ВУЗ: Не указан
Категория: Не указан
Дисциплина: Не указана
Добавлен: 29.04.2024
Просмотров: 23
Скачиваний: 0
ВНИМАНИЕ! Если данный файл нарушает Ваши авторские права, то обязательно сообщите нам.
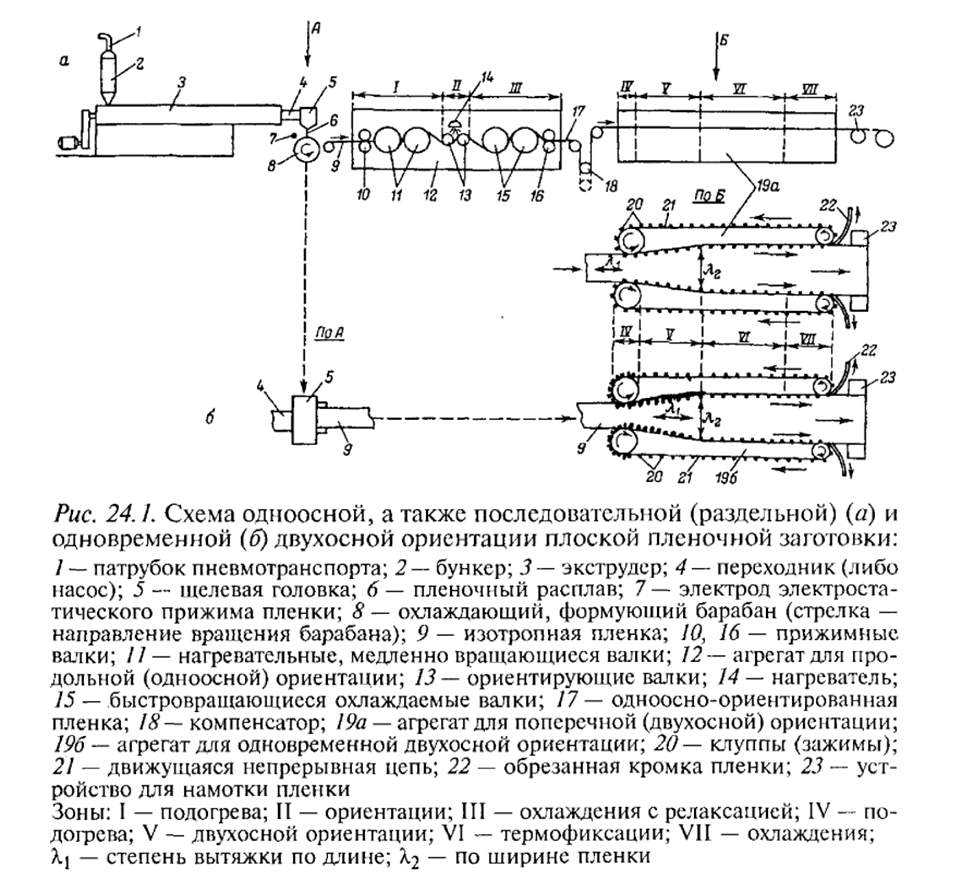
Последовательная двухосная ориентация пленок представлена на рис. 24.1, а. Заготовка 77 проходит через компенсатор 18, благодаря которому сглаживаются возможные колебания скорости подачи пленки. Пленка входит в агрегат 19а для растяжения ее по ширине. Здесь пленка с двух сторон захватывается зажимами (клуппами) 20 (см. вид "По Б') и направляется в зону предварительного прогрева TV; в последующей зоне V она растягивается по ширине и одновременно дополнительно разогревается. После зоны V двухосно-ориентированная пленка из аморфных полимеров (ПС) охлаждается на открытом воздухе в зоне VI, а из кристаллизующихся полимеров — поступает в зону термофиксации, где происходит кристаллизация. Охлаждение проходит в зоне VII на воздухе. Агрегат 19а иногда называют ширильной рамой. Выходя из агрегата 19а, клуппы 20 освобождают края пленки, которые тут же обрезаются и в виде отходов 22 идут на переработку. Оставшаяся плоская пленка с минимальной разнотолщинностью наматывается на барабан с помощью намоточного устройства 23. Одновременная двухосная ориентация пленок и тонких листов осуществляется по схеме, показанной на рис. 24.1, б, на агрегате 196, который имеет более сложную конструкцию. Изотропная пленка 9 поступает в зону IV, захватывается клуппами и предварительно подогревается. В зоне V она разогревается до температуры вытяжки и одновременно происходит ее вытяжка по ширине за счет движения зажимов по направляющим и вытяжка по длине — за счет увеличения расстояния между соседними зажимами. В этом случае зажимы вытягивают пленку в двух направлениях. Остальные операции аналогичны схеме, приведенной на рис. 24.1, а.
