ВУЗ: Не указан
Категория: Не указан
Дисциплина: Не указана
Добавлен: 11.04.2024
Просмотров: 21
Скачиваний: 0
ВНИМАНИЕ! Если данный файл нарушает Ваши авторские права, то обязательно сообщите нам.
Установите в рабочее положение сепаратор для очистки охлаждающей жидкости.
Установите электрошкаф согласно установочному чертежу,
прикрепите шкаф к станине станка.
Проверьте вручную работу всех механизмов станка, пользуясь рукоятками и маховичками, чтобы ознакомиться с его
управлением.
Установите упоры реверса стола на наибольшую длину хода стола; установите рычаг регулирования скорости перемещения
стола при шлифовании на определенную скорость.
Удостоверьтесь, что выполнены все указания, относящиеся к
пуску станка и приведенные в разделах паспорта станка «Смазка станка», «Электрооборудование станка», «Регулировка станка».
Включите электродвигатели привода станка и удостоверьтесь в правильности направления их вращения.
Проверьте работу всех механизмов станка на холостом ходу,
как указано ниже.
2.2.2 Система смазки станка
Правильная и своевременная смазка станка круглошлифовального станка 3А10П является основным условием высокопроизводительной безаварийной работы станка, значительно увеличивает
срок его службы, предотвращает преждевременный износ деталей,
способствует сохранению первоначальной точности и чистоты
шлифования.
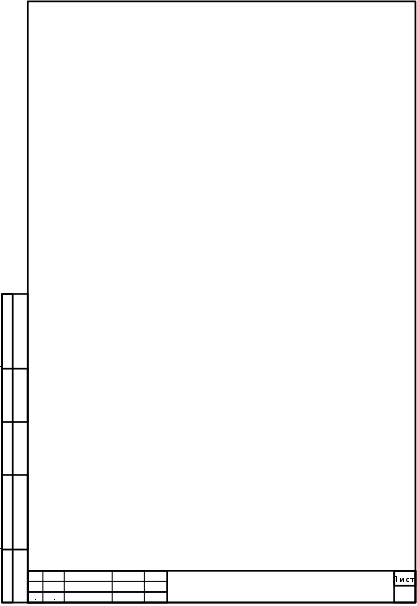
Вращение насоса осуществляется от механизма перемещения
стола.
Подшипники шпинделя шлифовальной бабки работают в
масляной ванне.
Бак смазки подшипников расположен в задней нише станка.
Он снабжен указателем уровня масла. Емкость резервуара составляет приблизительно 18 литров.
Полость корпуса шлифовальной бабки, в которой установлены шпиндель и его подшипники, должна быть полностью
заполнена маслом. Маслоуказатель, установленный на корпусе
шлифовальной бабки, во время работы шпинделя должен быть
заполнен маслом. Постоянная циркуляция масла в камере подшипников поддерживается насосной установкой в количестве одного литра в минуту. Производительность насоса регулируется переливным дросселем.
Масло из бака смазки подается через войлочный фильтр в камеру подшипников и возвращается обратно в бак через маслоуказатель шлифовальной бабки.
Масло рекомендуется менять один раз в 6 месяцев.
При замене масла следует:
1. Слить масло из бака и камеры подшипников.
2. Открыть крышку бака ипромыть его керосином.
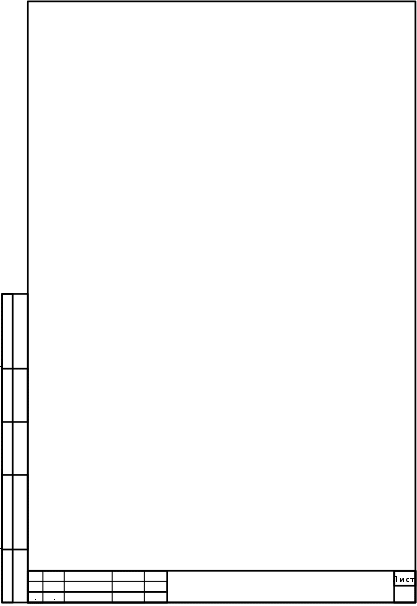
Промывку камеры подшипников повторить 2—3 раза.
4. Вынуть войлочный фильтр и заменить другим.
5. Залить чистое масло в бак.
Шлифовальная бабка установлена на салазки с шариковыми направляющими, которые набиваются консистентной смазкой при сборке станка.
Смазка подшипников бабки изделия осуществляется разбрызгиванием масла из картера бабки. Наличие смазки проверяется по маслоуказателю, расположенному на задней стенке бабки.
Масло в картер бабки доливается один раз в неделю.
Все места смазки нужно смазывать согласно прилагаемой схеме смазки
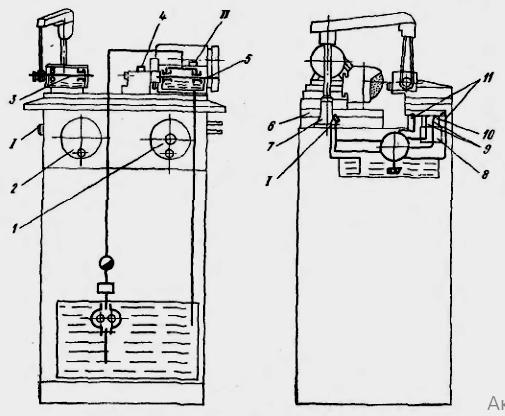
Рисунок 15 - Схема смазки станка 3А10П

