Файл: 1. 1 Характеристика депо и производственного участка (отделения).docx
Добавлен: 28.04.2024
Просмотров: 19
Скачиваний: 0
ВНИМАНИЕ! Если данный файл нарушает Ваши авторские права, то обязательно сообщите нам.
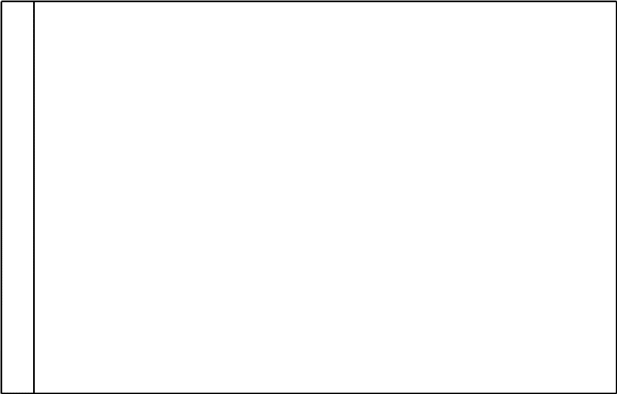
СОДЕРЖАНИЕ
Введение………………………………………………………………………….2
1 Теоретическая часть
1.1 Характеристика депо и производственного участка (отделения)….….….3
1.2 Технология ремонта…………………………………………………....……4
1.3 Оборудование участка (отделения) ………………………………………..6
1.4 Организация технологического процесса………………………………….7
1.5 Организация рабочих мест………………………………………….……...11
1.6 Механизация и автоматизация производственного процесса…….……..14
1.7 Мероприятия по охране труда и экологической безопасности……….…16
2 Расчетная часть
2.1 Определение фондов времени………………………………………..…….24
2.2 Расчет производственной программы………………………………….….25
2.3 Определение размеров участка (отделения) ………………………….…..28
2.4 Определение штата работников участка (отделения) …………….….…..29
2.5 Определение годового фонда заработной платы участка (отделения)….32
Заключение……………………………………………………………………....38
Список использованных источников………………………………………..…39
ВВЕДЕНИЕ
Транспортная система является неотъемлемой частью производственной и социальной инфраструктуры государства, обеспечивая ее территориальную целостность и национальную безопасность.
Главной задачей вагонного хозяйства является полное удовлетворение потребности государства в перевозках грузов и пассажиров. Для выполнения этой задачи в первую очередь необходимо иметь такой вагонный парк, который по своему техническому уровню и условиям прочности отвечал бы перспективным требованиям эксплуатации, кроме того, необходимо иметь такую систему ремонта и технического содержания вагонов, которая бы обеспечила надежную работу вагона в период между плановыми ремонтами.
Эффективное использование парка пассажирских вагонов неразрывно связано с улучшением организации ремонта вагонов на вагоноремонтных предприятиях.
С целью повышения эффективности производства, улучшения качества ремонта вагонов в вагонных депо совершенствуются технологические процессы ремонта вагонов и их узлов, вводятся в эксплуатацию новые высокопроизводительные машины и механизмы, широко внедряется более прогрессивный поточный метод деповского ремонта вагонов.
В дипломном проекте, в теоретической части, мною были рассмотрены такие вопросы, как характеристика депо и производственного участка, технология ремонта вагона, организация технологического процесса и организация рабочих мест в вагоносборочном участке. Рассмотрены мероприятия по охране труда и экологической безопасности.
В расчетной части проекта рассмотрены параметры производственного процесса на основе внедрения поточного метода ремонта вагонов, определена производственная мощность депо, его размеры, так же рассчитаны контингент работников и фонд заработной платы вагоносборочного участка.
1 ТЕОРЕТИЧЕСКАЯ ЧАСТЬ
1.1 Характеристика депо и производственного участка (отделения)
Вагоносборочный участок (ВСУ) служит для производства разборочных и ремонтно-сборочных работ на вагоне, которые выполняются в соответствующих отделениях.
В отделении очистки пассажирские вагоны проходят наружную обмывку в ангаре моечной машиной.
Отделение подготовки вагонов к ремонту служит для уравнивания объема работ на вагонах с повышенным износом. Здесь выполняются разборочные, газосварочные работы на раме и кузове вагона. Оно располагается вне основного здания.
Ремонтно-сборочное отделение предназначено для производства разборочных и ремонтно-сборочных работ на раме и кузове вагона.