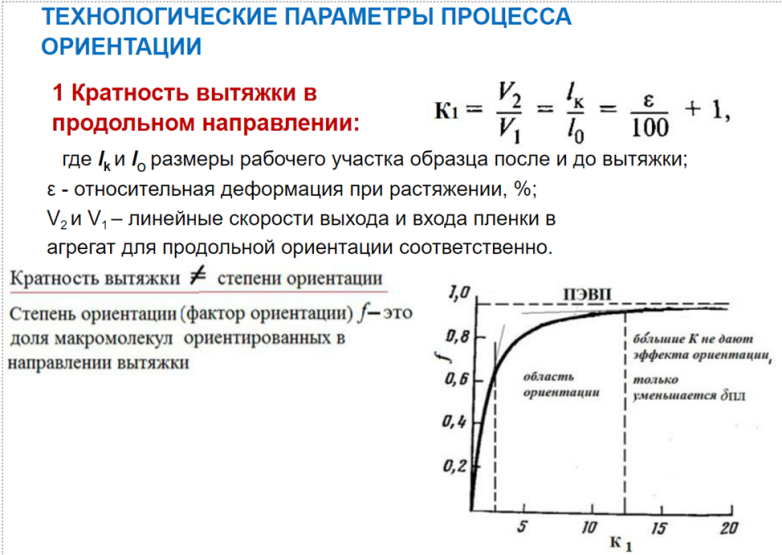
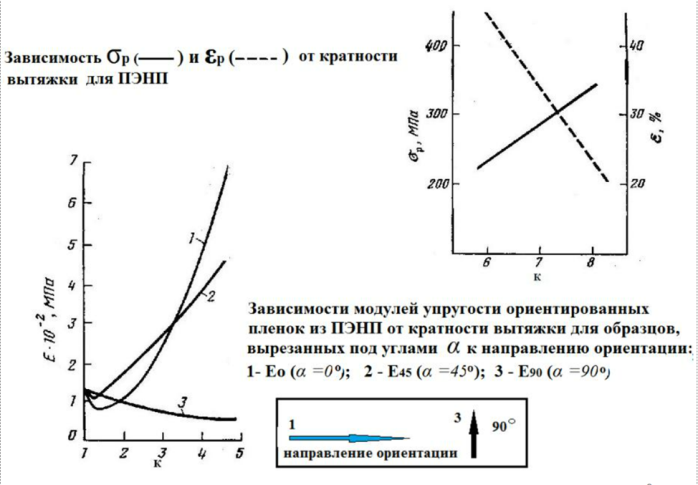
11. Литье под давлением реактопластов. Основные стадии процесса. Изменение давления
и температуры в форме в течение цикла литья.
Литье под давлением – метод формования изделий из полимерных материалов, заключающийся в нагревании материала до вязкотекучего состояния и передавливании его в закрытую форму, где материал приобретает конфигурацию внутренней полости формы и переходит в твердое состояние.
