Файл: Курсовая работа по дисциплине Общая химическая технология Тема Синтез аммиака в производстве аммиака.docx
Добавлен: 03.05.2024
Просмотров: 404
Скачиваний: 6
ВНИМАНИЕ! Если данный файл нарушает Ваши авторские права, то обязательно сообщите нам.
СОДЕРЖАНИЕ
объемнойскоростьюдо1000час
-1
притемпературевзонепассивациине
выше 150
о
С.
При разработке катализатора, используемого в промышленности следует
учитыватьдлительностьслужбыкатализатора(нескольколет)вусловиях
некоторой нестационарности технологического процесса.
В промышленных каталитических реакторах процесс синтеза аммиака
протекаетприменяющихсяподлинезоныкатализаторатемпературе,
объемнойскорости,составегазаит.д.,чтоприводиткизменению
химического состава и строения поверхности катализатора и вследствие этого
– активности катализатора.
При разработке катализатора, используемого в промышленности следует
учитыватьдлительностьслужбыкатализатора(нескольколет)вусловиях
некоторой нестационарности технологического процесса.
В промышленных каталитических реакторах процесс синтеза аммиака
протекаетприменяющихсяподлинезоныкатализаторатемпературе,
объемнойскорости,составегазаит.д.,чтоприводиткизменению
химического состава и строения поверхности катализатора и вследствие этого
– активности катализатора.
При разработке катализатора, используемого в промышленности следует
учитыватьдлительностьслужбыкатализатора(нескольколет)вусловиях
некоторой нестационарности технологического процесса
Для того, чтобы катализатор был эффективным, он должен обладать высокими селективностью, термостойкостью и износоустойчивостью, его зерна должны быть прочными, а также обладать стойкостью к действию ядов. При правильном соотношении промоторов катализатор будет иметь большую активную поверхность.
3.4. Общие выводы и рекомендации по изменению отдельных параметров с целью повышения выхода и улучшения качества целевого продукта
Данные об оптимальной температуре, полученные в ходе проведенного нами термодинамического и кинетического анализа, разнятся. С одной стороны, экзотермическая природа реакции благоприятствует понижению температуры в аппарате для сдвига равновесия в сторону прямой реакции и увеличения степени превращения исходных веществ. Но, исходя из кинетики, мы должны придерживаться оптимальной температуры, которая зависит от состава реакционной смеси. С увеличением содержания аммиака и уменьшением содержания азота и водорода оптимальная температура уменьшается. Чем глубже прошла реакция, тем больше степень превращения, тем меньше оптимальная температура. Из этого следует, что синтез аммиака необходимо проводить все же при повышенной температуре, а низкую степень превращения исходных веществ нивелировать с помощью других параметров реакции.
В случае поиска оптимального давления, результаты термодинамического и кинетического анализа согласуются между собой. Реакция синтеза аммиака протекает в газовой фазе и с уменьшением объема. В таком случае, руководствуясь принципом Ле-Шателье, для сдвига равновесия в сторону продуктов давление необходимо увеличить. В то же время, из анализа уравнение Тёмкина – Пыжева, очевидно, что увеличение давления в системе увеличит и скорость прямой реакции, а скорость обратной уменьшится. Соответственно, процесс синтеза аммиака необходимо проводить при высоком давлении.
С помощью термодинамического анализа (по принципу Ле-Шателье) устанавливаем, что для смещения равновесия в сторону прямой реакции нам необходимо в газовой смеси добиться наименьшего содержания аммиака и наибольшего содержания азота и водорода. Дополняя этот тезис с помощью кинетического анализа, делаем вывод, что для наибольшей скорости прямой реакции необходимое соотношение реагентов: H2:N2=P1,5H2:P1N2.
Катализаторы для синтеза аммиака необходимы для ускорения процесса, иначе данный процесс придется проводить при более высоких температурах, и он будет протекать с малой скоростью. Катализатор должен быть обязательно активным с содержанием промоторов, для усиления селективности и поддержания активности используемого катализатора. Так же важным требованием для катализатора является износостойкость, термостойкость, прочность зерен, устойчивость при длительной эксплуатации и малая стоимость.
Синтез аммиака побочных реакций не имеется, значит, селективность катализатора не будет играть важную роль. Если применять гранулированный катализатор будет обеспечиваться более равномерная структура слоя и равномерное распределение газового потока, а мелкозернистый катализатор в свою очередь уменьшает диффузионное торможение, увеличивая выход аммиака. При правильном подборе соотношения промоторов катализатор будет иметь большую активную поверхность и высокие показатели эффективности.
