Файл: Федеральное агентство железнодорожного транспорта филиал федерального государственного бюджетного образовательного учреждения высшего образования.docx
Добавлен: 20.03.2024
Просмотров: 27
Скачиваний: 0
ВНИМАНИЕ! Если данный файл нарушает Ваши авторские права, то обязательно сообщите нам.
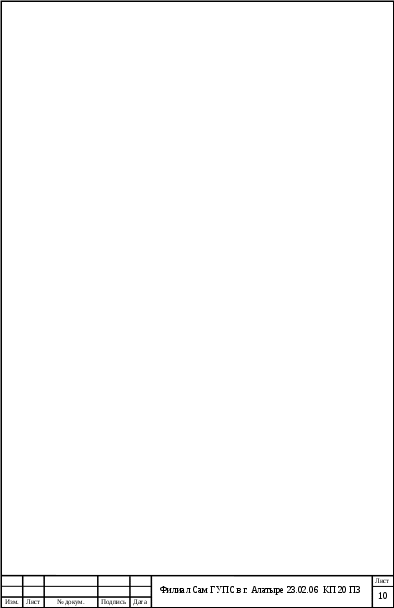
3. ПЕРИОДИЧНОСТЬ И СРОКИ ПЛАНОВЫХ ТО И ТР
С РАЗБОРКОЙ И БЕЗ НЕЁ
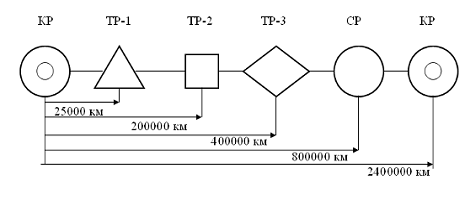
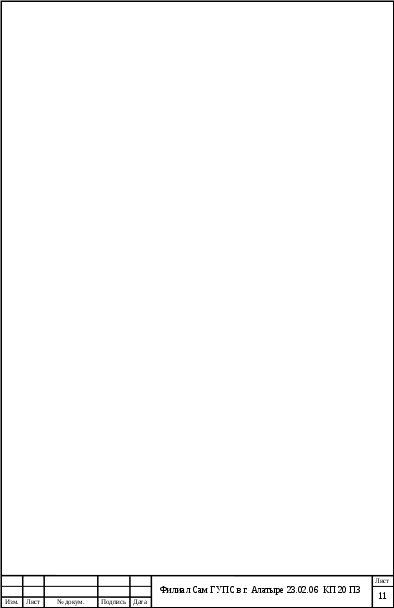
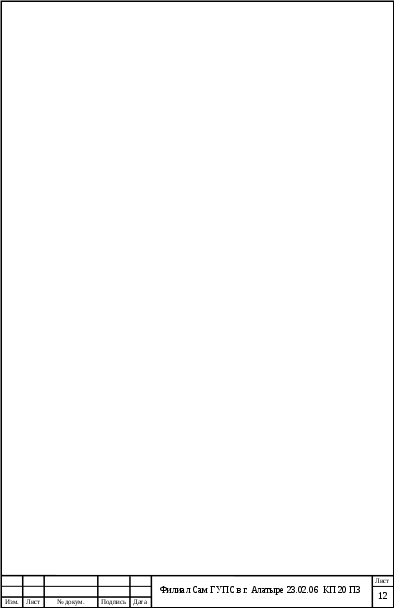
Тепловоз и его части в процессе эксплуатации покрываются сухой или пропитанной влагой и маслом, пылью. По действию среды на объект ремонта все способы очистки можно объединить в группы: механические, физико-химические, термические и смешанные.
Механические способы очистки основаны на воздействии твердого тела на объект очистки для разрушения и снятия слоя загрязнения.
