Файл: Задание курсовой нормирование точности гладких соединений.docx
ВУЗ: Не указан
Категория: Не указан
Дисциплина: Не указана
Добавлен: 08.02.2024
Просмотров: 28
Скачиваний: 0
ВНИМАНИЕ! Если данный файл нарушает Ваши авторские права, то обязательно сообщите нам.
Карта исходных данных для зубчатой передачи
Определить геометрические параметры зубчатого колеса
Диаметр делительной окружности d = m × z = 4 × 35 = 140 мм.
Диаметр окружности выступов dа = d + 2×m = 140 + 2×4 = 148 мм.
Диаметр окружности впадин df =d – 2,5 ×m = 140 – 2,5×4 = 130 мм.
Диаметр основной окружности db = d × cos = 140 × cos 20° = 131,5 мм.
Ширина зубчатого венца В = 10 × m = 10 × 4 = 40 мм.
Количество охватываемых зубьев при измерении длины общей нормалиzw =4.
Длина общей нормали W = 4 × 10,872 = 43,5 мм [1, табл. 6.1].
Назначить степень точности зубчатой передачи
Передача является кинематической. В этом случае наиболее важной является кинематическая точность, она назначается на одну степень точнее, чем нормы плавности и контакта зубьев.
По заданной окружной скорости, согласно [1, табл. 6.3] рекомендуется степень точности по нормам плавности – 6.
Принимаем степень кинематической точности – 5, степень точности по нормам контакта зубьев – 6.
Вид сопряжения определяется наименьшим гарантированным боковым зазором

jnmin ≥ jn1 + jn2
Для кинематической передачи

Боковой зазор соответствующей температурной компенсации определяется по формуле:

где a межосевое расстояние в передаче, мм;
− 1 и 2 коэффициенты линейного расширения для материалов зубчатых колес и корпуса;
− t1 и t2 предельные температуры, для которых рассчитывается боковой зазор, для зубчатых колес и корпуса соответственно.
При t1=+60С, t2=+30С, 1=2=11,5·10-6 получим:

jnmin = 0,040 + 0,033 = 0,073 мм.
Определяем вид сопряжения с учетом межосевого расстояния в передаче по [1, табл. 6.4].
Полное обозначение точности передачи:
5-6-6-D ГОСТ 1643-81.
Определить исполнительный размер длины общей нормали
Верхнее отклонение EWs = 40 мкм по [1, табл. 6.10] для вида сопряжения с 6-й степенью точности, d = 140 мм.
Допуск на длину общей нормали TW = 55 мкм, по [1, табл. 6.11] для Fr = 40 мкм [1, табл. 6.6].
Нижнее отклонение EWi = |EWs|+ Tw = 40 + 55 = 95 мкм
Исполнительный размер длины общей нормали –

