостью монтажа, осмотра и ремонта. Гидравлическое сопротивление этих тарелок невелико. Ситчатые тарелки устойчиво работают в довольно широком интервале скоростей газа, причем в определенном диапазоне нагрузок по газу и жидкости эти тарелки обладают высокой эффективностью. Вместе с тем ситчатые тарелки чувствительны к загрязнениям и осадкам, которые забивают отверстия тарелок. В случае внезапного прекращения поступления газа или значительного снижения его давления с ситчатых тарелок сливается вся жидкость, и для возобновления процесса требуется вновь запускать колонну.
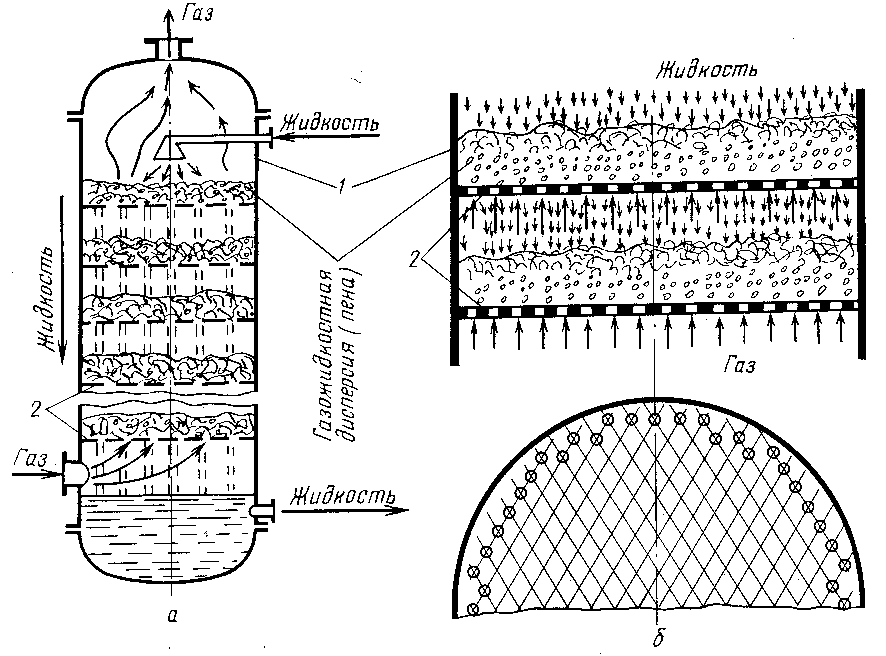
Рис.№7. Схема ректификационной колонны с ситчатой тарелкой.
2.6. Описание и принцип работы кожухотрубчатого холодильника-конденсатора.
Кожухотрубчатые холодильники применяются в нефтяной, газовой и химической отраслях промышленности для теплообмена (охлаждения) между двумя рабочими средами. В качестве теплоносителя (охладителя, хладагента) может выступать как вода, так и любая другая нетоксичная жидкость с температурой кипения под давлением 0,7 МПа не выше +60ºС.
ТД САРРЗ поставляет до места эксплуатации кожухотрубчатые холодильники, которые работают при давлении 0,6-4,0 МПа и при максимальной температуре рабочей среды до +300ºС. Благодаря своему устройству теплообменные холодильники данного типа имеют поверхность теплообмена до 970 м2.
Кожухотрубчатые холодильники представляют собой вертикальный или горизонтальный аппарат с эллиптическими днищами. Внутри аппаратов размещаются трубы, жестко закрепленные в трубные решетки. Эти решетки жестко крепятся к корпусу холодильника. В холодильниках типа ХК предусматриваются специальные гибкие температурные компенсаторы, которые необходимы для компенсации изменяющихся длин труб по отношению к кожуху. Температурные компенсаторы рассчитаны на эксплуатацию в аппаратах с рабочими средами, чья разница температур не превышает 60ºС. Вертикальное или горизонтальное исполнение холодильников (маркировки ХКВ/ХНВ и ХКГ/ХНГ соответственно) имеет одинаковую производительность, а выбор той или иной конструкции зависит от условий эксплуатации на объекте.
