Файл: 1 Общая характеристика с места прохождения практики 5.docx
Добавлен: 19.03.2024
Просмотров: 77
Скачиваний: 0
ВНИМАНИЕ! Если данный файл нарушает Ваши авторские права, то обязательно сообщите нам.
-
вести записи по подтверждению выполняемой деятельности в соответствии с должностными обязанностями персонала отдела.
Участок организационной структуры в организации:
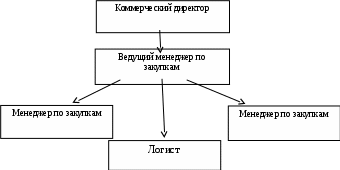
Рисунок 6. - Организационная структура ОМТС
ПК 2.2. Методология проектирования внутрипроизводственных логистических систем при решении практических задач
Методология - учение о методах, способах и стратегиях исследования предмета. Методологию можно рассматривать в двух срезах: как теоретическую, и она формируется разделом философского знания гносеология, так и практическую, ориентированную на решение практических проблем и целенаправленное преобразование мира.
Методология проектирования логистических систем базируется на совокупности принципов и методов системного подхода, системного анализа, проектирования и моделирования.
Принципы проектирования логистических систем, совпадают с общими принципами логистики: системный подход, принцип общих логистических издержек, глобальной оптимизации, логистической координации, моделирования и информационно-компьютерной поддержки, выделения комплекса обеспечивающих подсистем, комплексного управления качеством, гуманизации всех функций и решений, устойчивости и адаптивности. Эти принципы лежат в основе проектирования логистических систем.
Системное проектирование больших и сложных систем, к которым относятся логистические системы, включает в себя две стадии проектирования:
1) макропроектирование (внешнее), предполагающее решение функционально-структурных вопросов, определение внешних и внутренних факторов, оказывающих воздействие на систему, выбор критериев оценки эффективности функционирования системы;
2) микропроектирование (внутреннее, отражающее уровень отдельного экономического субъекта, склада, магазина и т.п.), которое связано с разбивкой звеньев и элементов логистической системы с учетом их взаимосвязи, и взаимодействия, специфических свойств и особенностей выполнения основных функций.
Методы проектирования логистических систем подразделяют на три класса: аналитические, имитационные и оптимизационные.
Аналитические методы, как правило, применяются для оценки и анализа существующих логистических систем. Они базируются на стандартных процедурах вычисления и рассматривают протекание логистических процессов и операций в условиях определенности и риска.
Имитационные методы находят широкое применение при проектировании в условиях неопределенности для принятия управленческих решений при наличии нескольких альтернатив. Имитационное моделирование наиболее эффективно при условии, когда параметры (факторы) логистической системы являются случайными величинами, подчиняющимися различным законам распределения, а материальные и сопутствующие потоки представляют собой случайные стационарные и нестационарные процессы.
Оптимизационные методы опираются на различные виды программирования (линейное, нелинейное, целочисленное и т. д.)- представленные в соответствующих разделах исследования операций. При проектировании логистических систем оптимизационные методы применяются при решении задач конфигурации цепей поставок (размещение объектов инфраструктуры, производств, терминалов, складов и т. п.); при выборе рациональных схем транспортировки, т. е. решении так называемых производственно-транспортно-складских задач; формировании стратегий управления запасами в многоуровневых логистических системах.
Возьмем для примера изготовление асбестовой ткани. Основное сырье для нее — это асбест и связующее волокно. Оно поступает на погрузчиках со склада в цех и распаковывается вручную. В ткацком цехе имеется автоматический весовой дозатор. По рецептурной карте оператор задает долю асбестового волокна и связующего. По пневмотранспортной линии идет раздача на оборудование и изготовление асбесто- волокнистой смеси. Эта смесь поступает на чесальный аппарат и изготавливается первый полуфабрикат — это ровница. Ровница по транспортеру подвесного конвейера поступает на прядильные машины и получается второй полуфабрикат — это пряжа. С прядильных машин в ручных тележках пряжа поступает на крутильные машины. После этого образуется третий полуфабрикат - асбестовая нить. Нить в ручных тележках поступает в ткацкое отделение, где часть отправляют к уточным автоматам, а другую часть на ткацкие станки. На уточных автоматах получают еще один полуфабрикат — это уточные початки; на ткацких станках нить развешивается на шпулярник. Далее эти компоненты перемещаются в соответствии с заданным рисунком ткани и получается асбестовая ткань. После этого ткань укладывают на поддон и электропогрузчик перемещает поддон на склад готовой продукции.
В организации ПАО «УралАТИ» используется следующая стадия проектирования – макропроектирование. Данная стадия предполагает решение функционально-структурных вопросов, определение внешних и внутренних факторов, оказывающих воздействие на систему, выбор критериев оценки эффективности функционирования системы Нами была составлена схема, как это происходит в организации
Схема макропроектирования продукции:

