Файл: Курсовой проект 46 л., 4 рис., 12 табл., 15 источников, 1 прил.docx
ВУЗ: Не указан
Категория: Не указан
Дисциплина: Не указана
Добавлен: 11.04.2024
Просмотров: 53
Скачиваний: 0
ВНИМАНИЕ! Если данный файл нарушает Ваши авторские права, то обязательно сообщите нам.
Далее часть пека поступает в реакторы Р-3 и Р-4 для получения пеков разного сорта на пластификацию дистиллятами процесса термополиконденсации, а балансовое количество пека выводится с установки.
В работе [3] предложена принципиальная схема (рисунок 2.3) установки получения нефтяного пека методом термополиконденсации тяжелой смолы пиролиза. Основными аппаратами установки являются печь нагрева сырья П-1, реакторы термополиконденсации Р-1 и Р-2, ректификационная колонна К-1.
Так как, обслуживание установки, из-за отсутствия аппаратов высокого давления, просто и безопасно, и процесс не загрязняет окружающую среду поскольку все продукты перерабатываются в жидкой или газовой фазах, то в данном курсовом проекте рассматривается именно эта схема. Описание технологической схемы представлено ниже.
Сырье, предварительно нагретое в теплообменниках Т-1, Т-2, поступает в колонну фракционирования К-1. В Т-1 в качестве теплоносителя подается фракция 200- 360 °С) из отпорной колонны К-2 и далее выводится с установки. В Т-2 в качестве теплоносителя подается промежуточное циркуляционное орошение основной колонны К-1 и далее возвращается в колонну. Кубовый остаток из К-1, пройдя через печь П-1, поступает в реакторы термополиконденсации Р-1, Р-2, которые работают циклически. Пары с верха колонны К-1, проходят последовательно воздушный холодильник ВХ-1, водяной холодильник Х-1 и поступают в сепаратор С-1. Дистиллят возвращается в виде орошения, а газы выводятся с установки. Продукты выводятся с установки.
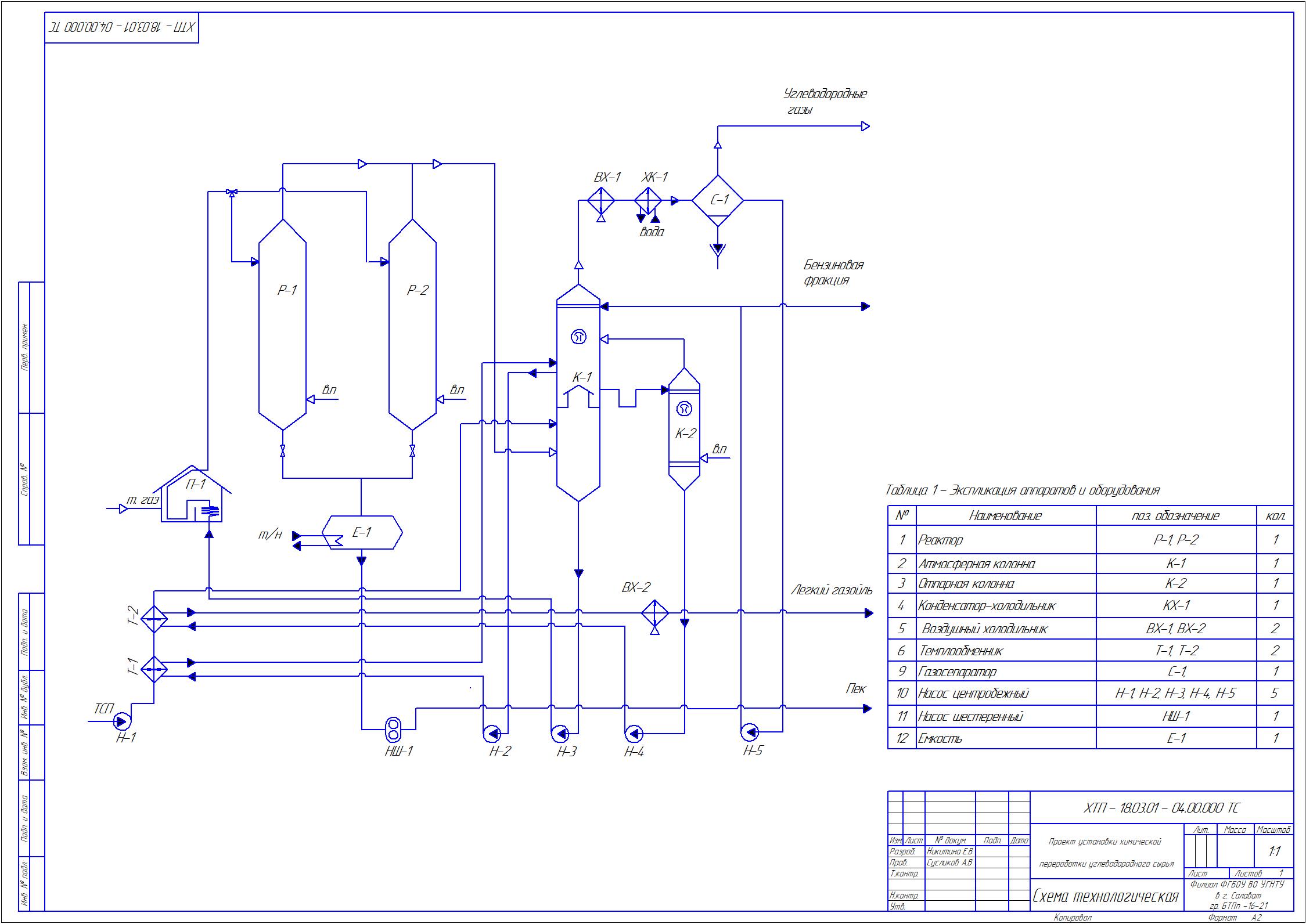
П-1– печь нагрева сырья; К-1 – ректификационная колонна; К-2 – отпорная колонна, Р-1, Р-2 – реакторы термополиконденсации; С-1 – газосепаратор; ВХ-1, ВХ-2 – воздушный холодильник; Х-1 – водяной холодильник; Т-1,Т-2, – теплообменники.
Рисунок 2.3 - Принципиальная технологическая схема установки получения нефтяного пека
3 Характеристика качества целевых продуктов, катализаторов, побочных продуктов
Качественные показатели сырья, основных и побочных продуктов процесса представлены в таблице 3.1
Таблица 3.1- Качественные показатели сырья и продуктов процесса
Наименоваие сырья, целевых и побочных продуктов | Номер ГОСТ, ОСТ, ТУ | Показатель качества | Норма по ГОСТ, ОСТ, ТУ | Область применения |
1 | 2 | 3 | 4 | 5 |
