Файл: Федеральное агентство железнодорожного транспорта филиал федерального государственного бюджетного образовательного учреждения высшего образования.docx
Добавлен: 20.03.2024
Просмотров: 26
Скачиваний: 0
ВНИМАНИЕ! Если данный файл нарушает Ваши авторские права, то обязательно сообщите нам.
.МИНИСТЕРСТВО ТРАНСПОРТА РОССИЙСКОЙ ФЕДЕРАЦИИ
ФЕДЕРАЛЬНОЕ АГЕНТСТВО ЖЕЛЕЗНОДОРОЖНОГО ТРАНСПОРТА
ФИЛИАЛ ФЕДЕРАЛЬНОГО ГОСУДАРСТВЕННОГО БЮДЖЕТНОГО ОБРАЗОВАТЕЛЬНОГО
УЧРЕЖДЕНИЯ ВЫСШЕГО ОБРАЗОВАНИЯ
САМАРСКИЙ ГОСУДАРСТВЕННЫЙ УНИВЕРСИТЕТ ПУТЕЙ
СООБЩЕНИЯ в г. Алатыре
ЗАЩИЩЕНО:
____________
Руководитель:
____________
"___"_______2022г.
ТЕХНОЛОГИЯ РЕМОНТА КРОНШТЕЙНОВ И ЩЕТКОДЕРЖАТЕЛЕЙ ТЭД ЭДУ-133Ц.
ПМ03.МДК 03.01 УвКТД Разработка технологических процессов,
технической и технологической документации
Филиал СамГУПС в г. Алатыре 23.02.06 КП 20 ПЗ
Руководитель проекта:
__________ Давыдов Г.В.
Разработал студент:
_________Уральский Д.А.
Группа: Л-18-1
"___"__________2022г.
2022
МИНИСТЕРСТВО ТРАНСПОРТА РОССИЙСКОЙ ФЕДЕРАЦИИ
ФЕДЕРАЛЬНОЕ АГЕНТСТВО ЖЕЛЕЗНОДОРОЖНОГО ТРАНСПОРТА
ФИЛИАЛ ФЕДЕРАЛЬНОГО ГОСУДАРСТВЕННОГО БЮДЖЕТНОГО ОБРАЗОВАТЕЛЬНОГО
УЧРЕЖДЕНИЯ ВЫСШЕГО ОБРАЗОВАНИЯ
САМАРСКИЙ ГОСУДАРСТВЕННЫЙ УНИВЕРСИТЕТ ПУТЕЙ
СООБЩЕНИЯ в г. Алатыре
Согласовано:
Председатель ПЦК
специальности 23.02.06
____________/ Пугачева Ю.А./
Задание на курсовой проект
ПМ03.МДК 03.01 УвКТД Разработка технологических процессов, технической и технологической документации
Студенту группы: Л-18-1 Уральскому Дмитрию Алексеевичу
Тема курсового проекта: Технология ремонта кронштейнов и щеткодержателей ТЭД ЭДУ-133Ц.
Содержание проекта:
Введение
-
Назначение и условия работы детали (сборочной единицы, комплекта). -
Основные неисправности, причины их возникновения и способы предупреждения. -
Периодичность и сроки плановых технических обслуживаний и текущих ремонтов с разборкой и без неё. -
Способы очистки, осмотра и контроля деталей. -
Технология ремонта (замена, восстановление, способ восстановления). -
Предельно - допускаемые размеры деталей при эксплуатации и различных видах ТО и ТР. -
Приспособления, технологическая оснастка, средства механизации, оборудование, применяемое при ремонте. -
Особенности сборки, проверки и испытания комплекта, сборочной единицы. -
Организация рабочего места. -
Техника безопасности при ремонте, сборке, испытании. -
Технологические карты. -
Список использованных источников.
Дата выдачи: "___"____________ 2021г.
Дата выполнения: "__"_______ 2022г.
Руководитель курсового проекта: ____________ Давыдов Г.В.
