Файл: Курсовая работа по дисциплине Общая химическая технология Тема Синтез аммиака в производстве аммиака.docx
Добавлен: 03.05.2024
Просмотров: 410
Скачиваний: 6
ВНИМАНИЕ! Если данный файл нарушает Ваши авторские права, то обязательно сообщите нам.
СОДЕРЖАНИЕ
4.3 Технологическая схема
Рисунок 4 – Технологическая схема синтеза аммиака
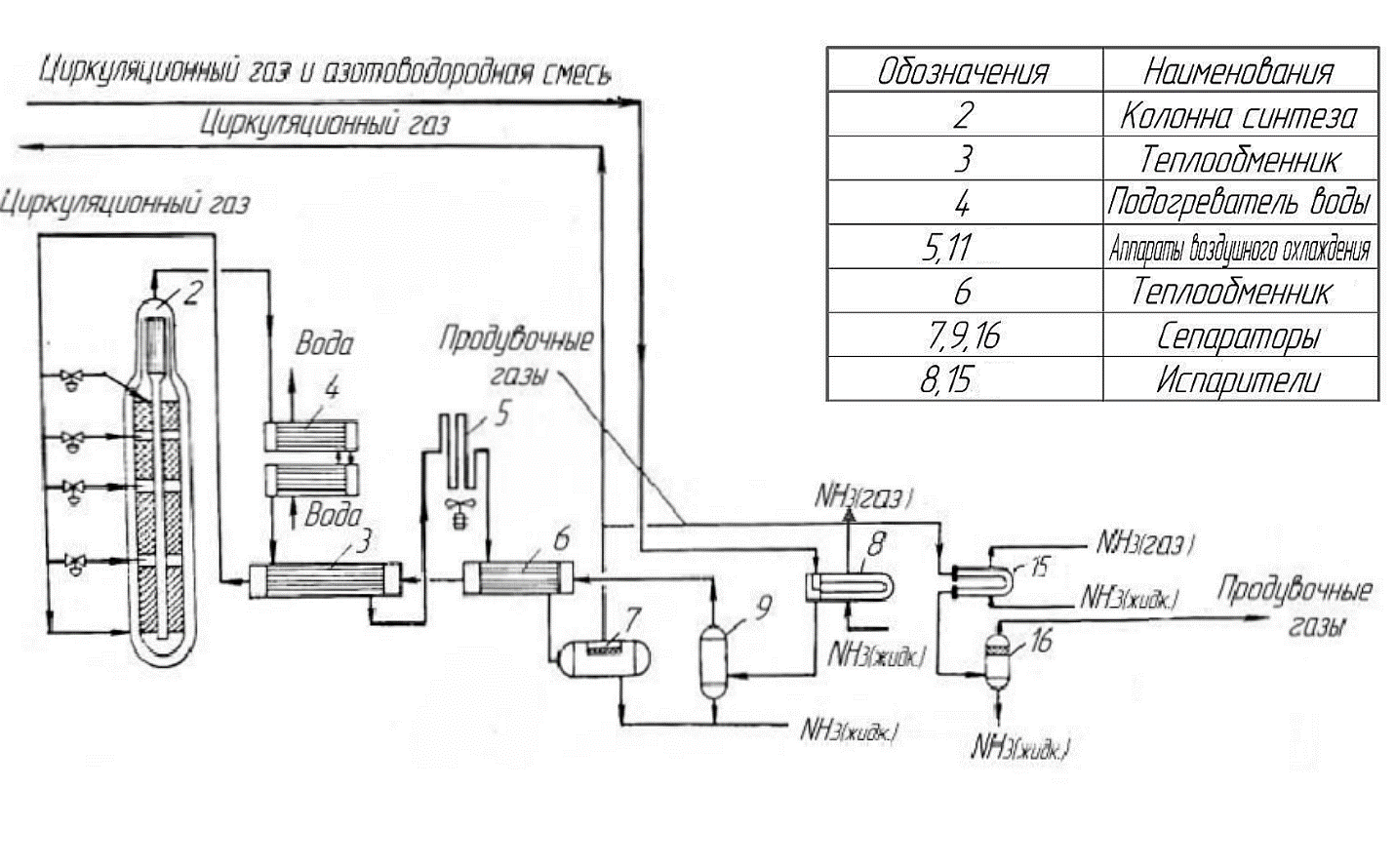
В этом агрегате (рис.4) синтез аммиака ведут в четырехполочной колонне 2, температурный режим регулируют введением в основной поток перед каждой полкой циркуляционного газа при 140°С. Для обеспечения автотермичной работы колонны синтеза устанавливают два теплообменника: в верхней части колонны над катализаторной коробкой и выносной 3.
