Файл: Расчет предельных и исполнительных размеров калибров и выбор универсальных измерительных средств.docx
ВУЗ: Не указан
Категория: Не указан
Дисциплина: Не указана
Добавлен: 02.05.2024
Просмотров: 43
Скачиваний: 0
ВНИМАНИЕ! Если данный файл нарушает Ваши авторские права, то обязательно сообщите нам.
Расчет исполнительных размеров калибров
Исполнительным размером калибра является один из предельных размеров (min или max) в зависимости от вида калибра (пробка или скоба). Предельные размеры калибров рассчитываются, как и предельные размеры деталей по следующим формулам (см. рис. 4.8). Калибр – пробка: Dmax(ПР) = D + EI + Z + H/2; Dmin (ПР) = D + EI + Z – H/2; Dmax (НЕ)= D + ES + H/2; Dmin (НЕ) = D + ES – H. Калибр – скоба: Dmax (ПР) = D + es – Z1 + H1/2; Dmin (ПР) = D + es – Z1 – H1/2; Dmax (НЕ) = D + ei + H1/2; Dmin (НЕ) = D + ei – H1/2. Контрольные калибры: Dmax (К–И) = D + es + Y1 + Hp/2; Dmin (К–И) = D + es + Y1 – Hp/2; Dmax(К–ПР) = D + es – Z1 + Hp/2; Dmin (К–ПР) = D + es – Z1 – Hp/2 ![]() solid.ru More information on the advertised website Learn More AD Dmax (К–НЕ) = D + ei + Hp/2; Dmin (К–НЕ) = D + ei – Hp/2. где D – номинальный размер контролируемой детали; ES, EI – верхнее и нижнее отклонения контролируемого отверстия; es, ei – верхнее и нижнее отклонения контролируемого вала; Z, Z1 – величины смещения средин полей допусков проходных калибров – пробок и калибров – скоб соответственно; Н, Н1, Нр – допуски калибров – пробок, калибров – скоб и контрольных калибров соответственно. Значения предельных отклонений контролируемых деталей (ES,EI, es, ei), а также значения допустимых величин износа калибров (Y, Y1) подставляются в формулы расчета исполнительных размеров проходных калибров с учетом их знака (+,–). В качестве исполнительного размера калибра – скобы принимается ее наименьший размер, а всю величину допуска на изготовление калибра со знаком «плюс» назначают к отклонение. Исполнительным размером калибра – пробки назначается наибольший его размер, а всю величину допуска на изготовление калибра назначают со знаком «минус» в отклонение. И для калибра – пробки и для калибра – скобы отклонения назначают в «тело» детали. Таким образом, при назначении исполнительных размеров калибров используется принцип «максимума металла», при выполнении которого гарантируется вероятность получения годных калибров в процессе их изготовления. Ниже приводится пример расчета размеров калибров и назначение исполнительных размеров. Пример: Определить размеры калибров – пробок и калибров – скоб для контроля деталей сопряжения Ø75Н7/d8. По ГОСТ 25346-89 определяются допуски и предельные отклонения, по которым строится схема полей допусков контролируемых деталей: отверстия Ø75Н7 и вала Ø75d8 (рис. 4.9). Определяем предельные размеры калибров по формулам, приведенным выше. Калибры – пробки: Dmax(ПР) = D + EI + Z + H/2 = 75 + 0 + 0,004 + 0,0025 = 75,0065 мм; Dmin (ПР) = D + EI + Z – H/2 = 75 + 0 + 0,004 – 0,0025 = 75, 0015 мм; Dmax(НЕ) = D + ES + H/2 = 75 + 0,039 + 0,0025 = 75,0415 мм; Dmin(НЕ) = D + ES – H/2 = 75 + 0,039 – 0,0025 = 75, 0365 мм; Калибры – скобы: Dmax(ПР) = D + es – Z1 + H1/2 = 75 + (–0,100) – 0,007 + 0,004 = 74,897 мм; Dmin(ПР) = D + es – Z1 – H1/2 = 75 + (–0,100) – 0,007 – 0,004 = 74,889 мм; Dmax(НЕ) = D + ei + H1/2 = 75 + (–0,146) + 0,004 = 74,858; Dmin (НЕ) = D + ei – H1/2 = 75 + (–0,146) – 0,004 = 74,850 мм; Контрольные калибры: Dmax(К–И) = D + es + Y1 + Hp/2 = 75 + (– 0,100) + 0 + 0,0015 = 74,9015 мм; Dmin (К–И) = D +es + Y1 – Hp/2 = 75 + (– 0,100) + 0 – 0,0015 = 748985 мм; Dmax (К–ПР)=D + es – Z1 + Hp/2 =75 + (– 0,100) – 0,007 + 0,0015 = = 74,8945 мм; Dmin(К–ПР) = D + es – Z1 – Hp/2 = 75 + (– 0,100) – 0,007 – 0,0015 = ![]() beeline.uz More information on the advertised website Learn More AD = 74,8915 мм; Dmax (К–НЕ) = D + ei + Hp/2 = 75 + (– 0,146) + 0, 0015 = 74,8555 мм; Dmin (К–НЕ) = D + ei – Hp/2 = 75 + (– 0,146) – 0,0015 = 74,8525 мм. Исполнительными следует назначить следующие размеры калибров Проходной калибр – пробка: Dисп (ПР) = 75,0065– 0,005 мм; Непроходной калибр – пробка: Dисп(НЕ) = 75,0415– 0,005 мм; Проходной калибр – скоба: Dисп.