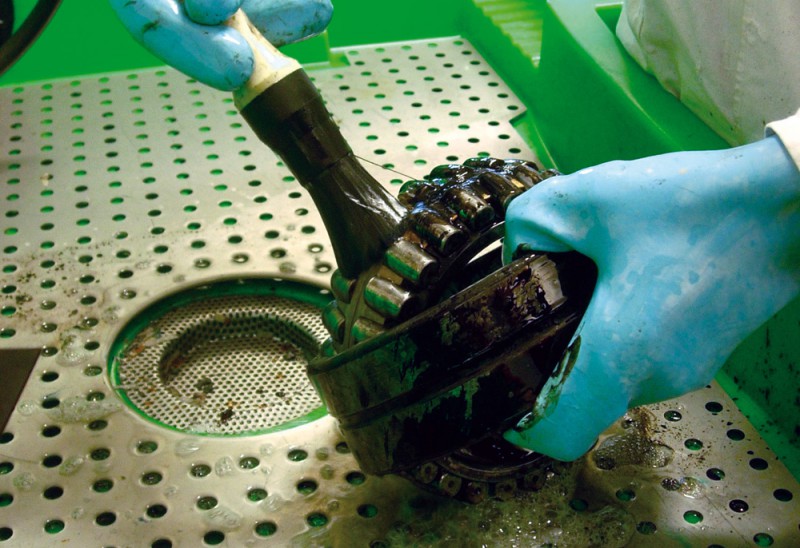
Рис. 5- Механическая очистка деталей
Очистка ручным механизированным инструментом. Этим способом удаляют с поверхностей деталей нагар, окислы, коррозию, старую краску. Ручной инструмент (скребок, шабер и т. п.) используют для очистки загрязнения труднодоступных мест и когда очищаемая площадь невелика. Механизированный инструмент (дрели с ручным, пневматическим или электрическим приводом, со сменными круглыми или торцовыми щетками) чаще применяют для очистки больших поверхностей и для ускорения процесса.
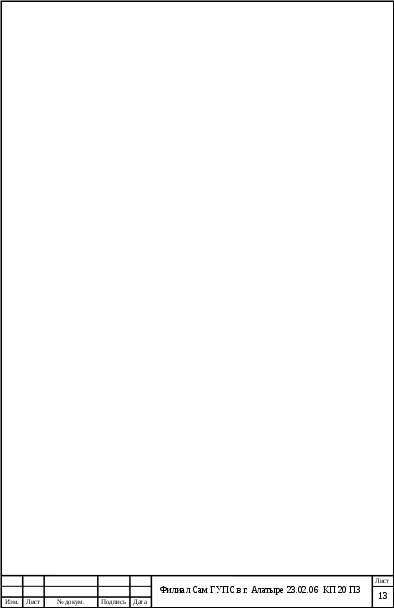
Очистка абразивами. Сущность очистки абразивами заключается в том, что загрязненную поверхность деталей, покрытую нагаром, коррозией, окислами, старой краской или прочно приставшей тонкой пленкой загрязнения, обрабатывают твердыми или мягкими абразивами, направляемыми струей воздуха или жидкости. Частицы абразива, ударяясь о поверхность детали, разрушают загрязненный слой и уносят с собой грязевые частицы. Очистка деталей абразивами очень эффективна.
При гидроабразивной очистке смесь (абразив с водой) к соплу установки может подаваться выдавливанием сжатым воздухом, центробежным или лопастным насосом, путем эжектирования при раздельной подачи воздуха в смеси с песком и воды. Недостатки абразивной очистки заключаются в том, что очистке подвергаются лишь те поверхности, которые попадают в зону прямого действия струй, внутренние полости, карманы и углубления, т. е. те поверхности, где скапливается наибольшее количество загрязнения, оказываются неочищенными, если не применять особые приспособления.
