Файл: Расчет и выбор допусков и посадок для типовых соединений деталей в узлах машин.doc
ВУЗ: Не указан
Категория: Не указан
Дисциплина: Не указана
Добавлен: 11.04.2024
Просмотров: 28
Скачиваний: 0
ВНИМАНИЕ! Если данный файл нарушает Ваши авторские права, то обязательно сообщите нам.
![]() Рисунок 4.1 – Схема расположения полей допусков калибров – пробок относительно контролируемого отверстия 24Js7 |
Таблица 4.1 – Исполнительные размеры калибров для контроля отверстий
Калибр | Размер калибра | Отклонения | ||
верхнее | нижнее | |||
Для отверстия | Р-ПР | ![]() | 0 | -Н |
Р-ПР изнош | ![]() | - | - | |
Р-НЕ | ![]() | 0 | -Н или -НS |
![]() Рисунок 4.1 – Схема расположения полей допусков калибров – скоб относительно контролируемого отверстия 24h6 |
Таблица 4.2 – Исполнительные размеры калибров для контроля валов
Калибр | Размер калибра | Отклонения | ||
верхнее | нижнее | |||
Для вала | Р-ПР | ![]() | +Н1 | 0 |
Р-ПР изнош | ![]() | - | - | |
Р-НЕ | ![]() | +Н1 | 0 | |
К-ПР | ![]() | 0 | -НР | |
К-НЕ | ![]() | 0 | -НР | |
К-И | ![]() | 0 | -НР |
4.2 Краткие пояснения указанных на СПД параметров:
-
Z=3 мкм – отклонение середины поля допуска на изготовление проходного калибра пробки относительно наименьшего предельного размера изделия; -
Y=3 мкм – допустимый выход размера изношенного проходного калибра для отверстия за границу поля допуска изделия; -
Н=4 мкм – допуск на изготовление калибров для отверстия (за исключением калибров со сферическими измерительными поверхностями). -
Z1=3 мкм - отклонение середины поля допуска на изготовление проходного калибра для вала относительно наибольшего предельного размера изделия; -
Y1=3 мкм - допустимый выход размера изношенного проходного калибра для вала за границу поля допуска изделия; -
Н1=4 мкм - допуск на изготовление калибров для вала; -
Нр=1,5 мкм - допуск на изготовление контрольного калибра для скобы.
4.3 В соответствии с расчетными схемами приведенными в таблицах 4.1 и 4.2 ниже приведены расчеты исполнительных размеров калибров:
Размеры проходного калибра-пробки:
ПРmax = Dmin + Z +H/2 = 23,99 + 0,003 + 0,004/2 = 23,995 мм,
ПРmin = Dmin + Z – H/2 = 23,99 + 0,003 – 0,004/2 = 23,991 мм,
ПР = 23,995-0,004 – исполнительный размер.
Граница износа проходного калибра-пробки:
ПРизн = Dmin – Y = 23,99 – 0,003 = 23,987 мм.
Размеры непроходного калибра-пробки:
НЕmax = dmах + H/2 = 24,01 + 0,004/2 = 24,012 мм,
НЕmin = dmах – H/2 = 24,01 – 0,004/2 = 24,008 мм,
НЕ = 24,012-0,004 – исполнительный размер.
Размеры проходного калибра-скобы:
ПРmax = dmax – Z1 + H1/2 =24 – 0,003 + 0,004/2 = 23,999 мм,
ПРmin = dmax – Z1 – H1/2 = 23 – 0,003 – 0,004/2 = 23,995 мм,
ПР = 23,995+0,004 – исполнительный размер.
Граница износа проходного калибра-скобы:
ПРизн = dmax + Y1 = 24 + 0,003 = 24,003 мм.
Размеры непроходного калибра-скобы:
НЕmax = dmin + H1/2 = 23,987 + 0,004/2 = 23,989 мм,
НЕmin = dmin – H1/2 = 23,987 – 0,004/2 = 23,985 мм,
НЕ = 23,985+0,004 – исполнительный размер.
Размеры контрольного проходного калибра-пробки для контроля новой проходной калибра-скобы:
К-ПРmax = dmax – Z1 + Hр/2 =24 – 0,003 + 0,0015/2 =23,99775 мм,
К-ПРmin = dmax – Z1 – Hр/2 =24 – 0,003 – 0,0015/2 =23,99625 мм,
Округляем исполнительный размер до 0,5 мкм в сторону уменьшения производственного допуска изделия
К-ПР = 23,9975-0,0015 – исполнительный размер.