(ПР) = 74,889 + 0,008 мм; Непроходной калибр – скоба: Dисп.(НЕ) = 74,850 + 0,008 мм; Контрольный калибр для контроля изношенной рабочей скобы: Dисп.(К-И) = 74,9015– 0,003 мм; Контрольный калибр для контроля проходной скобы: Dисп.(К-ПР) = 74,8945– 0,003 мм; Контрольный калибр для контроля непроходной скобы: Dисп.(К-НЕ) = 74,8555– 0,003 мм. |
Dmax (К–НЕ) = D + ei + Hp/2;
Dmin (К–НЕ) = D + ei – Hp/2.
где D – номинальный размер контролируемой детали; ES, EI – верхнее и нижнее отклонения контролируемого отверстия; es, ei – верхнее и нижнее отклонения контролируемого вала; Z, Z1 – величины смещения средин полей допусков проходных калибров – пробок и калибров – скоб соответственно; Н, Н1, Нр – допуски калибров – пробок, калибров – скоб и контрольных калибров соответственно.
Значения предельных отклонений контролируемых деталей (ES,EI, es, ei), а также значения допустимых величин износа калибров (Y, Y1) подставляются в формулы расчета исполнительных размеров проходных калибров с учетом их знака (+,–).
В качестве исполнительного размера калибра – скобы принимается ее наименьший размер, а всю величину допуска на изготовление калибра со знаком «плюс» назначают к отклонение. Исполнительным размером калибра – пробки назначается наибольший его размер, а всю величину допуска на изготовление калибра назначают со знаком «минус» в отклонение. И для калибра – пробки и для калибра – скобы отклонения назначают в «тело» детали. Таким образом, при назначении исполнительных размеров калибров используется принцип «максимума металла», при выполнении которого гарантируется вероятность получения годных калибров в процессе их изготовления. Ниже приводится пример расчета размеров калибров и назначение исполнительных размеров.
Пример: Определить размеры калибров – пробок и калибров – скоб для контроля деталей сопряжения Ø75Н7/d8.
По ГОСТ 25346-89 определяются допуски и предельные отклонения, по которым строится схема полей допусков контролируемых деталей: отверстия Ø75Н7 и вала Ø75d8 (рис. 4.9).
Определяем предельные размеры калибров по формулам, приведенным выше.
Калибры – пробки:
Dmax(ПР) = D + EI + Z + H/2 = 75 + 0 + 0,004 + 0,0025 = 75,0065 мм;
Dmin (ПР) = D + EI + Z – H/2 = 75 + 0 + 0,004 – 0,0025 = 75, 0015 мм;
Dmax(НЕ) = D + ES + H/2 = 75 + 0,039 + 0,0025 = 75,0415 мм;
Dmin(НЕ) = D + ES – H/2 = 75 + 0,039 – 0,0025 = 75, 0365 мм;
Калибры – скобы:
Dmax(ПР) = D + es – Z1 + H1/2 = 75 + (–0,100) – 0,007 + 0,004 = 74,897 мм;
Dmin(ПР) = D + es – Z1 – H1/2 = 75 + (–0,100) – 0,007 – 0,004 = 74,889 мм;
Dmax(НЕ) = D + ei + H1/2 = 75 + (–0,146) + 0,004 = 74,858;
Dmin (НЕ) = D + ei – H1/2 = 75 + (–0,146) – 0,004 = 74,850 мм;
Контрольные калибры:
Dmax(К–И) = D + es + Y1 + Hp/2 = 75 + (– 0,100) + 0 + 0,0015 = 74,9015 мм;
Dmin (К–И
) = D +es + Y1 – Hp/2 = 75 + (– 0,100) + 0 – 0,0015 = 748985 мм;
Dmax (К–ПР)=D + es – Z1 + Hp/2 =75 + (– 0,100) – 0,007 + 0,0015 =
= 74,8945 мм;
Dmin(К–ПР) = D + es – Z1 – Hp/2 = 75 + (– 0,100) – 0,007 – 0,0015 =
= 74,8915 мм;
Dmax (К–НЕ) = D + ei + Hp/2 = 75 + (– 0,146) + 0, 0015 = 74,8555 мм;
Dmin (К–НЕ) = D + ei – Hp/2 = 75 + (– 0,146) – 0,0015 = 74,8525 мм.
