ВУЗ: Не указан
Категория: Не указан
Дисциплина: Не указана
Добавлен: 05.02.2024
Просмотров: 17
Скачиваний: 0
ВНИМАНИЕ! Если данный файл нарушает Ваши авторские права, то обязательно сообщите нам.
1.ИЗУЧЕНИЕ ДОКУМЕНТАЦИИ.
Изучение техники безопасности и правил проведения ремонтных работ
Изучение правил ТБ противопожарной и электробезопасности.
Пожарной безопасностью называется система мероприятий и технических средств, направленных на защиту личности, имущества, общества, государства от пожаров; энергобезопасностью – мероприятия и технические средства, предотвращающие вредное и опасное воздействие на людей эклектического тока. Правила пожарной безопасности и электробезопасности регламентированы правовой и технической документацией. Знание основ пожарной безопасности и электробезопасности является обязательным требованием к персоналу, обслуживающему различные электроустановки и электрооборудование.
В связи с высокими требованиями, предъявляемыми законодательством к обеспечению пожарной безопасности, знаниями соответствующих нормативов и правил должны владеть не только руководители предприятий, но и все его работники, что позволит снизить вероятность возникновения несчастных случаев на производстве.
2. ИЗУЧЕНИЕ КОНСТРУКЦИИ ОСНОВНОГО ОБОРУДОВАНИЯ.
Конструкция основного оборудования.
Колонны с различными видами тарелок.
Тарельчатыми называют колонные аппараты, у которых внутренними устройствами в рабочей зоне являются тарелки.
Тарелки – это барботажное устройство, в котором при работе происходит массообменный процесс, т.е. переход компонента из одной фазы в другую в результате непосредственного контакта между рабочими средами.
Противоточные тарелки характеризуются высокими жидкостными нагрузками, малой металлоемкостью, простотой конструкции и монтажа. В то же время они имеют узкий диапазон устойчивой работы, низкую эффективность и неравномерное распределение жидкости по сечению колонн большого диаметра.
Наибольшее распространение получили перекрестно-точные тарелки, которые подразделяются: тарелки с постоянным свободным сечением для прохода паров-ситчатые, ситчатые с отбойниками, колпачковые с круглыми, шестигранными, S-ными и желобчатыми колпачками.
Перекрестно-точные тарелки (за исключением ситчатых) характеризуются большим временем пребывания жидкости по сравнению с другими типами тарелок, лучшей организацией барботажа и высокой эффективностью. К достоинствам колпачковых тарелок относится наличие постоянного слоя жидкости на тарелке и отсутствие провала жидкости; к недостаткам – небольшой диапазон эффективной работы, повышенная металлоемкость,
сложность изготовления и монтажа.
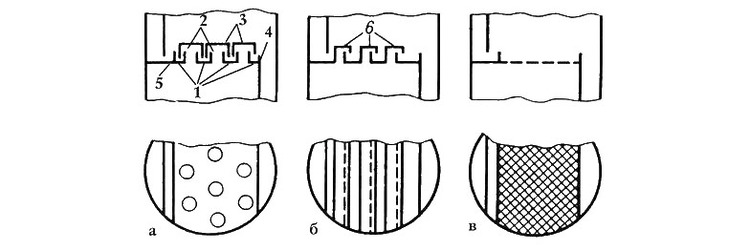
Насадочные колонны.
Насадочные контактные устройства широко применяются в нефтепереработке, они разнообразны по конструкции и обычно дороже тарельчатых. В зависимости от расположения ячеек насадки в объеме колонны их подразделяют на нерегулярные и регулярные. Нерегулярными считаются насадки, элементы которых засыпаются в колонну на определенную высоту и располагаются в ней хаотично; наиболее распространены насадки кольцевого типа.
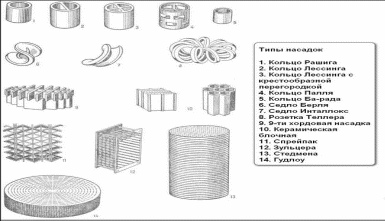
1 кольца Рашига
2 кольца Лессинга
3 кольцо Палля
4 кольца с крестообразными перегородками.
Трубчатая печь
Вертикальная, радиантно-конвекционная, однокамерная печь состоит из радиантной и конвекционной камер.