№ по схеме | Наименование смазываемых частей механизмов | Способ смазки | Марка смазочного масла | Периодичность смазки и заполнения резервуара | Количество масла зали- ваемого и резервуар |
/ | Подшипники механизма по- дачи | Набивка | ЦИАТИМ-201 | При ремонте | |
2 | Подшипники механизма руч- ного перемещения стола | Набивка | УС-2 | При ремонте | |
3 | Подшипники бабки изделии | Залника | Индустриальное 20 | 1 раз и неделю | 0.3 л |
4 | Пниоль ладней бабкн | Пресс-масленка | УС-2 | 1 раз в месяц | |
5 | Подшипники шлифовальной бабкн | Автоматически | Велосит | 1 раз в 6 месяцев | 18 А |
6 | Направляющие и подшип- ники универсальных салазок | Набивка | ЦИАТИМ 201 | 1 раз в 6 мссниси | |
7 | Подшипники контрпривода | Набивка | ЦИАТИМ 201 | При ремонте | |
8 | Подшипники редуктора при- вода стола | I 1абнвка | ЦИАТИМ 201 | При ремонте | |
9 | Рычаги и муфты механизма реверса стола | Автоматически | ВНИИНП-401 | При ремонте | |
10 | Подшипники механизма ре- верса стола | Набивка | ЦИАТИМ 201 | При ремонте | |
11 | Направляющие станины и стола | Автоматически | ЦИИИИП401 | 1 раз в год | 5 А |
2.2.3 Требования по технической эксплуатации станка
Устанавливая на круглошлифовальном станке 3А10П переднюю и
заднюю бабки в соответствии с длиной обрабатываемого изделия, располагать их нужно симметрично, приблизительно посредине стола. Перед тем, как передвинуть переднюю и заднюю бабки, протереть стол. Протрите и смажьте центры передней и задней бабок перед установкой на них изделия.

Наличие грязи или пыли на центрах или в гнездах шпинделей препятствуют плотной посадке центров и ухудшает качество шлифования.
Убедитесь в отсутствии грязи и пыли в центровых отверстиях
изделия, при необходимости протрите их.
Неправильная форма центровых отверстий (овальность, неправильный угол и пр.) также приводит к отклонениям от правильной геометрической формы изделия и ухудшает качество шлифования. Центровые отверстия должны быть по возможности наименьшего диаметра.
Новый шлифовальный круг следует балансировать дважды: предварительно - до установки на станке и окончательно — после правки. Работа неотбалансированным кругом недопустима.
В конце смены рекомендуется прокрутить шлифовальный круг
на полной рабочей скорости в течение 1—2 минут, выключив охлаждсние, чтобы жидкость нескоплялась в порах нижней части круга и не нарушала балансировки.
Пользуйтесь люнетами при шлифовании длинных изделий, только при этом условии их можно прошлифовать с требуемой точностью.
При внутреннем шлифовании отодвиньте шлифовальную бабку
в заднее положение и закрепите, а на освободившееся на салазках место установите кронштейн для внутренней шлифовки. Установите на столе поворотную бабку изделия с патроном. Перед закреплением детали непосредственно на станке прошлифуйте кулачки патрона по диаметру,
соответствующему устанавливаемому изделию.

