Файл: Современные металлорежущие станки обеспечивают исключительно высокую точность обработанных деталей.docx
Добавлен: 28.03.2024
Просмотров: 15
Скачиваний: 0
ВНИМАНИЕ! Если данный файл нарушает Ваши авторские права, то обязательно сообщите нам.
Система автоматизированного управления должна:
- вести постоянный контроль над технологическим процессом, состоянием технологического оборудования;
- обеспечить возможность управления процессами и оборудованием с помощью средств автоматики;
- обрабатывать показания аналоговых и дискретных датчиков и вести мониторинг технологического процесса с помощью пультов управления;
- производить диагностику и сигнализацию нарушений и аварийных ситуаций с их протоколированием;
Обеспечить возможность дистанционного управления регулирующими исполнительными механизмами;
Так же следует не забывать, что человек (выполняющий главенствующую роль в управлении процессом) подвержен влиянию множества внешних факторов. Поэтому следует также предусмотреть возможность слежения за действиями оператора, наложить ряд ограничений на ввод управляющих воздействий.
- автоматическая линия должна иметь центральный пульт управления для работы на наладочном и автоматическом режиме. Система автоматического управления должна обеспечивать невозможность самопереключения линии с наладочного на автоматический режим.
- все станки и агрегаты автоматической линии должны иметь самостоятельные органы управления для пуска и остановки их. Эти органы управления должны быть расположены так, чтобы обслуживающий персонал мог легко и быстро пользоваться ими.
- взаимная увязка работы узлов на агрегатных станках, получающих движение от гидроприводов, электрических или механических устройств, в автоматической линии должна быть обеспесчена надежной системой электрического управления и блокировкой.
- работа всех станков, работающих в автоматической линии, на автоматическом или наладочном режимах, во избежание аварий должна производиться в установленной технологическим процессом последовательности и иметь исправную систему блокировки для соблюдения этой последовательности.
2. РАСЧЕТНАЯ ЧАСТЬ
2.1. Расчет мощности электродвигателей фрезерного станка, их выбор и проверка по условиям пуска
1. Расчет и выбор двигателя главного привода фрезерного станка.
2. Определение параметров фрезы
3. Расчет технологического времени TМ
, мин
Усилие резания – окружное усилие при фрезеровании FZ,:
FZ = 9,81 × CF ×



FZ = 9,81 × 88 ×



где СF– силовой коэффициент обработки материала, от. ед. принимается по таблице 1, СF = 88;
ХF, YF, UF, qF - показатели степени принимаются по таблице 1, ХF = 1,1;
YF = 0,8;
UF = 0,95; qF = 1,1;
t - глубина резания, мм
S – подача на зуб фрезы принимается по таблице 2, S = 0,1 мм/зуб;
В – ширина фрезерования (фрезы), принимается по таблице 3, В = 50 мм;
z – число зубьев фрезы, принимается по таблице 3, z = 12шт;
Скорость резания VZ, м/мин
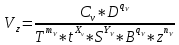
где СV – cкоростной коэффициент обработки материала, отн. ед. принимается по таблице 4, СV= ____;
ХV, YV, mV, UV, nV, qV - показатели степени принимаются по таблице 4, ХV = 0,1;
YV= 0,4; mV= 0,2; qV =; UV= 0,1; nV = 0,1
T - стойкость фрезы принимается по таблице 5, T = 180 мин

Мощность резания РZ, кВт
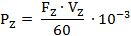

Расчетная мощность на валу главного привода РДР, кВт
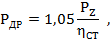
где ηСТ – КПД станка при номинальной нагрузке, отн.ед., ηСТ = 0,75…0,8
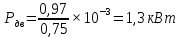
Определяем обороты двигателя (частоту вращения вала двигателя):
nдв.расч. = ʋб.пер./ρ,об/мин (5)
где: ʋб.пер. - наибольшая скорость быстрого перемещения, 2990, мм/мин;
ρ – радиус приведения от рейки стола к двигателю, 1,35 мм/об;
nдв.расч. = 2990/1,35 = 2214,8 об/мин
При выборе двигателя по мощности следует исходить из необходимости его полной загрузки в процессе работы. Кроме этого, необходимо выбирать двигатель таким образом, чтобы максимальная температура изоляции обмоток, не превышала допустимой величины. Это условие является одним из основных для обеспечения надежной работы электропривода в течение всего срока его эксплуатации.
Согласно условия РНОМ ≥ РДР выбирается асинхронный двигатель серии АИР80А2
РНОМ = 1,5 кВт
КПД = 78,5 %
UНОМ = 380 В
IНОМ = 3,46 А
cosφ = 0,84
МП/МНОМ = 2,2
ММАХ/МНОМ = 2,3
ММИН/МНОМ = 2,1
JД = 0,0011 кг м2
Для правильного выбора электродвигателей и всего электрооборудования следует учесть следующие условия:
Определение параметры фрезы.
Скорость вращения n:
n =

где n – скорость вращения, об/мин;
VZ – скорость резания, об/мин;
n =

Скорость продольной подачи фрезы VП, м/мин
Vп = S×z×n×10-3 м/мин (7)
Vп = 0,7 × 12 × 22,2 × 10-3 = 0,18 м/мин
Расчет технологического времени;
Технологическое время tМ, мин
tM =

tM =

Проверка двигателя по условиям пуска:
Максимальный статический момент нагрузки, Мст, Н
Мст =

Мст =

Определяем номинальный момент Мн, Н×м
Мн =

Мн =

Условие пуска:
Мн×1,2 ≥ Мст×0,8 (11)
193 × 1,2 ≥ 168×0,8
232 ≥ 134
Из проверки делаем вывод, что условие выполняется, двигатель проходит по условиям пуска. Окончательно принимаем двигатель серии АИР80А2 У2
2.2. Расчет и построение механической характеристики
Определяем номинальное скольжение:
SH =

где Sн – номинальное скольжение:
no -
SH =

Определяем критическое скольжение.
Sкр = SH × (λ+

где λ – кратность максимального момента;
Sкр = 0,02 × (2,2+

Определяем критический момент.
Мкр = λ × Мн
Мкр = 2,2 × 193 = 424,6Н×м (14)
Рассчитываем механическую характеристику.
Воспользуемся формулой Клосса.
М =

М =

М1 =

М2 =

М3 =

М4 =

М5 =

М6 =

М7 =

М8 =

М9 =

М10 =

Масштаб построения: 150 мм – Мmax
X =

X =

X1 =

X2 =

X3 =

X4 =

X5 =

X6 =

X7 =

X8 =

X9 =

X10 =

Полученные данные заносим в таблицу 1 для построения механической характеристики
Таблица 1. Данные для построения механической характеристики
S | 0,02 | 0,1 | 0,2 | 0,3 | 0,4 | 0,5 | 0,6 | 0,7 | 0,8 | 0,9 | 1 |
M (H×м) | 200 | 414 | 293 | 211 | 169 | 133 | 111 | 96 | 84 | 75 | 67 |
X, мм | 72 | 150 | 106 | 76 | 61 | 48 | 40 | 34 | 30 | 26 | 24 |