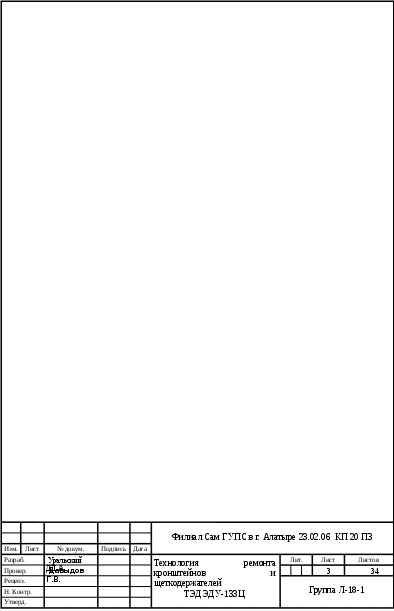
ВВЕДЕНИЕ
1. НАЗНАЧЕНИЕ И УСЛОВИЯ РАБОТ ДЕТАЛИ (СБОРОЧНОЙ
ЕДИНИЦЫ, КОМПЛЕКТА)………………………………………..……………5
2. ОСНОВНЫЕ НЕИСПРАВНОСТИ, ПРИЧИНЫ ИХ ВОЗНИКНОВЕНИЯ И СПОСОБЫ ПРЕДУПРЕЖДЕНИЯ……………………………...………………..9
3. ПЕРИОДИЧНОСТЬ И СРОКИ ПЛАНОВЫХ ТО И ТР С
РАЗБОРКОЙ И БЕЗ НЕЁ……………………………………………………….11
4. СПОСОБЫ ОЧИСТКИ, ОСМОТРА И КОНТРОЛЯ………………………….12
5. ТЕХНОЛОГИЯ РЕМОНТА (ЗАМЕНА, ВОССТАНОВЛЕНИЕ,
СПОСОБЫ ВОССТАНОВЛЕНИЯ)……………………………….………….17
6. ПРЕДЕЛЬНО - ДОПУСКАЕМЫЕ РАЗМЕРЫ ДЕТАЛЕЙ
ПРИ ЭКСПЛУАТАЦИИ И РАЗЛИЧНЫХ ВИДАХ…………………………..20
ТЕХНИЧЕСКОГО ОБСЛУЖИВАНИЯ И РЕМОНТА
7. ПРИСПОСОБЛЕНИЯ, ТЕХНОЛОГИЧЕСКАЯ ОСНАСТКА,
СРЕДСТВА МЕХАНИЗАЦИИ, ОБОРУДОВАНИЕ,
ПРИМЕНЯЕМОЕ ПРИ РЕМОНТЕ……………………………………..……..21
8. ОСОБЕННОСТИ СБОРКИ, ПРОВЕРКИ И
ИСПЫТАНИЯ КОМПЛЕКТА, СБОРОЧНОЙ ЕДИНИЦЫ.……...…………22
9. ОРГАНИЗАЦИЯ РАБОЧЕГО МЕСТА…………………………………….….24
10. ТЕХНИКА БЕЗОПАСНОСТИ ПРИ РЕМОНТЕ, СБОРКЕ,
ИСПЫТАНИИ…………………………………………………..…………….27
11. ТЕХНОЛОГИЧЕСКИЕ КАРТЫ………………………………………………30 12. СПИСКИ ИСПОЛЬЗОВАННЫХ ИСТОЧНИКОВ………………..…………34
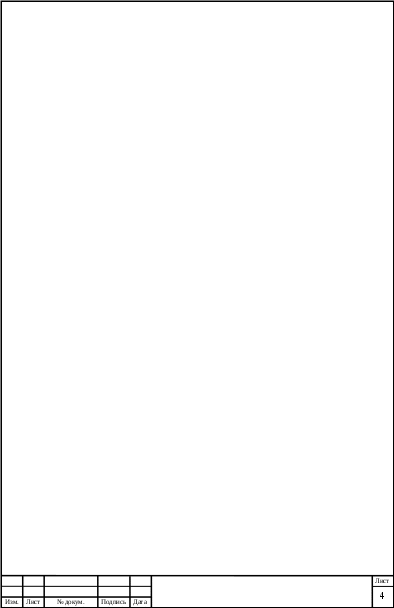
В электрических двигателях и генераторах часто необходимо установить электрическое соединение между неподвижной и вращающейся частью устройства.
В случае статорной (т. е. неподвижной) основной обмотки электрической машины устройство от нее ответвлений для присоединения внешней неподвижной электрической системы осуществляется легко, в случае же роторной (т. е. вращающейся) основной обмотки возникает необходимость в устройстве скользящего электрического контакта, так как иначе роторная обмотка недоступна.
