Файл: 1. Общее устройство машины. Основные механизмы и приводы.doc
ВУЗ: Не указан
Категория: Не указан
Дисциплина: Не указана
Добавлен: 16.10.2024
Просмотров: 5
Скачиваний: 0
ВНИМАНИЕ! Если данный файл нарушает Ваши авторские права, то обязательно сообщите нам.
План:
ВВЕДЕНИЕ
1. Общее устройство машины.
2. Основные механизмы и приводы.
3. Особенности конструкции.
ЗАКЛЮЧЕНИЕ.
Список литературы.
ВВЕДЕНИЕ
Конвейер – это машина непрерывного действия для перемещения сыпучих, кусковых или штучных грузов. Конвейеры нужно классифицировать по принципу действия и конструктивным признакам, типу тягового и грузонесущего органа, роду перемещаемого груза, назначению и областям применения.
Основной классификационный признак конвейера — тип тягового органа. Различают конвейеры с ленточным, цепным, канатным тяговыми органами. По принципу действия различают конвейеры:
-
перемещающие груз на непрерывно движущейся сплошной ленте или настиле, в непрерывно движущихся ковшах, подвесках, платформах, тележках; -
по неподвижному желобу или трубе непрерывно движущимися скребками.
По назначению различают конвейеры:
-
стационарные и передвижные для насыпных, штучных грузов и для пассажиров, -
по направлению перемещения грузов - с вертикально замкнутой, горизонтально замкнутой и пространственной трассами.
По областям применения конвейеры подразделяют на машины общего назначения и специальные (стакеры, элеваторы, эскалаторы, движущиеся тротуары).
Конвейеры являются составной, неотъемлемой частью современного технологического процесса, они устанавливают и регулируют темп производства, обеспечивают его ритмичность, способствуют повышению производительности труда и увеличению выпуска продукции. Наряду с выполнением транспортно-технологических функций конвейеры являются основными средствами комплексной механизации и автоматизации погрузочно-разгрузочных и складских операций.
На современных предприятиях конвейеры используют в качестве:
-
высокопроизводительных транспортных машин, передающих грузы из одного пункта в другой на участках внутризаводского и внешнего транспорта; -
транспортных агрегатов мощных перегрузочных устройств (например, мостовых перегружателей, отвалообразователей) и погрузочно-разгрузочных машин; -
машин для перемещения грузов-изделий по технологическому процессу поточного производства от одного рабочего места к другому, от одной технологической операции к другой, устанавливая, организуя и регулируя темп производства и совмещая, в ряде случаев, функции накопителей (подвижных складов) и распределителей грузов-изделий по отдельным технологическим линиям; -
машин и передаточных устройств в технологических автоматических линиях изготовления и обработки деталей и узлов изделий.
Тесная связь транспортирующих машин с общим технологическим процессом производства обусловливает высокую ответственность их работы и назначения. Поэтому конвейеры должны быть надежными (безотказными), прочными, удобными в эксплуатации и способными работать в автоматических режимах.
1. Общее устройство машины.
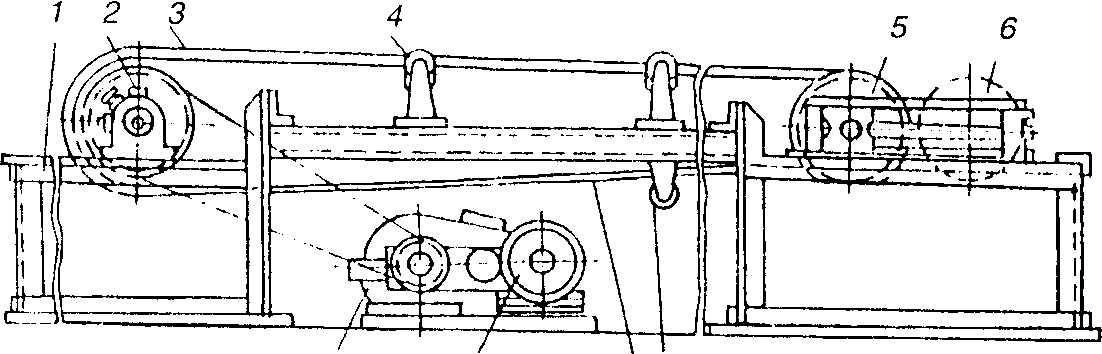
Рисунок 1. Конвейер 1 – остов: 2 – приводной барабан; 3 – рабочая ветвь ленты; 4 – верхняя роликоопора; 5 – натяжной барабан; 6 – натяжное устройство ленты; 7 – нижние роликоопоры; 8 – холостая ветвь ленты: 9 – электродвигатель; 10 – редуктор
Основой конвейера служит гибкая бесконечная лента, которая в зависимости от типа роликоопор может иметь в поперечном сечении плоскую или желобчатую форму. Верхняя и нижняя ветви поддерживаются от провисания роликоопорами. Поступательное движение ленты сообщаются приводным барабаном, для постоянного натяжения ленты используют натяжное устройство (грузовое или винтовое).
