Файл: Правила работы в учебнопроизводственной мастерской Виды работ, выполняемых на токарных станках.doc
ВУЗ: Не указан
Категория: Не указан
Дисциплина: Не указана
Добавлен: 16.03.2024
Просмотров: 12
Скачиваний: 0
ВНИМАНИЕ! Если данный файл нарушает Ваши авторские права, то обязательно сообщите нам.
3.Обработка деталей на токарных станках
3.1 Организация рабочего места токаря.
Планировка рабочего места, как и его оснащение, зависит от многих факторов, в том числе от типа станка и его размеров, размеров и формы заготовок, типа и организации производства и др. При обработке заготовок с установкой в центрах левой рукой планировка рабочего места. Инструментальный шкаф в этом случае располагается с правой стороны от рабочего, а стеллаж для деталей — слева, если токарь устанавливает заготовку и снимает обработанные детали правой рукой, то инструментальный шкаф располагается с левой стороны от рабочего, а стеллаж — с правой. Перед станком на полу укладывают деревянную решетку. Высоту расположения решеток выбирают в зависимости от роста рабочего.
3.2 Техника безопасности при работе на токарных станках.
При выполнении работ на токарных станках токарь должен выполнять все общие правила безопасной работы на металлорежущих станках и целый ряд специфических правил, используемых
только при токарной обработке:
1. При использовании прутка в качестве заготовки необходимо
следить, чтобы его конец, выступающий с противоположной стороны шпинделя, был огражден на всю длину. Ограждение должно
быть прочным. Длина прутка должна соответствовать паспортным
данным станка.
2. Закреплять заготовку в патроне за достаточно большую ее
часть. Желательно, чтобы из кулачков патрона выступало не более
2 — 3 диаметров заготовки. При большем вылете заготовки необходимо поджимать ее при обработке центром, установленным в
заднюю бабку.
3. При обработке нежестких заготовок, длина которых превышает диаметр более чем в 10 раз, а при скоростном или силовом
точении в 8 раз, использовать люнеты.
4. Вылет резца из резцедержателя не должен превышать более
чем в 1,5 раза высоту державки.
5. При установке резцов относительно оси центров под основание резца нужно устанавливать хорошо обработанные подкладки,
чтобы добиться требуемого расположения резца. Подкладки должны соответствовать размерам основания резца и не должны быть
смещены относительно друг друга.
6. При обработке вязких материалов применять конструкции
резцов, позволяющие дробить образующуюся сливную стружку,
например, резцы с накладными стружколомателями или с канавками на передней поверхности резца.
7. При обработке твердых хрупких материалов с образованием
стружки надлома использовать в процессе обработки специальные стружкоотражатели, прозрачные экраны или индивидуальные
средства защиты, например очки.
8. Стружку удалять только специальным крючком, щеткой или
скребком. Категорически запрещается удалять стружку руками
или струей воздуха.
9. Подводить режущий инструмент к уже вращающейся заготовке.
10. Выключать вращение заготовки после отвода инструмента.
11. Запрещается тормозить вращающийся шпиндель рукой.
12. Запрещается поддерживать отделяемую часть заготовки рукой при отрезании.
13. При выполнении ручных операций отводить суппорт, заднюю бабку на безопасное расстояние.
14. При выполнении работ с использованием пиноли ее вылет
должен быть минимальным.
15. Измерение обрабатываемой детали должно производиться
только после выключения фрикциона, отвода суппорта и задней
бабки.
16. Запрещается облокачиваться на станок и размещать заготовки и другие предметы на направляющих станка.
17. Запрещается оставлять в задней бабке или револьверной головке инструменты, которые не используются при обработке данной заготовки.
18. Устанавливать и снимать патроны, планшайбы необходимо
с помощью специальных приспособлений или при помощи грузоподъемного устройства, оснащенного специальным захватом.
19. Запрещается допускать воздействия движущихся частей
станка на электропроводку, трубопроводы подачи жидкости или
воздуха.