Продуктовый змеевик конвекционной части состоит из труб Ø159х11, сталь 15Х5М – 40 шт., соединенных калачами Ø159х12, сталь 15Х5М – 35 шт. Трубы расположены в четыре ряда. Конвекционная часть змеевика и радиантная часть соединены перекидкой. Продуктовый змеевик радиантной части двухпоточный состоит из труб Ø159х9, сталь Х8М – 40 шт., соединенных калачами Ø159х12,5, сталь Х8М – 35 шт. Форсунки расположены в печи горизонтально в 3 яруса по 2 форсунки на ярус. Продукты сгорания из радиантной камеры через газоход поступают в камеру конвекции. Печь может шуроваться газообразным топливом, жидким и комбинированно. Для сжигания топлива имеются газомазутные форсунки ФГМ.
Устройство и принцип действия теплообменных аппаратов различных конструкций.
Теплообменные аппараты используются для нагрева, испарения, конденсации, охлаждения, кристаллизации участвующих в процессе сырья и продуктов. Весьма важным в технологическом и экономическом плане является максимально полное использование тепла отходящих с установки потоков (рекуперация тепла). В качестве теплоносителей могут служить газообразные, жидкие или твердые (частицы кокса, катализатора) вещества. Практически на всех установках в качестве теплоносителей используется водяной пар как высокого давления, так и отработанный низкого. Одной из важнейших характеристик теплообменного аппарата является поверхность теплообмена: чем она больше (при одном и том же расходе металла), тем выше эффективность теплообмена. В заводской практике используются теплообменники с поверхностью от 10 до 1012 м2 при длине от 3 до 9 м и диаметре аппарата от 300 до 1400мм (диаметр трубок 20-25 мм).
Кожухотрубчатые теплообменники с плавающей головкой и с U-образными трубками получили наибольшее распространение в промышленности. Возможность перемещения («плавания») одной из трубных решеток в корпусе аппарата обеспечивает компенсацию температурных изменений длин трубного пучка и корпуса. Теплообменники данной конструкции обеспечивают высокий коэффициент теплопередачи K-420-630 кДж/(м2*ч*K).
Теплообменники типа «труба в трубе»
Они применяются главным образом для передачи тепла от высоковязких продуктов (гудронов, крекинг-остатков), при использовании которых требуются повышенные скорости, обеспечивающие хорошую теплоотдачу и сокращение возможности образования коксовых отложений.
3. ПУСК И ОСТАНОВКА ОБОРУДОВАНИЯ УСТАНОВКИ
Пуск и остановка установки осуществляется под руководством инженерно-технических работников при наличии приказа или письменного распоряжения в соответствии с разделом 6 «Технологического регламента», не нарушая последовательность операций и правил техники безопасности.
Перед пуском необходимо обеспечить установку средствами пожаротушения и пенотушения, проверить связь и сигнализацию и приступить к приему (электроэнергии, водяного пара, сжатого воздуха, топлива, инертного газа, воды).
Прием энергоресурсов проводить при участии работников соответствующих служб.
О приеме электроэнергии предупреждаются все работники и вывешиваются предупредительные плакаты.
Прием энергетических ресурсов ведется с соблюдением необходимых мер предосторожности, причем «секущие» задвижки на входе потоков на установку открывать постепенно, контролируя прохождение потоков по трубопроводам. Особое внимание уделить приему на установку водяного пара.
При приеме пара на установку открыть полностью дренажные вентили на основной паровой магистрали для спуска конденсата. Все задвижки на ответвлениях паропровода к насосам и оборудованию должны быть закрыты.
Прием пара производить плавным открытием входной задвижки до полного прогрева всей магистрали. Необходимо помнить, что быстрое открытие задвижек на паровой магистрали без достаточного прогрева паропровода может привести к сильным гидравлическим ударам, нарушению плотности соединений.
После спуска конденсата и появления сухого пара дренаж закрыть.
При приеме пара необходимо контролировать его давление, не допуская превышения установленных норм. Отдельные участки паропровода до потребителей (колонны, печи) прогреваются и включаются в работу по мере необходимости.
Перед приемом воздуха КИП открывается дренаж рессивера воздуха Е-17 и закрывается воздух на приборы КИП только при появлении сухого воздуха в дренаже.
– Перед приемом технического воздуха необходимо:
– закрыть задвижки на линиях разводки воздуха;
– открыть дренаж до появления сухого воздуха (присутствие воды в воздушной магистрали может быть причиной вспенивания сырья в реакторе и, как следствие, выброс продукта);
– из реактора удалить конденсат, для чего на воздушном стояке открывают вентиль, расположенный на воздушной линии внизу, при этом задвижка на воздушном стояке должна быть закрыта. После продувки вентиль закрыть и плавно открыть задвижку на стояке.