Газ, выходящий из колонны синтеза 2 при 328°С с содержанием аммиака 16% (об.), отдает тепло в подогревателе питательной воды 4, состоящем из двух расположенных один над другим кожухотрубчатых теплообменников. Затем газ охлаждается в теплообменнике 3, аппарате воздушного охлаждения 5, теплообменнике 6 и при 21°С поступает в сепаратор 7, где отделяется жидкий аммиак, а газовая фаза, содержащая 6% (об.) аммиака, идет в циркуляционное колесо турбокомпрессора.
Сжатый циркуляционный газ соединяют с исходной азотоводороднойсмесью и вводят в цикл синтеза перед испарителем 8, где он охлаждается до минус 4°С. Жидкий аммиак отделяют в центробежном сепараторе 9. Газ, содержащий около 3% (об.) NНз, направляют в колонну синтеза через теплообменник 6 и теплообменник 3. Жидкий аммиак из сепараторов 7, 9 и 16 направляют в товарный парк.
4.4 Операторная схема
Р
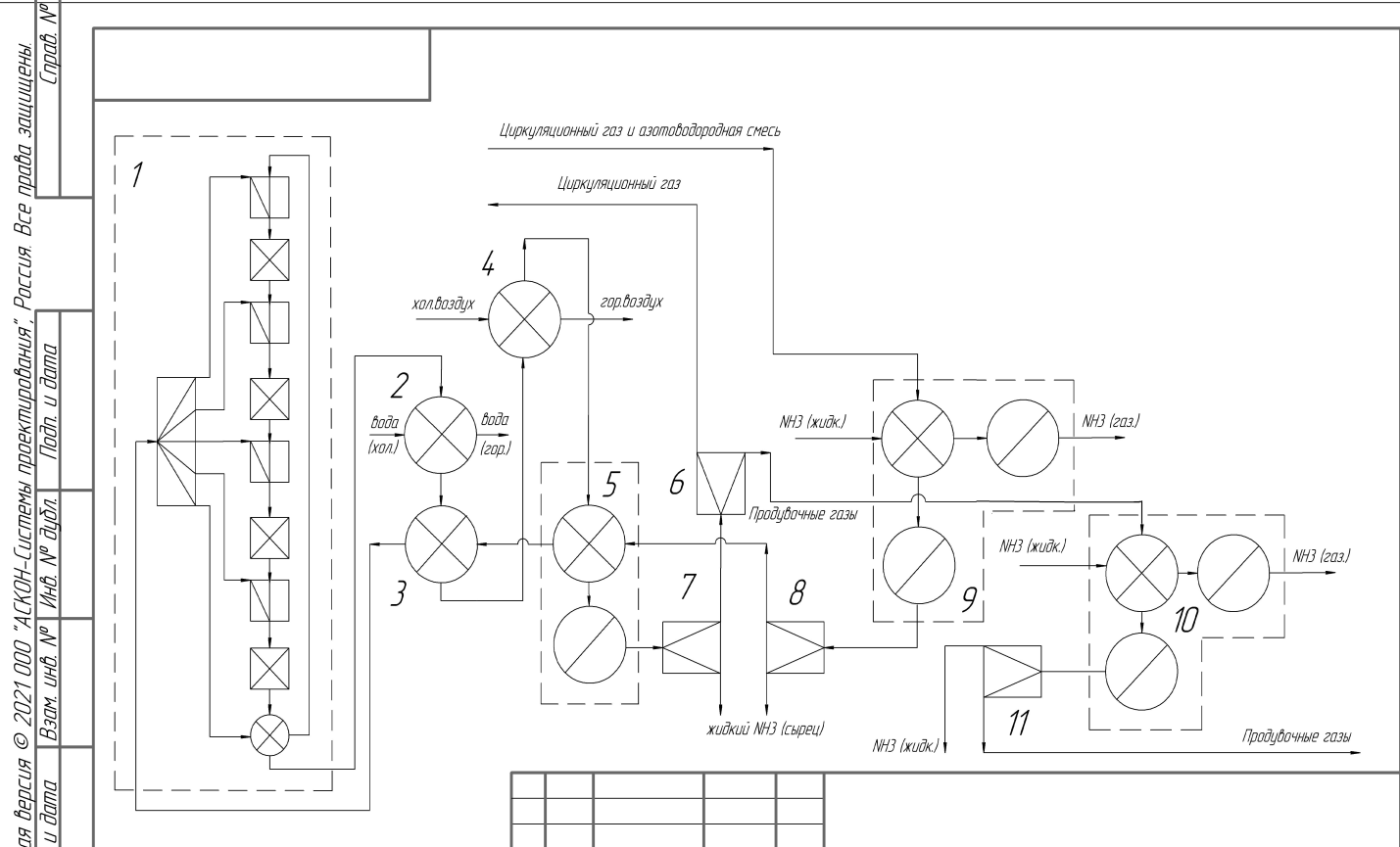
Колонна 1 состоит из 4 полок, на которых происходит синтез аммиака. На полки подается подогретый до 140°С циркуляционный газ. Выходящий из колонны газ проходит через серию теплообменников: охлаждается потоком воды в операторе 2, воздухом в операторе 4 и отдает свое тепло азотоводородной смеси в 3 и 5 операторах охлаждения. После теплообменника 5 аммиак частично конденсируется и в сепараторе 7 его разделяют на жидкую и газообразную фракции. Жидкую фракцию отправляют в товарный парк. Газовая фаза попадает в оператор разделения 6, где делится на циркуляционные и продувочные газы. Затем в операторе 10 продувочные газы охлаждаются потоком жидкого