ВУЗ: Не указан
Категория: Не указан
Дисциплина: Не указана
Добавлен: 11.04.2024
Просмотров: 22
Скачиваний: 0
ВНИМАНИЕ! Если данный файл нарушает Ваши авторские права, то обязательно сообщите нам.
Если станок отправляется для ремонта в специализированный ремонтно-механический цех предприятия, то он транспортируется к месту ремонта. Вместе со станком, что отправляется в специализированный ремонтный завод или цех, должна быть направлена следующая техническая документация:
-документы, которые прибыли со станком с завода-производителя (технический паспорт, руководство по эксплуатации, заводской акт приемки ;
- акт технического осмотра перед ремонтом;
- ведомость комплекта деталей и узлов, которые направляются в ремонт вместе со станком.
Перед разборкой станка для ремонта из резервуаров сливаются масло и охлаждающая жидкость. Станок должен быть очищен от стружки, грязи, пыли и масла. Площадка около ремонтируемого станка освобождают от загромождения и оснащают подъемно-транспортными средствами, необходимыми для разборки или ремонта, если ремонт ведется без снятия станка с фундамента. Подготовив площадку и очистив станок, электромонтер отключает его от электросети, изолирует концы оставшихся проводов и кабельных выводов, снимает предохранители с электрощита. Далее со станка снимаются приводные ремни, полумуфты вала двигателя и на месте ремонта вывешивается табличка "Не включать - ремонт!».

Необходимо все детали очистить от пленок окислов, масла и грязи. Эта операция является очень ответственной, потому что цель ее не только придать деталям опрятный вид, а главным образом выявить наличие износа и определить степень ее пригодности для дальнейшей эксплуатации.
При очистке и промывке деталей особое внимание следует обратить на правильность выбора промывочного раствора, поскольку отдельные компоненты этого раствора (например, щелочи, кислоты и т. д.) могут войти в реакцию с металлом и еще больше ухудшить рабочую поверхность. Особенно осторожно нужно применять растворы для промывания деталей из цветных металлов, в частности алюминиевых, цинковых и медных сплавов.
В процессе разборки станка промывку деталей рекомендуется проводить непосредственно в местах разборки станка, пользуясь также передвижным промывочным устройством, которое обычно состоит из ванн предварительной и окончательной промывки.
2.3.2 Разборка станка
Разборка круглошлифовального станка модели 3А10П может начинаться только после того, как будет проверено состояние станка и в акте разборки отмечено некомплектность и износ отдельных деталей
При осмотре станка, который поступил в ремонт, проверяют наличие и комплектность всех его механизмов и узлов. Испытанием станка на ходу обнаруживают шумы, вибрации, степень нагрева деталей во время их работы. При опросе шлифовщика, работающего на станке, получают дополнительные сведения о состоянии механизмов, узлов и даже отдельных деталей.

- разборку необходимо вести в порядке, обратном сборке;
-разборка должен выполняться с минимальными затратами труда;
-последовательность разборки устанавливается только после изучения конструкции станка и его узлов;
-разборка должен проводиться по отдельным узлам;
-необходимо выявить направления, по которому необходимо выпрессовывать втулки, выбивать штифты и так далее;
-разборку станка необходимо вести нормальными инструментами и приспособлениями, исключая вероятность порчи годных деталей
-удары молотком можно наносить по деталям только с помощью прокладки или выколотки из дерева или мягкого металла;
-детали станка следует снимать при разборе аккуратно, без перекосов и каких-либо повреждений;
-не следует применять больших усилий при снятии деталей, так как при внимательном рассмотрении причины, которая мешает снятию деталей, ее легко обнаружить и обезвредить;
-детали, которые снимаются при разборке для каждого узла, следует складывать в отдельные ящики и не накапливать одну деталь на другую;
-болты, шайбы и другие нормальные детали станка необходимо складывать в специальный ящик.
-необходимо маркировать снимаемые детали .
Разборка на узлы станка модели начинается с подготовки станка к ремонту. Перед демонтажем и разборкой надо станок отключить от электросети, снять с него электропроводку, которая может мешать разборке (эти операции выполняют электромонтеры), слить масло из резервуаров, слить охлаждающую жидкость из резервуара. Затем отвинчивают гайки фундаментных болтов (если станок намечено передать для ремонта в ремонтно-механический цех), снимают все кожухи и щитки, закрывают доступ к узлам, которые разбираются, удаляют арматуру системы охлаждения.