На вагоноремонтных машинах дополнительно к основным устройствам предусмотрены сверлильные электрические машинки, электрические молотки, резьбонарезные машины. Для хранения материалов и запасных частей имеются стеллажи и стенды. Рабочие места оборудуют раздаточными колонками сжатого воздуха, розетками для подключения электросварочных аппаратов и электрического инструмента. Передвигаются вагоны с позиции на позицию с помощью конвейера. Для подъёмки вагонов и перемещения тяжёлых деталей устанавливаются два мостовых крана грузоподъёмностью 10т.
На участке организованы поточно-конвейерные линии для ремонта вагонов. Ремонт осуществляется на четырёх позициях. На нулевой позиции, расположенной перед вагоносборочным участком, подготавливают вагон к ремонту.
На первой позиции устраняют дефекты металлических элементов рамы, производят сварочные работы. Изгибы, вмятины, прогибы и другие дефекты рамы вагона устраняют при помощи механизмов и приспособлений, размещённых на арочных эстакадах. Для транспортировки тяжёлых деталей используют мостовой кран.
На второй позиции заканчивают сварочные работы, демонтируют автосцепку, снимают концевые краны, ремонтируют автотормозное оборудование. Ремонтные работы выполняют с использованием тех же механизмов, что и на первой позиции.
На третьей позиции поточной линии вагон поднимают при помощи электродомкратов. При помощи приспособления заменяют поглощающие аппараты, ремонтируют неисправные элементы рамы и несъёмные детали автосцепного устройства,
устанавливают отремонтированные автосцепки, испытывают автотормоза при помощи специального испытательного стенда. Тележки выкатывают и передают в отделение ремонта тележек. Отремонтированные тележки поступают назад на трансбордере по пути.
Размещается ВСУ в центральном пролете здания депо.
С ВСУ связаны основные производственные участки, сформированные по принципу узлового метода ремонта, то есть ремонта узлов, снятых с вагона: тележек, колесных пар, автосцепного оборудования и т.д.
1.2 Технология ремонта
Существует шесть методов ремонта вагонов:
- стационарный метод предусматривает технологию, при которой вагоны и установки, поданные в ремонт, находятся на одной и той же позиции от начала и до конца работ. Этот метод способствует сокращению простоя вагона в ремонте вследствие замены неисправных узлов и деталей заранее отремонтированными.
- поточный метод является более высокой формой организации ремонта по сравнению со стационарным. Поточный метод характеризуется разделением комплекса операций, закрепленных за отдельными рабочими позициями.
- поточно-конвейерный метод представляет собой улучшенный поточный метод. Он нашел применение не только при ремонте вагонов, но и при ремонте их деталей и узлов.
- агрегатный метод позволяет неисправные агрегаты заменять на заранее отремонтированные или новые;
- пригоночный метод - это индивидуальный метод, характеризуемый тем, что ремонтируемый объект разбирается на отдельные сборочные единицы, а они - на детали; неисправные заменяют, а остальные (исправные) не обезличиваются, а устанавливаются в тот же узел или агрегат.
На вагоноремонтных предприятиях применяются стационарный и поточный методы организации процессов производства. Ведущее место принадлежит поточному методу, отличающемуся высокой эффективностью.
Стационарный метод более простой. Он характеризуется большой продолжительностью цикла и сравнительно низкой производительностью. Сущность его состоит в том, что все работы от начала до конца выполняются на немногих или даже на одном рабочем месте. За пределы этого места выносятся только те операции, выполнение которых связано с применением специального оборудования.
Поточным методом организации производства называется такой, при котором производственный процесс обработки детали или сборки изделия расчленяется на равные по продолжительности операции, выполняемые на специализированных рабочих местах (позициях). Позиции располагаются в последовательности технологического процесса, при этом обрабатываемая деталь или собираемое изделие перемещается с каждой предыдущей позиции на последующую без задержек и, как правило, при помощи специальных транспортных средств.
В поточном производстве наиболее полно осуществляются пропорциональность, ритмичность, параллельность и непрерывность процессов на основе широкого использования комплексной механизации и автоматизации, и прогрессивных форм организации труда.