Размеры контрольного проходного калибра-пробки для контроля изношенной проходной калибра-скобы:
К-Иmax = dmax + Y1 + Hр/2=24 + 0,003 + 0,0015/2=24,00375 мм,
К-Иmin = dmax + Y1 – Hр/2=24 + 0,003 – 0,0015/2=24,00225 мм,
Округляем исполнительные размеры до 0,5 мкм в сторону уменьшения производственного допуска изделия
К-И = 24,0035-0,0015 – исполнительный размер.
Размеры контрольного проходного калибра-пробки для контроля новой непроходной калибра-скобы:
К-НЕmax = dmin + Hр/2 = 23,987 + 0,0015/2 = 23,98775 мм,
К-НЕmin = dmin – Hр/2 = 23,987 – 0,0015/2 = 23,98625 мм,
Округляем исполнительный размер до 0,5 мкм в сторону уменьшения производственного допуска изделия
К-НЕmin = 23,988-0,0015 – исполнительный размер.
4.4 Ниже на рис. 4.3 и 4.4 приведены эскизы калибров пробок и калибров скоб с указанием исполнительных размеров, расчетные значения которых приведены выше.
![]() Рисунок 4.1 – Эскиз калибра-пробки |
![]() Рисунок 4.2 – Эскиз калибра-скобы |
0>
5 ВЫБОР ПОСАДОК КОЛЕЦ ПОДШИПНИКА
В соответствии с заданными параметрами подшипника (таблица 5.1), где вид нагрузки 1* – с умеренными толчками и вибрацией
Таблица 5.1 – Параметры подшипника
Вариант | Условное обозначение подшипника | Класс точности | Реакция опоры радиальная Fr, H | Нагрузка осевая Fa, Н | Вал dВ/d | Корпус D/DH | Вращающаяся деталь | Вид нагрузки* |
27 | 60210 | Нормальный | 9000 | - | 0,8 | - | Вал | 1 |
Размеры подшипника:
-
внутренний диаметр d = 50 мм; -
наружный диаметр D = 90 мм; -
ширина В = 20 мм; -
размер фаски (радиуса) r = 2 мм; -
вращающая деталь – вал; -
характер нагружения внутреннего кольца подшипника – циркуляционный; -
для наружного кольца подшипника характер нагружения – местный.
Для соединения внутреннего кольца с валом при циркуляционном нагружении выбор посадки на вал производим в зависимости от величины интенсивности нагрузки - Pr, которая определяется по формуле:
Pr =
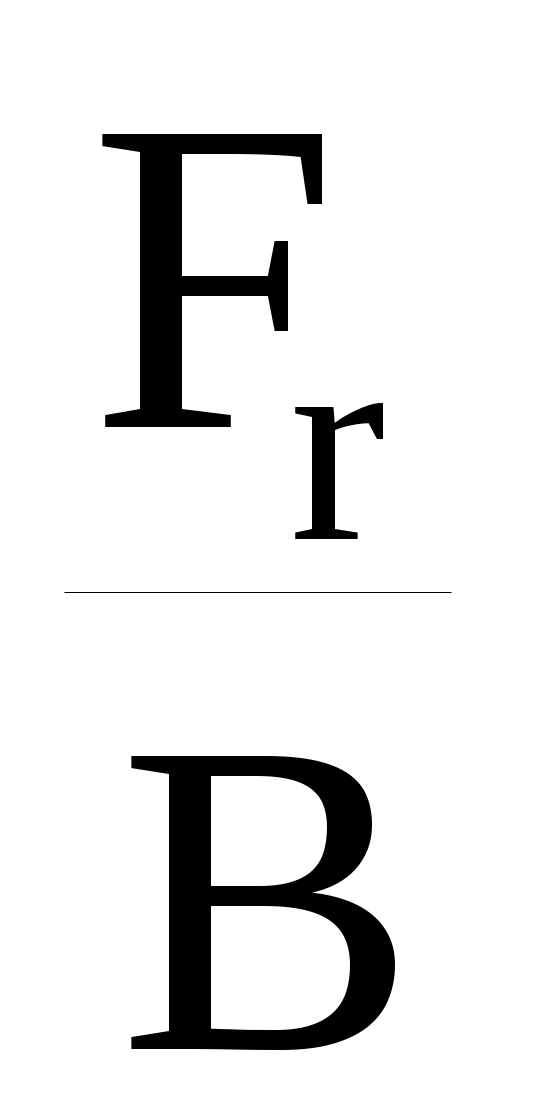
где Fr – радиальная нагрузка на опору, Н;
В = d – 2r – ширина посадочного места подшипника, мм;
K1, K2, K3 – коэффициенты, учитывающие перегрузки и другие условия работы подшипникового узла.