Скользящий электрический контакт может быть осуществлен двумя способами: либо в виде кольцевого скользящего контакта, либо в виде коллекторного скользящего контакта. В обоих случаях для работы электрической машины нужны специальные устройства - щетки.
1. НАЗНАЧЕНИЕ И УСЛОВИЯ РАБОТ ДЕТАЛИ
(СБОРОЧНОЙ ЕДИНИЦЫ, КОМПЛЕКТА)
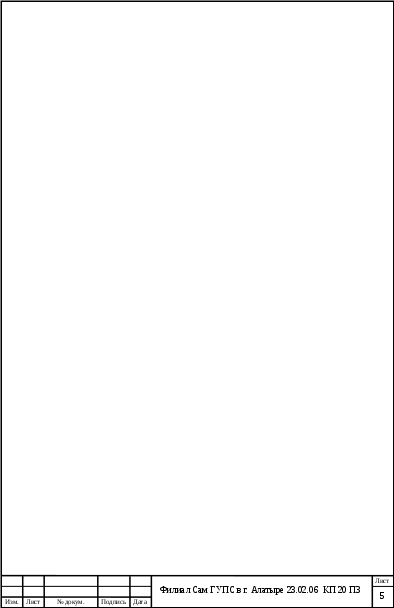
Щетки для тяговых двигателей изготовляют из графита, получаемого при нагреве в электрической печи сажи, кокса, антрацита. Такие щетки называют электрографитизированными.
Изготовляя их, стремятся к тому, чтобы они имели высокое переходное сопротивление, низкий коэффициент трения, были упругими, износоустойчивыми.
Одна щетка обычно перекрывает несколько коллекторных пластин, что ухудшает коммутацию (объяснение этого термина будет дано ниже) двигателей. Однако если щетки и коллекторные пластины выполнить равными по ширине, то щетки получились бы очень тонкими и хрупкими. Кроме того, при прохождении большого тока необходимо обеспечить достаточную поверхность контакта между щетками и коллектором. Поэтому, чтобы получить необходимую площадь рабочей поверхности щеток при небольшой их ширине, пришлось бы щетку удлинить, а это привело бы к удлинению коллектора.[3 http://umczdt.ru/books/37/225466/]
Щеточный аппарат состоит из четырех литых щеткодержателей, которые крепятся к траверсам. Зазоры между щеткодержателями и коллектором должны быть 2-4 мм. В каждом щеткодержателе установлено по три разрезные щетки марки ЭГ-61 с резиновыми амортизаторами. Для равномерного износа коллектора у каждого щеткодержателя одно окно выполнено под одну щетку, а другое под две и соседние разноименные щеткодержатели устанавливаются развернутыми в противоположные стороны. Нажатие на щетки регулируется спиральной стальной пружиной в пределах 4,2-4,8 кгс. На каждой щетке с боку имеются риски предельного износа. Одноименные щеткодержатели соединены между собой шинами, а к верхнему минусовому щеткодержателю еще крепится тонкий провод от БДС.При пересылке тепловоза в холодном состоянии нужно обязательно снять все щетки с тяговых электродвигателей, что бы исключить самовозбуждение ТЭД и предупредить возникновение пожара и образование ползунов на колесных парах.