аммиака, и, переходя через оператор изменения агрегатного состояния выходит газообразный аммиак. Оставшийся аммиак так же проходит через оператор изменения агрегатного состояние и в операторе разделения 11 отделяют жидкий аммиак от продувочных газов. Продувочный газ впоследствии сжигают. Поступающую в процесс азотоводородную смесь с циркуляционным газом сначала охлаждают потоком жидкого аммиака в операторе охлаждения и охлажденная смесь, проходя через оператор изменения агрегатного состояния 9, конденсируется и жидкий аммиак отделяют от газообразного в операторе разделения 8. В дальнейшем азотоводородную смесь нагревают в операторах нагрева 3 и 5, после чего она поступает в колонну 1.
5. Выбор и обоснование конструкции основного аппарата
В современном агрегате синтез аммиака ведут на катализаторе СА-1 при температуре 420 – 500°С и давлении 32 МПа; объемная скорость 25-103 ч-1; производительность 1 м3 контактной массы составляет 20 - 40 т/сут. Такие условия организации химико-технологической системы, состоящей из нескольких химико-технологических процессов большой единичной мощности, позволяют снизить капитальные вложения, полнее утилизировать низко- и высокопотенциальную теплоту процесса и, следовательно, снизить себестоимость продукта.
Высокопотенциальную теплоту конвертированного газов используют для получения пара высокого давления, применяемого в турбинах - приводах компрессоров и насосов высокого давления; низкопотенциальную теплоту - для получения технологического пара низкого давления, подогрева воды, получения холода и других нужд.