Требования к сплавам, применяемым для литья под давлением: 1. Сплавы не должны обладать красноломкостью, так как отливка в процессе затвердевания находится под действием механических усилий при удалении ее из неподвижной части формы, при выталкивании ее и при снятии со стержней. 2. Сплавы должны
иметь небольшую усадку и большую пластичность, а также достаточную прочность при высоких температурах, чтобы противостоять напряжениям, образующимся при затрудненной усадке на неподатливых металлических стержнях. 3. Сплавы должны обладать узким температурным интервалом кристаллизации, что необходимо для быстрого хода процесса, уменьшения термоусталости и сокращения износа форм. 4. Сплавы должны обладать высокой жидкотекучестью при небольшом перегреве; значительный перегрев хотя и увеличивает жидкотекучесть сплавов, но сильно влияет на износ форм.
Литье под давлением реактопластов – более прогрессивный метод по сравнению с компрессионным и литьевым прессованием, но требует наличия пресс-материалов с хорошей сыпучестью, меньшей вязкостью и более длительным временем вязко-пластичного состояния. Специфика переработки реактопластов литьем под давлением - не только процессы массопереноса и теплообмена, но и химические взаимодействия, ведущие к образованию трехмерной сетчатой структуры. Более жесткие требования к выполнению технологических условий литья, прежде всего, температурно-временных параметров процесса, а также исключению возможности образования застойных зон в материальном цилиндре литьевой машины.
Основные стадии процесса литья под давлением: 1. Получение сырья 2. Входной контроль сырья 3. Растаривание и хранение 4. Подготовка сырья к переработке (сушка) 5. Стадия формования 6. Промежуточный контроль качества изделий 7. Обработка отформованных изделий (термическая, механическая) 8. Контроль готовой продукции 9. Упаковка продукции 10. Хранение продукции
Формование
1. Загрузка пресс-порошка в пластикационный цилиндр из бункера с мешалкой, для предотвращения зависания. (для премиксов – специальные загрузочные устройства)