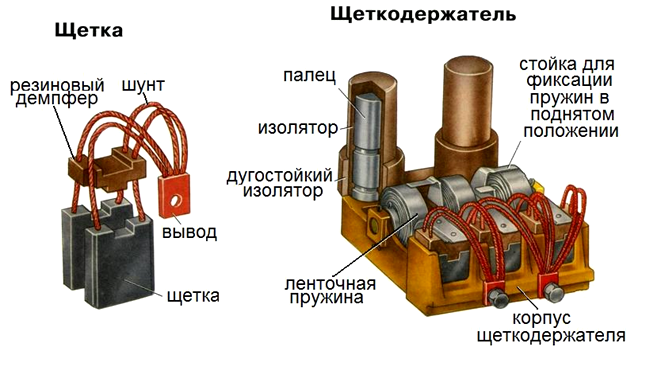
Рис.1- Щетка и Щеткодержатель
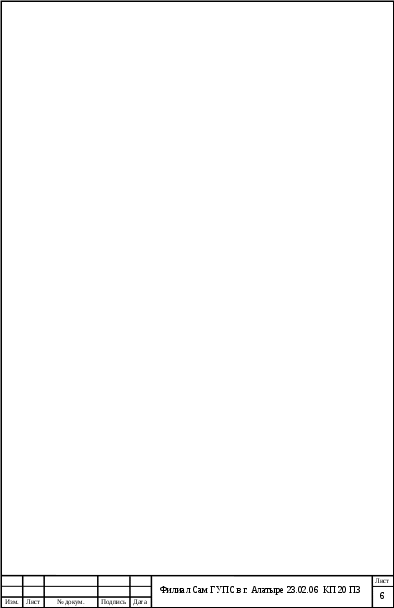
Щеткодержатель (рис.1) отлит из латуни, имеет гнезда для установки трехразрезных щеток ЭГ-61 (2х12,5)х40х64 с резиновыми амортизаторами для защиты от ударной и вибрационной нагрузки.
При разрезных щетках в случае неровности коллектора или выпучивании одной из коллекторных пластин подскакивает сначала одна, а затем вторая из половинок щетки, поэтому контакт щетки и коллектора сохраняется постоянно, коллектор почти не подгорает. Резиновые амортизаторы поглощают небольшие толчки и удары, не допуская отрыва щеток от коллектора.
На электродвигателе должны быть установлены щетки одной и той же марки. Это особенно важно при петлевой обмотке, так как различие в сортах щеток может вызвать протекание больших токов по уравнительным соединениям.
Латунный корпус щеткодержателя укреплен в кронштейне, вваренном в торцовую стенку остова. В корпус запрессованы два стальных пальца, служащих для крепления щеткодержателей в кронштейне. Пальцы изолированы от корпуса прессматериалом или твердым изоляционным слоем из эпоксидного компаунда, на который надеты изоляторы из прессматериала. Такое выполнение пальцев щеткодержателей дало возможность повысить их изоляционные свойства и тем самым избежать снижения сопротивления изоляции в эксплуатации, которое наблюдалось при использовании фарфоровых изоляторов.
В корпусе щеткодержателя имеются два гнезда для щеток. В одно гнездо вставлена одна пара щеток, в другое – две пары. Нажатие щеток на коллектор осуществляется спиральными пружинами. Нажатие (4,2 – 4,8 Н) регулируется поворотом втулки, находящейся в центре пружины. Характеристики спиральных пружин подобраны так, чтобы регулировка давления до полного износа щетки не требовалась. Щетки снабжены гибкими шунтами, прикрепленными болтами к корпусу щеткодержателя. Для удобства замены и осмотра щеток на щеткодержателях установлены стойки с заплечиками, позволяющие фиксировать пружины в приподнятом состоянии.
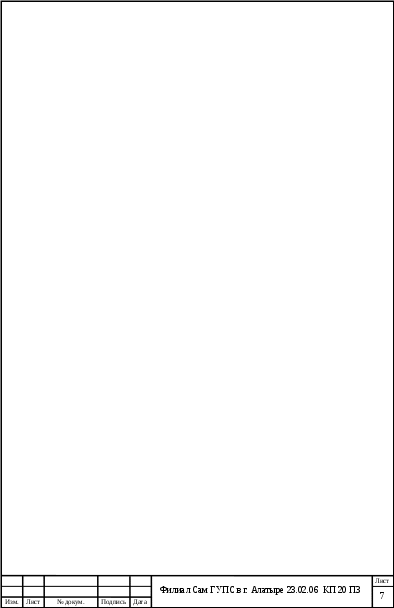
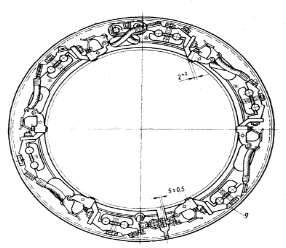
Рис. 2- Траверса.