На фланец со ступицей поставьте картонную прокладку и наденьте шлифовальный круг.
Сверху поставьте картонную прокладку и металлическую шайбу. Закрепляется шлифовальный круг фланцевой гайкой.
Диаметр картонных прокладок должен быть несколько боль-
ше диаметра фланца.
Шлифовальный круг должен свободно надеваться на центрирующую ступицу фланца. Тугая посадка шлифовального круга на ступице фланца может привести к образованию трещин на круге.
Для снятия шлифовального круга с фланцами с шпинделя
необходимо пользоваться специальным съемником, поставляемым со станком.
Недопустимо использовать молотки и другие предметы для
съема шлифовального круга.
БАЛАНСИРОВКА ШЛИФОВАЛЬНОГО КРУГА
Отбалансируйте шлифовальный круг на приспособлении для
статической балансировки.
Шлифовальный круг с фланцами крепится на балансировочной оправке, которая поставляется со станком.
Балансировка производится изменением положения трех балансировочных сухарей в кольцевой выточке фланца шлифовального круга.
Установите шлифовальный круг на станке и начерно заправьте его. Затем снимите шлифовальный круг и снова отбалансируйте.
Следует иметь в виду, что по мере износа круга балансировка его может нарушиться вследствие неравномерной плотности абразивного материала.
Нарушение балансировки круга может привести к возникновению вибраций, нагреванию подшипников и т. д. Правильный способ устранения неполадок такого рода заключается в повторной балансировке шлифовального
круга.
ПРАВКА ШЛИФОВАЛЬНОГО КРУГА
Правка шлифовального круга оказывает существенное влияние
на производительность, точность и чистоту шлифования
Правильно выполняемая и достаточно частая правка обеспечивает сохранение хорошей режущей способности и правильной геометрической формы шлифовального круга.
Со станком поставляются три приспособления для правки шлифовального круга:
1) для правки круга при наружном шлифовании (оно установлено на задней бабке);
2) для правки торца круга и для правки под углом (устанавливается на столе);
3) для правки круга при внутреннем шлифовании (устанавливается на столе).
Подача круга на алмаз или твердосплавный ролик производится механизмом поперечной подачи, а при правке под углом перемещается правильный инструмент.
При правке круга при наружном шлифовании следует включать обильную подачу охлаждающей жидкости во избежание
нагревания и внезапного охлаждения алмаза, которое может вы-
звать растрескивание его.
Подача круга на алмаз за один проход не должна превышать 0,05 мм. Слишком быстрое продольное перемещение инструмента для правки относительно шлифовального круга снижает срок службы алмаза и ухудшает
чистоту шлифования.
Рекомендуемая скорость продольного перемещения алмаза при чистовом шлифовании составляет 50 …100 мм/мин и 150 …300 мм/мин при предварительном шлифовании.


На станке предусмотрено раздельное регулирование скорости перемещения стола при шлифовании и правке.
2.3 Ремонт оборудования
2.3.1 Подготовка станка к ремонту
При ремонте круглошлифовального станка 3А10П необходимо придерживаться определенного порядка действий для наиболее четкой организации и наилучшего проведения ремонтных работ. Последовательность этих действий такова: определение неисправностей механизмов; установление последовательности их разборки; разборка станка на сборочные единицы и детали, промывка их; определение характера и величины износа деталей, их дефектов; ремонт деталей; сборка механизмов с подгонкой деталей; проверка и регулирование собранного станка.
За подготовку оборудования для передачи в ремонт несет ответственность начальник производственного цеха или начальники участков. Перед ремонтом оборудование должно быть очищено от пыли, грязи, рабочих жидкостей.
Передача оборудования в капитальный ремонт оформляется специальным актом, составленным инспектором УГМ совместно с механиком производственного цеха. В акт заносят результаты внешнего осмотра и испытаний на ходу, а также замечания работающего на машине специалиста. Внешним осмотром устанавливают комплектность всех механизмов станка, определяют наличие неисправностей, а также задиров, забоин, вмятин, трещин, изломов, изгибов и других дефектов деталей, видимых без разборки механизмов, кроме того, оценивают состояние смазочных и защитных устройств.

недостатки свойственны ему при разных режимах работы, каково состояние механизмов и даже отдельных деталей. Прослушивая действующий станок, определяют, нет ли недопустимых шумов, стуков, вибраций. Все неисправности, зафиксированные в акте, учитывают при составлении окончательной ведомости дефектов на ремонт.
Во время ремонта к моменту сборки отдельные детали могут быть изготовлены или отремонтированы не полностью. Это усложняет процесс ремонта, поэтому он должен быть правильно организован и проводиться по графику, составленному заранее. Основой для составления графика является типовая технология ремонта, укрупненные нормы на выполнение ремонтных работ, а также продолжительность ремонта, которая должна соответствовать сроку, назначенному по плану. Кроме того, необходимо учитывать состав и квалификацию членов бригады. Длительность каждой операции на графике отмечается горизонтальной, а начало и конец – вертикальными линиями.