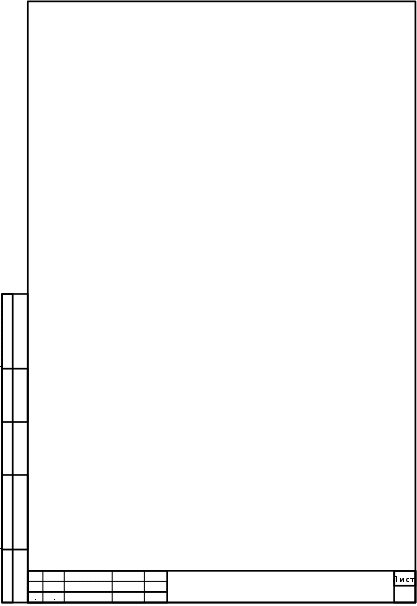
В разобранном состоянии все детали промывают и готовят к дефектации.
После промывки все детали подлежат дефектированию. Выполняется проверка деталей, степень их износа. Разделяют детали на пригодные, подлежащие восстановлению и замене и затем их красят в нужный цвет. Составляется дефектная ведомость и после этого начинается ремонт.
Таблица 4 - Последовательность разборки станка 3А10П
№ операции | Наименование операции | Содержание операции | Наименование и модель станка |
005 | Подготовка станка к ремонту | Промыть станок в сборе и протереть. Провести осмотр и выявить внешние дефекти деталей и узлов. Провести проверку станка по нормам точности | - |
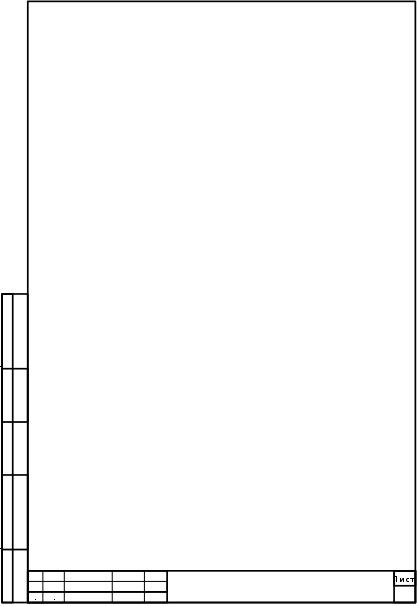
№ операции | Наименование операции | Содержание операции | Наименование и модель станка |
005 | Подготовка станка к ремонту | Промыть станок в сборе и протереть. Провести осмотр и выявить внешние дефекти деталей и узлов. Провести проверку станка по нормам точности | - |
010 | Разборка станка на узлы | Провести демонтаж; электрооборудования, системы охлождения с насосом, шпиндельной головкой, стола с магнитною плитою, станины | Электроталь |
015 | Разборка узлов станка на детали | Розборка станка на детали и узлы : шпиндельную головку, стол, станину. | Электроталь |
020 | Промывка и подготовка деталей к дефектации | Очистка деталей, в том числе корпусных, от грязи и старой краски, промыть и протереть. Скомплектовать по узлам для дефектации. | Моечная машина |
2.3.3 Дефектация деталей при ремонте
При дефектации деталей узла бабки изделия круглошлифовального станка модели 3А10П выявляют дефекты и определяют возможность дальнейшего использования деталей, необходимость их ремонта или замены. При этом составляют дефектную ведомость.
Дефектную ведомость составляют ремонтный мастер, представитель ОТК и конструктор отдела главного механика.
В начале ремонта при разборке станка составляется уточненная ведомость дефектов. При разборке оборудования на узлы и детали в процессе капитального ремонта производят контроль и сортировку деталей на следующие группы:
- годные, не имеющие повреждений и имеющие размеры в пределах допускаемых отклонений;

- негодные, подлежащие замене.
В ведомости учитываются все предварительные данные указанные к предварительной дефектации и подробно перечисляются дефекты в целом, каждого узла в отдельности и каждой восстанавливаемой детали.