2. Перевод материала в вязкопластичное состояние в пластикационном цилиндре при вращении шнека и отхода его от сопла – пластикация. Нагрев материала до Тр происходит за счет тепла от внешних нагревателей и разогрева массы при трении о вращающийся шнек. Вязкость материала снижается до 10 3 - 10 4 Па*с. Время вязкопластичного состояния завершается резким нарастанием скорости химического взаимодействия, быстро нарастает вязкость материала и теряется текучесть, т. е. формуемость материала. Транспортирование материала шнеком к соплу, прохождение через сопло и заполнение формующей полости должно происходить в течение времени вязкопластичного состояния перерабатываемого реактопласта.
Изменение давления в форме от времени процесса.
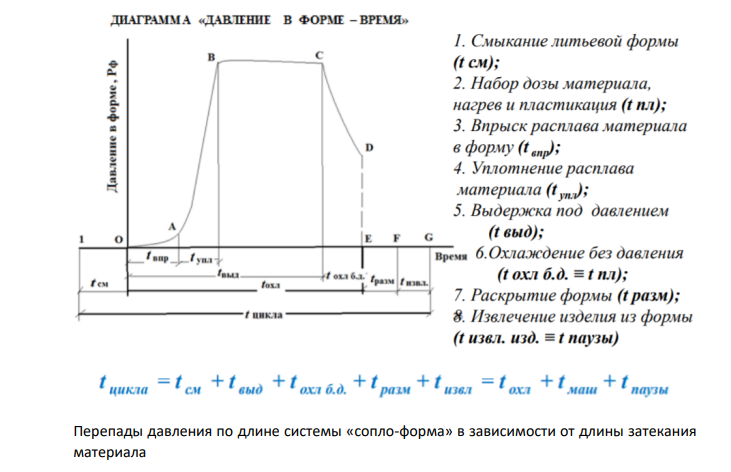
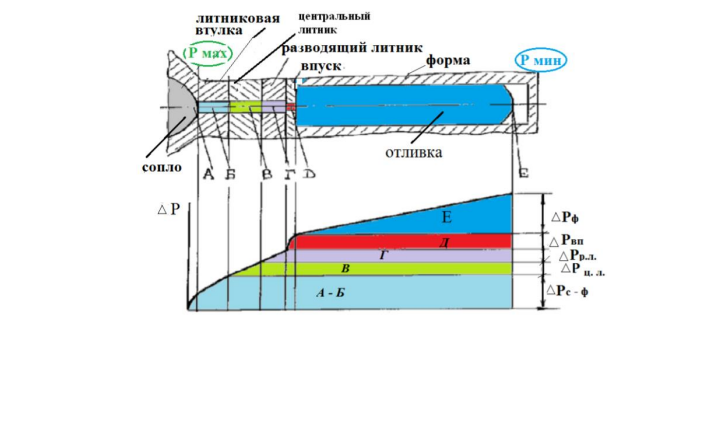
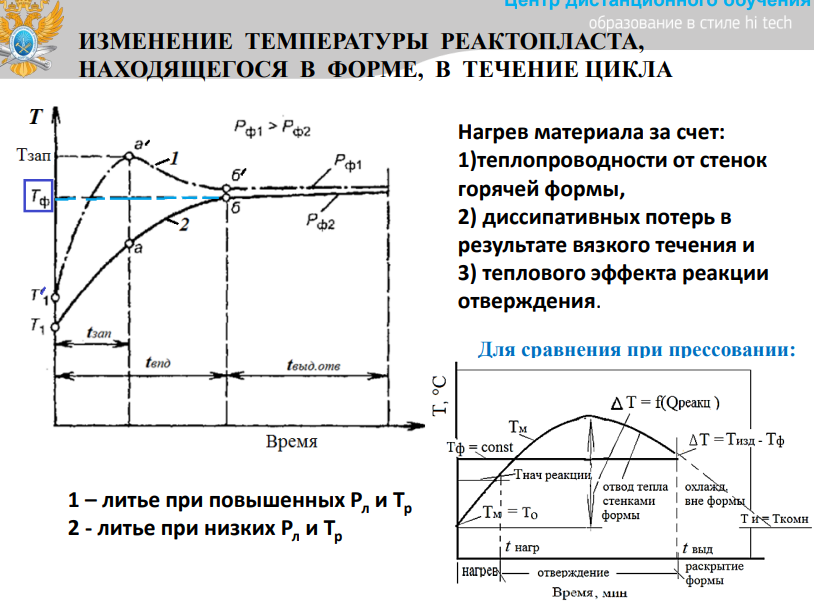
Р: Давление возникает с момента соприкосновения плунжера с материалов в форме, и оно заставляет растекаться полимер
, заполняя полость формы. Достигает наибольшего значения в момент окончательной остановки пуансона после смыкания формы. Обычно для характеристики режима используют удельное давление прессования – усилие, приходящееся на 1 площади прессования (площадь проекции изделия на плоскость разъема пресс-формы). На величину Руд влияет текучесть пресс-материала, форма изделия, его размеры и конструкция. Удельное давление возрастает при увеличении габаритов изделия и уменьшении толщины стенок. Прессование при недостаточном давлении ведет к появлению недопрессовок, увеличению грата, ухудшению внешнего вида и другим видам брака.
12. Литье под давлением термопластов. Требования к технологическим свойствам сырья.
Основные стадии процесса. Цикл литья, изменение давления в форме в течение цикла
литья.
Литье под давлением – метод формования изделий из полимерных материалов, заключающийся в нагревании материала до вязкотекучего состояния и передавливании его в закрытую форму, где материал приобретает конфигурацию внутренней полости формы и переходит в твердое состояние. Оборудование: плунжерные и червячные литьевые машины.
ОСНОВНЫЕ СТАДИИ ПРОЦЕССА ЛИТЬЯ ПОД ДАВЛЕНИЕМ: 1) Получение сырья; 2) Входной контроль сырья; 3) Растаривание и хранение; 4) Подготовка сырья к переработке (сушка); 5) Стадия формования; 6) Промежуточный контроль качества изделий; 7) Обработка отформованных изделий (термическая, механическая); 8) Контроль готовой продукции; 9) Упаковка продукции; 10) Хранение продукции.