4. Синтез и анализ ХТС
4.1 Химическая схема
Аммиак в производстве аммиака получается реакцией водорода с азотом: N2+3H2↔ NH3
Побочных реакций нет.
4.2 Структурная схема
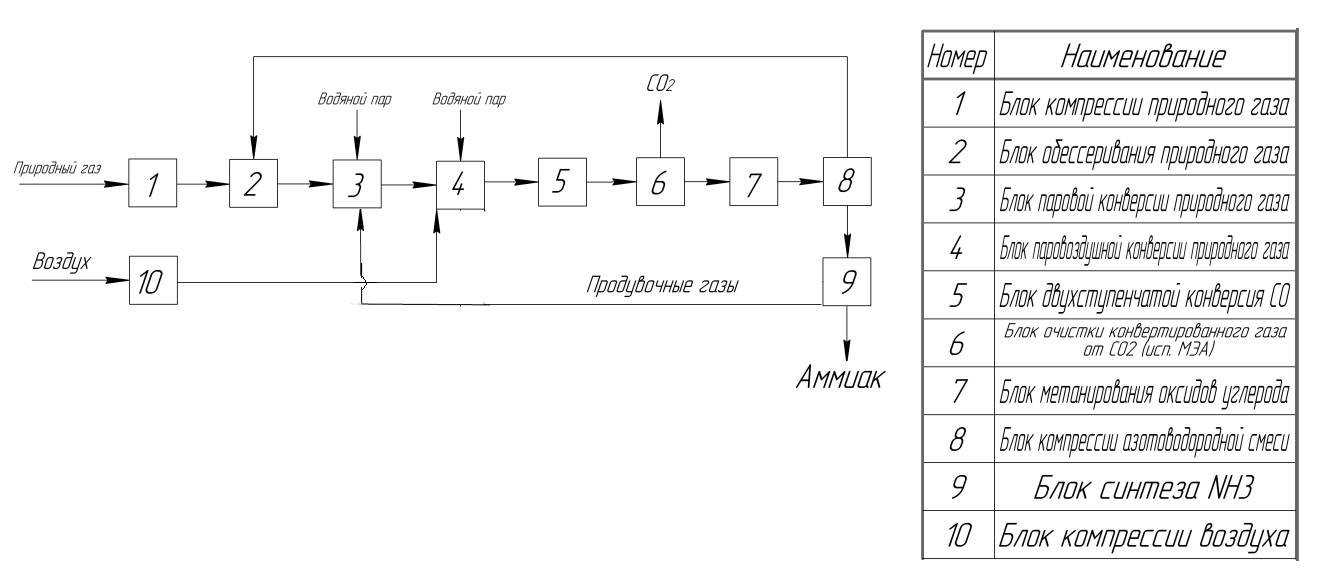
Рис. 3 – Структурная схема производства аммиака
1) Исходным сырьем для производства аммиака является природный газ. Для переработки природный газ сжимается до давления не более 4,5 Мпа компрессором и отчищается от присутствующих в нем сернистых соединений, являющихся каталитическими ядами для стадий паровой конверсии углеводородов и низкотемпературной конверсии оксида углерода. Из примесей в природном газе выделяют такие соединения как сероводород H2S, меркаптаны RSH, тиофен С4Н4S, сероуглерод СS2 и др.
2) Очистка природного газа от сернистых соединений производится в 2 ступени: 1-я ступень – гидрирование органических соединений серы в H2S на аллюмокобальтомолибденовом катализаторе при температуре 350 – 400°С. Необходимый водород для гидрирования поступает в виде азотоводородной смеси со стадий конверсии метана.
-
RSH + H2 = H2S + RH -
С4Н4S + 4H2 = H2S + С4Н10 -
СS2 + 4H2 = 2H2S + СН4
2я ступень – поглощение сероводорода оксидом цинка.
-
H2S+ ZnO = ZnS+Н2О.
После стадии сероочистки газовая смесь направляется на конверсию метана.