Производство, организованное по поточному методу, характеризуется следующими признаками:
- разделением производственного процесса на составные одинаковые или кратные по трудоемкости выполнения операции и установлением рациональной их последовательности;
- распределением операций по определенным рабочим местам и последовательным расположением рабочих мест и оборудования по ходу технологического процесса;
- специализацией рабочих мест на выполнении определенных операций;
- выполнением операций с возможно меньшими перерывами (почти непрерывно) с единым для всего производственного цикла ритмом;
- осуществлением межоперационной передачи обрабатываемых деталей, собираемых узлов или изделия в целом поштучно или небольшими партиями с одной позиции на другую;
- одновременностью выполнения работ на всех рабочих местах поточной линии, когда в каждый момент на линии имеется несколько экземпляров предмета труда на разных операциях технологического процесса;
- высокой степенью механизации и автоматизации технологического оборудования, оснащения и транспортных устройств на отдельных операциях и по всему процессу.
При ремонте пассажирских вагонов разбирают до металлической поверхности пол, а боковые стены - до верхнего уровня оконных проемов. В тамбурах, туалетах, котельных помещениях, служебных отделениях и малых коридорах всех типов вагонов пол и стены вскрывают до уровня верхней обвязки. В кухнях и раздаточных отделениях вагонов-ресторанов, кроме того, разбирают крышу над кухней и раздаточным отделением.
После разборки наружные и внутренние поверхности кузова очищают от загрязнений, коррозии, старого лакокрасочного покрытия и осматривают обстукиванием мест, наиболее поврежденных коррозии. Особое внимание обращают на состояние сварных швов, оконных проемов, подоконных панелей и пола.
Все деревянные детали обрешетки и настила пола при наличии гнили и механических повреждений заменяют. Деревянные детали, расположенные ниже подоконных слоев поясов, пропитывают для защиты от гнили антисептическими пастами, а выше подоконных поясов - антипиренами, обладающими огнезащитными свойствами. На внутренние поверхности вскрытых мест кузова после высыхания защитных покрытий укладывают новую изоляцию. Деревянный настил пола в вагонах заменяют новым, изготовленным из фанерных плит толщиной 20 мм, потом покрывают новым поливинилхлоридным линолеумом, изготовленным из трудногорючих материалов.
Для изготовления и ремонта обрешетки, обшивки стен, потолка, настила пола, изоляции применяют новые материалы, соответствующие требованиям пожарной безопасности. Повреждения наружных поверхностей стен, пола и
крыши в процессе эксплуатации происходят сравнительно редко и главным образом из-за случайных ударов при маневровых работах, из-за царапин и разрушения антикоррозионного покрытия. В средней части кузова оставшаяся толщина гофрированного листа пола составляет 0,7...1,0 мм при начальной толщине 2 мм.
Особенно интенсивно коррозирует пол в зоне расположения нижней обвязки и против оконных проемов. Наибольшие коррозионные повреждения боковой стены наблюдаются в нижней части на высоту до 200 мм под окнами и на высоту до 100 мм в зонах между окнами. Это дополнительно объясняется попаданием влаги снаружи через не плотности примыкания рамы окна к обшивке кузова. Кроме того, интенсивно развивается щелевая коррозия в зонах расположения стоек и стрингеров, а также по сварным швам и околошовным зонам.
Поражение коррозией на всю конструктивную толщину металла (2 мм) наблюдается также по периметру оконных проемов на ширину 20...25 мм.
На участках, где обнаружены коррозионные повреждения более 30 % сечения, производят разборку внутренней обшивки и теплоизоляции для устранения выявленных повреждений.
Постановка вставок допускается в случае, если площадь пораженного коррозией участка не превышает 1 м2. Если пораженный участок более 1 м2 или требуется постановка второй вставки, то производят замену всей секции.
В наиболее подверженных коррозии помещениях пассажирских вагонов (в туалетах, тамбурах, кухне вагона-ресторана) при ремонте устанавливают специальные поддоны из стеклопластика в качестве верхнего настила пола.
Устранение пробоин и прорезов длиной более 100 мм и шириной более 3 мм производят постановкой вставок с приваркой их по периметру. Ремонт оконных проемов кузова производят путем вырезки негодных частей и варки вставок по периметру окна.
При деповском ремонте проверяют состояние всех узлов и деталей кузова и рамы. При этом особое внимание обращают на сварные швы концевых, продольных и промежуточных балок рамы вагона. Сварные швы, имеющие трещины, вырубают и заваривают.
Кузова, изготовленные из низкоуглеродистых и низколегированных сталей, осматривают с обстукиванием мест наиболее подверженных коррозией. Для определения степени коррозионного повреждения рекомендуется применять ультразвуковой толщиномер.