Файл: 2 Расчетнотехнический раздел 1 Технология проведение работ.doc
ВУЗ: Не указан
Категория: Не указан
Дисциплина: Не указана
Добавлен: 24.04.2024
Просмотров: 11
Скачиваний: 0
ВНИМАНИЕ! Если данный файл нарушает Ваши авторские права, то обязательно сообщите нам.
2.1.4 Методы борьбы с эмульсией при эксплуатации скважин штанговыми насосами
Существуют следующие способы разрушения нефтяных эмульсий:
–отстаивание;
–фильтрация;
–центрифугирование;
–термическое воздействие;
–электрическое воздействие;
–внутритрубная деэмульсация;
–воздействие магнитного поля.
Отстаивание применяют при высокой обводненности нефти и осуществляют путем гравитационного осаждения диспергированных капель воды. На промыслах применяют отстойники периодического и непрерывного действия разнообразных конструкций*. В качестве отстойников периодического действия обычно используют сырьевые резервуары, при заполнении которых сырой нефтью происходит осаждение воды в их нижнюю часть. В отстойниках непрерывного действия отделение воды происходит при непрерывном прохождении обрабатываемой смеси через отстойник. В зависимости от конструкции и расположения распределительных устройств движение жидкости в отстойниках осуществляется в преобладающем направлении v горизонтально или вертикально.
Фильтрацию применяют для разрушения нестойких эмульсий. В качестве материала фильтров используются вещества, не смачиваемые водой, но смачиваемые нефтью. Поэтому нефть проникает через фильтр, а вода - нет.
Целью использования центрифуги является повышение эффективности разделения на фазы водонефтяной эмульсии, сокращение количества аппаратов, используемых в схемах промысловой подготовки нефти и газа, т.е. снижение металлоемкости добывающей нефтяной промышленности, удаление вместе с водой присутствующих в ней механических примесей, т.е. повышение эксплуатационной надежности промысловых трубопроводов.
Термическое воздействие на водонефтяные эмульсии заключается в том, что нефть, подвергаемую обезвоживанию, перед отстаиванием нагревают до температуры 45-80 0С. При нагревании уменьшается прочность слоев эмульгатора на поверхности капель, что облегчает их слияние. Кроме того, уменьшается вязкость нефти и увеличивается разница плотностей воды и нефти, что способствует быстрому разделению эмульсии. Подогрев осуществляют в резервуарах, теплообменниках и трубчатых печах.
Воздействие на эмульсии электрическим полем производят в электродегидраторах, снабженных электродами, к которым подводится высокое напряжение переменного тока промышленной частоты. Под действием электрического поля на противоположных концах капель воды появляются разноименные электрические заряды. В результате капли притягиваются, сливаются в более крупные и оседают на дно емкости.
Внутритрубную деэмульсацию проводят посредством добавления в эмульсию химического реагента-деэмульгатора. Это позволяет разрушать эмульсию в трубопроводе, что снижает ее вязкость и уменьшает гидравлические потери.
Ультразвуковое и магнитное поле воздействуют на поверхностно активные вещества, составляющие бронирующие оболочки глобул воды. Зарядовые ПАВ ориентируются в постоянном магнитном поле согласно силе Лоренца, а парамагнитные частицы – согласно силам обменного взаимодействия. В результате оболочка глобул деформируется, «раскачивается» и разрывается, освобождая капельки воды, которые коагулируют и осаждаются.
2.2 Расчеты технологических процессов
2.2.1 Расчет глубины погружения насоса под динамический уровень
Исходные данные:
D=32 мм- диаметр плунжера насоса;
d=14 мм- диаметр отверстия в седле всасывающего клапана;
S=1,5 м- длина хода сальникового штока;
n=8- число качаний в минуту;
ν=1,05·10-5- кинематическая вязкость нефти;
Py=30 кПа- упругость паров откачиваемой нефти;
ρ=850 кг/м3- плотность нефти.
Минимальное погружение насоса под динамический уровень:
![]() |
где F – площадь сечения плунжера, м2;
f0 – площадь сечения отверстия в седле всасывающего клапана, м2;
μ – коэффициент расхода, характеризующий пропускную способность клапана и являющийся функцией числа Рейнольдса;
Значение μ находят по графику [7,стр.100] (рис.1)
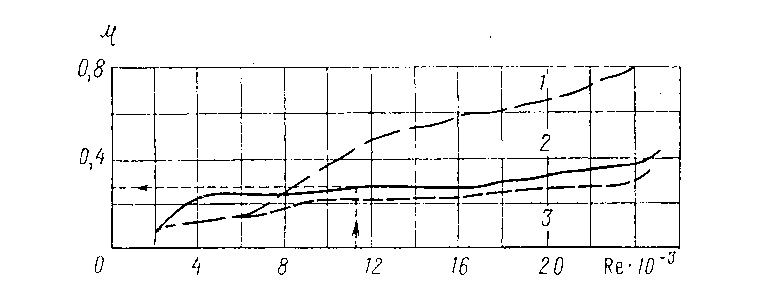
График для определения коэффициента расхода для различных клапанов штанговых насосов. [7,стр100]
Клапан: 1 - завода им. Дзержинского; 2 – нормального исполнения; 3 – закрытого типа
Число Рейнольдса:

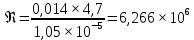
где υ– максимальная скорость жидкости в седле клапана, м/с:
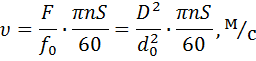
=

По кривой μ=f(Rе), (рис.VI.4), для одинарных клапанов нормального исполнения открытого типа находим μ=0,2
По формуле (VI.7)определяем минимальное погружение насоса под динамический уровень.

hн min

Таким образом, при погружении насоса более чем на 3,41 м будет обеспечено условие, необходимое для поступления жидкости в цилиндр насоса.
2.2.2 Расчет и подбор колонны насосных штанг.
Исходные данные:
D=32 мм- диаметр плунжера насоса;
L=500 м- глубина;
ρ=850 кг/м3- плотность нефти;
ρш=7850 кг/м3- плотность материала штанг;
S=1,5 м- длина хода сальникового штока;
n=8- число качаний в минуту.
А.С. Вирновский, пользуюсь зависимостью И.А. Одинга, предложил на основе элементарной теории расчетное уравнение для определения приведенных напряжений в любом сечении колонны насосных штанг:
ϭпр =


где ϭmax – максимальное напряжение в опасном сечении колонны, которое равно ϭср + ϭа. Здесь ϭср – среднее напряжение цикла, действующее на верхнее сечении колонны штанг, определяемое по формуле:
ϭср=Lg
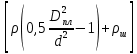
Приняв предварительно диаметр штанг d = 16 мм, получим по формуле (VI.32);
Ϭср = 500
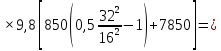

Ϭа = Lg(575
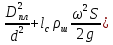
Ϭа=500



где lc = 1.05 – средний кинетический коэффициент станка-качалки; ω = πn/30 = =3,14·12/30 = 1,255 – угловая скорость кривошипа.
Следовательно,
По формуле [7,стр.122] (7);
Ϭmax = 42,63+16,13 = 58,76·106 Па.
Проверим напряжение в точке подвески штанг, для чего определим максимальную нагрузку на штанги, польюсь статическим методом по формуле (VI.22);
Pmax = Pж + Рш (b +

Pmax=67,9


где b – коэффициент, учитывающий потерю веса штанг в жидкости; Fпл = 67,9 см2 – площадь сечения плунжера диаметр 32 мм; qш = 3,14 кг – масса 1 м штанг диаметром 19 мм с муфтами.
Максимальное напряжение в точке подвески штанг;
ϭ΄max = Pmax/fш = 43,02