2. Основные механизмы и приводы
Основными элементами конвейера являются:
Лента конвейерная.
Конвейерная лента - основной элемент конвейеров, обеспечивающий перемещение грузов на требуемое расстояние и передачу возникающих при этом тяговых усилий. Лента должна обладать высокой прочностью, гибкостью, хорошей эластичностью, сопротивляемостью ударным нагрузкам и абразивному износу, способностью работать в агрессивной окружающей среде, иметь при этом возможно меньший вес и толщину. Возможны дополнительные требования:
-
пожаробезопаснось, -
способность работать при высоких или низких температурах, -
возможность транспортирования при повышенных углах наклона конвейера.
По назначению конвейерные ленты делятся:
-
ленты общего назначения. Условия эксплуатации, которых не предполагают повышенной пожароопасности. -
специальные. К ним относятся: огнестойкие (не воспламеняющиеся при пробуксовке на приводном барабане); морозостойкие (до -55°С), теплостойкие (до 100°С).
Конструкция ленты представляет собой завулканизированный в резиновую массу каркас, воспринимающий тяговое усилие и обеспечивающий нужную прочность. Резиновое покрытие (верхняя, нижняя и боковые обкладки), предохраняют каркас от ударных нагрузок, истирания, действия влаги. Для повышения гибкости ленты между прокладками часто помещают резиновые прослойки – сквиджи.
В настоящее время конструируют конвейерные ленты:
-
с тканевой основой (каркасом), -
с основой из стальных тросов.
Резинотканевые ленты изготавливаются из нескольких слоев ткани, соединяемых между собой слоями резины методом вулканизации.
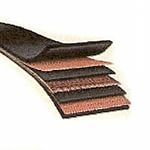
Ткань придает ленте прочность, необходимую для передачи значительных тяговых условий. Для защиты от механических повреждений, действия влаги ткань покрывается сверху, снизу и с боков слоем резины (обкладками). Толщина верхней (рабочей) обкладки, подверженной наибольшему износу, зависит главным образом от степени абразивности и кусковатости транспортируемого материала. Для предохранения основного каркаса от повреждений ударными нагрузками над ним может быть уложен слой ткани редкого переплетения (брекер).
Материалом для прокладок служит хлопковое волокно (бельтинг), синтетические (лавсан, амид, капрон) и комбинированные (лавсан с хлопком, лавсан с капроном), а также полиэфир-полиамидные ткани. Синтетические ткани наряду с высокой прочностью обладают эластичностью и влагоустойчивостью, благодаря чему при низкой температуре не смерзаются и не теряют гибкости.
Характеристики некоторых типов тканей:
-
ткань БКНЛ-65 - смесовая (полиэфир, хлопок); номинальная прочность при разрыве тяговой прокладки 65 Н/мм; толщина 1 прокладки 1,2 мм. -
ткань ТК-80 - синтетическая (капроновая); номинальная прочность при разрыве тяговой прокладки 80 Н/мм, толщина 1 прокладки 0,7-0,8 мм; -
ткань ТК-100 - синтетическая (капроновая); номинальная прочность при разрыве тяговой прокладки 100 Н/мм, толщина 1 прокладки 0,9-1,0 мм; -
ткань ТК-200-2 - синтетическая (капроновая); номинальная прочность при разрыве тяговой прокладки 200 Н/мм, толщина 1 прокладки 1,1-1,2 мм; -
ткань ЕР-415, 500, 630 - лавсаноанидная высокопрочная (импортная), толщина 1,4-1,9 мм. -
ТЛА-350 - лавсаноанидная высокопрочная (отечественная), толщина 1,45-1,55 мм.