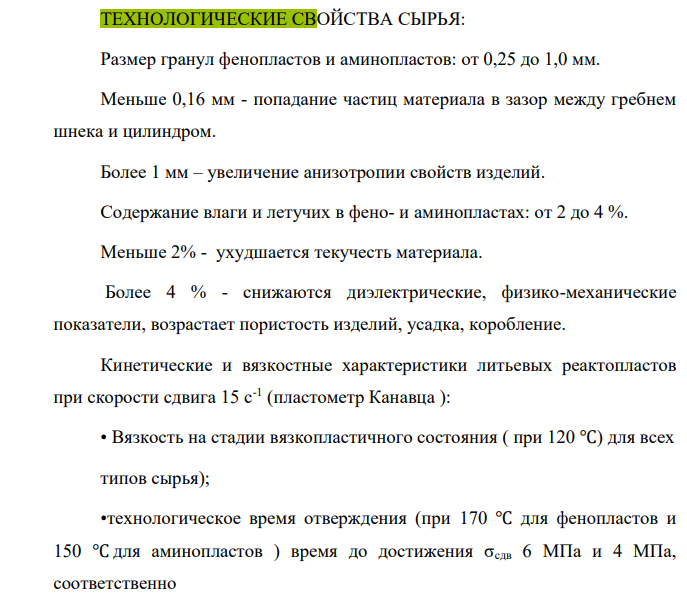
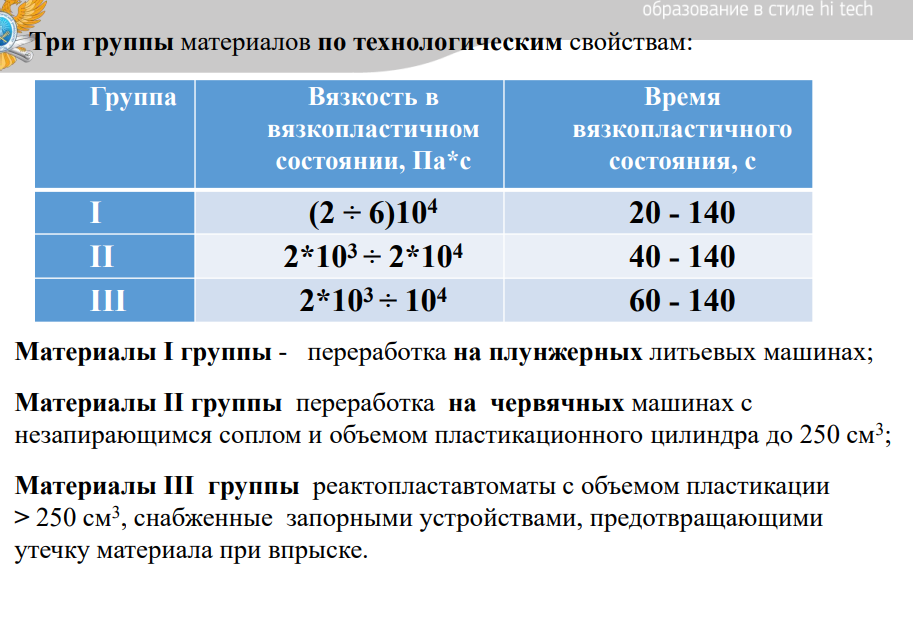
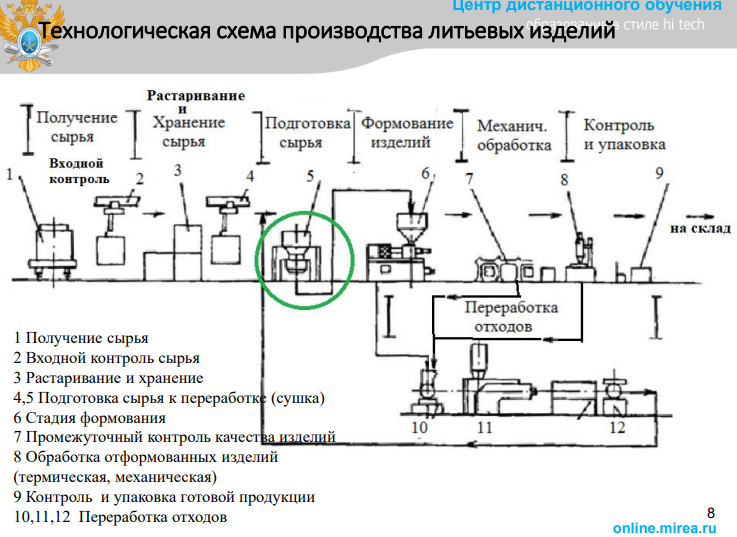
Цикл литья под давлением: 1) Сырье (гранулы, порошок) поступает в бункер
2) Через загрузочное окно в пластикационный цилиндр
3) Плавление, гомогенизация в пластикационном. цилиндре
4) Впрыск расплава в предварительно сомкнутую форму За счет движения шнека вперед (как поршня)
5) Выдержка под давлением (1) и без давления со стороны шнека (2). В период (2) набор новой дозы при вращении и отходе шнека назад
6) Охлаждение (кристаллизация) в форме.