где fш = 3,8·10-4 м2 – площадь сечение штанг.
Подберем сталь для штанг, исходя из установленных норм допускаемых приведенных напряжений ϭпр.
В данном случае по приведенному напряжению подходят нормализованные никельмолибденовые (НМ) штанги с dш = 19 мм. Они же удовлетворяют требованию о максимальной допустимом напряжении (130 МПа) В небольших количествах выпускаются штанги с допускаемыми напряжениями (150 МПа). Следовательно, эти соответствуют условиям работы.
2.2.3 Расчет технологической эффективности.
Таблица 6 – Исходные данные;
Скважина | до | после | прирост | |||||
Дебит нефти, т/сут | Дебит жидкости, т/сут | Обвод. | Дебит нефти, т/сут | Дебит жидкости, т/сут | Обвод. | Дебит нефти, т/сут | Дебит жидкости, т/сут | |
1 | 0,49 | 8 | 94,5 | 0,81 | 11,1 | 94 | 0,33 | 3,1 |
2 | 1,49 | 7,2 | 82,3 | 2,1 | 8,43 | 73,1 | 0,57 | 1,24 |
ИТОГО среднее значение | 0,99 | 7,6 | 88,4 | 1,45 | 9,71 | 83,5 | 0,44 | 2,17 |
Произведем расчет технологической эффективности по двум скважинам по нефти.
Производим расчет объем добычи при базовом дебите нефти
????нб=????н0∙Т∙????,т [5, стр.4](8)
где ????н0 –дебит скважины до ГТМ,т
Т- период между обработками, сут (принимаем 188 сут)
η- коэффициент эксплуатации скважин (принимаем 0,78)
-
????н1 –дебит скважины после ГТМ, т.
????нб1 = 0,49·188·0,78 = 71,8 т
????нб2 = 1,49·188·0,78 = 218,4 т
-
Производим расчет планируемой добычи нефти.
????нф = ????нб +
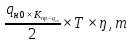
Qнф1 = 71,8 +
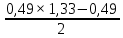

Qнф1 = Qнф1 = 218,4 +
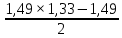

3. Расчет дополнительной добычи по скважинам.
∆????= ????нФ − ????нб, т [5, стр.4](10)
∆????н1 = 82,8 – 71,8 = 11 т
∆????н2 = 252,1 – 218,4 = 33,7 т
4. Дополнительная добыча по двум скважинам.
∆????общ = ∆????1 + ∆????2 + ∆????3, т [5, стр.4](11)
∆????общ = 11 + 33,7 = 44,7 т
5.Произведем расчет технологической эффективности по двум скважинам по жидкости.
????жб = ????ж0 ∙ Т ∙ ????,т [5, стр.4](12)
????жб1 = 8 ∙ 188 ∙ 0,73 = 1093 т
????жб2 = 7,2 ∙ 188 ∙ 0,73 = 988 т
6.Производим расчет планируемой добычи жидкости
????жф = Qжб +
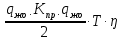
Qжф = 1093 +

Qжф = 988 +

7.Расчет дополнительной жидкости по скважинам.
∆???? = ????жф − ????жб, т [5, стр.4](14)
∆????ж1 = 1274,1 – 1093 = 181,1 т
∆????ж2 = 1151 – 988 = 163 т
8.Расчет дополнительной жидкости по трем скважинам.
∆????общ = ∆????1 + ∆????2, т [5, стр.4](15)
∆????общ = 181,1 + 163 = 344,1 т
По результатам расчета получили дополнительную добычу нефти по трем скважинам равную 44,7 т и по жидкости 344,1 т
2.3 Промышленная и экологическая безопасность при эксплуатации скважин, эксплуатируемых штанговыми насосами.
Промышленная.
Основные положения техники безопасности при эксплуатации скважин штанговыми насосными установками - ограждение движущихся частей станка-качалки и правильное выполнение требований при ремонте. С внедрением однотрубной системы сбора и транспорта продукции нефтяных скважин серьезные требования предъявляются к оборудованию устья скважины. При сравнительно высоких устьевых давлениях (2,0 МПа и выше) оборудование должно иметь достаточный запас прочности. Необходимо эксплуатировать только стандартное оборудование устья скважин, опробованное и принятое к серийному производству, в частности, устьевые сальники с самоустанавливающейся головкой типа СУ С1-73-25, рассчитанные на рабочее давление 2,5 МПа, и СУС2-73-40 - на давление 4,0 МПа.