В новых системах широко применяют аппараты воздушного охлаждения, что сокращает расход воды.
Основной аппарат агрегата синтеза аммиака - колонна синтеза, отвечающая требованиям ступенчатого синтеза аммиака. На рисунке представлена схема четырехполочной колонны синтеза.
Рис. 6 Колонна синтеза аммиака
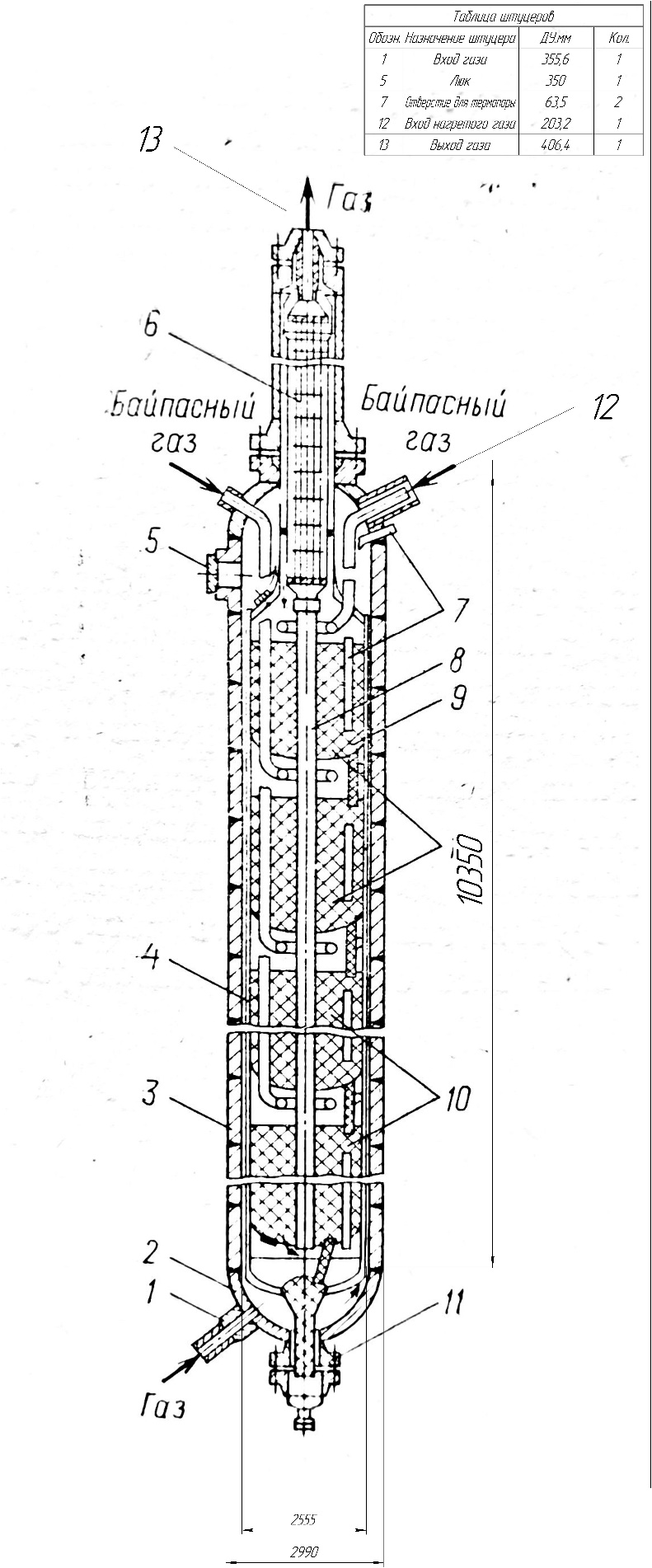
1- штуцер; 2 – днище; 3 – корпус высокого давления; 4 – корпус насадки; 5 – люк для загрузки катализатора; 6 – теплообменник; 7 – карман для термопары; 8 – центральная труба; 9 – люк; 10- полки с катализатором; 11 – люк для выгрузки катализатора.