20. Запрещается переносить через работающий станок какие-либо предметы.
3.3 Назначение, классификация, устройство токарных станков.
В токарную группу входят девять типов станков, различающихся по назначению, компоновке, степени автоматизации и другим
признакам.
К станкам токарной группы относятся токарно-винторезные,
токарно-револьверные, лоботокарные, токарно-карусельные, токарные автоматы и полуавтоматы, токарные станки с программным управлением обработки заготовок.
Станки отечественного производства имеют цифровое обозначение моделей.
Цифровое обозначение станка позволит правильно выбрать
нужные группу, тип, технические параметры, точность станка, необходимые для изготовления требуемого изделия.
Первая цифра в обозначении показывает, к какой группе относится станок: токарной, фрезерной, сверлильной и т. д. Вторая цифра указывает на тип станка в группе. Две последние
цифры условно определяют важнейшие технические параметры
станка.
Все станки, обозначение которых начинается с единицы, — токарные. В свою очередь токарные станки делятся на 9 типов.
Две последние цифры обозначают: для токарно-винторезных
станков — высоту центров над станиной, для револьверных —
наибольший диаметр обрабатываемого прутка, для карусельных —
наибольший диаметр планшайбы и т. д.
Буква после первой или второй цифры указывает на усовершенствование станка по сравнению с первой моделью.
Буква в конце марки означает, что в модель станка внесены некоторые изменения, например, повышена точность (П), станок с
числовым программным управлением (Ф) и т. д. Пример расшифровки марки токарно-винторезного станка
мод. 16К20:
1 — станок относится к токарной группе;
6 — токарно-винторезный;
К — в станок внесены некоторые изменения;
20 — высота центров над станиной 200 мм.
Серийный выпуск токарных станков в СССР был впервые осуществлен на московском заводе «Красный пролетарий».
Все металлорежущие станки классифицируются:
по степени универсальности:
На универсальные, позволяющие выполнять любой вид обработки, характерный для станков группы, например токарновинторезные станки;
Специализированные, предназначенные для обработки деталей
схожих по конфигурации и размерам;
Специальные, предназначенные для обработки одинаковых деталей или выполнения только одной операции.
по точности:
Нормальной точности (Н);
Повышенной точности (П);
Высокой точности (В);
Особо высокой точности (А);
Особо точные (С).
по массе:
Легкие — до 1 т;
Средние — до 10 т;
Крупные — до 15 т;
Тяжелые — до 100 т;
Особо тяжелые — свыше 100 т.
Подробно рассмотрим токарно-винторезные станки, имеющие
наиболее широкое использование в единичном и серийном производстве.
Основной объем токарных работ производится на токарновинторезных станках, они используются в инструментальном производстве, в приборостроении, в машиностроении и других областях промышленности. На них можно выполнить все виды токарных работ, а также нарезание резьбы.
Постоянно производится усовершенствование этих станков путем повышения точности, совершенствования управления, увеличения диапазонов скоростей и подач.
Все сборочные узлы и механизмы токарно-винторезных станков имеют одинаковое название, назначение и расположение.
-
Приспособление, режущий и измерительный инструмент применяемый при работе на токарных станках.
-
Патроны. Предназначены для зажима деталей или заготовок. -
Вращающиеся центры. Устанавливаются в пиноль задней бабки, служат для дополнительного крепежа детали. -
Резцедержатели. Предназначены для быстрой смены токарных резцов.
Токарные резцы применяются для обработки различных поверхностей деталей: цилиндрических, конических, фасонных, торцовых и т. д.
Резцы классифицируются в зависимости от различных параметров.
По назначению различают резцы:
Проходные (прямые, отогнутые упорные);
Подрезные (торцовые);
Прорезные (канавочные);
Отрезные;
Фасонные;
Резьбовые;
Расточные.
В зависимости от вида обработки на черновые, служащие для
предварительной обработки, и чистовые, служащие для окончательной (чистовой) обработки.