3) Процесс конверсии метана осуществляется в 2 ступени. Двухступенчатая система позволяет повысить степень превращения метана. Так как реакция метана с водой – эндотермическая, то повышение температуры повышает скорость реакции. Температура, необходимая для полного превращения в процессе – 1300 К. Материал, из которого сделаны части реактора, не позволяет использовать его при таких высоких температурах. Поэтому необходима вторая ступень конверсии, которая проходит в адиабатическом реакторе со стенками из высокотемпературного материала – бетона. Это позволяет повысить температуру внутри реактора и добиться почти полной степени превращения метана.
Для получения водорода конверсией метана кислородом необходимо провести процесс неполного окисления метана. Перед подачей в трубчатую печь очищенный от серы природный газ смешивается с перегретым паром давлением 4Мпа. Остаточное содержание метана в газовой смеси на выходе из печи первичного риформинга составляет до 1:3
И природный газ СН4, и вода Н2O являются сырьем для получения одного из компонентов для синтеза аммиака — водорода Н2. В этом превращении протекают одновременно две реакции:
СН4 + Н2О = СО + 3Н2;
СО + Н2О = СО2 + Н2.
4) Конверсия метана с водяным паром. В реакторе вторичного риформинга на катализаторе происходит окончательная конверсия метана с паром и кислородом воздуха до остаточного содержания метана в газе. Кислород воздуха поступает с блока конверсии 10, как источник кислорода. В данном воздухе присутствует содержание азота, который дальше будет протекать в процессе с конвертированным газом и в дальнейшем пойдет на реакцию синтеза аммиака.
Далее конвертированный газ поступает на двухступенчатую паровую конверсию оксида углерода.
5) Конверсия оксида углерода протекает по двухступенчатой схеме:
1 ступень — на среднетемпературном катализаторе (Твых<450°С)
2 ступень — на низкотемпературном катализаторе (Твых<280°С)
СО + Н2О = СО2 + Н2.
В конвертере СО 1 ступени на среднетемпературном катализаторе происходит конверсия оксида углерода с водяным паром. Остаточное содержание СО после конвертора 1 ступени составляет не более 4 об.%. В конверторе СО 2 ступени происходит более глубокая конверсия СО с водяным паром до его содержания в конвертированном газе 0.5 - 0.8 %.
Очищенный от СО конвертированный газ направляется на метанирование.
6) В конвертированном газе содержание СО2 до 17-18%. СО2 – балласт для синтеза аммиака и его необходимо удалить. Удаление сорбцией требует специфических сорбентов, необходимых в большом количестве. В настоящее время используется 19-21%-ный водный раствор моноэтиламина (МЭА) для абсорбции диоксида углерода:
СО2 + 2 RNH2+ Н2О = (RNH3)2CО3.
Эта стадия носит название МЭА-очистки. Поглощение диоксида углерода (карбонизация раствора МЭА) – обратимый процесс: с повышением температуры равновесия сдвигается влево, тем самым позволяя регенерировать сорбент. Поэтому в схеме очистки используются два аппарата: абсорбер и десорбер.
Но раствор МЭА не поглощает оксид углерода, поэтому последний превращают в метан, который безвреден для катализатора и инертен в процессе синтеза аммиака.
7) Метанирование. Тонкая очистка конвертированного таза от оксида и диоксида углерода, являющихся ядами для катализатора синтеза аммиака, производится в метанаторе путем каталитического гидрирования их до метана по реакциям:
СО + 3 Н2 = СН4 + Н2О + 206,3 кДж/моль
СО2 + 4 Н2 = СН4 + 2 Н2О + 165,1 Кдж/моль
Тепло азотоводородной смеси после метанатора используется для подогрева питательной воды для котлов. Окончательное охлаждение производится в аппаратах воздушного охлаждения.
8) Компрессия синтез-газа осуществляется в трехкорпусном центробежном компрессоре, имеющем четыре ступени для сжатия синтез-газа и ступень для сжатия циркуляционного газа. Синтез-газ после сжатия в четвертой ступени компрессора и охлаждения в воздушном холодильнике смешивается с циркуляционным газом с нагнетания в циркуляционной ступени компрессора.
9) В колонне синтеза аммиака на катализаторе при температурах 390 – 530°С протекает экзотермическая реакция образования аммиака.
3 H2 + N2 = 2 NH3
Продувочные газы после колонны синтеза выходят с температурой до 350°С и содержанием аммиака до 19,9 % и подвергаются охлаждению с целью конденсации аммиака. Сконденсировавшийся аммиак отделяется в сепараторе. А остаточные продувочные газы направляются на сжигание в печи риформинга.