Файл: Курсовой проект 46 л., 4 рис., 12 табл., 15 источников, 1 прил.docx
ВУЗ: Не указан
Категория: Не указан
Дисциплина: Не указана
Добавлен: 11.04.2024
Просмотров: 56
Скачиваний: 0
ВНИМАНИЕ! Если данный файл нарушает Ваши авторские права, то обязательно сообщите нам.
1.3.1 Сырье процесса.
Сырьем для производства пеков, на сегодняшний день, могут служить различные фракции нефти, как дистиллятные, так и остаточные, а также продукты ее химической переработки, отвечающие общим требованиям, основным из которых является содержание большого количества полициклоароматических (ПЦА) углеводородов. Чем выше содержание ПЦА, тем выше выход пекового остатка. В свою очередь присутствие гетероэлементов в сырье является нежелательным, также как и твердых дисперсных частиц. Именно от этих факторов зависит термическая стабильность пека, а также его способность к образованию жидкокристаллической структуры или мезофазы.
Для получения нефтяных волокнообразующих пеков наиболее перспективным сырьем являются тяжелые смолы пиролиза углеводородов. Однако и другие остаточные продукты нефтепереработки могут служить сырьем для получения волокнообразующих пеков при их соответствующей подготовке, а также пеков, используемых в других направлениях, в том числе и для приготовления анодных масс в металлургии. Применение смесевого сырья, прошедшего специальную подготовку, также является перспективным направлением.
В качестве сырья так же могут быть использованы остатки прямой перегонки нефти. Эти продукты представляют собой растворы нефтяных высокомолекулярных соединений, таких как смолы и асфальтены, в сложной многокомпонентной смеси с низкой степенью конденсации углеводородов, а также содержанием гетероатомных соединений. Состав этих остатков, также как структура и свойства, полностью определены природой нефти, из которой они получены. При практическом же рассмотрении, не менее определяющим фактором при их применении является глубина и четкость отбора дистиллятных фракций из этой нефти.
В отличие от прямогонных остатков, для крекинг - остатков характерны большая плотность и коксуемость. В свою очередь они более ароматизированы и степень конденсации ароматических структур, содержащихся в них, также выше. Асфальтены и смолы, содержащиеся в крекинг – остатках, отличает меньшая молекулярная масса, чем у соответствующих компонентов прямогонных остатков. Это возникает в результате деструкции парафино – нафтеновых углеводородов в процессе крекинга.
Известно, что в качестве сырья для получения нефтяных пеков наиболее желательны остаточные нефтепродукты, обладающие высокой плотностью, ароматичностью и малым содержанием серы. Однако из-за высокой потребности в сырье такого качества для коксования ресурсы малосернистых нефтяных остатков являются ограниченными. Именно поэтому возникает потребность вовлечения в переработку сернистых дистиллятных крекинг-остатков, являющихся побочным продуктом процесса получения сырья для технического углерода.
1.3.2 Температура процесса.
Поскольку энергия активации различных реакций, протекающих при термолизе, существенно отличается, температура проведения процесса играет важнейшую роль. Правильно подобранный температурный режим позволяет обеспечить требуемую скорость термолиза, соотношение между реакциями распада и уплотнения, а также скорость реакций поликонденсации, регулируя тем самым свойства фаз.
При регулировании продолжительности процесса представляется возможным обрывать на требуемой стадии термолиз, получая при этом продукт заданного качества.
При пониженных температурах, скорость реакций также будет низкая, а в продуктах термолиза будут преобладать нафтено-ароматические структуры с короткими боковыми алкильными цепочками. В дальнейшем они будут препятствовать реакциям уплотнения и формирования мезофазы.
При повышенных температурах скорости всех реакций резко возрастают. Выбор оптимальной температуры сводится к составу сырья подлежащего термолизу, и обычно варьируется в интервале от 380-440 °С.
1.3.3Давление.
В процессе термолиза давление следует рассматривать как параметр, оказывающий значительное влияние на скорость газофазных реакций, на фракционный и групповой углеводородный состав. Изменение давления обуславливает изменение скоростей образования и расходования, а также молекулярной структуры асфальтенов, карбенов и карбоидов.
С повышением давления возрастают скорости радикально-цепных газофазных реакций распада с образованием низкомолекулярных соединений, увеличивается содержание парафино-нафтеновых углеводородов и карбоидов. Обычно процесс термополиконденсации проводят под давлением 0,1–0,5 МПа, в зависимости от вида сырья и получаемой продукции.
1.4 Аппаратурное оформление
Известно, что процесс термоконденсации нефтяных остатков с получением пеков по аппаратурному оформлению аналогичен замедленному коксованию. Оборудование установок производства пеков можно разделить на следующие группы:
- технологическое оборудование, с помощью которого осуществляется процесс пекования. Сюда входят трубчатые печи, реакторы пекования, насосы, колонная аппаратура, запорная и переключающая арматура, теплообменники, конденсаторы, трубопроводы, металлоконструкции и др.