Для данных условий нагружения Fr = 9000 Н, К1=1 при перегрузке до 150%; К2=1,7 при dВ/d =0,8 и D/d=1,8; К3=1 при однорядном подшипнике.
Таким образом
PR =
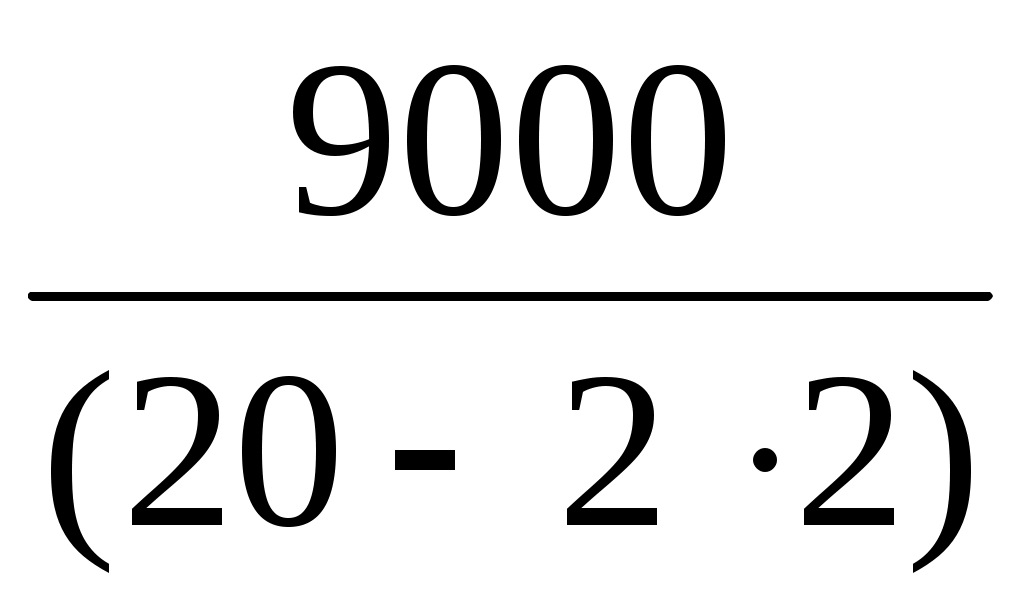
По таблице 4.7 [1] заданным условиям для вала диаметром d = 50 мм при интенсивности нагрузки 300-1400 Н/мм соответствует поле допуска k6.
Для соединения наружного кольца подшипника с корпусом при местном виде нагружения, перегрузке до 150 % и разъемном корпусе, для отверстия корпуса - 90 по таблице 4.89 [2] выбираем посадку – Н7.
Отклонения диаметров внутреннего и наружного колец подшипника определяем по ГОСТ 520-2011.