1) Штангенинструменты - штангенциркули, штангенглубиномеры, штан- генрейсмусы, штангензубомеры;
2) Микрометрические инструменты - рычажные микрометры, резьбовые микрометры, нутромеры, глубиномеры;
3) Рычажно-измерительные инструменты-индикаторы, миниметры, индикаторные скобы;
4) Плоскопараллельные концевые меры длины - измерительные плитки;
5) Угловой инструмент - конусные угломеры, синусные линейки, угломерные плитки;
6) Оптические приборы - инструментальные микроскопы, универсальные микроскопы, вертикальные оптиметры, оптические делительные головки, большой проектор;
7) Плоские стеклянные пластины (метод интерференции);
8) Одномерный инструмент - калибры, шаблоны.
3.5 Способы установки заготовки на станке
Установка заготовок в патронах. Производится при обработке деталей небольшой длины. Наиболее часто используются
трехкулачковые самоцентрирующие и цанговые патроны.
Установка и закрепление заготовок в центрах. Если необходимо обработать деталь с высокой степенью соосности левой и правой сторон, то используются центры.
Поводковые устройства. Для передачи вращения от шпинделя
к заготовке, установленной в центрах, служат поводковые устройства. Простейшее из них — токарный хомутик.
Установка заготовок в патронах с поджимом задним центром. Такой способ установки самый жесткий, обычно используется
при обработке заготовок, у которых отношение длины к диаметру
больше 3 при черновом точении. При перезакреплении заготовки
для обработки с другой стороны точность центрирования теряется.
-
Установка, выверка и закрепление резцов в резцодержателе.
Перед обтачиванием нужно правильно установить резец в резцедержателе, следя за тем, чтобы выступающая из него часть резца была возможно короче — не больше 1,5 высоты его стержня. В большинстве случаев рекомендуется устанавливать вершину резца на высоте центров станка. Для этого применяют подкладки (не больше двух), помещая их под всей опорной поверхностью резца. Подкладка представляет собой плоскую стальную линейку длиной 150—200 мм, имеющую строго параллельные верхнюю и нижнюю поверхности. Токарь должен иметь набор таких подкладок разной толщины, чтобы получить необходимую для установки резца высоту. Не следует для этой цели пользоваться случайными пластинками.
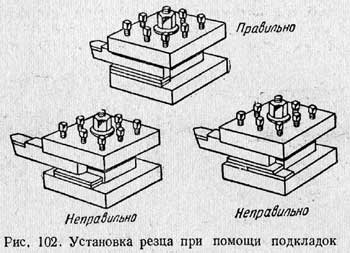
-
Обработка наружных цилиндрических и торцевых поверхностей на токарном станке.
4.1 Обработка гладких цилиндрических поверхностей и поверхностей с уступами.
Требования, предъявляемые к цилиндрическим поверхностям, выдержать трудно, так как целый ряд факторов влияет на изготовление детали, например, износ деталей станка и приспособлений, износ режущего инструмента, правильность выбора способа закрепления заготовки, температура окружающей среды, неравномерность припуска, неоднородность твердости поверхностного слоя, наличие нароста на инструменте, вибрации, передаваемые от других станков, и т.д. Все эти факторы необходимо учитывать при обработке, чтобы в результате их влияния не возникали различные погрешности формы цилиндрической формы, такие как конусообразность, бочко-образность, седло-образность, изогнутость, овальность, огранка. Эти погрешности могут привести к некачественному изготовлению детали и невозможности использовать ее по назначению.
К цилиндрическим поверхностям предъявляются следующие требования:
Прямолинейность образующей;
Цилиндричность: в любом сечении, перпендикулярном оси,
Окружности должны быть одинакового диаметра (не должно
быть конусообразности, бочкообразности, седлообразности);
Круглость: любое сечение должно иметь форму правильной
окружности (не должно быть овальности или огранки);
Соосность: расположение осей всех ступеней ступенчатых деталей на общей прямой.