Колонна представляет собой вертикальный аппарат из корпуса высокого давления и катализаторной коробки из четырех полок, размещенной в нем. Между ними имеется зазор, по которому проходит поток газа при температуре 140 С, предохраняя корпус колонны от воздействия высоких температур из зоны катализатора. На 1 катализаторной полке размещено 5,83 м3 катализатора, на 2 - 6,8 м3, на 3 полке – 10,7 м3 и на 4 полке – 12,63 м3. Загрузку и выгрузку катализатора ведут через люки, так как катализаторная коробка не извлекается.
Теплообменник расположен в верхней части основного корпуса. Внутренний диаметр колонны 2,4 м, толщина стенки 218 мм, высота около 19 м.
Для процесса синтеза аммиака существенное значение имеет оптимальный температурный режим. Количество катализатора на полках колонны увеличивается по мере снижения скорости газа и снижении степени превращения азотоводородной смеси.
Регулирование температур и обеспечение автотермичности процесса обеспечивается с помощью системы внешних теплообменников и теплообменников, расположенных в слое контактной массы. Для обеспечения максимального синтеза процесс следует начинать при высокой температуре и по мере увеличения степени превращения понижать ее.
Рис 7. Распределение температур по высоте слоя катализатора полочной колонны синтеза аммиака.
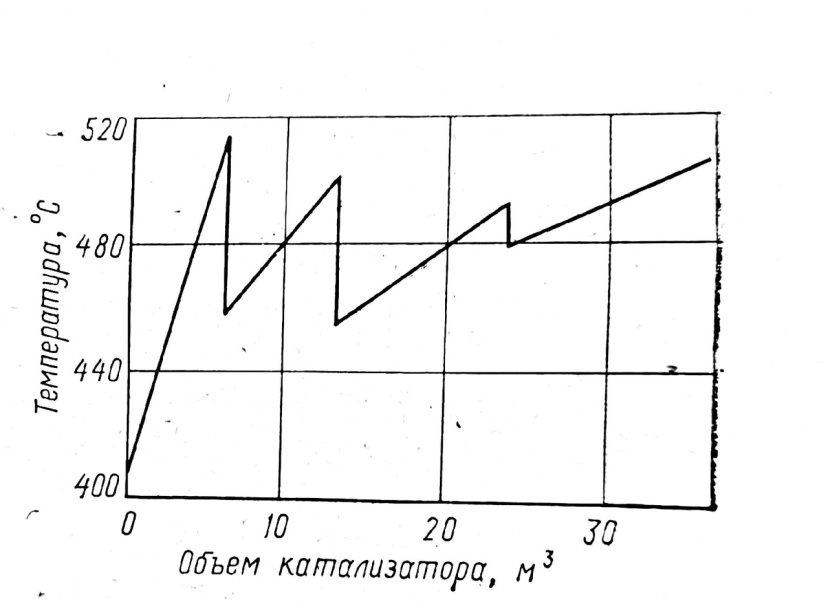
Для снижения влияния высокой температуры на корпус, холодную азотоводородную смесь подают снизу-вверх по кольцевому зазору между корпусом колонны и катализаторной коробкой, после чего смесь поступает в межтрубное пространство теплообменника, нагреваясь в нем до 420 С. Для регулирования температуры газовой смеси имеется байпас, через который газ идет в зону катализатора, минуя теплообменник. Нагретый газ фильтруется через 4 слоя катализатора, затем по центральной трубе поднимается вверх, поступает в трубки теплообменника, охлаждаясь в нем до 330 С и выходит через верхний штуцер колонны синтеза. Для регулирования температуры в слоях катализатора в слой катализатора подводят для охлаждения байпасный газ.
6. Расчет материального и энергетического балансов
6.1 Расчет материального баланса
Проводить расчет будем на 1000 Нм3/ч газовой смеси.