Исполнительными следует назначить следующие размеры калибров
Проходной калибр – пробка: Dисп (ПР) = 75,0065– 0,005 мм;
Непроходной калибр – пробка: Dисп(НЕ) = 75,0415– 0,005 мм;
Проходной калибр – скоба: Dисп.(ПР) = 74,889 + 0,008 мм;
Непроходной калибр – скоба: Dисп.(НЕ) = 74,850 + 0,008 мм;
Контрольный калибр для контроля
изношенной рабочей скобы: Dисп.(К-И) = 74,9015– 0,003 мм;
Контрольный калибр для контроля
проходной скобы: Dисп.(К-ПР) = 74,8945– 0,003 мм;
Контрольный калибр для контроля
непроходной скобы: Dисп.(К-НЕ) = 74,8555– 0,003 мм.
Пример расчёта калибров для контроля деталей
Гладких цилиндрических сопряжений
В качестве примера для расчета калибров выбираем гладкое цилиндрическое сопряжение Ø34Н7/k6.
Определяем предельные отклонения и размеры отверстияØ34Н7:
IT7= 25 мкм,
ЕI = 0,
ES = +25 мкм;
Dmax = 34,000 + 0,025 = 34,025 мм;
Dmin = 34,000 + 0 = 34,000 мм.
Определяем предельные отклонения и размеры вала Ø34k6.
IT7= 16 мкм,
ei = +2 мкм,
es = +18 мкм;
dmin= 34,000 + 0,002 = 34,002 мм;
dmax= 34,000 + 0,018 = 34,018 мм.
Строим схемы расположения полей допусков калибров для контроля отверстия и вала:
а) для отверстия Ø34Н7– схема, приведенная в ГОСТ 24853 (чертеж 1);
б) для вала Ø34k6– схема, приведенная в ГОСТ 24853 (чертеж 3).
В соответствии с выбранной схемой расположения полей допусков калибров для контроля отверстия Ø34Н7 определяем числовые значения параметров H, Z, Y (табл. 2 ГОСТ 24853).
H = 4 мкм – допуск на изготовление калибров;
Z = 3,5 мкм – отклонение середины поля допуска на изготовление проходного калибра;
Y = 3 мкм – допустимый выход размера изношенного проходного калибра за границу поля допуска отверстия.
Строим схемы расположения полей допусков калибров для контроля отверстия Ø34Н7 (рис. 40).
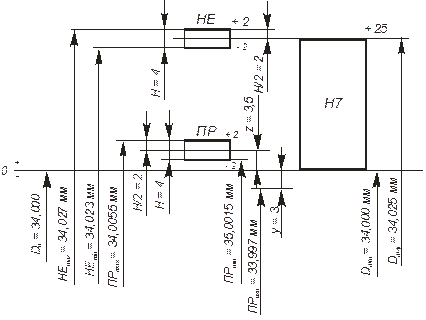
Рис. 40. Схема расположения полей допусков калибров
для контроля отверстия Ø34Н7
Рассчитываем предельные (табл. 1 ГОСТ 24853) и исполнительные размеры калибров для контроля отверстия Ø34Н7, и результаты сводим в табл. 33.
Таблица 33
Предельные и исполнительные размеры калибров-пробок
Обозначение калибра | Размер, мм | | | |
наибольший | наименьший | изношенной стороны | исполни-тельный | |
ПР | 34,0055 | 34,0015 | 33,997 | 34,0055-0,004 |
НЕ | 34,027 | 34,023 | - | 34,027-0,004 |