1 Тяжелая смола пиролиза | СТО 44905015-002 2014 | Плотность при температуре 20 °С, кг/м3 не более Фракционный состав: -Начало кипения, °С, не ниже -50%(об) перегоняется при температуре, °С Массовая доля серы, % не более Массовая доля механических примесей, % не более | 1052 190 Не нормируется 0,8 0,30 | Сырье установки |
2 Углеводо-родные газы | - | Не регламентируется | - | В топливную сеть предприятия |
3 Бензин пекования | ГОСТ 322350 | Концентрация свинца, мг/дм3 Не более Индукционный период, мин, не менее Концентрация марганца, мг/дм3 не более | 5 360 Отсутствует | На установку гидроочистки бензина |
Продолжение таблицы 3.1
1 | 2 | 3 | 4 | 5 |
Легкий газойль | | Не регламентируется | | На установку гидроочистки дизельного топлива |
Нефтяной пек | ГОСТ 9950 | Температура размягчения, °С Массовая доля веществ, нерастворимых в толуоле % Выход летучих веществ, % Зольность, %, не более Массовая доля воды в твердом пеке, %, не более | 65-70 24-28 59-63 0,3 4 | Основной продукт установки (как связующее в производстве электродной и анодной массы) |
4 Технологический расчет процесса и основных аппаратов
4.1 Исходные данные для расчета процесса
Исходные данные для расчёта:
- производительность установки 425 000 т/год;
- коэффициент рециркуляции К=1,2;
- количество дней работы установки 315 дней;
- температура пекования t = 430 °С;
- давление в камере Рр = 0,3 МПа;
- высота заполнения пеком реактора Нз = 6 м;
- давление верха реактора Рв = 0,25 МПа;
- диаметр реактора Dр = 5 м;
- плотность сырья ρ = 1052,0 кг/м3;
- объемная скорость подачи сырья ω = 0,25 ч-1.
4.2 Материальный баланс установки
ТСП получается на установке пиролиза как побочный продукт.
В таблице 4.1 показан материальный баланс процесса разгонки ТСП.
Таблица 4.1 – Материальный баланс процесса разгонки ТСП [8]
Фракция | Выход, % масс. |
Атмосферная перегонка | |
нк-220 °С | 13,4 |
220 – 250 °С | 14,2 |
250 – 300 °С | 16,9 |
300 – 330 °С | 17,4 |
Вакуумная перегонка | |
нк-360 °С | 16,6 |
Остаток | 16,6 |
Потери | 4,9 |
Итого | 100,0 |
В качестве сырья для производства нефтяного пека использована фракция выкипающая с 250 оС, что в свою очередь, позволяет увеличить выход целевого продукта (пека) и снизить выход дистиллята путем удаления из ТСП низкокипящих фракций. С учетом разгонки ТСП (таблица 4.1), имеем без учета легкой фракции (температура кипения менее 250 оС) состав тяжелой смолы пиролиза, представленный в таблице 4.2.
Таблица 4.2 – Состав тяжелой смолы пиролиза с учетом отгона легкой смолы пиролиза [11]
Фракция | Выход, % масс |
250 – 300 °С | 23,34 |
300 – 330 °С | 24,03 |
нк-360 °С | 22,93 |
Остаток | 22,93 |
Потери | 6,77 |
Итого | 100,00 |