Химическая реакция:N2(г)+3 H2(г)=2NH3(г)
Воспользуемся литературными данными, чтобы определить количество веществ, которые будут на входе в колонну синтеза и расчитаем степень превращения, чтобы полученный материальный баланс совпал с литературными данными на выходе.
Таблица 6.1 – Литературные данные материального баланса
Состав из литературы | ||
Сырье | На входе | На выходе |
NH3(г) | 2,8% | 17,5% |
H2 (г) | 66,0% | 54,3% |
N2(г) | 22,0% | 18,1% |
CH4 | 4,2% | 5,1% |
Ar | 5,0% | 5,0% |
Cумма | 100,0% | 100,0% |
Расчеты проводились с использованием программы Excel из пакета MS Office 2016.
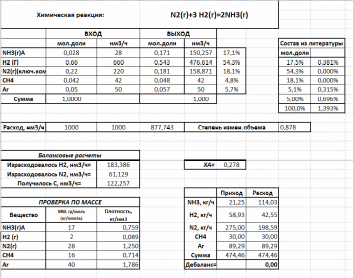
Таблица 6.2 – Результаты материального баланса
Материальный баланс | ||||||
| На входе | На выходе | ||||
Сырье | мол.доли | Нм3/ч | кг/ч | Нм3/ч | мол.доли | кг/ч |
NH3(г)A | 2,80% | 28 | 21,25 | 150,2571 | 17,1% | 114,03 |
H2 (Г) | 66,00% | 660 | 58,93 | 476,6144 | 54,3% | 42,55 |
N2(г) | 22,00% | 220 | 275,00 | 158,8715 | 18,1% | 198,59 |
CH4 | 4,20% | 42 | 30,00 | 42 | 4,8% | 30,00 |
Ar | 5,00% | 50 | 89,29 | 50 | 5,7% | 89,29 |
Сумма | 1,0000 | | 474,46 | | 100,0% | 474,46 |
Расход | | 1000 | | | 877,74 | |
По итогам материального баланса мольное содержание сырья на выходе практически совпало с литературным.
6.2 Расчет теплового баланса
На основе материального баланса рассчитаем тепловой. Так как наша реакция является экзотермической и протекает в адиабатном реакторе, то для нас будет актуально данное уравнение: QФИЗ.ВХ + QХР = QФИЗ.ВЫХ + QПОТЕРЬ.
Воспользуемся температурой, взятой из литературных данных, на входе: 128⁰С и на выходе 330⁰С.Полученная температура в тепловом балансе на выходе должна сойтись с литературной. Воспользуемся данными из таблицы 2.2.
Рассчитаем в Exсel теплоемкости для всех веществ, а так же теплоты потоков для составления теплового баланса.
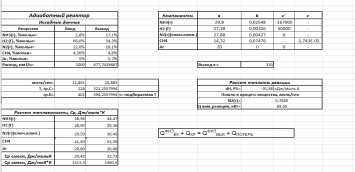
Полученные данные приведены ниже:
Таблица 6.3 – Результаты теплоемкости
Расчет теплоемкости | Вход Дж/моль*К | Выход, Дж/моль*К |
NH3(г) | 38,98 | 42,18 |
H2 (Г) | 28,90 | 29,14 |
N2(г) | 29,59 | 30,06 |
CH4 | 41,50 | 47,96 |
Ar | 20,00 | 20,00 |
Ср смеси, Дж/моль*К | 29,42 | 31,92 |
Ср смеси, Дж/Нм3*К | 1313,3 | 1424,9 |
Таблица 6.4 – Результаты теплового баланса
Приход | Расход | ||||
Статья | кВт | % | Статья | кВт | % |
Теплота, вносимая потоком | 146,28 | 67,75 | Теплота, уносимая потоком | 211,61 | 98,00 |
Теплота химических реакций | 69,65 | 32,25 | | | |
| | | Потери | 4,32 | 2,00 |
Итого | 215,93 | 100,00 | Итого | 215,93 | 100,00 |