Склад сырья


Производство


Ткацкий цех


Изготовление асбесто-волокнистой смеси


Чесальный аппарат


Первый полуфабрикат- ровница


Прядильные машины


Второй полуфабрикат- пряжа



Крутильный машины

Третий полуфабрикат- асбестовая нить



Уточные автоматы

Ткацкие станки



Четвертый полуфабрикат -Уточные початки


Асбестовая ткань


Склад готовой продукции
Рисунок 7 - макропроектирование производства
ПК 2.3. Модели и методы управления запасами
Основная цель управления запасами – обеспечение производственных процессов и снижение сопутствующих затрат. Конечной целью является извлечение прибыли, обеспечение стабильности работы. Рассмотрим задачи политики:
-Установление точного объема запасов, имеющихся на складе на данный момент.
-Установление объема запасов, который нужно закупить в ближайшее время.
-Определение оптимальных сроков исполнения заказов.
Под управлением понимается расчет норм запаса, контроль над фактическими объемами, своевременное пополнение запасов.
Самыми распространенными моделями управления запасами являются:
1) Модель Уилсона. Является основной. Подходит для расчета нужного объема запасов, оптимизации товара. Траты на запасы делятся на две категории: стоимость партии товара и расходы на хранение. При минимизации трат на запасы можно направить средства на хранение.
2) Модель ABC. В рамках этой модели осуществляется объемно-стоимостный анализ. Резервы подразделяются на три группы. Группы формируются исходя из этих категорий: стоимость, объем, частота пользования. Группа «А» – это дорогостоящая продукция с длительным циклом пользования. Группа «В» – это запасы, которые меньше воздействуют на непрерывное производство. Группа «С» – это продукция с низкой стоимостью, которая не влияет на окончательный финансовый результат.
3) Модель MRP. Представляет собой компьютерную систему со следующими функциями: обработка заказа, создание графика запасов.
4) Модель установленного уровня. Новые закупки осуществляются только при достижении определенного порога запасов. Порог этот определяется самой компанией.
Среди принципиальных систем регулирования запаса следует выделить:
-
модель управления запасами с фиксированным размером заказа; -
модель управления запасами с фиксированным интервалом времени между заказами; -
модель управления запасами с установленной периодичностью пополнения запасов до постоянного уровня; -
модель «минимум-максимум»
На предприятии «УралАТИ» используется модель установленного уровня запасов. Более подробно можно рассмотреть в схеме.
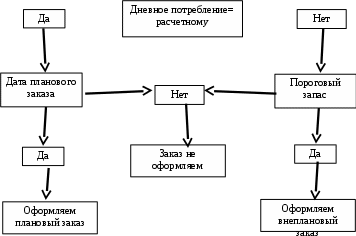


Рисунок 8 -схема установленного уровня запасов
Данная модель определяет уровень запасов от производства и отправки готовой продукции потребителю. Когда на складе сырья недостаточно запасов, сотрудники отдела сбыта и ОМТС определяют недостающие запасы и пополняют их. Также на предприятии создан страховой запас ключевых видов сырья, полуфабрикатов и готовой продукции. Сбалансированность страховых запасов позволяет предприятию всегда своевременно и в полном объеме выполнить заказы потребителей.
ПК 2.4. Управление заказами, запасами, транспортировкой, складированием, грузопереработкой, упаковкой, сервисом.
Управление заказами в организации начинается с приема и обработки заказов потребителей материальных ресурсов или готовой продукции. При этом используется интегрированный подход к управлению заказами. Он предполагает принятие оптимальных решений по закупкам и запасам материальных ресурсов, производству, складированию и распределению готовой продукции на базе точного прогнозирования потребительского спроса. Это возможно при условии высокой готовности организации к поставкам заказанных товаров, высокого качества сервиса поставок, а также функционирования логистической информационной системы и базовых логистических систем.
Управление запасами в логистике — это системный подход к получению, хранению и получению прибыли от некапитальных активов (сырья и готовой продукции). Правильный запас, на нужных уровнях, в нужном месте, в нужное время и по разумной цене.
Управление транспортировкой фирмы состоит из основных этапов:
-выбора способа транспортировки;
-выбора вида транспорта;
-выбора транспортного средства;
-выбора перевозчика и логистических партнеров по транспортировке;
-оптимизации параметров транспортного процесса.
Доступны различные методы управления складированием: процессно-ориентированное управление складированием, а также управление складами с учетом схемы размещения. Цель управления складированием заключается в отображении шагов комплексного процесса приемки на склад или отпуска со склада на основе процессов или данных схемы размещения. Во время приемки на склад или отпуска со склада отдельные шаги процесса могут выполняться на одном или нескольких уровнях (т. е. через типы промежуточного складирования).