Таким образом, получаем следующие посадки:
- в сопряжении внутреннего кольца с валом 50
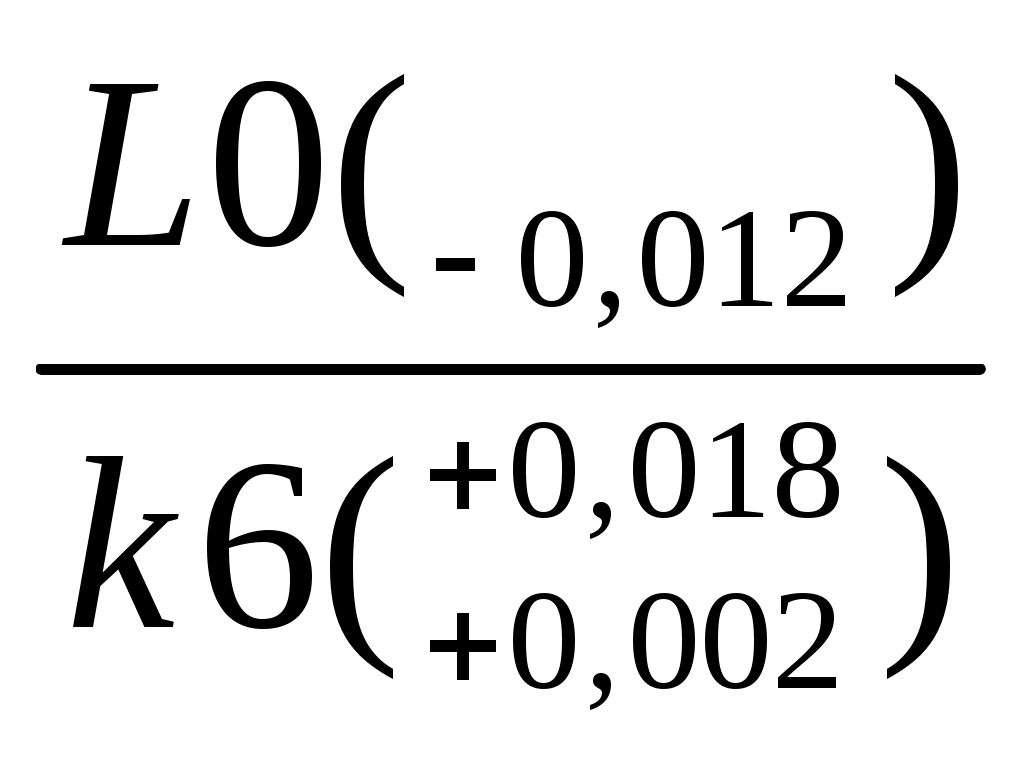
- в сопряжении корпуса с наружным кольцом 90
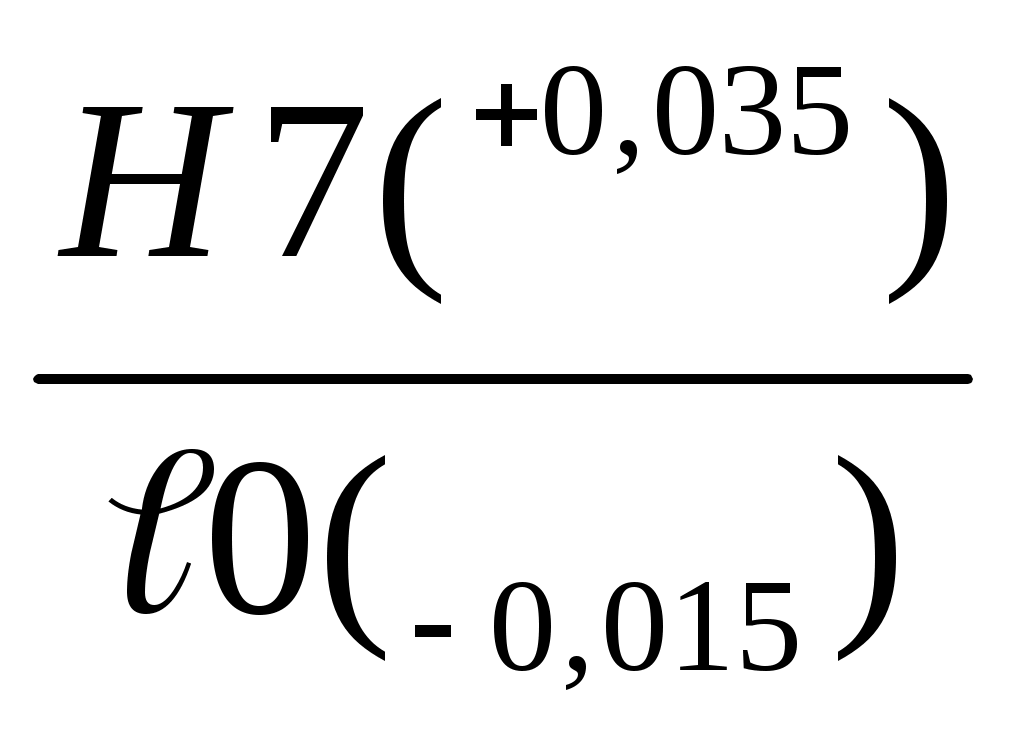
Строим схему расположения полей допусков (рис 5.1), выполняем эскизы подшипникового узла и входящих деталей (рис 5.2). Требования к шероховатости поверхностей, формы и расположения поверхностей посадочных мест назначаем по ГОСТ 3325-85.
![]() Рисунок 5.1 – Схема полей допусков |
![]() ![]() Рисунок 5.2 – Эскизы подшипникового узла и входящих деталей |