- oборудование для внутриустановочной обработки и транспортирования пека. К ним относятся мостовые и козловые грейферные краны, питатели, дробилки, конвейеры, грохоты, бункеры, склады, грануляторы, бобины и др.
1.4.1 Трубчатая печь.
Трубчатая печь представляет собой огневой нагреватель первичного и вторичного сырья коксования до температуры, требуемой технологическим режимом. На установках в основном применяют радиантно-конвекционные трубчатые печи коробчатого типа. Они имеют две камеры радиации (радиаптные камеры) и одну камеру конвекции (конвекционную камеру). Внутри камер расположены трубчатые змеевики. В камерах радиации сжигается топливо, поэтому их называют также топочными камерами. Змеевики, расположенные в камерах радиации, получают тепло главным образом излучением (радиацией). Трубы конвекционной камеры получают тепло главным образом конвекцией — путем омывания их дымовыми газами, поступающими из камер радиации, и частично радиацией (от излучения газов и кладки). Большой объем топочного пространства печи позволяет применять длиинофакельное сжигание топлива и иметь интенсивный лучистый теплообмен. Для равномерного обогрева трубчатого змеевика вдоль боковых стен в амбразурах из огнеупорного кирпича расположены комбинированные форсунки. При сжигании топлива образуется факел, температура, размеры и (конфигурация которого существенно влияют на теплоотдачу. Факел представляет собой струю газов со взвешенными в ней раскаленными частицами аморфного углерода, образующимися в процессе горения.
Характерной особенностью теплового режима работы печи пекования являются высокие начальные температуры вторичного сырья (360-380 °С), поступающего на нагрев. Это вызывает повышение температуры уходящих дымовых газов, увеличение потерь тепла и снижение коэффициента полезного действия печи. Помимо перерасхода топлива высокие температуры уходящих газов способствуют более интенсивному износу дымовых труб.
1.4.2 Ректификационная колонна.
Колонная аппаратура установок производства пеков включает ректификационные и отпарные колонны. Из них основными являются ректификационные колонны, конструкция которых разработана для специфических условий процесса пекования.
Ректификационная колонна предназначена для разделения нефтяных паров и газов, поступающих из реакторов, на отдельные фракции (газ, бензин, легкий газойль и др.). Кроме того, в колонну вводят первичное сырье. Вступая в контакт с более горячими парами и газами ректоров пекования, первичное сырье смешивается с ним, обогащается тяжелыми компонентами (рециркулятом) и выводится из колонны в качестве вторичного сырья.
Ректификационная колонна представляет собой вертикальный аппарат, имеющий внутреннее оборудование, которое обеспечивает нормальное проведение процессов испарения, контактирования и ректификации. В ректификационной колонне расположены барботажные тарелки, на которых происходит массо- и теплообмен между средами, движущимися навстречу друг другу. Конструкция барботажных тарелок должна обеспечивать раздрабливание паров на мелкие пузырьки, их равномерное распределение по сечению тарелки, где происходит обмен, а также одинаковое погружение элементов (колпачков) тарелки в жидкость, что достигается строго горизонтальным положением тарелки.
1.4.3 Реактор.
Реактор представляет собой автоклав периодического действия. На установке может работать каскад реакторов.
В процессе термической обработки в результате реакций конденсации и полимеризации, а также частичного пиролиза с последующей конденсацией в пеке накапливаются продукты поликонденсации, что сказывается на его групповом составе и физико-химических свойствах. Одновременно в процессе длительного нагрева происходит удаление легколетучих компонентов смолы. Для интенсификации процесса и получения пека с заданной температурой размягчения термическая обработка сочетается с дегидрирующим воздействием кислорода воздуха.
Корпус и днища изготовлены из биметалла (сталь 20К + сталь ЭИ496).
2 Выбор и обоснование технологического осуществления процесса
В настоящее время известно несколько технологий получения нефтяных пеков. В работе [2] предложена принципиальная схема установки получения мезофазного волокнообразующего пека методом термополиконденсации ТСП.
Кубовый остаток из колонны К-1 насосу Н-2 подают в печь П-1. Нагретую реакционную массу подают в реактор Р-1 или Р-2, работающие периодически. После заполнения уровня 1/2-2/3, реактор Р-1 отключают, далее проходит сам процесс поликонденсации в потоке перегретого водяного пара с получением пека. Из реакторов Р-1 и Р-2 пек направляется в отгонную колонну К-2, в которой отгоняются летучие в этих условиях низкомолекулярные компоненты, а высококипящие компоненты подвергаются термополиконденсации до образования пека с заданным групповым составом и температурой размягчения. Принципиальная схема представлена на рисунке 2.1.