Условное обозначение ленты должно содержать:
-
буквенные и цифровые индексы, обозначающие тип и вид ленты, -
ее ширину в миллиметрах, -
число тканевых прокладок каркаса, -
сокращенное наименование ткани, -
толщину резиновых обкладок на рабочей, и нерабочей сторонах ленты в миллиметрах, -
класс обкладочной резины и обозначение стандарта. Также маркировка может включать название предприятия-изготовителя (товарный знак), год изготовления, номер ленты. Пример условного обозначения по ГОСТ 20-85: 2ШТС-(ТГ)-900-5-ТК-200-4,5/3,5. Здесь: 2ШТС - тип ленты (шахтная трудносгораемая); ТГ - трудногорючее исполнение; 800 - ширина ленты, мм; 5 - число прокладок; ТК - вид материала тканевой прокладки; 200 - удельная разрывная прочность прокладки, Н/мм ширины; 4,5/3,5 - толщина верхней и нижней обкладки ленты.
Привод.
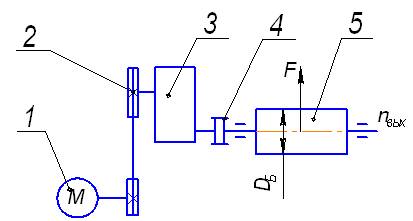
Составляющими звеньями привода ленточного конвейера являются электродвигатель (1), зубчатоременная передача (2), редуктор (3), зубчатая муфта (4), приводной барабан (5). Кинематическая схема привода ленточного конвейера построена на том, что асинхронный электродвигатель вращает с помощью ременной передачи быстроходный входящий вал цилиндрического редуктора. Входящий вал редуктора вращение передает на промежуточный вал при помощи косозубой передачи.
В свою очередь промежуточный вал при помощи прямозубой зубчатой передачи вращает выходной вал редуктора. С помощью компенсирующей зубчатой муфты крутящий момент от выходного вала редуктора передается к валу приводного барабана конвейера.
Став с роликоопорами.
Став конвейера обеспечивает устойчивое, в основном прямолинейное движение ленты с грузом. При резком отклонении от трассы, перекосах стоек, перекосах барабанов груз «сваливается» с ленты, центровка ее невозможна.
Роликоопора – металлическая конструкция, предназначенная для установки роликов на ленточных конвейерах. Став конвейера оснащается специальными роликоопорами, обеспечивающими автоматическое центрирование верхней и нижней ветвей ленты. Выпускаются роликоопоры трёх типов - лёгкой средней и тяжёлой серии.
-
Тяжёлая серия, разработанная для шахтных конвейеров, отличается повышенной жёсткостью и надёжностью конструкции. Роликоопоры изготавливаются с различным углом наклона боковых роликов по желанию заказчика, а также специального назначения – центрирующие подвесные. Конструкция роликоопор исключает возможность выпадения ролика из кронштейна и повреждения ленты роликоопорами при боковом сходе ленты.
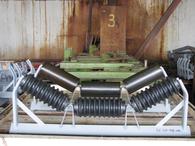
Для предотвращения схода ленты используют желобчатые центрирующие роликоопоры. Они выглядят как обыкновенные желобчатые, но только снабжены двумя роликами дефлекторными на поворотном кронштейне и вращаются относительно оси.
Есть подвесная опора, или как её ещё называют гирлянда. Эта роликоопора разрабатывалась для того чтобы приспосабливать её на тросово-канатовых конвейерах, которые предназначены для транспортировки крупнокусковых материалов. Эта конструкция имеет ряд преимуществ:
-
значительно увеличивает ресурс работы подшипников; -
за счет гибкости опоры уменьшается давление на ленту и увеличивается скорость движения ленты в полтора-два раза.
Гирлянда выпускается с разным количеством роликов, (трех или двухроликовые), благодаря этому снижаются нагрузки на ленту; появляется возможность центрирования ленты. Такой вид роликовых опор удобен при установке или демонтаже.
Загрузочное и натяжное устройство.
Натяжные устройства придают ленте натяжение, достаточное для передачи на приводном барабане тяговой силы трением при пуске конвейера, а при установившемся движении ограничивают провисание ленты между роликоопорами, компенсируют удлинение ленты в результате вытяжки её в процессе работы и сохраняют некоторый запас длины ленты, необходимый для ремонта её при повреждениях.