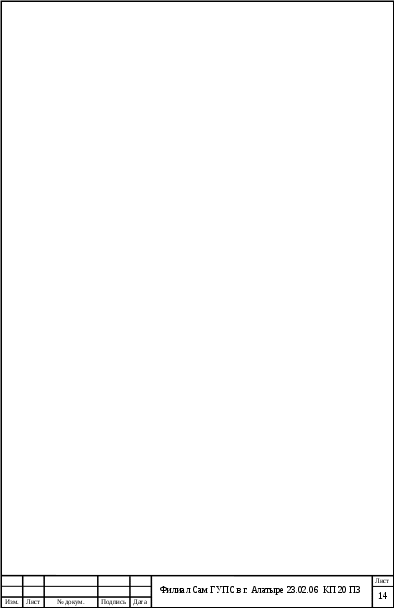
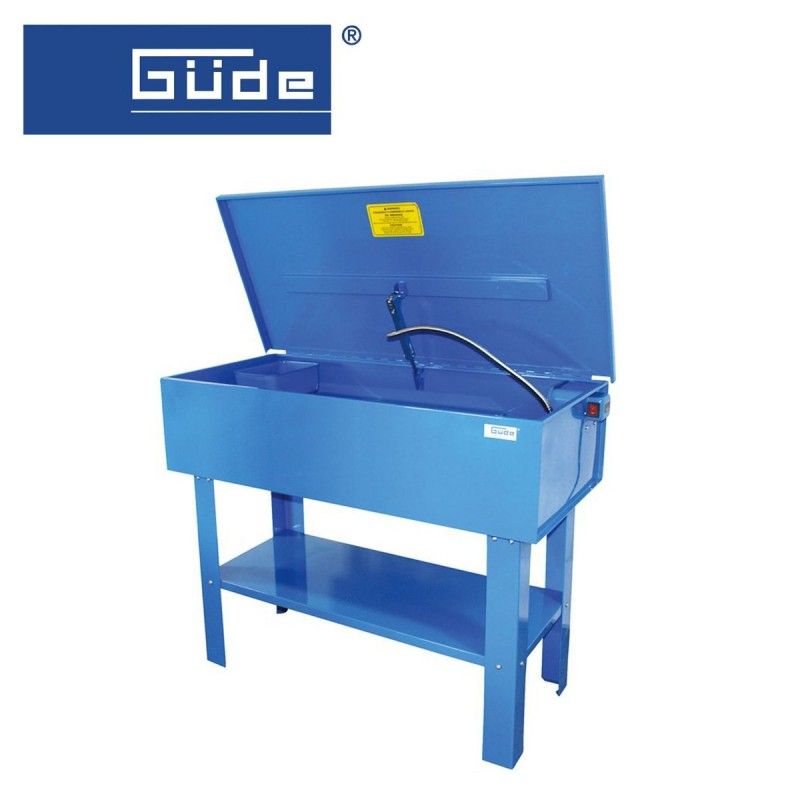
Рис.6- Мойка для очистки деталей
Очистка деталей в водных растворах заключается в следующем: под действием раствора, нагретого до 80-90° С, слой загрязнения смачивается и размягчается. Масляная пленка, расширяясь, разрушается, на поверхности детали образуются мельчайшие капли масла с грязевыми частицами. Для снижения силы сцепления в состав раствора вводят эмульгаторы, а чтобы ускорить отрыв капель, раствор заставляют принудительно перемещаться у очищаемой поверхности. Эмульгаторы обволакивают капли масла с загрязненными частицами особой пленкой, ослабляющей силу сцепления масла с металлом, и способствуют формированию мельчайших капелек масла в растворе, т. е. эмульсии. Присутствие в растворе эмульгаторов, а также хромпика или жировой смазки предохраняет детали от коррозии.
Ополаскивание деталей водой необходимо для удаления с поверхности деталей следов щелочи или кислоты, для предотвращения последующей коррозии металла, а также вредного влияния на кожу рук. Если ополаскивание ведется холодной водой, деталь после этого сушат, а если горячей водой, то процесс сушки отпадает.
Струйный способ очистки. При этом способе химическое действие раствора усиливается динамическим воздействием его струи. Давление, под которым моющие растворы подаются на очищаемые детали, изменяется в различных моечных машинах от 0,1 до 3, 5МПа.Моечные машины для струйной очистки принято делить на камерные (одно, двух и многокамерные) и конвейерные.