После проведения всех необходимых мероприятий по подготовке к пуску установки в первую очередь принять теплоноситель, пустить систему теплоносителя, проверить на проходимость каждый участок теплоспутника, затем принять сырье на установку и наладить «холодную» циркуляцию согласно пункта 6.2.1. «Технологического регламента».
«Холодная» циркуляция необходима для выявления неисправностей, для наладки работы насосов, аппаратов, контрольно-измерительных приборов, что является обязательным перед пуском.
При выводе на технологический режим усилить контроль за работой печи, колонны, так как подача свежего сырья вызывает колебания параметров.
Вывод гудрона на битумный блок контролируется руководителем пуска. Пуск битумного блока осуществляется строго в соответствии с разделом 6 «Технологического регламента».
Для обеспечения безопасности пуска битумного блока заполнение реакторов производить после достижения температуры в топке печи дожига 400оС. «Холодную» циркуляцию проводить при температуре сырья 120 – 140оС.
При подключении аппаратов к источнику давления соблюдать меры, исключающие образование опасного давления в корпусах, подъем температуры рабочей среды в аппаратах производить постепенно, обеспечив равномерный прогрев корпусов, что позволяет исключить разгерметизацию из-за резкого теплового расширения металла.
При изменении безопасных условий эксплуатации аппарат немедленно выводится из технологического процесса.
До отключения теплообогрева тщательно проверить отсутствие застывающих продуктов в трубопроводах, и только после полного удаления приступить к остановке системы обогрева.
Во время испытания следить, чтобы давление в аппарате и трубопроводах не поднималось выше разрешенного. Прокачку и опрессовку производить фракцией дизельного топлива. Возможные дефекты в системе устранить.
При пуске необходимо:
- вести контроль за состоянием аппаратуры, оборудования, трубопроводов и своевременно устранять все неполадки, которые могут привести к аварии и несчастному случаю.
При остановке аппаратов для подготовки к ремонту необходимо:
– освободить аппараты от газообразных и жидких продуктов через линии откачки и дренажи, избыточное давление газа сбросить на факел, аппараты продуть инертным газом или водяным паром;
– отглушить аппараты от всех отводящих и подводящих трубопроводов, промыть водой и пропарить паром;
– вскрытие люков производить сверху вниз;
– при наличии пирофорных соединений стенки аппарата поддерживать влажными до окончания чистки аппарата;
– работы внутри аппаратов производить только по наряду-допуску, где указан порядок ведения работ и меры безопасности в строгом соответствии с инструкцией по безопасному ведению газоопасных работ;
– ремонтные работы внутри аппаратов с применением открытого огня производить при наличии плана ведения огневых работ, где разработаны меры безопасности, и наличии разрешения на производство огневых работ.
– При подготовке к ремонту насосов необходимо:
– закрыть задвижку на напорном и всасывающем трубопроводах;
– отключить электродвигатель и проследить, чтобы он был обесточен, после чего на пусковом устройстве вывесить плакат «Не включать – работают люди!»;
– охладить корпус насоса до 45оС;
– освободить насос от перекачиваемого продукта;
– отглушить насос от действующих трубопроводов заглушками.
4.ПЕРЕХОД НА РЕЗЕРВНОЕ ОБОРУДОВАНИЕ ПРИ ВОЗМОЖНЫХ НЕПОЛАДКАХ.
Переход с работающего на резервное оборудование должен осуществляться периодически по графику, утвержденному начальником соответствующего цеха. Перед переходом с работающего на резервное оборудование, как правило, должны проверяться все защиты и блокировки резервного оборудования.
Переход с работающего на резервное оборудование необходим для равномерного использования ресурса оборудования, поддержания его характеристик наравне с работающим, опробования его в работе. Во время перехода производится и проверка всех защит и блокировок, если это возможно без нарушения технологического режима и не угрожает работающему оборудованию. График таких переходов и опробований составляется в каждом цехе обычно на год или на другой промежуток времени, но не менее чем на месяц. Во время перехода и проверок выявляются неисправности, которые не могут быть выявлены путем простых осмотров. Это позволяет своевременно устранять дефекты и поддерживать высокий уровень надежности.