Определить требования к базовым поверхностям зубчатого колеса
Требования к точности заготовок под операцию зубонарезание определяются по рекомендациям [1, табл. 6.14].
Базовое отверстие должно быть выполнено по 6-му квалитету, 45H6(+0,016), так как по нормам плавности 6-я степень.
Диаметр вершин зубьев используется по 2-му варианту (как измерительная база для выверки заготовки на станке), следовательно, его точность –
Тda = 0,01·m= 0,04 мм; 148h5(-0,018).
Допуск на радиальное биение по вершинам зубьев: Fd= 0,6·Fr= 0,640 = 24 мкм.
Принимаем Fd= 25 мкм по [1, табл. 2.9].
Торцовое биение базового торца на диаметре 0,75d= 0,75140 = 105 мм находим расчетом, определив F= 9 мкм, по [1, табл. 6.9]:
FТ = (0,5F dб)/B = (0,50,009105)/40 = 47 мкм, по [1, табл. 2.10] принимаем FT= 50 мкм.
Все расчетные параметры указываем на чертеже зубчатого колеса (рис. 3.11).
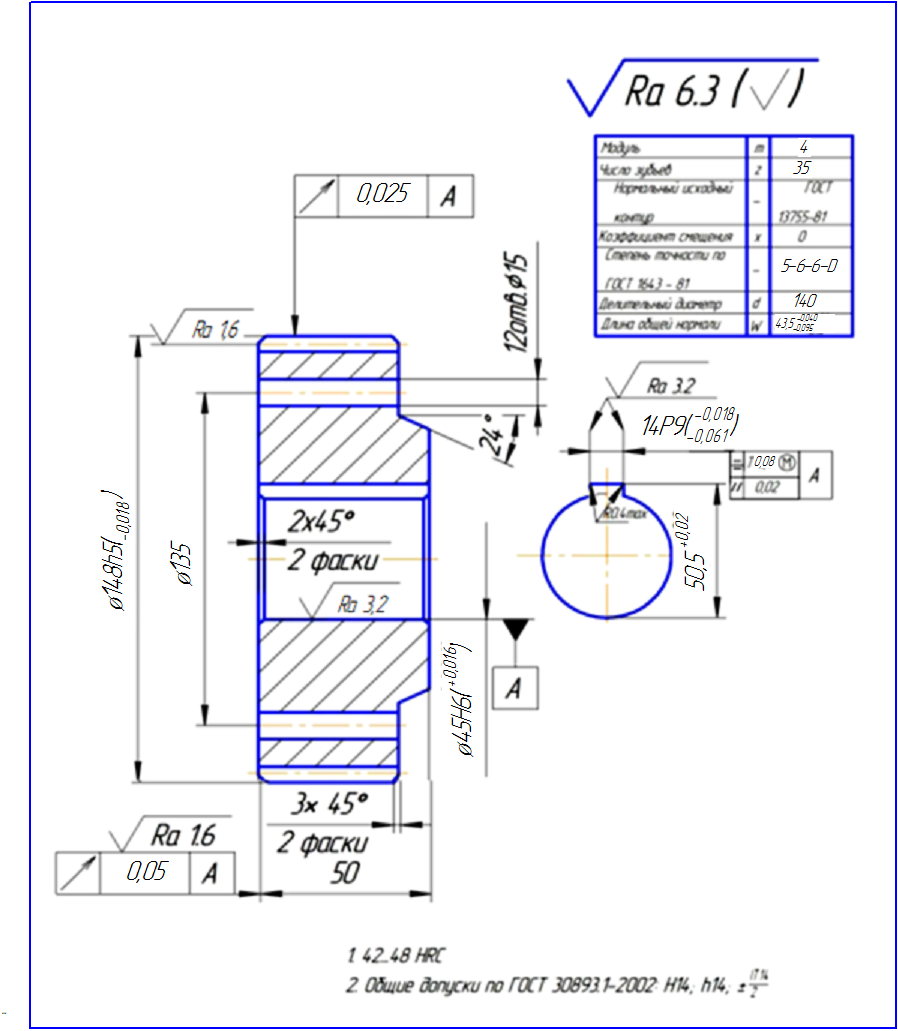
Рис. 3.11. Зубчатое колесо
4. Выбор универсальных средств измерения.
Таблица 4.1
Карта исходных данных по выбору средств измерения
Наименования исходных данных | Значения исходных данных |
Контролируемая поверхность | Отверстие |
Исполнительный размер D1 | 190H7(+0,046) |
Коэффициент технологической точности ![]() | 3,5 |
Тип производства | серийное |
Выбрать универсальное средство измерения для цехового
контроля
Выбор средств измерений зависит (СИ) от ряда факторов:
- организационно – экономических (тип производства, вид взаимозаменяемости, стабильность технологического процесса, стоимость, наличие СИ и др.);
- конструкторских параметров изделия (габариты, масса, жесткость, вид контролируемой поверхности и др.);
- метрологических (пределы и диапазон измерения, цена деления, класс точности, погрешность СИ и др.).
Универсальные СИ находят широкое применение во всех типах производств, так как имеют низкую себестоимость.
Произведем выбор СИ по метрологическим факторам, учитывая, что контролируется отверстие.
Считаем, что некоторые систематические погрешности (температурная, погрешность базирования и др.) устранены до начала процесса измерения. Допускаемая погрешность метода измерения должна быть больше неисключенной систематической погрешности СИ.
По ГОСТ 8.051 определим для размера 190 допуск на изготовление (IT) и допускаемую погрешность измерения (δ) согласно [1, табл. 7.1]:
IT = 0,046 мм; δ =12 мкм.
Выбираем возможное измерительное средство: [1, табл. 7.2].
Это код 18 – нутромер индикаторный НИ 160-260 ГОСТ 9244 со следующими техническими характеристиками:
- цена деления отсчетного устройства: i=0,001 мм;
- предельна погрешность измерительного средства: Δ=7,5 мкм;
Метод измерения прямой, контактный, относительный.
Для настройки на ноль требуются концевые меры длины 3-го класса точности.
Оценка влияния погрешностей измерения на результаты разбраковки выполняется по относительной точности метода измерения:
Амет(σ) = σмет ×100/ IT = 3,75 · 100/ 46 = 16%
где σмет =Δ/2= 5/2 = 2,5 мкм - среднее квадратичное отклонение погрешности измерения принятого средства измерения.
Для 7-го квалитета стандарт рекомендует принять
Амет(σ) = 16%
.
По заданному коэффициент технологической точности K = 3,5 по графикам [1, рис. 7.1] определяем параметры разбраковки:
- необнаруженный брак (риск заказчика) m= 2,3%;
- ложный брак (риск изготовителя) n= 7,2%;
- вероятностный выход размера за границу поля допуска c/IT= 0,16%,
С = IT× c/IT = 46 · 0,16 = 7,4 мкм.
Оценка годности деталей производится по предельно допустимым размерам:
Dmax = 190,046 мм; Dmin = 190,000 мм.
Среди годных деталей могут оказаться бракованные (не более 2.3%), у которых размеры выходят за границы поля допуска на величину до 7,4 мкм. Это риск заказчика. Риск изготовителя не более 7,2%.
Выполним расчет производственного допуска
Принимаем условие недопустимости риска заказчика при Δ>δ и проводим расчет производственного допуска для измерения СИ по коду 17. Это индикаторный нутромер НИ-160-260 ГОСТ 868, который имеет цену деления индикатора 0,01 мм и предельную погрешность Δ=25 мкм:
Тпр = IT - 2·С = 46 - 2·7,4 = 31,2 мкм.
Предельно-допустимые размеры с учетом производственного допуска:
Dmax= 190,046 – 0,0046 = 190,0414 мм;
Dmin= 190,000 + 0,0046 = 190,0046 мм.
Варианты установления приемочных границ даны на рис. 4.1.
Выбор средств измерения для арбитражной перепроверки
При разногласиях между рабочим и контроллером требуется арбитражная перепроверка. Допускаемая погрешность при арбитражной перепроверке:
Δарб = 0,3· δ = 0,3·12 = 3,6 мкм.
Выбираем измерительное средство с кодом 27 [1, табл. 7.2].
Индикатор многооборотный, который имеет цену деления 0,002 мм и предельную погрешность 4 мкм. Настройка прибора на 0 производится с помощью винта, служащего для установки механизма в нулевое положение. Крепят индикатор за присоединительную гильзу.
Метод измерения – относительный, прямой, контактный.
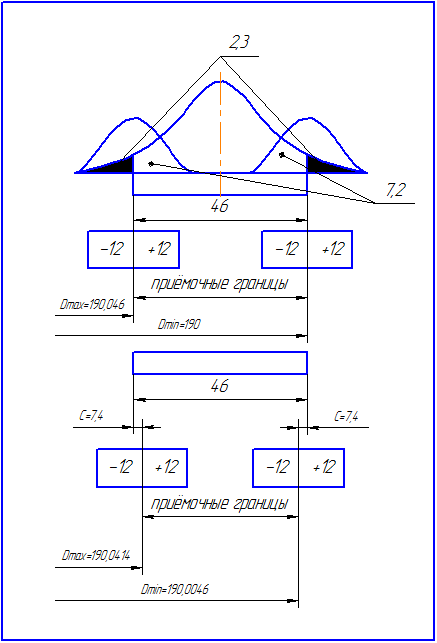
Рис. 4.1. Варианты установления приёмочных границ:
а - границы совпадают с конструкторским допуском;
б - смещены на вероятную величину с
СПИСОК ЛИТЕРАТУРЫ
Основная
1. Кайнова, В.Н. Нормирование точности изделий машиностроения: учеб. пособие / В.Н. Кайнова [и др.]; НГТУ. Н.Новгород, 2007.−207с.
2. Нормирование точности деталей машин: метод. указ./ сост.: Л.А. Болдин [и др.]; НГТУ. Н.Новгород, 1999.
3. Нормирование точности деталей машин: метод. указ./ сост.: В.Н. Кайнова, И.Н. Фролова [и др.]; НГТУ. Н. Новгород, 1996.
4. Проектирование гладких калибров для контроля валов и отверстий: метод. указ. / сост.:В.Н. Кайнова [и др.]; НГТУ. Н.Новгород, 2004.
5. Выбор универсальных средств измерения: метод. указ./ сост.: В.Н. Кайнова, [и др.]; НГТУ. Н. Новгород, 1996.
Дополнительная
6. Белкин, И.М. Допуски и посадки /И.М.Белкин.− М.:Машиностроение, 1992.
7. Марков, Н.Н Нормирование точности в машиностроении: – учеб. для машиностр. спец. вузов / Н.Н. Марков [и др.], под ред. Ю.М. Соломенцева. – 2-е изд., испр. и доп..− М.: Высш. шк., 2001.
8. Марков А.Л. Измерение зубчатых колес / А.Л. Марков. − Л.: Машиностроение, 1977.
9. Допуски и посадки: справочник в 2-х ч. / под ред. В.Д. Мягкова. − Л.: Машиностроение, 1983.
10. Дунаев, П.Ф. Расчет допусков размеров / П.Ф. Дунаев, О.П. Леликов. − М.: Машиностроение, 1992.
11. Палей, М.А. Допуски и посадки: справочник в 2-х ч./ М.А. Палей [и др.]. − Л.: Политехника, 1991.
12. Черменский О.Н. Подшипники качения: справочник-каталог/ О.Н. Черменский, Н.Н. Федотов. − М.: Машиностроение, 2003.
13. Радкевич Я. М. Метрология, стандартизация и сертификация: учеб для вузов / Я.М. Радкевич [и др.]. − М.: Высш. шк., 2004.
14. Варианты заданий курсовых работ по дисциплине «Метрология, стандартизация и сертификация» Ч.2: метод. указ./ сост.: В.Н. Кайнова [и др.]; НГТУ. Н.Новгород, 2006.
15. Кайнова В.Н., Гребнева Т.Н. Метрология, стандартизация и сертификация: комплекс учебно-методических материалов: Ч1/ В.Н. Кайнова, Т.Н.Гребнева; НГТУ, Н.Новгород, 2006.