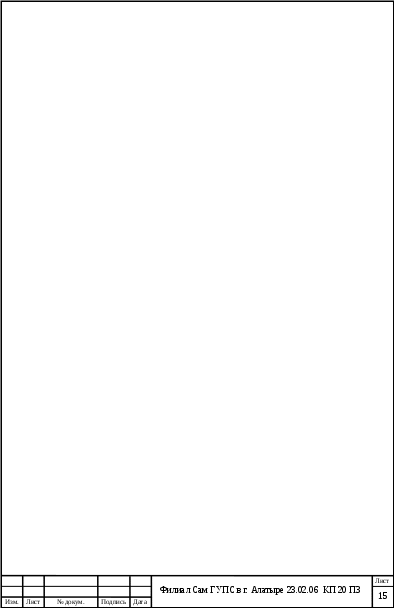
Очистка погружением. Объект ремонта при этом способе очистки погружается в ванну с горячим моющим раствором, циркулирующим у очищаемых поверхностей с помощью лопастных мешалок или гребных винтов. Применение для этих целей пара или воздуха не рекомендуется. Не создавая нужной турбулентности вокруг омываемых деталей, воздух (и пар) лишь взбалтывает осадок загрязнений в ванне и усиливает пенообразование. Кроме того, воздух охлаждает нагретый раствор и окисляет входящие в него компоненты. Недостаток очистки погружением - быстрое загрязнение раствора, а следовательно, необходимость частой его замены или фильтрации.
Очистка парами растворителя. Сущность этого способа состоит в следующем: в паровое облако достаточно сильного растворителя помещают в подвешенном состоянии холодную деталь, которая быстро покрывается конденсатом растворителя; растворитель, стекая с поверхности детали, уносит с собой частицы грязи. Процесс продолжается до тех пор, пока деталь не нагреется до температуры паров. В большинстве случаев этого времени оказывается вполне достаточно для очистки, так как процесс протекает весьма интенсивно. Чаще всего к рассматриваемому способу прибегают для удаления прочно приставшей пленки грязи с поверхности деталей с электрической изоляцией, т. е. якорей и катушек полюсов электрических машин и других массивных деталей. В качестве растворителя применяют трихлорэтилен и перхлорэтилен, температура кипения которых соответственно 87 и 121° С.
.
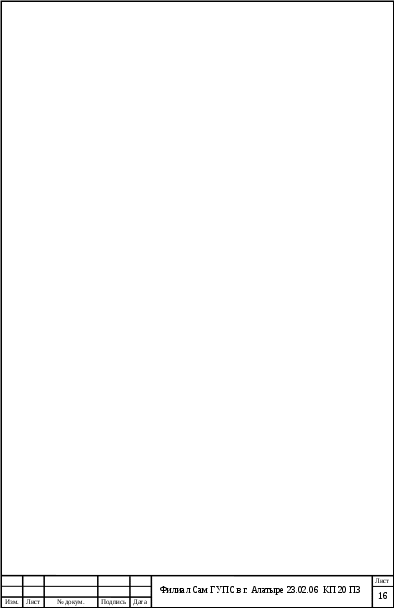
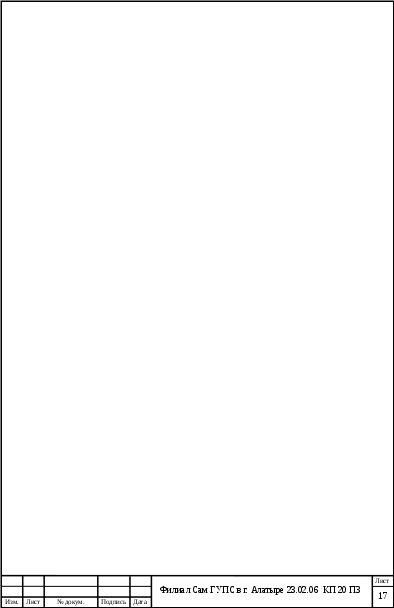
СПОСОБЫ ВОССТАНОВЛЕНИЯ)
Исправность щеточно-коллекторного узла проверяют при осмотре и необходимых измерениях. У исправных коллекторов поверхность гладкая, без выступающей слюды или отдельных пластин, вмятин, подгаров, эксцентриситета или биения. Щетки свободно скользят в обоймах щеткодержателей, без качки и с достаточной силой прижимаются к коллектору. Болты, траверсы, пальцы, на которых крепятся щеткодержатели, достаточно жесткие и не имеют вибраций, качки и т.п. Щетки должны быть одной марки, требуемого размера и притертыми к коллектору.
При техническом обслуживании пыль с коллектора и щеточного механизма удаляют пылесосом или продувкой сжатым воздухом; коллектор протирают салфеткой, смоченной спиртом. Проверяют легкость перемещения щетки в щеткодержателе.