Окончательные результаты контроля и сортировки деталей с указанием метода ремонта мастер заносит в «Дефектную ведомость», являющуюся основным документом, определяющим объем ремонтных работ.
При проведении дефектации рационально использовать заранее заготовленные типовые ведомости дефектов. Эти ведомости отличаются от обычных тем, что в них внесены все изнашиваемые детали станка, определены различные возможные виды дефектов детален и узлов и перечислены операции или даны краткие описания конкретных работ, подлежащих выполнению при ремонте. Такая ведомость представляет собой документ, синтезирующий опыт наиболее знающих работников ремонтной службы.
При использовании типовой ведомости процесс дефектации в основном сводится к сверке обнаруженных дефектов ремонтируемых деталей с перечнем дефектов в типовой ведомости. Найдя в ведомости обнаруженный у детали дефект, подчеркивают соответствующий порядковый номер, операцию, группу операций и ремонтных работ. Если в типовой ведомости отсутствует нужная деталь или не предусмотрен возможный дефект у какой-либо детали, тогда в ведомости делают соответствующую дополнительную запись.
После оформления ведомости на ремонт осуществляется конструкторская проработка чертежей для проведения ремонта и изготовления деталей, а также оформляется технологическая документация. Эта ведомость является документом, по которому контролируют ход
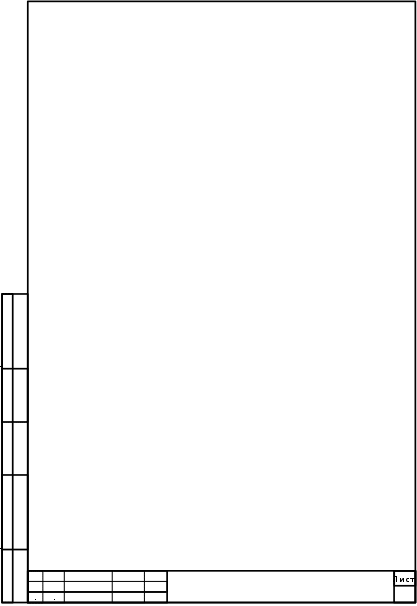
Оформленную «Дефектную ведомость» утверждает главный механик. Все данные о ремонте оборудования находятся у главного механика. В процессе ремонта представитель ОТК сверяет с дефектной ведомостью ход работы и делает в ведомости соответствующие отметки.
При дефектации выполняют следующие операции. Внешний осмотр, проверкой на ощупь, простукиванием выявляют наружные дефекты. Далее, используются универсальный и специальный измерительный инструмент, определяют геометрические параметры деталей. Для обнаружения скрытых дефектов, проверки на герметичность, упругость, контроля взаимного положения элементов деталей используют специальные приборы и приспособления.
При сортировке деталей по группам рекомендуется их помечать
краской: годные — голубой, ремонтно-пригодные — желтой, негодные — красной.
В зависимости от назначения детали или от предполагаемого дефекта процесс дефектации производят различными способами.
Существует несколько способов дефектации деталей:
1. Наружный осмотр, позволяет определить наличие на детали трещин, забоин, раковин, изгибов, отклонения от форм и т.д.
2. Измерение, позволяет определить величину износа отклонение от правильной геометрической формы и взаимного расположения поверхностей.
3. Остукивание, деталь остукивается мягким молотком или рукояткой молотка, что позволяет обнаружить наличие трещин о чем свидетельствует дребезжащий звук.
4. Гидравлическое (пневматическое) испытание, применяется для корпусных деталей. Деталь собирают, ставят заглушки во все отверстия кроме одного и закачивают в него под давлением жидкость (воздух).

6. Магнитная и ультразвуковая дефектоскопия, позволяет обнаружить скрытые дефекты (трещины, раковины) стальных и чугунных изделий. Действие основано на различной магнитной проницаемости сплошного металла и металла имеющего дефект.
7. Люминесцентный способ, позволяет обнаружить наружные трещины. На поверхность детали наносятся люминесцентный раствор, через 10 - 15 сек поверхность протирают и просушивают, наносят тонкий слой порошка (тальк, углекислый магний) впитывающего раствор из трещин или пор, затем деталь осматривают в затемненной комнате в ультрафиолетовых лучах. Расположение трещин определяется по свечению люминофора.