Принцип работы кожухотрубчатых холодильников заключается в теплообмене между охлаждающим веществом и рабочей средой. В зависимости от требований к процессу теплообмена выпускаются одноходовые и многоходовые кожутотрубчатые холодильники. В одноходовых поток рабочих сред не меняет направление в процессе прохождения внутри аппарата. Многоходовые холодильники характеризуются изменением направления движения рабочих сред за счет размещения внутри специальных перегородок. Смена направления положительно влияет на скорость потока, что ведет к увеличению КПД теплообмена.
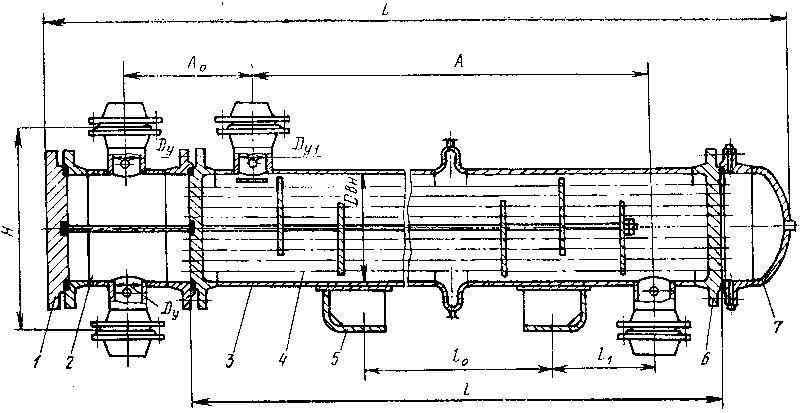
Рис.№8 Схема холодильника-конденсатора.
2.7. Описание и принцип работы трубчатой печи.
УСТРОЙСТВО
Конструкция таких устройств аналогична со всеми нагревательными агрегатами, отличие только в цилиндрической форме топочного отсека. Для монтажа и изготовления печи понадобится:
1.для промышленной установки необходим отдельный фундамент, в его конструкции учитывается высокий уровень нагрева поверхностей. Лабораторные аппараты в такой конструкции не нуждаются;
2.наружный корпус агрегата. Это главная деталь, которая воспринимает нагрузку слоя футеровки, загружаемых деталей, различных устройств управления. Каркас собран на опорной раме, каждая стойка которой закреплена с помощью анкеров к основанию печи. Отдельные части корпуса соединяются с помощью ферм и шарниров, которые равномерно распределяют нагрузку от высоких температур и массы печи;
3.слой футеровки из огнеупорного шамотного кирпича, предохраняющий наружный корпус от высокого уровня нагрева и сохраняющий тепло в рабочем отсеке. На промышленных установках наружный слой футеровки закрывают теплоизоляционными листовыми материалами. Блоки слоя с маркировкой «А», «Б», «В» должны выдерживать температуру нагрева соответственно 17300, 16700, 15800. Для современных промышленных агрегатов допускается использование жаростойкого пенобетона;
4.устройство, отвечающее за уровень производительности агрегата – технологический змеевик. Его изготавливают из толстостенной горячекатаной бесшовной трубы. Это обусловлено условиями его работы в агрессивной среде с высоким уровнем нагрева. Горизонтальную конструкцию теплообменника крепят на кронштейнах или подвесах к основному каркасу печи. Вертикальная конвекционная конструкция заводится в специальные направляющие, где трубы заведены в отдельные отверстия;
5.нагревательные элементы предназначены для быстрого набора температуры в рабочей камере. Промышленные печи оснащаются разными видами горелок, работающими на газу или жидком топливе. Основная задача равномерное и быстрое распределение тепла по всей площади печи;
в качестве устройства, способствующего снижению потерь тепла, промышленные трубчатые агрегаты оснащаются утилизаторами тепловой энергии. Они нагревают поступающий воздух до температуры в 3000, благодаря чему значительно увеличивается производительность агрегата;
блок управления и безопасности. Используются различные термодатчики, которые управляют работой печи и препятствуют возникновению аварийных ситуаций;
система отвода отработанных газов в атмосферу по дымовой трубе, которая обеспечивает подачу кислорода в топку и выводит продукты горения.
