Файл: Курсовой проект 46 л., 4 рис., 12 табл., 15 источников, 1 прил.docx
ВУЗ: Не указан
Категория: Не указан
Дисциплина: Не указана
Добавлен: 11.04.2024
Просмотров: 56
Скачиваний: 0
ВНИМАНИЕ! Если данный файл нарушает Ваши авторские права, то обязательно сообщите нам.
Откуда:
ΔtБ =280-159,2 = 120,8 ˚С;
Δt М =150 - 120 = 30 ˚С;
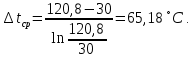
Предполагаемую поверхность теплообменника найдём по формуле:

где К – коэффициент теплопередачи, Вт/(м2

Q – тепловая нагрузка, кДж/ч;

На основании практических данных, учитывая показатели работы заводских теплообменников, принимаем коэффициент теплопередачи К = 150 Вт/(м2

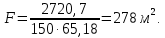
.
По ГОСТ 14246-79 выбираем кожухотрубчатый теплообменник со следующими характеристиками:
-
число ходов по трубам 2; -
наружный диаметр кожуховых труб 325 мм; -
наружный диаметр труб 25 мм; -
поверхность теплообмена 300 м2.
4.8 Расчет и выбор насосов
Рассчитываем требуемую производительность насоса, м3/ч:

где G – расход перекачиваемой жидкости, кг/ч;
ρt – плотность жидкости при температуре откачки, кг/м3.
Находится по формуле:

где α – коэффициент, зависящий от температуры.
Рассчитаем насос Н-1, подающий тяжелую смолу пиролиза на установку