7) Размыкание формы за счет отвода подвижной плиты
8) Съем изделия.
9) Смыкание формы за счет продвижения подвижной плиты вперед поршнем гидроцилиндра узла смыкания
10) Впрыск новой дозы
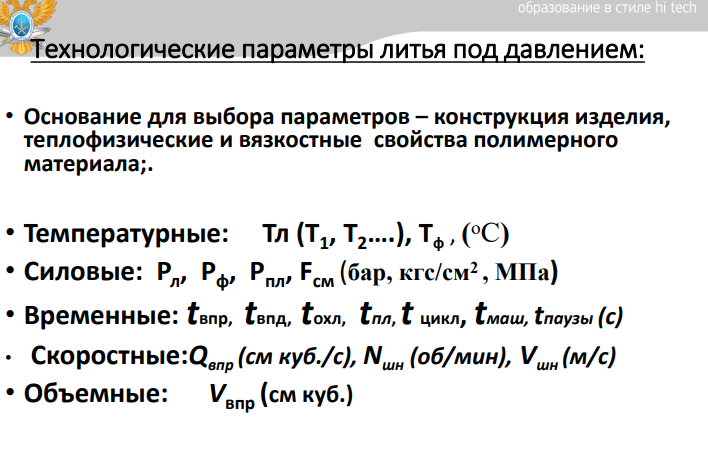
Температура расплава должна обеспечивать необходимую вязкость для заполнения формы, но при этом не должна протекать декструкция материала. Обычно вязкость расплава достигается для у аморфных полимеров при температуре на 100-150 ℃ выше температуры стеклования, а у кристаллических при температурах, на несколько градусов превышающих температуру плавления – на 30-40 ℃ ниже, чем температура деструкции. С ростом температуры снижается термостабильность расплава, необходимо учитывать, что продолжительность пребывания материала в пластикационном цилиндре не должна быть больше времени термостабильности расплава при данной температуре.
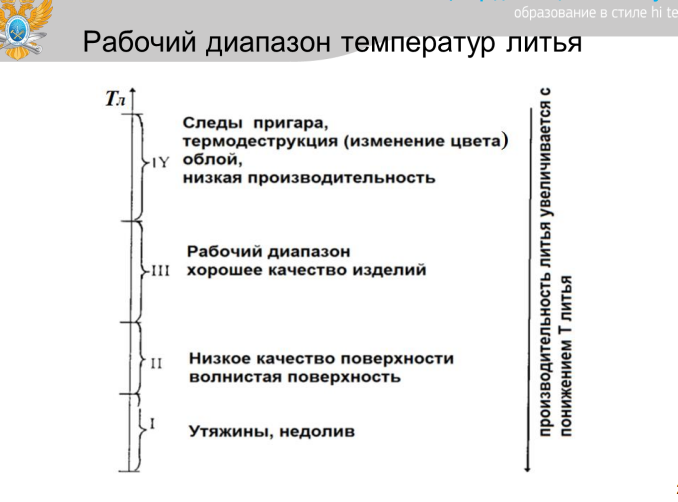