Низкие температуры, кроме того, увеличивают жесткость пути и как следствие, происходит увеличение динамического воздействия на щёточный узел в целом особенно при опорно-осевом подвешивании. Высокая влажность воздуха уменьшает сопротивление изоляции, что может привести к её пробою и выходу из строя щёточного узла. Резкие перепады температуры с высокой влажностью воздуха могут привести к обледенению. Коллектор покрывается инеем, что вызывает сильное искрение. Кроме того, высокая влажность воздуха вызывает ускоренную коррозию деталей крепления щёткодержателей выполненных из металлов. Пыль, содержащаяся в воздухе, осаждаясь на изолированных поверхностях, снижает сопротивление электрической изоляции, а также теплопроводность, что может привести к перегреву соединений. Пыль оказывает абразивное воздействие на подвижные детали щёткодержателей и тем самым вызывает их повышенный износ, а также на изоляционные и антикоррозионные поверхности и ускоряя их старение.
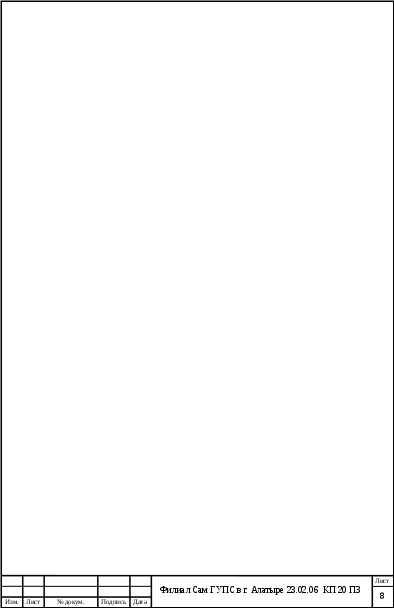
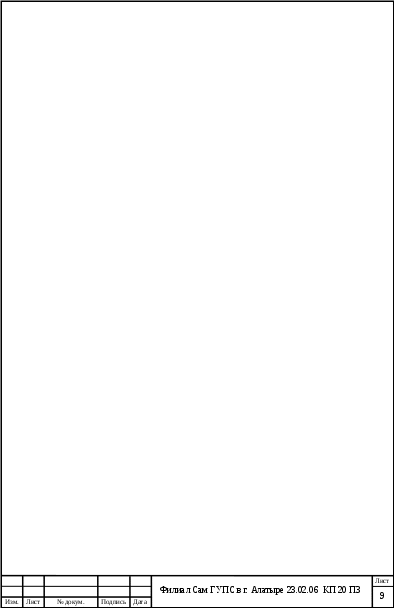
Щеточно-коллекторный узел в машинах постоянного тока и других машинах является наименее надежным узлом и требует тщательного технического обслуживания. Для обеспечения безыскровой работы необходимо выполнение ряда условий, обеспечивающих надежный контакт между щеткой и коллектором и равномерную допустимую нагрузку током рабочей поверхности щетки.
Основными неисправностями щеточного механизма являются обгорание или механическое повреждение обойм, потеря пружинами своих свойств, ослабление затяжки в контактных соединениях, наличие трещин в траверсах и повреждение изоляции пальцев щеткодержателей. Из всех деталей щеточного узла наиболее подвержены износу щетки.
А наиболее распространенная неисправность коллекторно-щеточного аппарата – это элементарный износ токосъемных щеток. Собственно говоря, сами графитовые щетки можно считать расходным материалом, а многие производители ручного инструмента даже предоставляют покупателю своей продукции дополнительную пару щеток бесплатно в качестве ремкомплекта.
Износ щеток приводит к потере контакта в паре «коллектор-щетка» и к разрыву цепи двигателя. Если контакт утерян не полностью, то возможно возникновение усиленного искрения под щетками (небольшое искрение может считаться нормой).
Может возникнуть «подергивание», привод будет работать неравномерно. В самых тяжелых случаях привод вообще невозможно запустить – когда силовая цепь полностью разомкнута.
Состояние щеток можно оценить и визуально, поскольку чрезмерный износ графита виден невооруженным глазом. Нередко возникают случаи, когда щетки просто «зависают», то есть, грубо говоря, «застревают» в своих направляющих, и пружина не может поджать их к коллектору для надежного контакта. Решение этой проблемы заключается в замене щеток, или их повторной установке с притиркой.
Причиной проблем со щетками может стать и их несоответствие по размерам и форме. Поэтому, приобретая щетки на замену, важно знать марку и модель техники, электропривод которой планируется ремонтировать. После замены щеток их необходимо «прикатать» работой на холостых оборотах в течение 10-15 минут.