Натяжные устройства могут быть винтовыми и грузовыми, а по их расположению на трассе – хвостовыми и промежуточными; натяжение ленты осуществляют перемещением натяжного барабана.
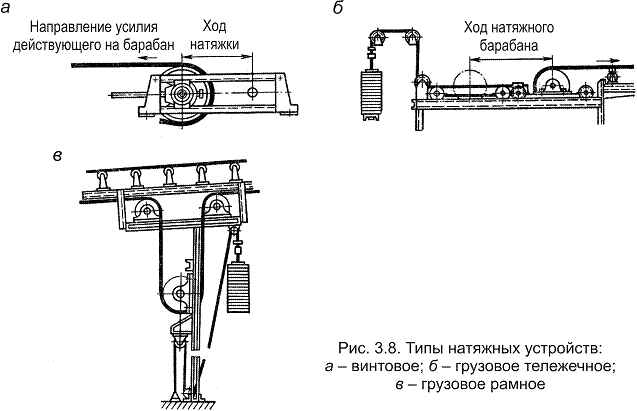
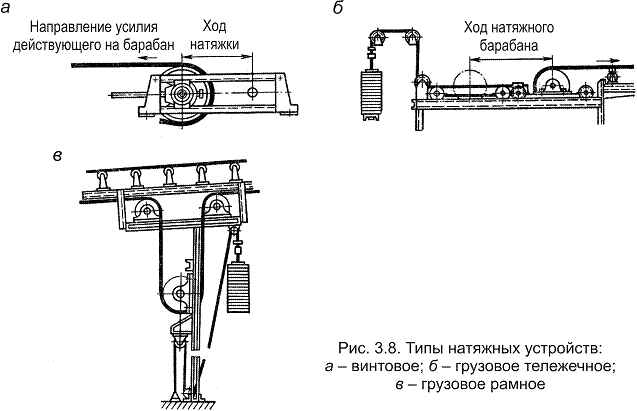
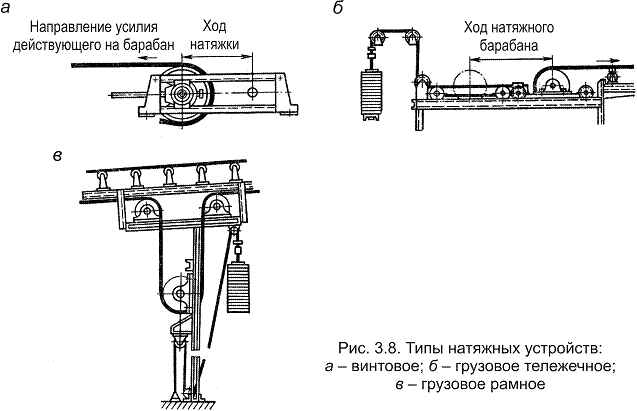
Винтовое и грузовое тележечное натяжные устройства (хвостовые) располагаются на концевом барабане перед выходом ленты на рабочую ветвь; грузовое рамное (промежуточное) натяжное устройство, устанавливается вблизи приводного барабана на холостой ветви, где лента имеет минимальное натяжение.
Загрузочные устройства предназначены для загрузки ленты конвейера из приемных бункеров или с технологических транспортных и погрузочных агрегатов. Загрузочные устройства конвейеров равномерно распределяют груз по длине ленты и центрально по ее ширине.
Исходя из технологических требований, конвейер может загружаться и разгружаться в любом пункте трассы. Загрузку осуществляют у заднего концевого барабана.
Загрузочные устройства по конструктивным особенностям делят на три группы:
-
с самотечным, -
принудительным, -
сложным движением грузов.
При подборе типа загрузочного устройства необходимо учесть основные требования, предъявляемые к данному оборудованию. Оно должно обеспечивать:
-
Центровку и равномерное распределение груза по поверхности ленты; -
Скорость подачи материала на ленту транспортера, как по величине, так и по направлению (желательно, чтобы эти значения были близки к параметрам движения ленты); -
Максимально возможное уменьшение вредных воздействий на ленту и механизмы транспортера от поступающего потока груза; -
Исключение завалов, заторов и просыпания материала в сторону от ленты загрузочного конвейера; -
Возможность регулировки интенсивности подачи при изменении физико-механических характеристик материала; -
Износоустойчивость при интенсивном абразивном и ударном воздействии; -
Простое и удобное техническое обслуживание и ремонтопригодность.