ПРИНЦИП РАБОТЫ
Основная работа таких устройств разбита на 2 этапа:
1.При сгорании топлива образующийся газ собирается в главном секторе топочного отсека. Выделяется большое количество тепла, и дым постепенно вытесняется в полость теплообменника с конвекционными трубами. Постепенно остывая, он вытесняется нагретым воздухом. Температура доводится до заданного уровня.
2.В конвекционные трубы снизу поступает холодный воздух, затем проходя по нагретым пучкам трубопроводных экранов, он разогревается до максимальной температуры и поддерживает оптимальный и заданный уровень нагрева трубчатой камеры печи. Детали проходят термическую обработку в несколько этапов и после окончания работы агрегата выдвигаются на тележке или другом виде оборудования.
Температура может постепенно понижаться в период перерыва в нагреве, все зависит от операции по обработке изделий, а детали остывая, получают определенные свойства и структуру. За работой печей следит автоматика с системой термодатчиков.
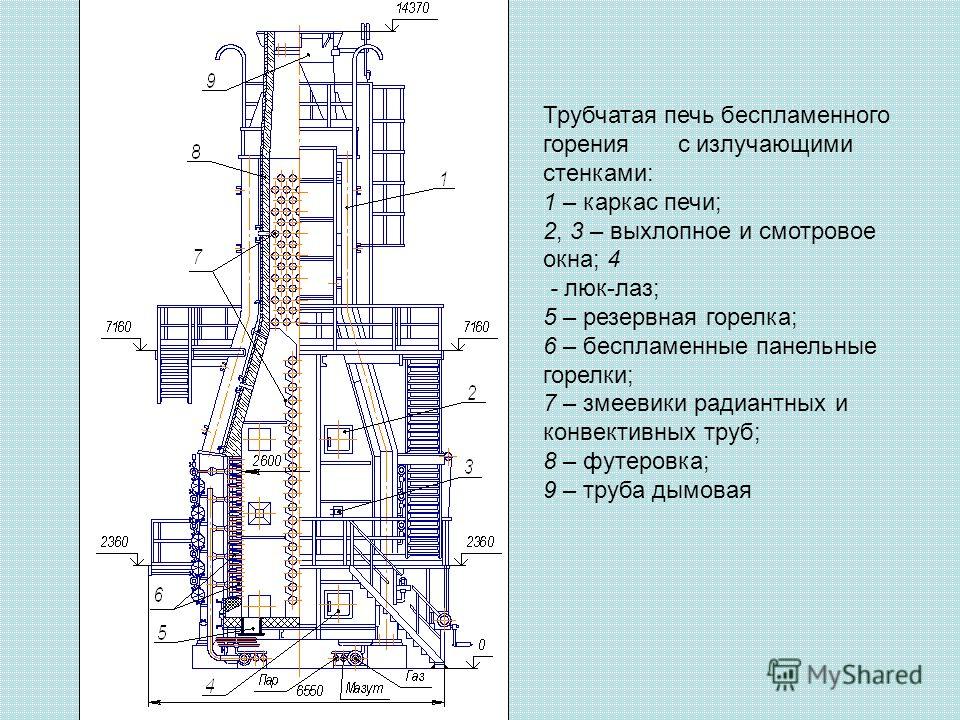
Рис.№9 Трубчатая печь
Печь работает следующим образом. Мазут или газ сжигается с помощью горелок, расположенных на стенах или поду камеры радиации. Газы сгорания из камеры радиации поступают в камеру конвекции, направляются в дымоход и по дымовой трубе уходят в атмосферу. Продукт одним или несколькими потоками поступает в трубы конвективного змеевика, проходит трубы экранов камеры радиации и нагретый до необходимой температуры, выходит из печи. Тепловое воздействие на исходные материалы в рабочей камере печи, является одним из основных технологических приемов, ведущих к получению заданных целевых продуктов. Главной частью трубчатой печи является радиационная секция, которая одновременно является и камерой сгорания. Передача тепла в радиационной секции осуществляется преимущественно излучением, вследствие высоких температур газов в этой части печи. Тепло, переданное в этой секции конвекцией, является только небольшой частью от общего количества переданного тепла, т. к. скорость газов,