С учетом что производительность по сырью составляет 425000 тонн в год, ассортимента и выхода получаемых продуктов в процессе производства пека составим материальный баланс установки. Результаты расчетов материального баланса установки представлены в таблице 4.3.
Таблица 4.3 – Материальный баланс установки
| % масс. | т/год | т/сут | кг/ч | кг/с |
Взято: | | | | | |
ТСП | 100 | 425000 | 1349,21 | 56216,93 | 15,62 |
Итого: | 100 | 425000 | 1349,21 | 56216,93 | 15,62 |
Получено | | | | | |
Газы С1-С4 | 4,47 | 18997,50 | 60,31 | 2512,90 | 0,70 |
Бензин (н.к-200 °С) | 8,3 | 35275,00 | 111,98 | 4666,01 | 1,30 |
Легкий газойль (200-350 °С) | 52,3 | 222275,00 | 705,63 | 29401,46 | 8,17 |
Пек | 34,93 | 148452,50 | 471,28 | 19636,57 | 5,45 |
Итого: | 100 | 425000,00 | 1349,21 | 56216,93 | 15,62 |
Учитывая количество рециркулята и подаваемого водяного пара (10% масс. на первичное сырье) составляем материальный баланс реактора (таблица 4.4).
Таблица 4.4 – Материальный баланс реактора
Взято | % масс | т/год | т/сут | кг/ч | кг/с |
Вторичное сырье | 120 | 510000 | 1619,05 | 67460,32 | 2,18 |
Водяной пар | 10 | 51000 | 161,90 | 6746,03 | 0,21 |
Итого: | 130 | 561000 | 1780,95 | 74206,35 | 2,39 |
Получено: | | | | | |
Газы С1-С4 | 4,47 | 18997,50 | 60,31 | 2512,90 | 0,70 |
Бензин (н.к-200°С) | 8,3 | 35275,00 | 111,98 | 4666,01 | 1,30 |
Легкий газойль (200-350°С) | 52,3 | 222275,00 | 705,63 | 29401,46 | 8,17 |
Пек | 34,93 | 148452,50 | 471,28 | 19636,57 | 5,45 |
Водяной пар | 10 | 51000,00 | 161,90 | 6746,03 | 1,87 |
Рециркулят | 20 | 85000,00 | 269,84 | 11243,39 | 3,12 |
Итого: | 130 | 561000,00 | 1780,95 | 74206,35 | 20,61 |
4.3 Расчет реактора
Примем геометрические размеры реактора, представленные в таблице 4.5.
Таблица 4.5 – Геометрические размеры реактора [9]
Показатель | Условное обозначение | Значение |
Высота конической части, м | h | 0,9 |
Диаметр конической части, м | d | 1,8 |
Высота реактора, м | Н | 13 |
Диаметр реактора, м | D | 5,4 |
Высота пека в цилиндрической части реактора равна
Нц = Нз – h, (4.1)
где Hз – высота заполнения пеком реактора, Hз =13 м.
Н3 = 13 – 0,9= 12,1 м.
Объем пека в нижней конической части реактора
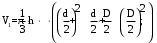

Объем пека в цилиндрической части реактора


Общий объем пека в реакторе

V=9,91+276,98=286,89 м3.
Общая объемная скорость образования пека


где gп – количество образовавшегося пека, кг/ч;
ρп – плотность пека, кг/м3.
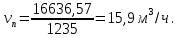
Время пекования в реакторе

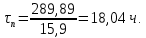
Количество ректоров составит:
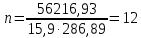
4.4 Расчет температуры верха реактора
Расчётная схема представлена на рисунке 4.1.
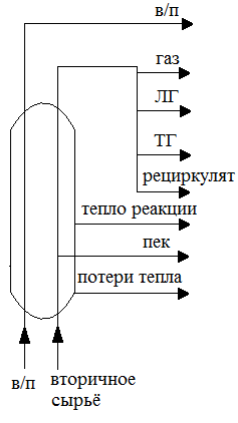