Если щетка перемещается туго, необходимо почистить щеткодержатель и щетку. Зазор между щеткодержателем и коллектором должен быть в электродвигателях постоянного тока большой мощности 2 — 4 мм, в электродвигателях постоянного тока малой мощности 1—2,5 мм.
Люфт щетки в гнезде щеткодержателя в направлении вращения коллектора не должен превышать 0,1—0,2 мм при толщине щетки 8—16 мм и 0,15 — 0,25 мм при толщине свыше 16 мм.
Измеряют также давление щетки на коллектор. Под щетку подкладывают лист бумаги, а динамометр крепят к щетке.
Показание динамометра, при котором бумага легко вытаскивается из-под щетки, позволяет определить давление щетки на коллектор. Недостаточное давление щетки приводит к сильному искрению и ускоренному износу коллектора и щеток. Слишком сильное давление увеличивает силу трения в скользящем контакте, а также износ.
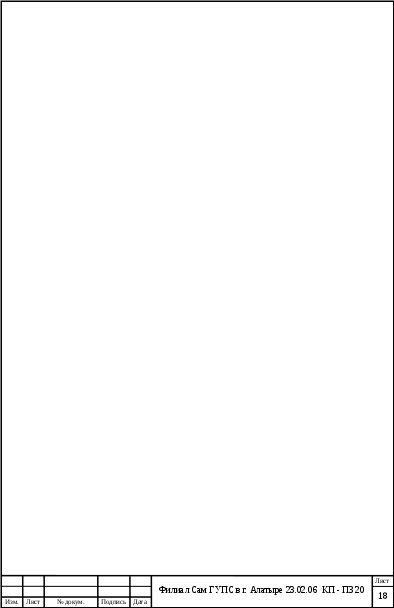
Для большего числа притираемых щеток применяют специальные станки с барабанами. На барабан, наружный диаметр которого на 1 мм меньше диаметра коллектора машины, устанавливают с помощью щеткодержателей щетки, обертывают барабан стеклянной бумагой, опускают на щетки нажимные рычаги и включают электродвигатель для вращения барабана. Щетки пришлифовываются и используются для одновременной замены. Это позволяет ускорить процесс замены щеток и исключить попадание пыли в щеточный механизм, что неизбежно происходит при притирании щеток непосредственно на машине.
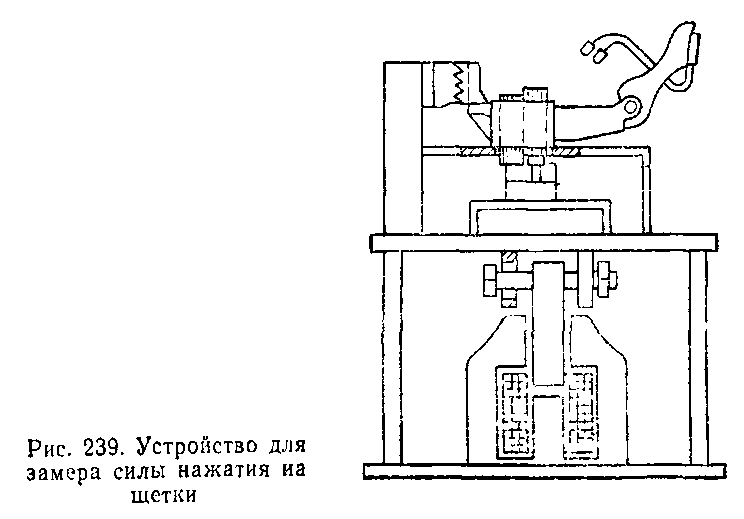
Рис. 7- Устройство для замера силы нажатия щетки
Крепление щеточных пальцев проверяют, покачивая их за концы, противоположные траверсе. При большой длине щеточных пальцев их скрепляют со стороны петушков коллектора с помощью кольца из изоляционного материала, которое крепят к щеточным пальцам болтами, ввернутыми в их торцы. Щетки сдвигают по длине коллектора, перемещая щеточные пальцы в головках траверсы. При неравномерном износе поверхности коллектора проверяют расстановку щеток, измеряя расстояние между торцом коллектора и крайними щетками на каждом щеточном пальце.