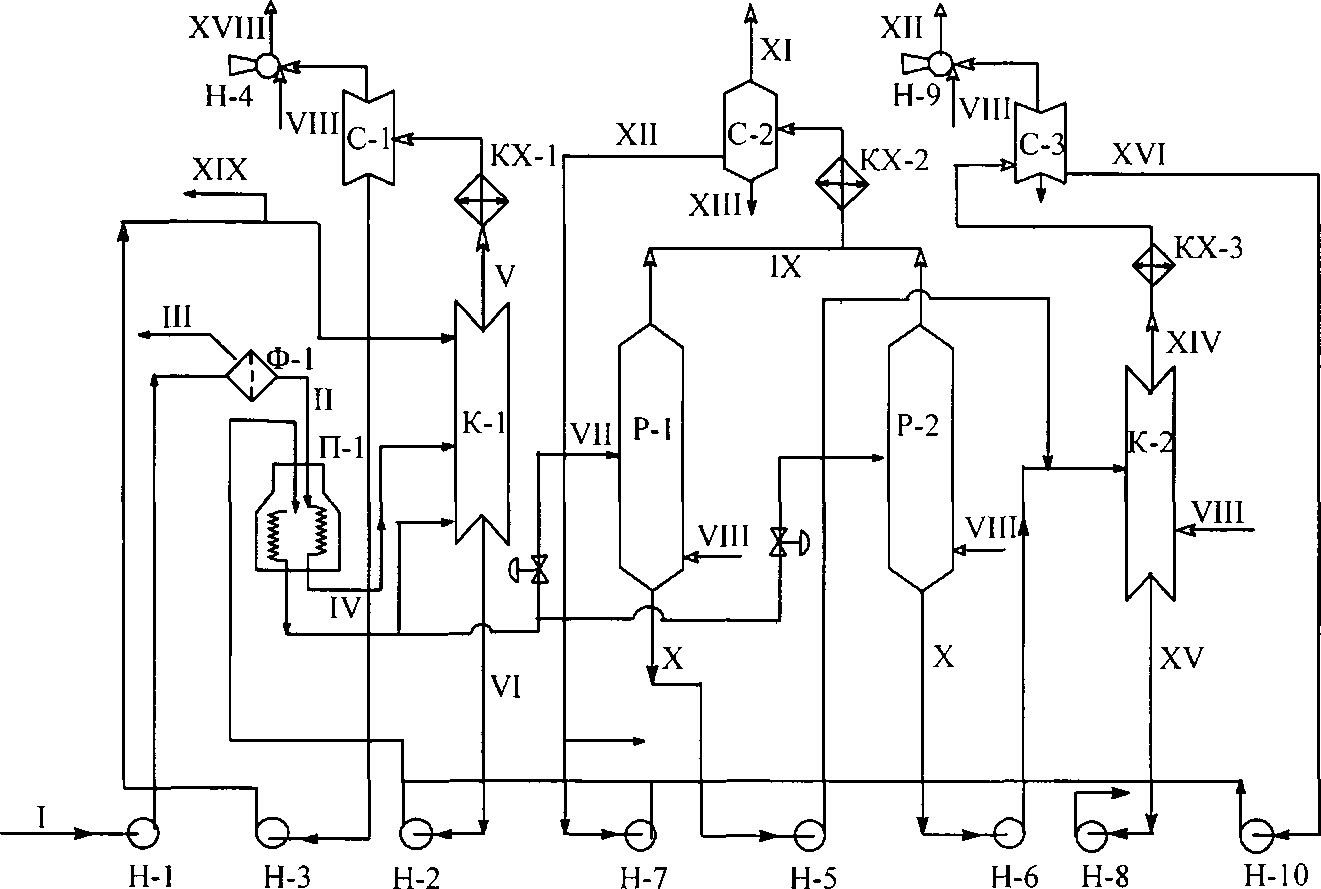
К-1 – ректификационная колонна, К-2 – отгонная колонна; П-1 – трубчатая печь; Р-1, Р-2 - реакторы; С-1 – С-3 – сепараторы
Рисунок 2.1 – Принципиальная схема установки получения МВП из тяжелой смолы пиролиза
В работе [3] предложена принципиальная технологическая схема промышленной установки получения пеков с заданными свойствами. Особенностью данного процесса является его гибкость, расширенный ассортимент, и как следствие снижение энергозатрат (рисунок 2.2).

П-1 – печь нагрева сырья; К-1 – ректификационная колонна; К-2 – отпарная колонна, Р-1, Р-2 – реакторы термополиконденсации; Е-1 – газосепаратор; ВХ-1 – воздушный холодильник; Х-1 – водяной холодильник; Т-1 – теплообменник; Р-3,Р-4 – реакторы пластификации.
Рисунок 2.2- Технологическая схема получения нефтяных пеков из тяжелой смолы пиролиза термополиконденсацией с узлом пластификации
Нагретая парожидкостная смесь поступает последовательно в реакторы термополиконденсации Р-1 и Р-2, где отделяются легкокипящие фракции и обеспечивается время выдержки в определенных условиях температуры и давления процесса термополиконденсации. Легкие фракции сырья и продуктов термополиконденсации поступившие из реакторов Р-1 и Р-2 в колонну К-1 подвергается разделению на бензиновую и газойлевые фракции. С низа реактора Р-2 выводится жидкий продукт термополиконденсации - нефтяной пек.