Расчет для остальных насосов, проводится аналогичным образом. Подбор насосов производим исходя из требуемой производительности, а также температуры и вязкости перекачиваемой жидкости [13].
Расчетные и основные характеристики насосов сведём в таблицу 4.4.
Таблица 4.4 – Основные характеристики насосов
Перекачива-емый н/п | № насоса | Кол-во продукта, кг/ч | Температу-ра перекачки, ºС | Плот-ность, ρ204, кг/м3 | Температур-ная поправка, α | Плотность, ρt, кг/м3 | V, м3/ч | Марка насоса |
ТСП | Н-1 | 56216,93 | 50 | 1,052 | 0,00052 | 1036,55 | 54,23 | НК 8/10 |
Вторичное сырье | Н-3 | 67460,32 | 350 | 1,052 | 0,00052 | 882,05 | 76,48 | НК 12/40 |
Пек | НШ-1 | 19636,57 | 430 | 1,25 | 0,00078 | 930,2 | 21,11 | NM-18 |
Легкий газойль | Н-4 | 29401,46 | 280 | 0,89 | 0,00062 | 728,8 | 40,34 | НК-5/0 |
Бензин | Н-4 | 29401,46 | 40 | 0,75 | 0,00083 | 733,38 | 40,09 | А4 3В 4-3 |
5 Описание технологической схемы установки
Сырье – тяжелая смола пиролиза (ТСП), насосом Н-1 прокачивается последовательно через теплообменники предварительного нагрева сырья Т-1 и Т-2, где нагревается за счет тепла отходящих потоков. В Т-1 в качестве теплоносителя насосом Н-2 подается промежуточное циркуляционное орошение основной колонны К-1 и далее возвращается в колонну. В Т-2 в качестве теплоносителя насосом Н-3 подается фракция 205-350 °С из отпарной колонны К-2 и далее, пройдя воздушный холодильник ВХ-2, выводится с установки. Пройдя теплообменники, подогретая ТСП подается в колонну К-1 на фракционирование. Тепло, необходимое для осуществления массообменного процесса в колонну К-1 вносится вместе с дистиллятами из реакторов Р-1, Р-2. Из колонны К-1 насосом Н-4 вторичное сырье прокачивается через печь П-1, где нагревается за счет сжигания газового топлива и подается в реакторы термополиконденсации Р-1 и Р-2, которые работают циклически. Пары с верха колонны К-1 проходят последовательно воздушный холодильник ВХ-1, водяной холодильник Х-1 и поступают в сепаратор С-1, откуда дистиллят поступает на всас насоса Н-5, а газы выводятся на фракционирующую установку. В колонны К-1 и К-2 подается водяной пар, который вместе с дистиллятом К-1 конденсируется из сепаратора С-1 направляется в канализацию. Дистиллят из сепаратора С-1, представляющий собой фракцию н.к-200°С, насосом Н-5 подается на орошение обратно в колонну, а балансовый избыток выводится с установки. Пек из реакторов Р-1, Р-2 собирается в емкость Е-1, далее насосом НШ-1 выводится с установки.
6 Сводные показатели технологического режима
В таблице 6.1 представлены сводные показатели технологического режима процесса пекования.
Таблица 6.1 – Сводные показатели технологического режима
Оборудование | Параметр | Показатели |
Реактор | Высота, м | 9,65 |
Диаметр,м | 2 | |
Температура верха, º С | 395 | |
Температура ввода сырья, º С | 430 | |
Давление в реакторе, МПа | 0,3 | |
Печь | Длина радиантных труб, м | 4 |
Поверхность нагрева радиантных труб, м2. | 31 | |
Температура вторичного сырья на выходе , º С | 430 | |
Температура вторичного сырья на входе, º С | 350 | |
Давление на выходе, МПа | 0,3 | |
Теплообменник | Диаметр кожуха, мм. | 30 |
Длина труб, мм. | 6000 | |
Поверхность теплообмена, м2. | 13 | |
Температура ЛГ на входе, º С | 280 | |
Температура ТСП на входе, º С | 120 | |
Температура ЛГ на выходе, º С | 229,0 | |
Температура ТСП на выходе, º С | 153,12 |
7
Лабораторный контроль производства
В таблице 7.1 представлен лабораторный контроль производства
Таблица 7.1 – Лабораторный контроль производства
№ п/п | Наименование стадий процесса, анализируемый продукт | Контролируемые показатели | Нормативные документы на методы измерений (испытаний, контроля анализов) | Норма | Частота контроля | |||||||||||
1 | 2 | 3 | 3 | 5 | 6 | |||||||||||
Сырье | ||||||||||||||||
1 | Тяжелая смола пиролиза | Коксуемость, % масс, не более | ISO 10370-95 | Не нормируется | По заданию | |||||||||||
Содержание серы, % масс., не более | ГОСТ Р 50442-92 | Не нормируется | По заданию | |||||||||||||
Фракционный состав: - до 400 ºС выкипает, % масс. | ГОСТ 10120-71 | Не нормируется | По заданию | |||||||||||||
- до 500 ºС выкипает, % масс | Не нормируется | По заданию | ||||||||||||||
Получаемые продукты | ||||||||||||||||
2 | Газ пекования | -Н2S % об., | ГОСТ 5439-76* | Не норм* | 1 раз в сутки | |||||||||||
-∑С5 % масс. и выше, % масс. | ГОСТ 14920-79 | Не норм* | 1 раз в сутки | |||||||||||||
3 | Легкий газойль пекования | Фракционный состав: - 50 % выкипает при температуре,ºС , не выше | ГОСТ 2177-99 | 280 | 1 раз в сутки | |||||||||||
- 96 % выкипает при температуре,ºС, не выше | 360 | 1 раз в сутки | ||||||||||||||
Массовая доля серы, % масс. | ГОСТ Р 50442-92 | Не норм* | 1 раз в сутки | |||||||||||||
Плотность при 20 ºС, кг/м³, не менее | ГОСТ 3900-85 | 880 | 1 раз в сутки | |||||||||||||
| | Температура вспышки ºС, не ниже | ГОСТ 6356-75 | 30 | 1 раз в сутки | | ||||||||||
Йодное число | ГОСТ 2070-82 | Не норм* | По заданию | | ||||||||||||
4 | Бензин пекования | Температура вспышки, определяемая в закрытом тигле, ºС, не ниже | ГОСТ 6356-75 | 110 | 1 раз в сутки | |||||||||||
Массовая доля серы, % масс. | ГОСТ Р 50442-92 | Не норм* | 1 раз в сутки | |||||||||||||
Коксуемость по Кондрансону, % масс. | ISO 10370-95 | Не норм* | 1 раз в сутки | |||||||||||||
Плотность при 20 ºС, кг/м3, не ниже | ГОСТ 3900-85 | 0,68 | 1 раз в сутки |
Продолжение таблицы 7.1
1 | 2 | 3 | 4 | 5 | 6 |
5 | Нефтяной пек | Содержание влаги, %, не более | ГОСТ 27314-91 ГОСТ 27588-88 | 3,0 | По заданию |
Зольность, %, не более | ГОСТ 11022-95 | 1,0 | По заданию | ||
Содержание общей серы, %, не более | ГОСТ 8606-93 ГОСТ 1437-75 | 2,50* | По заданию | ||
Выход летучих веществ, %, не более | ГОСТ 6382-2001 ГОСТ 22898-78 | 7,00 | По заданию | ||
Массовая доля мелочи: куски менее 8,0 мм, %, не более | ГОСТ 2093-82 ГОСТ 22898-78 | 45,0 | По заданию | ||
Зольность, %, не более | ГОСТ 11022-95 ГОСТ 22692-77 | 1,0 | По заданию | ||
Содержание общей серы, %, не более | ГОСТ 8606-93 ГОСТ 1437-75 | 5,0* | По заданию | ||
Выход летучих веществ, %, не более | ГОСТ 6382-2001 ГОСТ 22898-78 | Не норм* | По заданию | ||
Массовая доля мелочи: куски менее 8,0 мм, %, не более | ГОСТ 2093-82 или ГОСТ 22898-78 | Не норм* | По заданию |
8 Безопасность жизнедеятельности и экологичность
Технологические процессы, осуществляемые на установке производства нефтяных пеков, протекают при повышенных температурах и высоком давлении. Оборудование установки содержит значительное количество перегретой жидкости, углеводородных газов, паров, которые могут образовывать с воздухом взрывоопасные смеси.
На основании вышеизложенного технологические процессы, протекающие на установке, относятся к категории взрывопожароопасных. Основными опасными факторами являются:
- применение, обращение и получение взрывопожароопасных веществ (топливного газа, бензина, легкого газойля); наличие их в аппаратах в значительном количестве;